The Importance of Quick Turn PCB Assembly
In today’s fast-paced technological landscape, time-to-market is a critical factor in the success of electronic products. Quick turn PCB assembly plays a vital role in accelerating the development process by providing the following benefits:
-
Rapid prototyping: Quick turn assembly enables designers and engineers to test and validate their designs quickly, allowing for faster iterations and improvements.
-
Reduced time-to-market: By minimizing the time spent on pcb fabrication and assembly, companies can launch their products faster, gaining a competitive edge in the market.
-
Cost-effective low-volume production: For small-batch production or prototype runs, quick turn assembly offers a cost-effective solution compared to traditional high-volume production methods.
The Quick Turn PCB Assembly Process
The quick turn PCB assembly process involves several key steps that are optimized for speed and efficiency:
1. PCB Design and File Preparation
The first step in the quick turn assembly process is to design the PCB using specialized software such as Altium Designer, Eagle, or KiCad. The design files, typically in Gerber format, are then prepared for manufacturing. This includes generating the necessary files for each layer of the PCB, such as the copper layers, solder mask, and silkscreen.
2. PCB Fabrication
Once the design files are ready, the PCB fabrication process begins. This involves the following sub-steps:
a. Material selection: The appropriate PCB substrate material, such as FR-4, is selected based on the design requirements.
b. Copper etching: The copper layers are etched onto the substrate using a photolithographic process, which transfers the circuit pattern from the design files onto the board.
c. Drilling: Holes are drilled into the board for through-hole components and vias, which connect different layers of the PCB.
d. Solder mask application: A protective solder mask is applied to the board, leaving exposed areas for component soldering and preventing short circuits.
e. Silkscreen printing: The component labels and other markings are printed onto the board using a silkscreen process.
3. PCB Assembly
After the fabrication process, the PCB is ready for assembly. The quick turn assembly process typically involves the following steps:
a. Solder paste application: Solder paste is applied to the pads on the PCB where components will be placed. This is typically done using a stencil and a solder paste printer.
b. Component placement: The components are placed onto the PCB using a pick-and-place machine, which accurately positions each component based on the design files.
c. Reflow soldering: The PCB with the placed components is then passed through a reflow oven, which melts the solder paste and creates a strong electrical and mechanical connection between the components and the board.
d. Inspection and testing: The assembled PCB undergoes visual inspection and automated optical inspection (AOI) to ensure that all components are properly placed and soldered. Electrical testing is also performed to verify the functionality of the board.
4. Shipping and Delivery
Once the assembled PCBs have passed inspection and testing, they are packaged and shipped to the customer. Quick turn assembly providers often offer expedited shipping options to ensure that the boards reach the customer as quickly as possible.
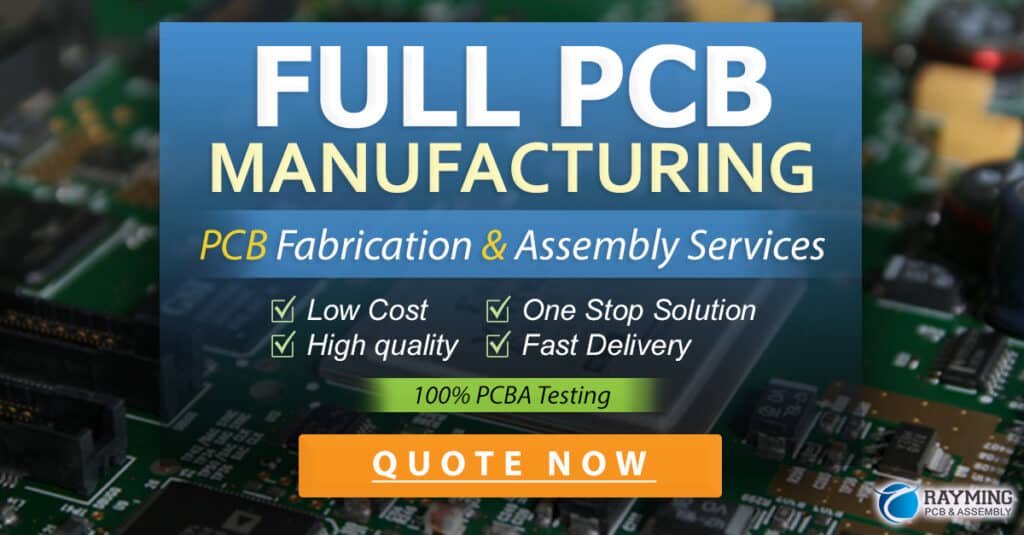
Factors Affecting Quick Turn PCB Assembly Timeframes
Several factors can impact the turnaround time for quick turn PCB assembly:
-
Design complexity: More complex designs with higher layer counts, smaller feature sizes, or advanced technologies like HDI (High Density Interconnect) may require additional time for fabrication and assembly.
-
Material availability: The availability of specific substrate materials, components, or surface finishes can affect the lead time for quick turn assembly.
-
Quantity: While quick turn assembly is well-suited for low-volume production, larger quantities may require more time for fabrication and assembly.
-
Workload and capacity: The current workload and capacity of the quick turn assembly provider can impact the turnaround time, especially during periods of high demand.
Choosing a Quick Turn PCB Assembly Provider
When selecting a quick turn PCB assembly provider, consider the following factors:
-
Capabilities: Ensure that the provider has the necessary equipment, expertise, and certifications to handle your specific PCB design and assembly requirements.
-
Turnaround time: Look for providers that offer the fastest turnaround times that meet your project deadlines. Some providers offer 24-hour or 48-hour expedited services for critical projects.
-
Quality control: Choose a provider with a robust quality control process, including automated optical inspection (AOI), X-ray inspection, and electrical testing, to ensure the reliability and functionality of your assembled PCBs.
-
Customer support: Select a provider with responsive and knowledgeable customer support to assist you throughout the quick turn assembly process, from design review to final delivery.
-
Pricing: Compare pricing from multiple providers to ensure that you are getting a competitive price for your quick turn assembly project. Keep in mind that the lowest price may not always offer the best value in terms of quality, reliability, and customer support.
Quick Turn PCB Assembly Technologies and Capabilities
Quick turn PCB assembly providers often offer a range of technologies and capabilities to accommodate different design requirements:
Technology/Capability | Description |
---|---|
SMT (Surface Mount Technology) | Components are mounted directly onto the surface of the PCB, enabling smaller board sizes and higher component density. |
Through-Hole Technology | Components with leads are inserted into drilled holes in the PCB and soldered on the opposite side. |
Mixed Technology | A combination of SMT and through-hole components on a single PCB. |
HDI (High Density Interconnect) | PCBs with fine pitch components, micro-vias, and high layer counts for advanced applications. |
Flexible and Rigid-Flex PCBs | PCBs that can flex or bend, often used in wearable electronics, aerospace, and medical devices. |
Multilayer PCBs | PCBs with multiple layers of copper interconnects, enabling more complex designs and higher component density. |
Impedance Control | Precise control of the impedance of PCB traces, critical for high-speed and RF applications. |
Conformal Coating | A protective coating applied to the PCB to protect against moisture, dust, and other environmental factors. |
Advantages of Quick Turn PCB Assembly over Traditional Assembly
Quick turn PCB assembly offers several advantages over traditional assembly methods:
-
Faster turnaround times: Quick turn assembly can reduce lead times from weeks to days, enabling faster prototyping, testing, and time-to-market.
-
Lower minimum order quantities: Traditional assembly often requires high minimum order quantities (MOQs), making it cost-prohibitive for low-volume production or prototyping. Quick turn assembly typically has much lower MOQs, making it accessible for a wider range of projects.
-
Reduced inventory costs: With faster turnaround times and lower MOQs, companies can reduce their inventory costs by ordering only what they need when they need it, rather than stockpiling large quantities of PCBs.
-
Faster design iterations: Quick turn assembly enables designers and engineers to test and refine their designs more quickly, leading to faster product development and improvement cycles.
-
Improved cash flow: By reducing lead times and inventory costs, quick turn assembly can help companies improve their cash flow and allocate resources more efficiently.
Quick Turn PCB Assembly Case Studies
Case Study 1: Medical Device Prototyping
A medical device startup needed to quickly prototype a new wearable health monitoring device. By utilizing quick turn PCB assembly, they were able to:
- Receive assembled prototypes within 5 business days
- Test and validate their design quickly
- Iterate on the design based on user feedback
- Bring their product to market 3 months faster than anticipated
Case Study 2: Automotive Electronics Testing
An automotive electronics manufacturer needed to test a new control module for their vehicle’s infotainment system. With quick turn PCB assembly, they were able to:
- Fabricate and assemble 50 test boards within 48 hours
- Perform extensive testing and validation of the new module
- Identify and fix design issues early in the development process
- Avoid costly delays in their production schedule
Frequently Asked Questions (FAQ)
1. What is the minimum order quantity (MOQ) for quick turn PCB assembly?
The minimum order quantity for quick turn PCB assembly varies by provider but is typically much lower than traditional assembly methods. Some providers offer MOQs as low as 1-5 pieces for prototype runs.
2. How much does quick turn PCB assembly cost?
The cost of quick turn PCB assembly depends on factors such as design complexity, material selection, quantity, and turnaround time. In general, quick turn assembly is more expensive per unit than traditional high-volume assembly but offers significant time and cost savings for low-volume production and prototyping.
3. What file formats are required for quick turn PCB assembly?
Most quick turn PCB assembly providers require Gerber files for each layer of the PCB, as well as a bill of materials (BOM) and assembly drawings. Some providers may also accept design files from popular PCB design software such as Altium Designer, Eagle, or KiCad.
4. Can quick turn PCB assembly handle complex designs with high layer counts or HDI features?
Yes, many quick turn PCB assembly providers have the capability to handle complex designs with high layer counts and advanced features like HDI. However, these designs may require additional time for fabrication and assembly compared to simpler designs.
5. What quality control measures are in place for quick turn PCB assembly?
Quick turn PCB assembly providers typically employ a range of quality control measures, including automated optical inspection (AOI), X-ray inspection, and electrical testing. These measures help ensure the reliability and functionality of the assembled PCBs, even with the accelerated turnaround times.
Conclusion
Quick turn PCB assembly is a vital service for businesses and individuals who need fast, reliable, and cost-effective PCB prototyping and low-volume production. By understanding the quick turn assembly process, factors affecting turnaround times, and the advantages over traditional assembly methods, you can make informed decisions when choosing a quick turn assembly provider for your next project.
As technology continues to evolve and time-to-market pressures increase, the demand for quick turn PCB assembly is expected to grow. By leveraging this service, companies can accelerate their product development cycles, reduce costs, and gain a competitive edge in their respective markets.