Understanding PCB Surface Finish
In the world of printed circuit boards (PCBs), the term “surface finish” refers to the coating applied to the copper traces and pads on the board. The purpose of this coating is to protect the copper from oxidation, enhance solderability, and improve the overall reliability of the PCB. Choosing the right PCB surface finish is crucial for ensuring the proper functioning and longevity of electronic devices.
Types of PCB Surface Finishes
There are several types of surface finishes available, each with its own advantages and disadvantages. Some of the most common PCB surface finishes include:
- Hot Air Solder Leveling (HASL)
- Electroless Nickel Immersion Gold (ENIG)
- Immersion Silver (IAg)
- Immersion Tin (ISn)
- Organic Solderability Preservative (OSP)
Let’s take a closer look at each of these surface finishes.
1. Hot Air Solder Leveling (HASL)
HASL is one of the most widely used surface finishes in the PCB industry. The process involves dipping the PCB into a molten solder bath and then using hot air to level the solder on the surface. This creates a thin, uniform layer of solder on the copper traces and pads.
Advantages of HASL:
– Cost-effective
– Excellent solderability
– Good shelf life
– Suitable for both through-hole and surface mount components
Disadvantages of HASL:
– Uneven surface due to solder dipping process
– Not suitable for fine-pitch components
– Potential for thermal shock during the process
2. Electroless Nickel Immersion Gold (ENIG)
ENIG is a two-layer surface finish that consists of a thin layer of gold over a layer of nickel. The nickel layer provides a barrier between the copper and the gold, while the gold layer offers excellent solderability and protection against oxidation.
Advantages of ENIG:
– Flat and uniform surface
– Excellent solderability
– Good shelf life
– Suitable for fine-pitch components
– Resistant to multiple reflow cycles
Disadvantages of ENIG:
– Higher cost compared to other surface finishes
– Potential for “black pad” defect due to improper plating process
– Not suitable for press-fit connectors
3. Immersion Silver (IAg)
Immersion silver is a single-layer surface finish that involves depositing a thin layer of silver directly onto the copper surface. It offers good solderability and is often used as a more cost-effective alternative to ENIG.
Advantages of IAg:
– Lower cost compared to ENIG
– Good solderability
– Suitable for fine-pitch components
– Flat and uniform surface
Disadvantages of IAg:
– Limited shelf life due to silver tarnishing
– Not suitable for environments with high levels of sulfur
– Potential for silver migration in high-humidity environments
4. Immersion Tin (ISn)
Immersion tin is another single-layer surface finish that involves depositing a thin layer of tin directly onto the copper surface. It offers good solderability and is often used in applications where lead-free soldering is required.
Advantages of ISn:
– Good solderability
– Suitable for lead-free soldering
– Flat and uniform surface
– Lower cost compared to ENIG
Disadvantages of ISn:
– Limited shelf life due to tin whiskers formation
– Not suitable for environments with high levels of mechanical stress
– Potential for tin diffusion into the copper layer
5. Organic Solderability Preservative (OSP)
OSP is a single-layer organic coating that is applied directly onto the copper surface. It acts as a barrier against oxidation and provides good solderability. OSP is often used in applications where the PCB needs to be stored for an extended period before assembly.
Advantages of OSP:
– Cost-effective
– Good solderability
– Suitable for fine-pitch components
– Flat and uniform surface
– Environmentally friendly
Disadvantages of OSP:
– Limited shelf life due to the gradual degradation of the organic coating
– Not suitable for multiple reflow cycles
– Potential for poor wetting during soldering
Comparison of PCB Surface Finishes
Surface Finish | Cost | Solderability | Shelf Life | Fine-Pitch Compatibility | Multiple Reflow Cycles |
---|---|---|---|---|---|
HASL | Low | Excellent | Good | Poor | Good |
ENIG | High | Excellent | Excellent | Excellent | Excellent |
IAg | Moderate | Good | Limited | Good | Good |
ISn | Moderate | Good | Limited | Good | Poor |
OSP | Low | Good | Limited | Good | Poor |
Factors to Consider When Choosing a PCB Surface Finish
When selecting a surface finish for your PCB, there are several factors to consider:
-
Application requirements: Consider the specific needs of your application, such as the type of components being used, the environment in which the PCB will operate, and the expected lifespan of the device.
-
Cost: Different surface finishes have varying costs, so it’s essential to balance your budget with the required performance characteristics.
-
Solderability: Choose a surface finish that provides good solderability to ensure reliable connections between components and the PCB.
-
Shelf life: If your PCBs need to be stored for an extended period before assembly, opt for a surface finish with a longer shelf life, such as ENIG or HASL.
-
Fine-pitch compatibility: For applications using fine-pitch components, select a surface finish that offers a flat and uniform surface, such as ENIG, IAg, or OSP.
-
Multiple reflow cycles: If your manufacturing process involves multiple reflow cycles, choose a surface finish that can withstand the repeated exposure to high temperatures, such as ENIG.
Frequently Asked Questions (FAQ)
-
Q: What is the most cost-effective PCB surface finish?
A: HASL and OSP are generally the most cost-effective surface finishes, while ENIG tends to be the most expensive. -
Q: Which surface finish is best for applications requiring lead-free soldering?
A: Immersion tin (ISn) is often used in applications where lead-free soldering is required, as it offers good solderability and compatibility with lead-free solder alloys. -
Q: What is the “black pad” defect associated with ENIG?
A: The “black pad” defect is a phenomenon that can occur during the ENIG plating process, where the nickel layer separates from the copper surface, resulting in a dark appearance and poor solderability. -
Q: Can OSP be used for PCBs that undergo multiple reflow cycles?
A: OSP is not recommended for PCBs that undergo multiple reflow cycles, as the organic coating can degrade during repeated exposure to high temperatures, leading to poor solderability. -
Q: Which surface finish is best suited for fine-pitch components?
A: ENIG, IAg, and OSP are well-suited for fine-pitch components, as they provide a flat and uniform surface that allows for precise placement and soldering of small components.
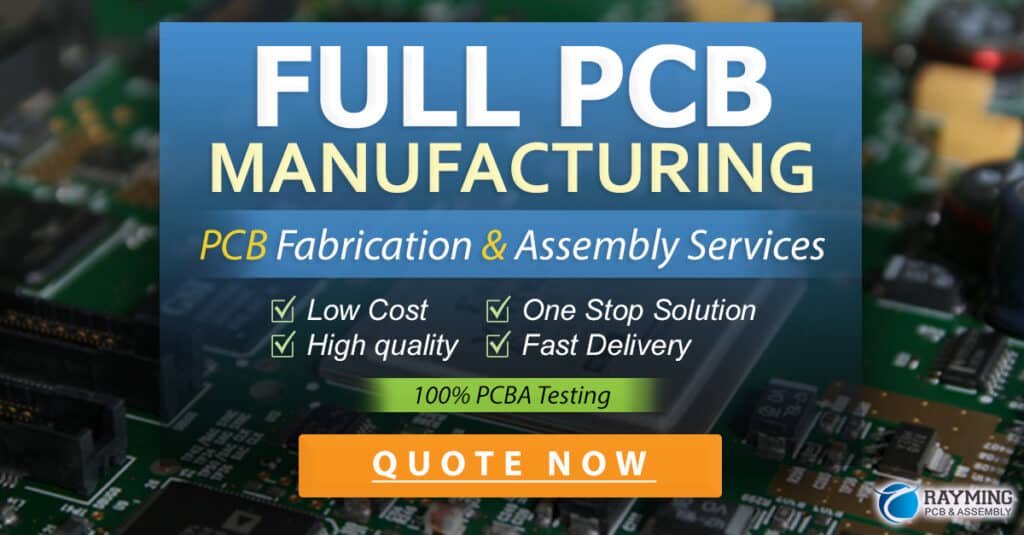
Conclusion
Choosing the right PCB surface finish is crucial for ensuring the reliability, solderability, and longevity of your electronic devices. By understanding the advantages and disadvantages of each surface finish and considering the specific requirements of your application, you can make an informed decision that balances cost, performance, and manufacturability.
As technology continues to advance, new surface finishes may emerge, offering even better performance and cost-effectiveness. Staying up-to-date with the latest developments in PCB surface finishes will help you stay ahead of the curve and ensure that your products remain competitive in the ever-evolving world of electronics.