Introduction to Controlled Impedance PCBs
Printed Circuit Boards (PCBs) are the backbone of modern electronics. They provide a platform for mounting and interconnecting electronic components to create complex circuits. As the demand for high-speed and high-frequency applications grows, the importance of controlling the impedance of PCB traces becomes increasingly critical. This is where controlled impedance PCBs come into play.
What is Impedance?
Before diving into controlled impedance PCBs, let’s first understand what impedance is. Impedance is a measure of the opposition that a circuit presents to the flow of alternating current (AC) at a given frequency. It is a complex quantity that consists of both resistance and reactance. Resistance is the opposition to the flow of current, while reactance is the opposition to the change in current due to capacitance or inductance.
In a PCB, the impedance of a trace is determined by its geometry, the properties of the dielectric material surrounding it, and the frequency of the signal passing through it. When the impedance of a trace matches the impedance of the source and load, maximum power transfer occurs, and signal integrity is maintained.
Why is Controlled Impedance Important?
Controlling the impedance of PCB traces is crucial for several reasons:
-
Signal Integrity: In high-speed digital circuits, impedance mismatches can cause signal reflections, which lead to distortion, ringing, and overshoot. By matching the impedance of the trace to the source and load, these reflections can be minimized, ensuring clean and accurate signal transmission.
-
EMI Reduction: Impedance mismatches can also cause electromagnetic interference (EMI) issues. When a signal encounters an impedance mismatch, some of its energy is reflected back, causing unwanted radiation. Controlling the impedance helps reduce EMI and ensures compliance with electromagnetic compatibility (EMC) regulations.
-
Power Efficiency: In high-frequency applications, such as RF and microwave circuits, impedance matching is essential for efficient power transfer. When the impedance of the trace matches the impedance of the source and load, maximum power is delivered to the load, minimizing power loss and heat generation.
Types of Controlled Impedance PCBs
There are three main types of controlled impedance PCBs:
-
Surface Microstrip: In a surface microstrip configuration, the signal trace is routed on the outer layer of the PCB, with a ground plane beneath it. The impedance is controlled by adjusting the width of the trace and the thickness of the dielectric material between the trace and the ground plane.
-
Stripline: Stripline traces are embedded within the PCB, with ground planes above and below the signal trace. This configuration provides better shielding and reduces crosstalk compared to surface microstrip. The impedance is controlled by adjusting the width of the trace and the spacing between the ground planes.
-
Dual Stripline: Dual stripline is similar to stripline, but it has two signal traces running in parallel, with ground planes above and below them. This configuration is useful for differential signaling, where two complementary signals are transmitted simultaneously. The impedance is controlled by adjusting the width and spacing of the traces, as well as the spacing between the ground planes.
Here’s a table comparing the characteristics of these controlled impedance configurations:
Configuration | Shielding | Crosstalk | Density | Cost |
---|---|---|---|---|
Surface Microstrip | Low | High | High | Low |
Stripline | High | Low | Medium | Medium |
Dual Stripline | High | Low | Low | High |
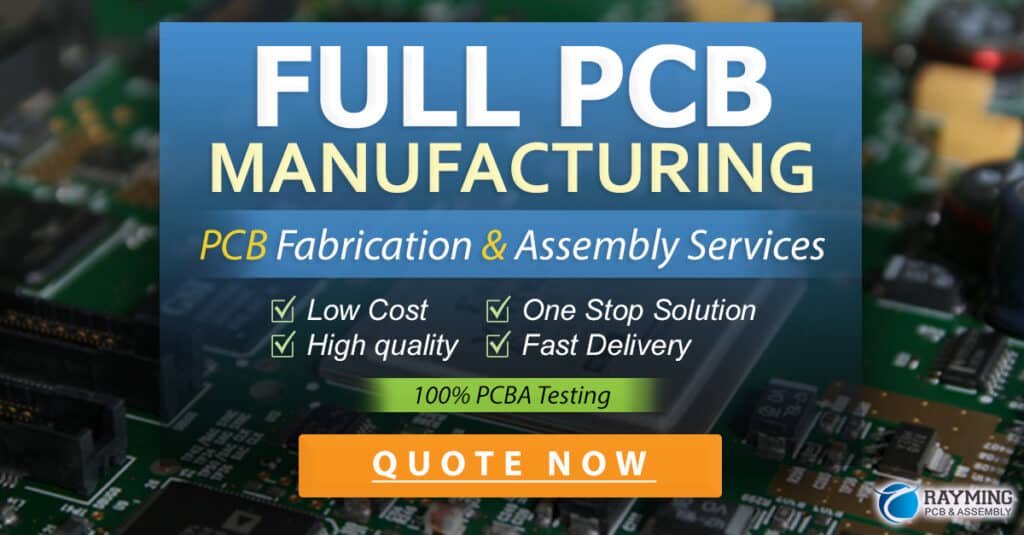
Designing Controlled Impedance PCBs
Designing controlled impedance PCBs requires careful consideration of several factors:
Material Selection
The choice of dielectric material plays a significant role in determining the impedance of a trace. The dielectric constant (Dk) and dissipation factor (Df) of the material affect the propagation velocity and loss of the signal. Common dielectric materials used in controlled impedance PCBs include FR-4, Rogers, and Isola.
Trace Geometry
The width, thickness, and spacing of the traces impact their impedance. Wider traces have lower impedance, while narrower traces have higher impedance. The thickness of the trace also affects its resistance and current-carrying capacity. Spacing between traces is critical to minimize crosstalk and maintain signal integrity.
Stack-up Design
The arrangement of layers in a PCB, known as the stack-up, is crucial for controlled impedance. The position of the signal traces relative to the ground and power planes determines the impedance and shielding effectiveness. A well-designed stack-up ensures consistent impedance throughout the board and minimizes EMI.
Simulation and Modeling
Before manufacturing a controlled impedance PCB, it is essential to simulate and model the design to predict its performance. Electronic design automation (EDA) tools, such as Mentor Graphics HyperLynx and Cadence Allegro, allow designers to analyze the impedance, crosstalk, and signal integrity of the PCB. These simulations help optimize the design and catch potential issues early in the development process.
Manufacturing Controlled Impedance PCBs
Manufacturing controlled impedance PCBs requires stringent process control and specialized equipment. The key aspects of the manufacturing process include:
Lamination
The lamination process involves pressing the layers of the PCB together under high temperature and pressure. Consistent lamination is critical for maintaining uniform dielectric thickness and minimizing variations in impedance.
Etching
The etching process removes the unwanted copper from the PCB, leaving behind the desired traces. Precise control over the etching process is necessary to achieve the specified trace widths and spacing. Over-etching or under-etching can lead to impedance variations.
Plating
Copper plating is often used to increase the thickness of the traces and improve their current-carrying capacity. However, plating can also affect the impedance of the traces, so it must be carefully controlled.
Impedance Testing
After manufacturing, the impedance of the PCB traces is measured using a time-domain reflectometer (TDR) or a vector network analyzer (VNA). These instruments send a signal through the trace and measure the reflected signal to determine the impedance. If the measured impedance deviates from the specified value, the manufacturing process may need to be adjusted.
Applications of Controlled Impedance PCBs
Controlled impedance PCBs find applications in a wide range of industries and products, including:
-
High-Speed Digital Circuits: Controlled impedance is essential for high-speed digital interfaces, such as USB, HDMI, and PCI Express, to ensure signal integrity and minimize reflections.
-
RF and Microwave Circuits: In wireless communication systems, radar, and satellite applications, controlled impedance is critical for efficient power transfer and minimizing signal loss.
-
Automotive Electronics: As vehicles incorporate more advanced driver assistance systems (ADAS) and infotainment features, controlled impedance PCBs are necessary to ensure reliable and robust performance in harsh automotive environments.
-
Medical Devices: Medical equipment, such as MRI machines and ultrasound systems, rely on controlled impedance PCBs for precise signal transmission and image quality.
-
Aerospace and Defense: In military and aerospace applications, controlled impedance PCBs are used in radar systems, avionics, and satellite communication equipment, where reliability and performance are paramount.
Frequently Asked Questions (FAQ)
-
What is the difference between characteristic impedance and controlled impedance?
Characteristic impedance is the inherent impedance of a transmission line, determined by its geometry and the properties of the surrounding dielectric material. Controlled impedance refers to the process of designing and manufacturing a PCB to achieve a specific target impedance value. -
How does the dielectric constant affect impedance?
The dielectric constant (Dk) of a material influences the speed at which a signal propagates through it. A higher Dk results in a slower signal velocity and a lower impedance. Conversely, a lower Dk leads to a faster signal velocity and a higher impedance. -
What is the typical impedance value for a USB interface?
USB interfaces typically use a differential impedance of 90 ohms for the data lines (D+ and D-). This impedance is achieved using a controlled impedance PCB design with carefully selected trace geometry and dielectric materials. -
Can controlled impedance be achieved on a two-layer PCB?
Yes, controlled impedance can be achieved on a two-layer PCB using a surface microstrip configuration. However, the design options are more limited compared to multilayer PCBs, and the impedance control may not be as precise. -
What is the impact of impedance mismatch on signal integrity?
Impedance mismatch causes signal reflections, which can lead to distortion, ringing, and overshoot. These effects degrade signal integrity and can cause data errors, especially at high frequencies. Matching the impedance of the trace to the source and load minimizes these reflections and ensures clean signal transmission.
Conclusion
Controlled impedance PCBs are essential for high-speed, high-frequency applications where signal integrity and power efficiency are critical. By carefully designing the trace geometry, selecting appropriate dielectric materials, and controlling the manufacturing process, PCB designers can achieve precise impedance matching and optimize circuit performance.
As electronic systems continue to push the boundaries of speed and complexity, the demand for controlled impedance PCBs will only grow. Staying up-to-date with the latest design techniques, simulation tools, and manufacturing processes is crucial for engineers working on cutting-edge applications in industries such as telecommunications, automotive, aerospace, and medical devices.
By understanding the principles of controlled impedance and applying them effectively, PCB designers can create robust, reliable, and high-performance electronic systems that meet the evolving needs of today’s technology landscape.