Introduction to PCB Circuit Drawing
Drawing a PCB (Printed Circuit Board) circuit is an essential skill for anyone involved in electronics design and manufacturing. A well-designed PCB ensures that the electronic components are connected correctly and efficiently, leading to a reliable and functional end product. In this comprehensive guide, we will walk you through the process of drawing a PCB circuit, from understanding the basics to using advanced tools and techniques.
What is a PCB?
A PCB is a flat board made of insulating material, such as fiberglass or plastic, with conductive tracks, pads, and other features etched onto its surface. These conductive elements are used to electrically connect various components, such as resistors, capacitors, and integrated circuits, to create a functional electronic circuit.
Why is PCB design important?
Proper PCB design is crucial for several reasons:
- Functionality: A well-designed PCB ensures that the electronic components are connected correctly, allowing the circuit to function as intended.
- Reliability: Proper PCB layout and routing minimize the risk of signal integrity issues, electromagnetic interference, and thermal problems, leading to a more reliable product.
- Manufacturing: A well-designed PCB is easier to manufacture, reducing the likelihood of errors and defects during the production process.
- Cost-effectiveness: Efficient PCB design can help minimize the board size and layer count, reducing manufacturing costs.
PCB Design Workflow
The PCB design workflow typically consists of the following steps:
- Schematic capture
- Component placement
- PCB routing
- Design rule checking (DRC)
- Gerber file generation
Schematic Capture
Schematic capture involves creating a diagram that represents the electrical connections between components in the circuit. This is usually done using Electronic Design Automation (EDA) software, such as KiCad, Eagle, or Altium Designer.
To create a schematic:
- Select the appropriate components from the EDA software’s library or create custom components if needed.
- Place the components on the schematic canvas.
- Connect the components using wires or nets, ensuring that the connections match the circuit diagram.
- Assign unique reference designators to each component (e.g., R1 for the first resistor, C1 for the first capacitor).
- Add power and ground symbols to the schematic.
- Annotate the schematic with additional information, such as component values and part numbers.
Component Placement
Once the schematic is complete, the next step is to place the components on the PCB layout. This process involves arranging the components in a logical and efficient manner, taking into account factors such as signal integrity, thermal management, and manufacturability.
To place components on the PCB:
- Import the netlist generated from the schematic into the PCB layout editor.
- Define the board outline and any mechanical constraints, such as mounting holes or connectors.
- Place the components on the board, considering the following factors:
- Group related components together to minimize signal path lengths.
- Place sensitive components, such as high-speed devices or analog circuits, away from potential sources of interference.
- Ensure adequate spacing between components for heat dissipation and manufacturability.
- Orient components to facilitate easy assembly and soldering.
- Add any necessary copper pours or ground planes to the layout.
PCB Routing
PCB routing involves creating the conductive tracks that connect the components on the board. The goal is to create a routing scheme that is efficient, reliable, and compliant with the design rules specified by the PCB manufacturer.
To route the PCB:
- Define the design rules, such as minimum track width, minimum clearance between tracks, and via size.
- Route the power and ground nets first, using wider tracks or copper pours to minimize resistance and ensure a low-impedance return path.
- Route the critical signals, such as high-speed or sensitive analog signals, using controlled impedance techniques and avoiding sharp bends or vias whenever possible.
- Route the remaining signals, prioritizing shorter path lengths and minimizing the number of vias.
- Ensure that all connections are complete and that there are no unintended short circuits or open connections.
Design Rule Checking (DRC)
Design Rule Checking (DRC) is the process of verifying that the PCB layout meets the specified design rules and is free from errors. EDA software typically includes built-in DRC tools that can automatically check the layout for violations.
To perform a DRC:
- Define the design rules in the EDA software, including track width, clearance, via size, and other relevant parameters.
- Run the DRC tool on the PCB layout.
- Review any reported violations and make necessary corrections to the layout.
- Repeat the DRC process until the layout passes all checks.
Gerber File Generation
Gerber files are the industry-standard format for describing the PCB layout for manufacturing. These files contain information about the copper layers, solder mask, silkscreen, and drill holes.
To generate Gerber files:
- Set up the Gerber file export settings in the EDA software, specifying the desired file format and any required parameters.
- Generate separate Gerber files for each copper layer, solder mask, silkscreen, and drill layer.
- Review the generated files to ensure they are complete and accurate.
- Send the Gerber files to the PCB manufacturer for fabrication.
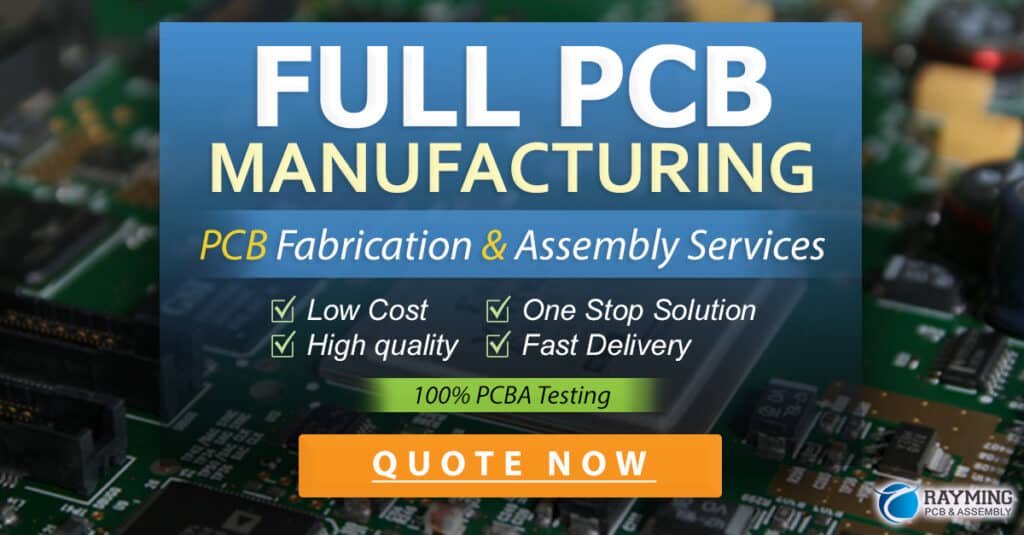
Advanced PCB Design Techniques
High-Speed PCB Design
When designing PCBs for high-speed applications, such as high-frequency digital circuits or RF systems, special considerations must be taken to ensure signal integrity and minimize electromagnetic interference (EMI).
Some key techniques for high-speed PCB design include:
- Controlled impedance routing: Matching the impedance of the tracks to the source and load impedances to minimize reflections and signal distortion.
- Differential signaling: Using balanced differential pairs for high-speed signals to reduce EMI and improve noise immunity.
- Ground planes: Using continuous ground planes to provide a low-impedance return path for high-frequency currents and minimize EMI.
- Decoupling capacitors: Placing decoupling capacitors close to power pins of high-speed devices to reduce power supply noise and improve signal integrity.
Analog PCB Design
Analog PCB design focuses on preserving the integrity of sensitive analog signals, such as those in audio, video, or measurement systems. Some important considerations for analog PCB design include:
- Grounding: Using separate analog and digital ground planes, connected at a single point, to minimize ground loops and noise coupling.
- Shielding: Using copper pours or metal shields to isolate sensitive analog circuits from sources of EMI.
- Component placement: Placing analog components away from potential sources of interference, such as digital circuits or power supplies.
- Filtering: Using passive or active filters to remove unwanted noise or interference from analog signals.
Thermal Management
Proper thermal management is essential for ensuring the long-term reliability and performance of electronic devices. Some techniques for managing heat in PCB design include:
- Component placement: Placing high-power components, such as voltage regulators or power transistors, away from heat-sensitive devices.
- Copper pours: Using large copper pours or thermal vias to efficiently dissipate heat from high-power components to the PCB substrate or external heatsinks.
- Airflow: Designing the PCB layout to facilitate adequate airflow over heat-generating components, using fans or vents if necessary.
- Thermal interface materials: Using thermal interface materials, such as thermal pads or heatsink compounds, to improve heat transfer between components and heatsinks.
PCB Design Tools and Resources
There are many software tools and resources available for PCB design, ranging from free and open-source options to professional-grade commercial packages. Some popular PCB design tools include:
Tool | Description | Pricing |
---|---|---|
KiCad | Open-source, cross-platform EDA suite for schematic capture and PCB layout | Free |
Eagle | Popular EDA software for schematic capture and PCB layout, now owned by Autodesk | Paid, with free version available |
Altium Designer | Professional-grade EDA software with advanced features for high-speed and complex PCB design | Paid |
OrCAD | Comprehensive EDA solution for schematic capture, simulation, and PCB layout | Paid |
Fritzing | User-friendly EDA software for beginners, with a focus on breadboard and prototyping projects | Paid, with free version available |
In addition to software tools, there are many online resources and communities dedicated to PCB design, offering tutorials, forums, and design tips. Some notable resources include:
- EEVblog: Popular electronics engineering video blog and forum, with a strong focus on PCB design and manufacturing.
- Hackaday: Online community for electronics enthusiasts, featuring project showcases, tutorials, and news.
- Adafruit: Online retailer and resource for electronics makers, offering tutorials, project ideas, and a supportive community.
- Sparkfun: Online retailer and resource for electronics hobbyists, with a focus on education and accessible project ideas.
Frequently Asked Questions (FAQ)
1. What is the difference between a schematic and a PCB layout?
A schematic is a diagram that represents the electrical connections between components in a circuit, using symbols and lines. A PCB layout, on the other hand, is a physical representation of the circuit, showing the actual placement and routing of components on a printed circuit board.
2. How do I choose the right PCB design software for my needs?
When selecting PCB design software, consider factors such as your budget, the complexity of your projects, and your level of experience. Free and open-source tools like KiCad are a good choice for beginners or small-scale projects, while professional-grade tools like Altium Designer or OrCAD are better suited for complex, high-speed designs.
3. What are the most common PCB manufacturing processes?
The two most common PCB manufacturing processes are through-hole technology (THT) and surface-mount technology (SMT). THT involves drilling holes in the PCB and inserting component leads through the holes, which are then soldered on the opposite side. SMT involves placing components directly on the surface of the PCB and soldering them in place using a reflow oven or wave soldering process.
4. How do I ensure my PCB design is manufacturable?
To ensure your PCB design is manufacturable, follow these guidelines:
- Adhere to the design rules specified by your PCB manufacturer, such as minimum track width, clearance, and via size.
- Use standard component footprints and packages whenever possible.
- Avoid using unnecessarily small or fine-pitch components.
- Provide adequate spacing between components for assembly and soldering.
- Use a consistent grid size for component placement and routing.
5. What are the most common PCB materials, and how do I choose the right one for my project?
The most common PCB materials are FR-4, a glass-reinforced epoxy laminate, and Rogers materials, which are high-performance laminates designed for high-frequency applications. When choosing a PCB material, consider factors such as the operating frequency, dielectric constant, thermal conductivity, and cost. FR-4 is a good choice for most general-purpose applications, while Rogers materials are better suited for high-frequency or RF designs.
Conclusion
Drawing a PCB circuit is a complex process that involves multiple steps, from schematic capture to component placement, routing, and design rule checking. By understanding the basics of PCB design and following best practices for high-speed, analog, and thermal management, you can create reliable and efficient PCBs for a wide range of applications.
To further develop your PCB design skills, explore the various software tools and online resources available, and engage with the vibrant community of electronics enthusiasts and professionals. With practice and dedication, you can master the art of PCB design and bring your electronic projects to life.