How PCB Transformers Work
PCB transformers operate on the principle of electromagnetic induction. They consist of two or more coils of wire, typically referred to as the primary and secondary windings, which are wound around a common magnetic core. When an alternating current (AC) is applied to the primary winding, it creates a magnetic field that induces a voltage in the secondary winding. This allows for the transfer of electrical energy from one circuit to another, while also providing electrical isolation between the two circuits.
Key Components of a PCB Transformer
-
Primary Winding: The primary winding is the input side of the transformer, which receives the AC voltage from the power source.
-
Secondary Winding: The secondary winding is the output side of the transformer, which provides the transformed voltage to the load.
-
Magnetic Core: The magnetic core is the material around which the windings are wrapped. It is typically made of ferromagnetic materials such as ferrite or laminated steel, which help to concentrate and guide the magnetic field.
-
Insulation: The windings and the core are insulated from each other to prevent short circuits and ensure proper operation of the transformer.
Types of PCB Transformers
There are several types of PCB transformers, each designed for specific applications and requirements.
1. Step-Up Transformers
Step-up transformers are used to increase the voltage from the primary winding to the secondary winding. They have more turns in the secondary winding than in the primary winding, resulting in a higher output voltage.
2. Step-Down Transformers
Step-down transformers are used to decrease the voltage from the primary winding to the secondary winding. They have fewer turns in the secondary winding than in the primary winding, resulting in a lower output voltage.
3. Isolation Transformers
Isolation transformers are designed to provide electrical isolation between the primary and secondary windings. They have a 1:1 turns ratio, meaning that the input and output voltages are the same. Isolation transformers are used to protect sensitive electronic components from voltage spikes, noise, and other disturbances in the power supply.
4. Multiple Winding Transformers
Multiple winding transformers have more than two windings, allowing for multiple input or output voltages. They are commonly used in power supplies and other applications that require multiple voltage levels.
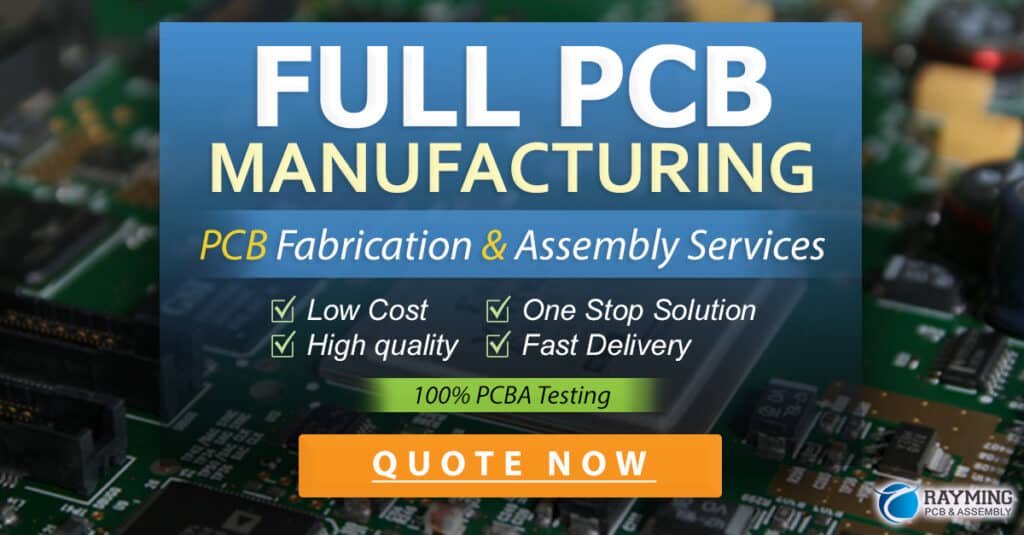
Advantages of PCB Transformers
PCB transformers offer several advantages over traditional transformers:
-
Compact Size: PCB transformers are designed to be mounted directly on a printed circuit board, making them much smaller and more compact than traditional transformers. This allows for more efficient use of space in electronic devices.
-
High Efficiency: PCB transformers are designed to minimize losses and maximize efficiency. They typically have lower leakage inductance and higher coupling factors than traditional transformers, resulting in better power transfer and less heat generation.
-
Ease of Integration: PCB transformers are easy to integrate into electronic circuits, as they can be soldered directly onto the PCB. This eliminates the need for additional wiring and connectors, simplifying the assembly process and reducing the risk of connection failures.
-
Cost-Effective: Due to their compact size and ease of integration, PCB transformers are often more cost-effective than traditional transformers. They require less material and labor to manufacture, and their standardized designs allow for high-volume production.
Applications of PCB Transformers
PCB transformers are used in a wide range of electronic devices and systems, including:
-
Power Supplies: PCB transformers are commonly used in power supplies to step down high voltage AC to low voltage DC, which can then be used to power electronic components.
-
Isolation: PCB transformers provide electrical isolation between different sections of a circuit, preventing ground loops, noise, and other interference from propagating between circuits.
-
Signal Conditioning: PCB transformers can be used to match impedances, filter noise, and amplify or attenuate signals in electronic circuits.
-
Telecommunications: PCB transformers are used in telecommunications equipment to couple signals between different stages of a circuit, while providing electrical isolation and impedance matching.
-
Automotive Electronics: PCB transformers are used in various automotive electronic systems, such as engine control units, infotainment systems, and lighting controls.
-
Medical Devices: PCB transformers are used in medical devices to provide isolation between patient-connected circuits and other parts of the device, ensuring patient safety and preventing electrical shock.
Choosing the Right PCB Transformer
When selecting a PCB transformer for a specific application, several factors should be considered:
-
Power Requirements: The transformer must be capable of handling the required power levels, both in terms of voltage and current.
-
Frequency: The transformer must be designed to operate at the required frequency, which can range from a few hertz to several megahertz depending on the application.
-
Isolation: The transformer must provide the necessary level of electrical isolation between the primary and secondary windings, depending on the safety and performance requirements of the application.
-
Size and Mounting: The transformer must fit within the available space on the PCB and be compatible with the chosen mounting method (e.g., through-hole or surface-mount).
-
Environmental Factors: The transformer must be able to withstand the expected environmental conditions, such as temperature, humidity, and vibration, without degrading in performance or reliability.
Designing with PCB Transformers
When designing a circuit that incorporates a PCB transformer, several best practices should be followed to ensure optimal performance and reliability:
-
Placement: The transformer should be placed as close as possible to the components it is powering or isolating, to minimize the length of the connecting traces and reduce the risk of noise pickup or signal loss.
-
Grounding: Proper grounding techniques should be used to minimize ground loops and other sources of noise that can affect the performance of the transformer and the overall circuit.
-
Shielding: In some cases, it may be necessary to shield the transformer or the surrounding components to prevent electromagnetic interference (EMI) from affecting the circuit or from radiating out to other devices.
-
thermal management: PCB transformers generate heat during operation, which must be properly dissipated to prevent overheating and ensure reliable long-term performance. Adequate cooling measures, such as heatsinks or forced air cooling, should be provided if necessary.
PCB Transformer Manufacturing Process
PCB transformers are manufactured using a combination of winding, assembly, and testing processes.
-
Winding: The primary and secondary windings are wound around the magnetic core using automated winding machines. The number of turns, wire gauge, and winding pattern are carefully controlled to achieve the desired electrical characteristics.
-
Assembly: The wound transformer is then assembled onto a PCB carrier, which provides the necessary mechanical support and electrical connections. The transformer may be secured to the carrier using adhesive, soldering, or other methods.
-
Encapsulation: In some cases, the transformer may be encapsulated in a protective material, such as epoxy or silicone, to provide additional mechanical and environmental protection.
-
Testing: The completed transformer is then tested to ensure that it meets the specified electrical and performance requirements. This may include tests for inductance, resistance, turns ratio, insulation resistance, and other parameters.
Future Trends in PCB Transformers
As electronic devices continue to become smaller, more complex, and more energy-efficient, PCB transformers are evolving to meet these challenges.
-
High-Frequency Transformers: The demand for high-frequency PCB transformers is increasing, driven by the growth of wireless communication and high-speed digital systems. These transformers are designed to operate at frequencies of several megahertz or even gigahertz, enabling faster data transfer and more efficient power conversion.
-
High-Power Density: There is a growing need for PCB transformers that can handle higher power levels in smaller packages. This is being achieved through the use of advanced materials, such as high-permeability ferrites and low-loss conductors, as well as innovative winding and assembly techniques.
-
Integration with Other Components: PCB transformers are increasingly being integrated with other components, such as capacitors and inductors, to create complete power conversion modules. These modules offer improved performance, reliability, and ease of use compared to discrete components.
-
Automation and Standardization: The manufacturing process for PCB transformers is becoming increasingly automated and standardized, enabling faster production times, lower costs, and more consistent quality. This is being driven by the adoption of advanced manufacturing technologies, such as 3D printing and robotic assembly.
Frequently Asked Questions (FAQ)
-
What is the difference between a PCB transformer and a traditional transformer?
A PCB transformer is designed to be mounted directly on a printed circuit board, making it more compact and easier to integrate into electronic circuits than a traditional transformer. PCB transformers also typically have lower leakage inductance and higher coupling factors, resulting in better power transfer and less heat generation. -
Can PCB transformers be used for high-voltage applications?
Yes, PCB transformers can be designed for high-voltage applications, such as in power supplies and isolation circuits. However, special consideration must be given to the insulation and safety requirements of high-voltage transformers, and appropriate safety standards must be followed. -
How do I choose the right PCB transformer for my application?
When choosing a PCB transformer, consider factors such as power requirements, frequency, isolation, size and mounting, and environmental factors. Consult with the transformer manufacturer or a qualified engineer to select the most appropriate transformer for your specific application. -
Can PCB transformers be custom-designed for specific applications?
Yes, PCB transformers can be custom-designed to meet the specific requirements of a particular application. This may involve modifying the winding configuration, core material, or other parameters to achieve the desired electrical and performance characteristics. -
What are the main failure modes of PCB transformers?
The main failure modes of PCB transformers include insulation breakdown, winding shorts or opens, core saturation or damage, and overheating. These failures can be caused by factors such as voltage spikes, overcurrent, physical damage, or environmental stress. Proper design, manufacturing, and use of PCB transformers can help to minimize the risk of these failures.
Transformer Type | Description | Typical Applications |
---|---|---|
Step-Up | Increases voltage from primary to secondary | High-voltage power supplies, ignition systems |
Step-Down | Decreases voltage from primary to secondary | Low-voltage power supplies, battery charging |
Isolation | Provides electrical isolation between windings | Medical devices, telecommunications, safety circuits |
Multiple Winding | Has more than two windings for multiple voltages | Complex power supplies, multi-voltage systems |
In conclusion, PCB transformers are essential components in many electronic devices and systems, enabling efficient power transfer and isolation while offering advantages such as compact size, high efficiency, and ease of integration. As electronic technologies continue to advance, PCB transformers will play an increasingly important role in enabling the development of smaller, faster, and more energy-efficient devices.