Introduction to Flex Boards
Flex boards, also known as flexible printed circuit boards (FPCBs), are a rapidly growing technology in the world of electronics manufacturing. As the name suggests, flex boards are thin, bendable circuit boards made from flexible insulating substrate materials like polyimide or polyester.
The flexible nature of flex boards allows them to be folded, bent, twisted or formed into 3D shapes. This makes them ideal for use in small, complex devices where space is limited or where frequent flexing of the circuitry is required. Some common applications of flex boards include:
- Wearable electronics
- Medical devices
- Consumer electronics
- Automotive electronics
- Industrial equipment
- Aerospace and defense products
Key Properties and Advantages
Flex boards offer several key properties that give them advantages over traditional rigid circuit boards:
- Flexible – Can be bent and formed to fit constrained spaces and moving components.
- Thin and lightweight – Flex boards can be extremely thin, less than 0.2 mm. This allows compact, lightweight design.
- Durable – Withstands vibration, shock and repeated flexing.
- High connectivity – Flexible construction allows more interconnects in a small space.
- Reliable – Polyimide materials provide reliable insulation and protection.
Manufacturing Process
The specialized materials and construction of flex boards require unique manufacturing processes. Here is a general overview:
- A layer of adhesive copper foil is laminated onto the flexible substrate material. This forms the conductive traces.
- Photolithography is used to print the circuit pattern onto the copper layer.
- Etching removes excess copper, leaving only the desired conductive traces.
- Components are precisely positioned and soldered onto the traces.
- Protective coverlay or encapsulation is applied over the circuitry.
- Electrical testing verifies function.
- The boards are cut or routed to final dimensions.
Careful process controls during each step ensure reliability and performance.
Trends Driving Adoption of Flex Boards
Several technology and market trends are fueling rapid growth in demand and innovation for flex board electronics:
Miniaturization
As electronic devices like smartphones, wearables and medical devices get smaller, flex boards allow compact circuitry to fit into increasingly tight spaces. The thin, bendable design can “wrap around” rigid components and flatten out dead space.
Lightweight Portability
Weight reduction is a priority for mobile and portable devices. The lightweight nature of polyimide and other flex board substrate materials contributes to overall weight savings compared to traditional rigid circuit boards.
Innovation in Electronics
Emerging products like flexible displays, electronic fabric, and stretchable circuits take advantage of the dynamic flex capabilities of FPCBs. Flex boards are enabling whole new categories of flexible electronics.
Cost Savings
When designed properly for the application, flex boards can offer significant cost reductions compared to rigid boards. Simpler assembly, fewer layers, and less hardware can lower overall system cost.
Consumer Demand
As consumers expect faster, thinner, more robust devices, flex boards allow manufacturers to meet these expectations through intelligent and reliable design.
Applications Utilizing Flex Boards
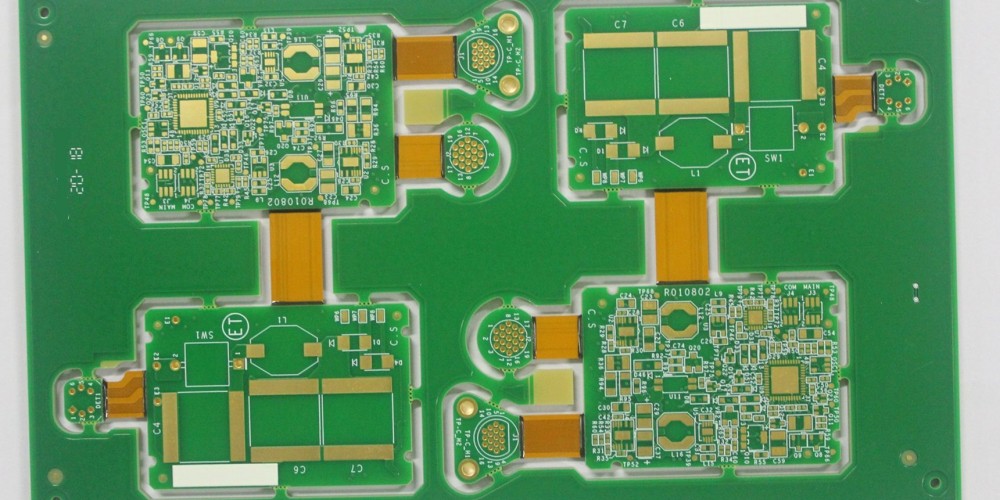
Flex boards are used across a wide range of industries and applications. Here are some of the leading products using flex board technology:
Consumer Electronics
- Smartphones – Interconnect rigid PCBs and integrate antennas
- Laptops and tablets – Foldable interconnects for displays and keyboards
- Wearable devices – Flexible circuit foundation for smart watches and activity trackers
Automotive
- Circuitry in seats, mirrors and controls subject to movement and vibration
- Sensor interconnects needing dynamic flexing as suspension moves
- Save space in crowded engine compartments and instrument panels
Medical
- Implantable devices like pacemakers and glucose monitors
- Wearable health monitors bending with body movement
- Endoscopes with flex boards threaded through narrow openings
Aerospace and Military
- Missile guidance systems
- Avionics packages in tight confines
- Communications links on flexible antennas
Industrial
- Robotics joints and manipulators
- Navigate tight spaces in chambered equipment
- Resist vibration in harsh environments
This table summarizes some of the top applications making use of flex board technology:
Application | Key Benefits |
---|---|
Smartphones | Compact, high-density interconnections |
Wearable Electronics | Flexible, lightweight, durable |
Laptops/Tablets | Dynamic folding |
Automotive Electronics | Vibration resistance, tight spaces |
Medical Devices | Biocompatible, miniature |
Aerospace/Military | Rugged, tight confines |
Industrial Robotics | Withstand vibration, enable articulation |
Flex Board Design Considerations
Proper design is critical to achieving optimal performance and reliability from flex boards. Here are some key design factors to consider:
- Flexibility requirements – The bend radius, repeat cycles, and range of motion help determine minimum trace widths and substrate thickness.
- Component mounting – Both surface-mount and through-hole components can be used, with attention to adhesion, vibration, and termination styles.
- Trace routing – Avoid sharp corners or acute angles that put stress on traces. Use smooth curves and teardrops at turns.
- Substrate openings – Openings in the substrate provide flexibility but require careful reinforcement around the edges.
- Stiffeners and encapsulation – Strategically placed stiffeners or protective coatings can strengthen high-stress areas while allowing flexibility elsewhere.
- ESD protection – Polyimide’s insulating properties increase susceptibility to electrostatic discharge damage, requiring protection measures.
- Testing – Ensure the boards undergo appropriate inspection and electrical testing after flexing and assembly.
With mindful design optimized for the specific application demands, flex boards can deliver reliable, high-performance interconnections in challenging electronic packages.
The Future of Flex Boards
Continued technology improvements and market pressures promise an exciting future for flex board applications. Here are some emerging trends to watch:
- Extreme miniaturization down past 50 microns to integrate multiple flex layers and components.
- Flexible hybrid electronics combining flex boards with printed electronics, sensors and other stretchable technologies.
- Flex board innovation enabling foldable, rollable, and stretchable smart devices.
- Wider adoption in wearable devices, medical applications, consumer products and the Internet of Things.
- Flex board metamaterials with properties engineered at the structural level.
- Improved manufacturability and economies of scale to reduce costs.
As electronics manufacturers push the boundaries of innovation, flex circuit technology will play an increasingly vital role in enabling many emerging product designs.
Conclusion
With their flexible, lightweight and rugged design, flex boards deliver interconnectivity solutions where rigid boards cannot. As electronic applications demand ever-greater miniaturization, portability and sophistication, flex boards provide the capabilities needed to meet these challenges. With sound design principles and continual technology evolution, flex boards will be at the heart of many of tomorrow’s most advanced electronic devices.
Frequently Asked Questions
What are the main materials used in flex board construction?
The most common materials are polyimide films like Kapton for the flexible substrate, and copper foil for the conductive traces. Polyester films are also used, along with acrylic, polyurethane and epoxy adhesives.
How thin can flex boards be manufactured?
Extremely thin – down to about 25 microns, which is around 1/3 the thickness of a human hair. Typical flex boards range from 50 to 150 microns thick.
Can components be mounted on both sides of a flex board?
Yes, components can be surface mounted or inserted through holes on both sides. Care must be taken in routing traces and terminals between sides.
What are some methods for connecting flex boards to rigid PCBs?
Common methods include soldered tabs, various connectors like ZIF and pressure-fit sockets, and anisotropic conductive films.
How much does a typical flex board cost compared to a rigid PCB?
Simple flex boards can cost 20-30% less than an equivalent rigid board. But complex, multilayer flex boards may cost more than rigid technology.