As electronic devices become smaller and more complex, flexible printed circuit boards (flex PCBs) have become an increasingly popular solution. Flex PCBs allow circuits to bend and flex to fit into tight spaces. They are commonly used in consumer electronics, medical devices, automotive applications and more.
When sourcing flex PCBs, one of the key considerations is cost. Pricing for flex PCBs depends on many factors. In this guide, we’ll break down the key influences on flex PCB pricing and provide price ranges for reference. We’ll also look at pricing trends and ways to reduce flex PCB costs.
Key Factors That Impact Flex PCB Price
Several variables affect the pricing for custom flex PCB orders. Here are some of the most important factors:
Layer Count
A flex PCB’s layer count significantly impacts its cost. Each layer adds complexity to the manufacturing process, requiring additional steps of lamination, drilling, plating, etc. Here are typical layer count ranges and associated pricing levels:
- Single layer: Lowest cost option. Ideal for simple circuits.
- 2-4 layers: Medium cost. Balances complexity and affordability.
- 5-8 layers: Moderately high cost. For complex, dense circuits.
- 10+ layers: Highest cost. Only for highly advanced applications.
As a rough guideline, each additional conductive layer adds about 30% to the overall cost.
Board Size
In general, larger flex PCBs cost more than smaller ones. This is because more raw materials are required.
However, the pricing versus size relationship is not directly proportional. There are economies of scale that come into play with larger boards sizes.
Here are typical size ranges and associated pricing levels:
- <100 mm2: Low cost for prototype volumes. Becomes very expensive at higher quantities due to tooling costs.
- 100-500 mm2: Economical size range for full production runs. Allows spreading out tooling costs.
- 500-2000 mm2: Moderately expensive since more materials are required, but size efficiencies still help costs from being prohibitive.
- >2000 mm2: Larger sizes get progressively more expensive. Additional challenges come with handling large boards during manufacturing and assembly.
Quantity Ordered
As with most manufactured items, PCB prices are significantly affected by order quantities. Tooling, setup and NRE costs get amortized over larger order volumes.
Here are typical quantity ranges and associated pricing:
- 1-50 pcs: Very high cost per board, since no economies of scale. Best for early prototyping.
- 50-500 pcs: Cost per board drops rapidly. Recommended for pilot builds.
- 500-5,000 pcs: Cost efficiencies start leveling off, but per unit cost continues to decrease. Ideal for initial production runs.
- 5,000+ pcs: Lower cost per board plateau. Large orders required to drive cost down further.
Materials
- Flex PCB substrate: Polyimide, polyester, polyethylene are common. Polyimide is most expensive but offers the best performance.
- Cover layers: Additional coated layers add cost but protect conductors. Coverlay + bonding adhesive is an economical option. Laminates are more expensive but more durable.
- Conductor material: Copper is standard. Silver plating adds cost for higher conductivity.
- Number of coverlayers: More coverlayers increases cost. Often a tradeoff with durability.
- Plated through holes vs vias: Plated through holes cost more due to additional drilling/plating steps.
Tolerances and Specifications
Tight tolerances and precise specifications require more attention during manufacturing, increasing costs. Here are some examples:
- Line width/space: Tighter tolerances increase cost. A 0.1mm line/space costs more than a 0.2mm line/space.
- Hole size: Smaller drill diameters and tighter tolerances raise cost.
- Hole pitch: Denser hole spacing requires more precision, increasing cost.
- Bending radius: A tighter minimum bend radius calls for special materials and processes.
- Impedance control: Tight impedance control for RF circuits requires additional process steps.
- Testing/QC requirements: More rigorous inspection and testing adds cost.
Lead Time
Shorter lead times often command higher prices, depending on supplier capabilities. Typical lead times range from 2 weeks (or faster) for “quick turn” orders, up to 8-12 weeks for standard “low cost” orders.
Unique Requirements
Special flex PCB requirements like controlled impedance, HDI technology, flex-rigid boards, etc. increase cost due to additional materials and process complexities.
Location of Supplier
Country and region where a supplier is located affects labor rates, raw material expenses and other overhead costs that influence pricing.
Flex PCB Price Ranges
With the many variables involved, it’s hard to provide definitive flex PCB pricing without evaluating a specific set of requirements. However, the following ranges can serve as a general price guide based on typical specs:
Flex PCB Specs | Typical Price Range |
---|---|
2-4 layer;<br>100mm x 100mm size;<br>FR-4, 1 oz copper;<br>No coverlay;<br>0.2mm features; | Prototyping (1-50 pcs): $200 – $500 per board<br><br>Small pre-production (50-500 pcs): $50 – $150 per board<br><br>Volume production (1,000+ pcs): $20 – $50 per board |
2-4 layer;<br>250mm x 250mm;<br>Polyimide, 1 oz copper;<br>Coverlay 1 side;<br>0.15mm features; | Prototyping (1-50 pcs): $500 – $1,000 per board<br><br>Small pre-production (50-500 pcs): $150 – $250 per board<br><br>Volume production (1,000+ pcs): $50 – $100 per board |
6-8 layers;<br> 400mm x 500mm;<br>Polyimide, 1oz copper;<br>Laminate coverlayers 2 sides;<br>0.1mm features;<br>Blind/buried vias; | Prototyping (1-10 pcs): $2,000 – $4,000 per board<br><br>Pre-production (25-100 pcs): $500 – $1,000 per board<br><br>Volume production (500+ pcs): $200 – $400 per board |
These price ranges assume standard prototypes with minimal NRE charges from the supplier. Prices may be higher for highly complex designs requiring significant engineering development work.
Flex PCB Pricing Trends
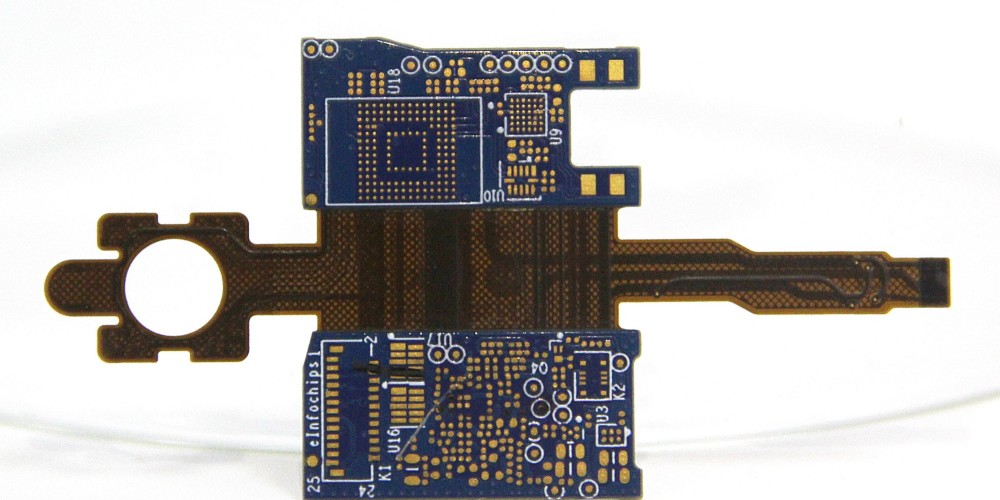
Several trends are impacting flex PCB pricing:
- Increasing circuit densities: Continued miniaturization and higher densities lead to more complex flex PCBs, driving prices upward.
- Advanced materials: New substrates, cover layers and other innovations allow more capabilities but cost more than standard options.
- Improved manufacturing capabilities: Advanced machinery, automation and processes enable more precision and complexity, but increase capex costs for suppliers.
- Consolidation among suppliers: Industry consolidation results in larger suppliers who enjoy economies of scale. However, reduced competition sometimes enables price increases.
- Offshoring production: Many North American and European suppliers have moved production to China and Southeast Asia seeking lower labor costs. However, this trend has slowed recently due to IP concerns and shifting politics.
- Higher raw material expenses: Copper and oil/gas price fluctuations lead to higher costs for key flex PCB inputs like copper foil, polyimide films and acrylic adhesives. These increases get passed along to customers.
On balance, these factors tend to push flex PCB pricing higher over time, though competition helps keep manufacturers from raising prices unduly. Typical annual price increases range from 3-8%.
Ways to Reduce Flex PCB Costs
Here are some tips to lower costs when sourcing flex PCBs:
- Review design to minimize layers, features sizes, tolerances wherever possible
- Specify industry standard materials rather than exotic or custom options
- Utilize design guidelines from supplier to avoid unnecessary cost drivers
- Leverage templating/panelization to maximize board size for better economies of scale
- Partner with supplier early in design process to optimize for manufacturability
- Use supplier’s DFM check to identify any “red flags” that may increase cost
- Consider flex-rigid boards to eliminate interconnects between separate PCBs
- Look for tradeoffs between redundant components vs. cheaper PCB solutions
- Order larger quantities when moving to full production to get volume discounts
- Negotiate pricing for committed forecasts rather than one-off purchase orders
- Cultivate multiple supplier relationships to encourage competition
- Be flexible on lead times to get better pricing from supplier’s available capacity
- Take advantage of supplier NRE discounts for follow-on designs reusing initial tooling
Carefully optimizing the design, specifications, order quantities and purchasing strategies for your flex PCB requirements can drive significant cost savings in many cases. Partnering closely with your chosen supplier is also key to striking the right balance of cost, capabilities and delivery schedule for your specific program needs.
Flex PCB Cost Reduction Example
Here is an example illustrating how an optimized design and procurement approach can reduce flex PCB costs:
Initial design:
- 6 layer flex PCB
- 150 x 350 mm size
- 25μm line/space
- 0.15mm via holes
- 0.076mm finished thickness
- FR-4 dielectric
- 1 oz copper
- 275 pcs needed
- 2 week lead time requested
Initial quote:
$4,125 total ($15 per board)
Cost reductions achieved:
- Changed design to 4 layers by optimizing component placement
- Increased line width to 100μm minimum
- Increased via hole size to 0.2mm
- Adjusted thickness to 0.1mm standard
- Selected polyimide dielectric for better flexibility
- Ordered 500 pcs to get volume discount
- Accepted 4 week lead time for lower cost fabrication queue
- Took advantage of supplier NRE discount on follow-on order
Final quote:
$2,250 total ($4.50 per board)
Total cost reduction:
45% cost savings!
This example illustrates the significant reductions in flex PCB pricing that are often possible through an optimized design and purchasing approach. Taking the time to carefully review every aspect of the flex board requirements, and collaborating with an experienced supplier to tailor the solution to the application’s needs, can yield major savings over an unoptimized design and buying process.
Frequently Asked Questions
Here are answers to some common questions about flex PCB pricing:
Q: How can I estimate pricing for a new flex PCB design?
A: Contact 2-3 reputable flex PCB suppliers and provide them with your preliminary requirements – they will often provide free design reviews and budgetary pricing to win your business. Use the cost factors above to identify areas to optimize in order to reduce unnecessary costs.
Q: Should I expect large NRE charges the first time I order from a supplier?
A: Most suppliers waive or reduce NRE for prototype quantities. Expect moderate one-time NRE fees when moving to full production volumes, typically a few thousand dollars depending on complexity. This covers their engineering review time and initial tooling.
Q: Is it less expensive to order flex PCBs directly from China rather than US/EU sources?
A: In years past, direct China sourcing yielded significant cost savings, though often with higher risk. These pricing gaps have narrowed as North American and European suppliers have moved their volume production offshore. When factoring in shipping, duty, and IP protection considerations, the savings may be minimal or even nonexistent in many cases.
Q: How can I get accurate pricing without spending weeks finalizing my design first?
A: Experienced suppliers can provide budgetary estimates based on preliminary details, with the caveat that pricing may change if requirements shift significantly. Aim to define the key parameters like layers, board size, line widths, quantities, etc before requesting quotes.
Q: Are flex PCBs always more expensive than rigid PCBs?
A: The base materials for flex PCBs tend to be more costly than rigid FR-4 boards. However, flex PCBs can sometimes avoid the need for multiple rigid PCBs, connectors and cables – the total system cost may be lower in some designs when using flex technology appropriately.
Q: When do higher quantities start to yield meaningful cost reductions?
A: You will see gradual price drops as volumes increase from prototypes up to about 500 pcs. Beyond 500-1000 pcs is where scaling effects typically deliver major cost decreases with each quantity increment. Plan production needs carefully to optimize cost.
Conclusion
Flex PCB pricing ultimately comes down to optimizing design requirements, procurement strategies and supplier selection to minimize total cost while still meeting functionality and reliability needs. By researching pricing trends, leveraging supplier expertise and applying the guidelines in this article, engineers can drive sizable reductions in flex PCB costs. Careful attention to cost considerations during requirements definition, design and sourcing processes pays major dividends in flex PCB budget management.