Characteristics of White PCBs
Solder Mask Color
The most distinguishing feature of a white PCB is its white solder mask. Solder mask is a protective layer applied to the copper traces on a PCB to prevent oxidation and provide electrical insulation. While green is the most common color for solder masks, white PCBs utilize a special white-colored solder mask.
Substrate Material
White PCBs can be fabricated using various substrate materials, such as FR-4, Rogers, or aluminum. The choice of substrate depends on the specific requirements of the application, including thermal conductivity, dielectric constant, and mechanical stability.
Copper Thickness
The copper thickness on a white PCB can vary depending on the desired current carrying capacity and signal integrity. Standard copper thicknesses include 1 oz (35 μm), 2 oz (70 μm), and 3 oz (105 μm). Thicker copper layers are used for high-power applications or to improve thermal dissipation.
Layer Count
White PCBs can be manufactured as single-layer, double-layer, or multi-layer boards. The number of layers depends on the complexity of the circuit design and the required functionality. Multi-layer white PCBs are commonly used in advanced electronic devices where high density and signal integrity are critical.
Manufacturing Process of White PCBs
PCB Design
The manufacturing process of a white PCB begins with the circuit design. Engineers use specialized software to create schematic diagrams and layout the PCB, taking into account the component placement, signal routing, and design rules.
PCB Fabrication
Once the design is finalized, the PCB fabrication process starts. The main steps involved in PCB fabrication are:
-
Copper Clad Laminate Preparation: The substrate material is cut to the desired size, and copper foil is laminated onto both sides of the substrate using heat and pressure.
-
Drilling: Holes are drilled through the PCB to accommodate through-hole components and provide electrical connections between layers.
-
Patterning: The copper layer is selectively removed to create the desired circuit pattern. This is typically done using photolithography and etching processes.
-
Plating: The drilled holes and exposed copper areas are plated with a thin layer of copper to improve conductivity and protect against oxidation.
-
Solder Mask Application: The white solder mask is applied to the PCB, covering the copper traces while leaving the pads and other exposed areas uncovered.
-
Surface Finish: A surface finish, such as HASL (Hot Air Solder Leveling), ENIG (Electroless Nickel Immersion Gold), or OSP (Organic Solderability Preservative), is applied to the exposed pads to enhance solderability and prevent oxidation.
-
Silkscreen: The silkscreen layer is added to the PCB to provide component labels, logos, and other markings.
-
Electrical Testing: The manufactured PCB undergoes electrical testing to ensure proper functionality and adherence to design specifications.
Quality Control
Stringent quality control measures are implemented throughout the manufacturing process to ensure the reliability and performance of white PCBs. Visual inspections, automated optical inspections (AOI), and electrical testing are performed to detect and rectify any defects or inconsistencies.
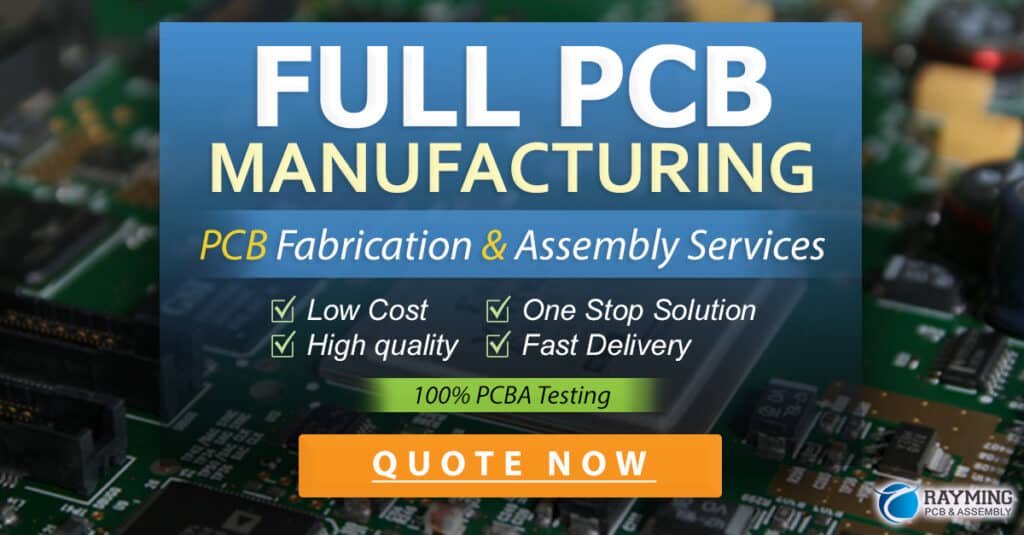
Applications of White PCBs
White PCBs find applications in various industries and products where aesthetics, reflectivity, or specific functionality are required. Some common applications include:
LED Lighting
White PCBs are extensively used in LED lighting applications, such as LED bulbs, LED strips, and LED panels. The white solder mask enhances the reflectivity of the PCB, leading to improved light distribution and efficiency. The white color also provides a clean and attractive appearance to the lighting fixtures.
Consumer Electronics
White PCBs are used in consumer electronic devices, such as smartphones, tablets, and wearables. The white color gives a premium and sleek look to the devices, enhancing their visual appeal. White PCBs also offer better contrast for component labels and markings, making them easier to identify during assembly and repair.
Medical Devices
In medical devices, white PCBs are preferred for their clean and hygienic appearance. The white color symbolizes cleanliness and sterility, which is crucial in medical applications. White PCBs are used in various medical equipment, including patient monitors, diagnostic devices, and imaging systems.
Automotive Electronics
White PCBs are increasingly used in automotive electronics, particularly in interior lighting and infotainment systems. The white color complements the modern and sophisticated interiors of vehicles, providing a premium look and feel. White PCBs also offer improved visibility for indicators and displays in automotive applications.
Industrial Control Systems
White PCBs are utilized in industrial control systems, such as process control panels, automation equipment, and monitoring devices. The white color enhances the visibility of components and markings, making it easier for technicians to identify and troubleshoot issues. White PCBs also provide a clean and professional appearance to industrial control systems.
Benefits of White PCBs
Enhanced Aesthetics
One of the primary benefits of white PCBs is their enhanced aesthetics. The white color gives a clean, modern, and sophisticated look to electronic devices. It offers a visually appealing contrast to components and markings, making the PCB design more attractive and professional.
Improved Reflectivity
White PCBs exhibit excellent reflectivity, which is particularly advantageous in LED lighting applications. The white solder mask reflects light more efficiently than traditional green PCBs, resulting in better light distribution and increased luminous efficiency. This reflectivity also helps in reducing light absorption and minimizing hot spots in LED lighting fixtures.
Better Contrast and Visibility
The white background of white PCBs provides better contrast for component labels, markings, and silk-screen designs. This improved visibility makes it easier for assembly operators and technicians to identify components, reducing the chances of errors during the manufacturing process. The enhanced contrast also facilitates easier inspection and troubleshooting of the assembled PCBs.
Compatibility with Various Components
White PCBs are compatible with a wide range of electronic components, including surface mount devices (SMDs) and through-hole components. The white solder mask does not interfere with the soldering process or the electrical performance of the components. White PCBs can accommodate various package sizes and types, making them suitable for diverse applications.
Customization Options
White PCBs offer excellent customization options to meet specific design requirements. The white solder mask can be selectively applied to certain areas of the PCB, creating unique patterns or exposing copper traces for aesthetic purposes. Additionally, the silkscreen layer can be customized with logos, text, or graphics in different colors to enhance branding or provide additional information.
Frequently Asked Questions (FAQ)
-
Q: Are white PCBs more expensive than traditional green PCBs?
A: Yes, white PCBs are generally more expensive than green PCBs. The white solder mask material and the specialized manufacturing process contribute to the higher cost. However, the cost difference is justified by the enhanced aesthetics, reflectivity, and other benefits offered by white PCBs. -
Q: Can white PCBs be used for high-frequency applications?
A: Yes, white PCBs can be used for high-frequency applications. The choice of substrate material, such as Rogers or Teflon, determines the suitability of white PCBs for high-frequency designs. The white solder mask itself does not have a significant impact on the high-frequency performance of the PCB. -
Q: Are there any limitations or challenges in manufacturing white PCBs?
A: One challenge in manufacturing white PCBs is ensuring the consistency and uniformity of the white solder mask. The white color can be affected by factors such as the curing process, material batch variations, and environmental conditions. Strict process control and quality assurance measures are necessary to maintain the desired white color and finish. -
Q: Can white PCBs be used for outdoor applications?
A: White PCBs can be used for outdoor applications, but additional considerations must be taken into account. The white solder mask should be UV-resistant and able to withstand exposure to sunlight and weather conditions. Conformal coating or encapsulation can be applied to provide additional protection against moisture, dust, and other environmental factors. -
Q: Are there any special handling or storage requirements for white PCBs?
A: White PCBs do not have any specific handling or storage requirements compared to traditional green PCBs. However, it is important to handle them with care to avoid scratches, fingerprints, or contamination that may be more noticeable on the white surface. Proper packaging and storage in a clean, dry environment are recommended to maintain the quality and appearance of white PCBs.
Conclusion
White PCBs offer a unique combination of aesthetics and functionality, making them a popular choice for various electronic applications. With their distinctive white solder mask, enhanced reflectivity, and improved contrast, white PCBs provide a clean and modern look to electronic devices. The manufacturing process of white PCBs involves specialized techniques to achieve the desired white color and finish.
White PCBs find extensive use in LED lighting, consumer electronics, medical devices, automotive electronics, and industrial control systems. They offer benefits such as enhanced aesthetics, improved reflectivity, better visibility, compatibility with various components, and customization options. While white PCBs may have a higher cost compared to traditional green PCBs, the benefits they offer justify the investment.
As technology advances and the demand for visually appealing and high-performance electronic products increases, white PCBs are likely to gain even more popularity. With their versatility and aesthetic appeal, white PCBs are set to play a significant role in shaping the future of electronic design and manufacturing.