What is FR4 Material?
FR4 is a composite material made of woven fiberglass cloth with an epoxy resin binder. The “FR” stands for “Flame Retardant,” indicating that the material has been treated to resist burning. The “4” refers to the specific grade of flame retardancy, which is defined by the National Electrical Manufacturers Association (NEMA).
Composition of FR4
The composition of FR4 consists of two main components:
- Woven fiberglass cloth: This provides the structural strength and dimensional stability of the material.
- Epoxy resin: This acts as a binder, holding the fiberglass cloth together and providing insulation between the layers.
The combination of these materials results in a strong, rigid, and dimensionally stable substrate that can withstand high temperatures and harsh environments.
Properties of FR4
FR4 has several key properties that make it an excellent choice for PCB fabrication:
- High mechanical strength: FR4 has a high tensile strength and flexural strength, making it resistant to bending and breaking.
- Excellent electrical insulation: The epoxy resin provides excellent electrical insulation, preventing short circuits and signal interference.
- Good thermal stability: FR4 can withstand temperatures up to 130°C (266°F) continuously and 180°C (356°F) for short periods, making it suitable for high-temperature applications.
- Flame retardancy: The material is treated with flame retardants to prevent the spread of fire in case of ignition.
- Moisture resistance: FR4 has low moisture absorption, which helps maintain its electrical and mechanical properties in humid environments.
Manufacturing Process of FR4 PCB
The manufacturing process of FR4 PCB involves several steps, each of which is critical to ensuring the quality and reliability of the final product.
1. Preparing the Substrate
The first step in the manufacturing process is to prepare the FR4 substrate. This involves cutting the material to the desired size and shape, and then cleaning it to remove any contaminants or debris.
2. Applying the Copper Layer
Once the substrate is prepared, a thin layer of copper is applied to one or both sides of the board. This is typically done using a process called electroless copper plating, which involves depositing a thin layer of copper onto the surface of the board using a chemical solution.
3. Patterning the Circuit
After the copper layer is applied, the desired circuit pattern is created on the board. This is typically done using a photolithography process, which involves applying a photoresist material to the surface of the board and then exposing it to light through a patterned mask. The exposed areas of the photoresist are then developed and removed, leaving behind the desired circuit pattern.
4. Etching the Copper
Once the circuit pattern is created, the excess copper is removed using an etching process. This involves exposing the board to a chemical solution that selectively removes the copper in the areas not protected by the photoresist.
5. Applying the Solder Mask
After the etching process is complete, a solder mask is applied to the surface of the board. This is a thin layer of insulating material that covers the copper traces and protects them from damage during the soldering process.
6. Applying the Silkscreen
The final step in the manufacturing process is to apply the silkscreen, which is a layer of text and graphics that is printed onto the surface of the board. This is typically used to label components and provide other important information about the board.
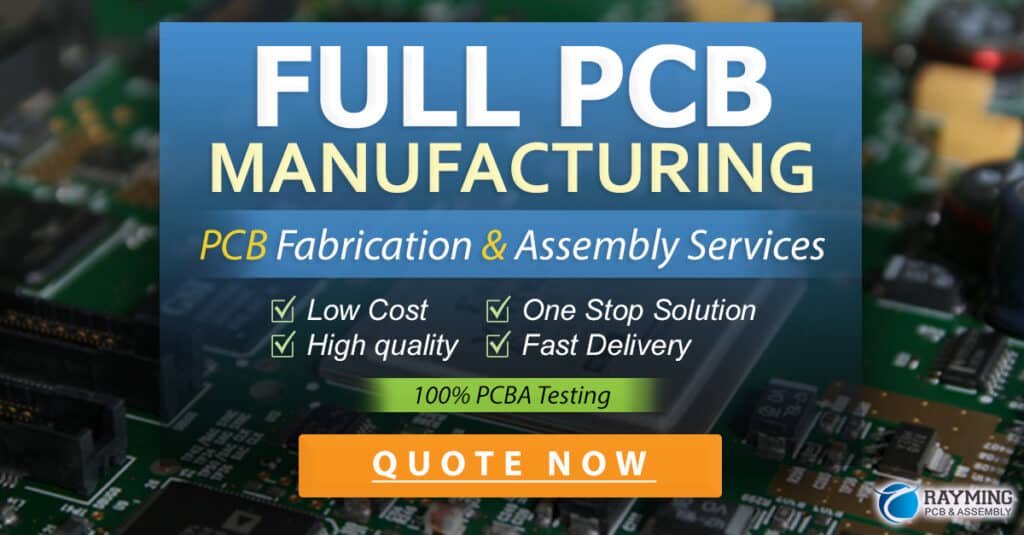
Applications of FR4 PCB
FR4 PCB is used in a wide range of applications, from consumer electronics to industrial equipment. Some of the most common applications include:
1. Consumer Electronics
FR4 PCB is widely used in consumer electronics, such as smartphones, tablets, laptops, and televisions. Its excellent electrical and mechanical properties make it an ideal choice for these applications, where reliability and durability are critical.
2. Industrial Equipment
FR4 PCB is also used in industrial equipment, such as power supplies, motor drives, and control systems. Its high thermal stability and flame retardancy make it well-suited for these applications, where the board may be exposed to high temperatures and harsh environments.
3. Medical Devices
FR4 PCB is used in a variety of medical devices, such as patient monitors, diagnostic equipment, and surgical instruments. Its excellent electrical insulation and moisture resistance make it an ideal choice for these applications, where patient safety is of paramount importance.
4. Automotive Electronics
FR4 PCB is used in automotive electronics, such as engine control units, infotainment systems, and safety features. Its high mechanical strength and thermal stability make it well-suited for these applications, where the board may be exposed to vibration, shock, and extreme temperatures.
Advantages of FR4 PCB
FR4 PCB offers several advantages over other types of PCB materials:
- Cost-effective: FR4 is relatively inexpensive compared to other PCB materials, making it an attractive option for high-volume production.
- Easy to manufacture: The manufacturing process for FR4 PCB is well-established and straightforward, making it easy to produce high-quality boards consistently.
- Versatile: FR4 can be used in a wide range of applications, from consumer electronics to industrial equipment, making it a versatile choice for PCB fabrication.
- Reliable: FR4 has excellent electrical and mechanical properties, making it a reliable choice for applications where durability and long-term performance are critical.
Disadvantages of FR4 PCB
Despite its many advantages, FR4 PCB also has some disadvantages:
- Limited high-frequency performance: FR4 has a relatively high dielectric constant and dissipation factor, which can limit its performance at high frequencies.
- Moisture absorption: Although FR4 has low moisture absorption compared to other PCB materials, it can still absorb moisture over time, which can affect its electrical and mechanical properties.
- Thermal expansion: FR4 has a relatively high coefficient of thermal expansion (CTE), which can cause the board to expand and contract with changes in temperature. This can lead to stress on the components and solder joints, potentially causing failures over time.
Comparison with Other PCB Materials
FR4 is just one of many PCB materials available, each with its own unique properties and advantages. Some of the most common alternatives to FR4 include:
1. Polyimide
Polyimide is a high-performance PCB material that offers excellent thermal stability and mechanical strength. It is often used in applications where high temperatures and harsh environments are a concern, such as aerospace and defense.
2. Rogers
Rogers is a family of high-frequency PCB materials that offer excellent electrical performance at high frequencies. They are often used in RF and microwave applications, where signal integrity is critical.
3. Aluminum
Aluminum PCBs are used in applications where heat dissipation is a concern, such as power electronics and LED lighting. The aluminum substrate provides excellent thermal conductivity, helping to dissipate heat away from the components.
FAQs
1. What does FR4 stand for?
FR4 stands for “Flame Retardant 4,” indicating that the material has been treated to resist burning and meets the UL94 V-0 flammability rating.
2. What is the maximum operating temperature of FR4 PCB?
FR4 PCB can withstand temperatures up to 130°C (266°F) continuously and 180°C (356°F) for short periods.
3. Can FR4 PCB be used in high-frequency applications?
While FR4 PCB can be used in high-frequency applications, its relatively high dielectric constant and dissipation factor can limit its performance at very high frequencies. For these applications, alternative materials such as Rogers or PTFE may be a better choice.
4. Is FR4 PCB environmentally friendly?
FR4 PCB is not considered environmentally friendly due to the use of flame retardants and other chemicals in its manufacture. However, many PCB manufacturers are working to develop more sustainable and eco-friendly alternatives to FR4.
5. How does the cost of FR4 PCB compare to other PCB materials?
FR4 PCB is generally less expensive than other high-performance PCB materials such as polyimide or Rogers. However, the exact cost will depend on factors such as the size and complexity of the board, the number of layers, and the volume of production.
In conclusion, FR4 PCB is a versatile and reliable choice for a wide range of electronics applications. Its excellent mechanical, electrical, and thermal properties, combined with its cost-effectiveness and ease of manufacture, make it a popular choice for PCB fabrication. While it may not be the best choice for every application, particularly those requiring high-frequency performance or extreme environmental conditions, FR4 remains a workhorse material that is widely used throughout the industry.
Property | FR4 | Polyimide | Rogers | Aluminum |
---|---|---|---|---|
Dielectric Constant | 4.3 | 3.5 | 2.2 – 10.2 | – |
Dissipation Factor | 0.02 | 0.002 | 0.0009 – 0.0035 | – |
Thermal Conductivity (W/mK) | 0.3 | 0.2 | 0.6 – 1.5 | 150 – 200 |
Tensile Strength (MPa) | 400 | 345 | 200 – 400 | 70 – 90 |
Flexural Strength (MPa) | 500 | 517 | 200 – 400 | 100 – 150 |
Glass Transition Temperature (°C) | 130 | 260 | 200 – 280 | – |
Table 1: Comparison of key properties of common PCB materials
As shown in Table 1, each PCB material has its own unique set of properties that make it suitable for different applications. FR4 offers a good balance of electrical, mechanical, and thermal properties at a relatively low cost, making it a popular choice for general-purpose PCBs. Polyimide and Rogers offer superior high-frequency performance and thermal stability, but at a higher cost. Aluminum PCBs are used primarily for their excellent thermal conductivity, but have lower mechanical strength compared to other materials.
Ultimately, the choice of PCB material will depend on the specific requirements of the application, including factors such as operating temperature, frequency, mechanical stress, and cost. By understanding the properties and advantages of each material, designers and manufacturers can make informed decisions and select the best option for their needs.