Introduction to Rigid Flex PCBs
A rigid flex PCB, also known as a flex-rigid PCB or rigiflex PCB, is a unique type of printed circuit board that combines the benefits of both rigid and flexible substrates. It consists of multiple layers of flexible PCB (flex PCB) and rigid pcb materials that are laminated together into a single structure. This hybrid design allows for the integration of flexible circuitry with rigid board sections, enabling 3D packaging and advanced electronic applications.
Rigid flex PCBs offer several advantages over traditional rigid PCBs, including:
- Reduced size and weight
- Increased reliability and durability
- Enhanced electrical performance
- Improved design flexibility
- Simplified assembly processes
These benefits make rigid flex PCBs an attractive solution for a wide range of industries, such as aerospace, automotive, medical devices, consumer electronics, and telecommunications.
Construction of Rigid Flex PCBs
Layers and Materials
A typical rigid flex PCB consists of the following layers:
-
Flexible layers: These are made of thin, flexible polymeric materials such as polyimide (PI) or polyester (PET). The most common flexible substrate is Kapton, a polyimide film developed by DuPont. Flexible layers allow the PCB to bend and flex as needed.
-
Rigid layers: These are made of standard FR-4 or high-temperature FR-4 materials, similar to traditional rigid PCBs. Rigid layers provide structural support and house components that require a stable platform.
-
Copper layers: Copper foil is used to create conductive traces and pads on both flexible and rigid layers. The copper thickness can vary depending on the electrical requirements of the design.
-
Adhesive layers: These are used to bond the flexible and rigid layers together. Adhesives are typically acrylic or epoxy-based and must be compatible with the substrates and able to withstand the stresses of flexing.
-
Coverlay or soldermask: A protective layer is applied to the outer surfaces of the PCB to insulate and protect the copper traces. Flexible coverlays are used on flex layers, while soldermask is used on rigid layers.
Fabrication Process
The fabrication process for rigid flex PCBs is more complex than that of standard rigid PCBs due to the integration of flexible and rigid materials. The general steps involved are:
-
Material preparation: The flexible and rigid substrates are cut to size, and copper foil is laminated onto the surfaces.
-
Drilling: Through-holes and vias are drilled into the rigid sections of the PCB.
-
Patterning: The copper layers are patterned using photolithography and etching processes to create the desired circuit layout.
-
Lamination: The flexible and rigid layers are aligned and laminated together using heat and pressure, with adhesive layers in between.
-
Plating: Through-holes and vias are plated with copper to create electrical connections between layers.
-
Surface finishing: A protective surface finish, such as ENIG (Electroless Nickel Immersion Gold) or HASL (Hot Air Solder Leveling), is applied to the exposed copper areas.
-
Singulation: The panel is cut into individual rigid flex PCBs using routing or laser cutting techniques.
-
Testing and inspection: The finished PCBs are tested for electrical functionality and inspected for visual defects.
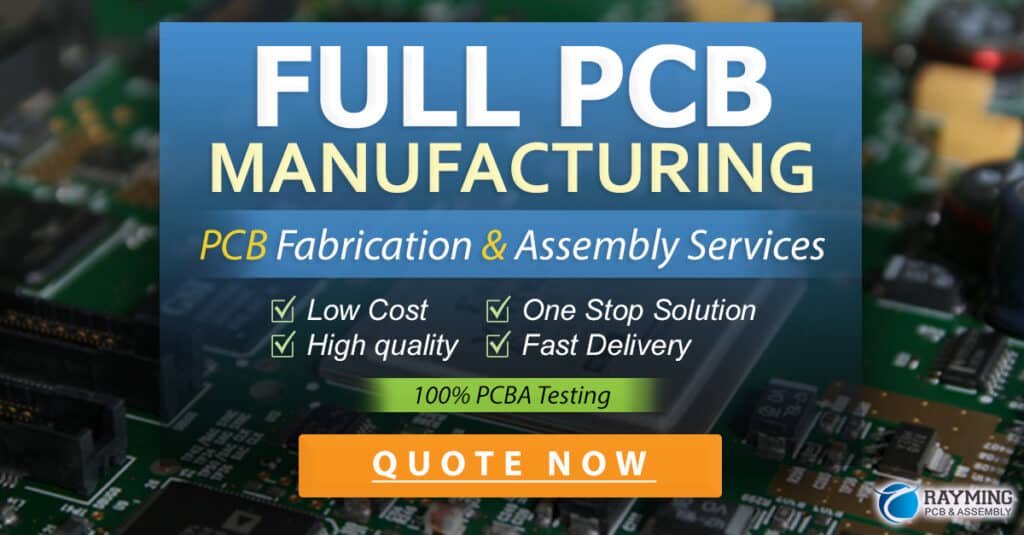
Advantages of Rigid Flex PCBs
Size and Weight Reduction
One of the primary advantages of rigid flex PCBs is their ability to reduce the size and weight of electronic assemblies. By combining flexible and rigid sections, designers can create more compact packaging solutions that conform to the available space within a device. This is particularly beneficial for applications where space is limited, such as in smartphones, wearables, and aerospace systems.
Rigid flex PCBs also eliminate the need for bulky connectors and cables between rigid boards, further reducing the overall size and weight of the assembly. This not only saves space but also improves reliability by minimizing the number of potential failure points.
Increased Reliability and Durability
Rigid flex PCBs offer increased reliability and durability compared to traditional rigid PCBs with separate flexible connectors. The integrated design reduces the number of solder joints and connections, which are common points of failure in electronic assemblies. By eliminating these weak points, rigid flex PCBs can withstand greater mechanical stresses and vibrations without compromising electrical performance.
Additionally, the flexible sections of a rigid flex PCB are designed to endure repeated flexing and bending without breaking or delaminating. The choice of high-quality materials, such as Kapton polyimide films, ensures that the PCB can withstand the stresses of flexing over its intended lifetime.
Enhanced Electrical Performance
Rigid flex PCBs can provide enhanced electrical performance compared to traditional rigid PCBs with separate flexible connectors. The integrated design minimizes signal loss and interference by reducing the length of interconnects between components. Shorter signal paths also enable higher signal speeds and lower propagation delays, which is crucial for high-frequency applications.
Furthermore, rigid flex PCBs offer better impedance control and reduced crosstalk due to the consistent dielectric properties of the flexible substrate materials. This is particularly important for applications that require high signal integrity, such as in telecommunications and high-speed data transmission systems.
Improved Design Flexibility
Rigid flex PCBs offer improved design flexibility by allowing for 3D packaging and the integration of multiple rigid boards into a single assembly. The flexible sections can be folded and shaped to fit within the available space, enabling more creative and efficient packaging solutions. This is particularly useful for applications that require a high degree of customization or have unique form factor requirements.
Designers can also use rigid flex PCBs to reduce the number of separate PCBs and connectors in an assembly, simplifying the overall design and reducing the potential for errors during manufacturing and assembly.
Simplified Assembly Processes
Rigid flex PCBs can simplify the assembly process by reducing the number of separate components and connectors that need to be assembled. This not only saves time and costs during manufacturing but also improves the reliability of the final product by minimizing the potential for human error during assembly.
Additionally, rigid flex PCBs enable the use of automated assembly processes, such as surface mount technology (SMT), for both rigid and flexible sections. This further streamlines the assembly process and reduces the need for manual intervention, leading to higher throughput and lower production costs.
Applications of Rigid Flex PCBs
Rigid flex PCBs are used in a wide range of industries and applications where size, weight, reliability, and performance are critical factors. Some common applications include:
-
Aerospace and defense: Avionics systems, satellites, missiles, and military communication devices.
-
Automotive: In-vehicle infotainment systems, driver assistance systems, and electronic control units.
-
Medical devices: Implantable devices, diagnostic equipment, and patient monitoring systems.
-
Consumer electronics: Smartphones, smartwatches, gaming devices, and virtual reality headsets.
-
Telecommunications: Routers, switches, and base stations for 5G networks.
-
Industrial automation: Robotics, motion control systems, and machine vision equipment.
Design Considerations for Rigid Flex PCBs
When designing rigid flex PCBs, engineers must consider several key factors to ensure optimal performance, reliability, and manufacturability:
-
Bend radius: The minimum bend radius of the flexible sections must be specified to prevent damage to the copper traces and substrate materials during flexing.
-
Stiffener placement: Stiffeners are used to reinforce the flexible sections and prevent excessive bending. The placement and size of stiffeners must be carefully considered to ensure proper support without hindering the desired flexibility.
-
Copper weights: The copper weight (thickness) of the traces on flexible layers must be selected based on the electrical requirements and the desired flexibility. Thinner copper is more flexible but may not be suitable for high-current applications.
-
Adhesive selection: The choice of adhesive materials must be based on the desired flexibility, temperature resistance, and compatibility with the substrate materials.
-
Panelization: Rigid flex PCBs must be panelized in a way that allows for efficient fabrication and assembly while minimizing waste material.
-
Testing and validation: Comprehensive testing and validation procedures must be established to ensure the reliability and performance of the rigid flex PCB over its intended lifetime.
Future Trends in Rigid Flex PCB Technology
As electronic devices continue to become smaller, more complex, and more powerful, the demand for advanced packaging solutions like rigid flex PCBs is expected to grow. Some of the future trends in rigid flex PCB technology include:
-
Increased layer counts: The development of thinner substrate materials and improved lamination techniques will enable the fabrication of rigid flex PCBs with higher layer counts, allowing for more complex designs and higher component densities.
-
Advanced materials: New substrate materials, such as liquid crystal polymers (LCPs) and polyether ether ketone (PEEK), will offer improved thermal stability, chemical resistance, and electrical performance for demanding applications.
-
Embedded components: The integration of passive components, such as resistors and capacitors, into the inner layers of rigid flex PCBs will further reduce the size and weight of electronic assemblies.
-
High-frequency applications: As 5G networks and other high-frequency applications become more prevalent, rigid flex PCBs will play a critical role in enabling high-speed data transmission and minimizing signal loss.
-
Sustainable manufacturing: The development of eco-friendly materials and processes for rigid flex PCB fabrication will help reduce the environmental impact of electronics manufacturing.
Frequently Asked Questions (FAQ)
-
What is the difference between a rigid PCB and a flex PCB?
A rigid PCB is made of a solid, inflexible substrate material, such as FR-4, while a flex PCB is made of a thin, flexible polymeric material, such as polyimide. Rigid PCBs are used for applications that require a stable platform for components, while flex PCBs are used for applications that require the ability to bend or flex. -
Can rigid flex PCBs be repaired?
Repairing rigid flex PCBs can be challenging due to their complex construction and the presence of both rigid and flexible sections. In most cases, it is recommended to replace a damaged rigid flex PCB rather than attempting to repair it. However, minor repairs, such as replacing a single component or repairing a broken trace, may be possible depending on the extent of the damage and the accessibility of the affected area. -
How much do rigid flex PCBs cost compared to traditional rigid PCBs?
Rigid flex PCBs are generally more expensive than traditional rigid PCBs due to the complexity of their fabrication process and the use of specialized materials. The cost of a rigid flex PCB can be several times higher than that of an equivalent rigid PCB, depending on factors such as the number of layers, the size of the PCB, and the volume of the order. However, the higher initial cost can often be offset by the benefits of reduced assembly time, improved reliability, and smaller form factors. -
What are the limitations of rigid flex PCBs?
While rigid flex PCBs offer many advantages, they also have some limitations. One of the main limitations is the higher cost compared to traditional rigid PCBs. Additionally, the design and fabrication of rigid flex PCBs can be more complex, requiring specialized knowledge and tools. The minimum bend radius of the flexible sections must also be carefully considered to prevent damage during use, which can limit the range of motion in some applications. -
How do I choose the right rigid flex pcb manufacturer?
Choosing the right rigid flex PCB manufacturer is critical to ensuring the quality, reliability, and timely delivery of your PCBs. When selecting a manufacturer, consider factors such as their experience with rigid flex PCBs, their manufacturing capabilities, their quality control processes, and their customer support. Look for manufacturers that have a proven track record of delivering high-quality rigid flex PCBs for applications similar to yours. Request references and samples to evaluate their workmanship and attention to detail. Finally, consider their pricing and lead times to ensure they align with your project requirements and budget.
Conclusion
Rigid flex PCBs are a versatile and innovative solution for a wide range of electronic applications, offering benefits such as reduced size and weight, increased reliability, enhanced electrical performance, improved design flexibility, and simplified assembly processes. As the demand for more compact, reliable, and high-performance electronic devices continues to grow, rigid flex PCBs will play an increasingly important role in enabling the next generation of electronics.
To successfully implement rigid flex PCBs in your designs, it is essential to work with experienced PCB design engineers and reliable manufacturing partners who can help you navigate the complexities of rigid flex PCB design and fabrication. By carefully considering the design requirements, material selection, and manufacturing processes, you can unlock the full potential of rigid flex PCBs and create electronic assemblies that are smaller, lighter, and more reliable than ever before.