Understanding Copper PCBs
Definition and Composition
A copper PCB is a printed circuit board that uses copper as the primary conductive material for its traces and pads. The board consists of a non-conductive substrate, typically made of fiberglass or other composite materials, with a thin layer of copper laminated onto one or both sides.
The copper layer is etched to create the desired circuit pattern, connecting various electronic components such as resistors, capacitors, and integrated circuits. The etching process removes unwanted copper, leaving behind the necessary traces and pads.
Types of Copper PCBs
Copper PCBs come in various types, depending on the number of layers and the specific manufacturing process used. The most common types include:
-
Single-sided PCBs: These boards have copper traces on only one side of the substrate. They are the simplest and most cost-effective option for basic electronic circuits.
-
Double-sided PCBs: These boards have copper traces on both sides of the substrate, allowing for more complex circuit designs and higher component density. Conductive vias are used to connect traces between the two sides.
-
Multi-layer PCBs: These boards consist of multiple layers of copper traces separated by insulating layers. They offer the highest level of complexity and density, making them suitable for advanced electronic applications.
-
Flexible PCBs: These boards use a flexible substrate, such as polyimide, allowing them to bend and conform to various shapes. They are commonly used in wearable electronics and applications requiring flexibility.
Manufacturing Process of Copper PCBs
The manufacturing process of copper PCBs involves several steps, each critical to ensuring the quality and functionality of the final product.
PCB Design and Layout
The first step in manufacturing a copper PCB is designing the circuit and creating the PCB layout. This process involves using specialized software to create a schematic diagram of the circuit and then translating it into a physical layout.
The layout determines the placement of components, the routing of traces, and the overall dimensions of the board. Designers must adhere to various design rules and guidelines to ensure proper functionality, signal integrity, and manufacturability.
Copper Lamination
Once the PCB layout is finalized, the next step is to laminate the copper onto the substrate. This process involves placing a thin sheet of copper onto the substrate material and bonding them together under high pressure and temperature.
The most common method of lamination is the “foil lamination” process, where a pre-patterned copper foil is laminated onto the substrate. Another method is the “direct metallization” process, where copper is deposited directly onto the substrate using chemical or electrochemical processes.
Etching and Plating
After the copper is laminated onto the substrate, the next step is to etch away the unwanted copper to create the desired circuit pattern. This process involves applying a photoresist layer onto the copper, exposing it to UV light through a photomask, and then developing the photoresist to remove the exposed areas.
The exposed copper is then etched away using a chemical solution, typically ferric chloride or ammonium persulfate. The remaining photoresist is then stripped away, leaving behind the desired copper traces and pads.
In some cases, additional plating processes may be used to improve the conductivity and durability of the copper traces. These processes include electroplating, where a thicker layer of copper is deposited onto the existing traces, and solder mask application, where a protective coating is applied to the board to prevent oxidation and improve solderability.
Drilling and Finishing
The final steps in the manufacturing process involve drilling holes for through-hole components and applying the finishing touches to the board.
Drilling is typically done using a computer-controlled drill machine, which creates holes of various sizes and locations based on the PCB layout. The holes are then plated with copper to ensure proper electrical conductivity.
After drilling, the board undergoes a series of finishing processes, such as solder mask application, silkscreen printing, and surface finish application. These processes improve the aesthetics and functionality of the board, making it ready for component assembly and final testing.
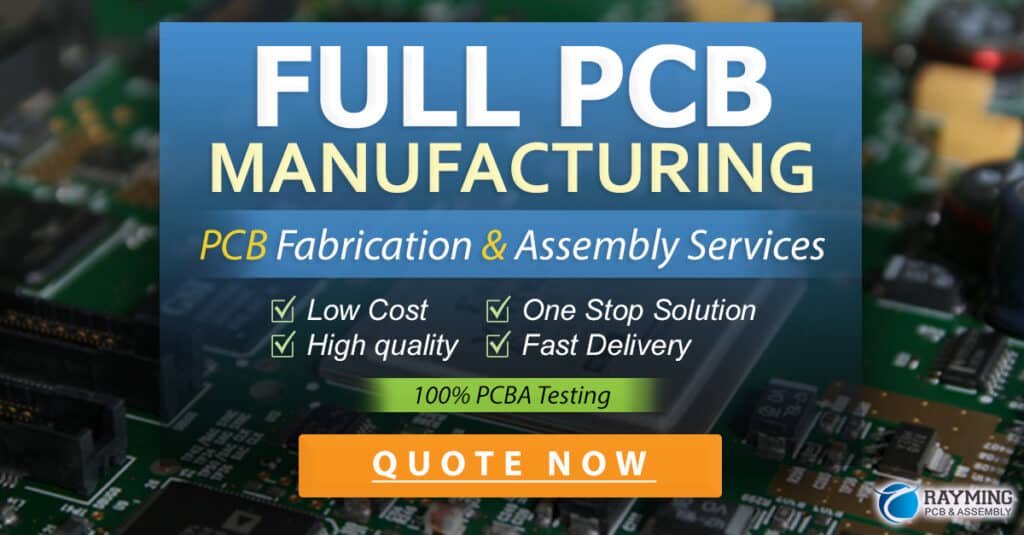
Advantages of Copper PCBs
Copper PCBs offer several advantages over other types of PCBs, making them the preferred choice for most electronic applications.
Excellent Conductivity
Copper is an excellent conductor of electricity, second only to silver among common metals. This high conductivity ensures that signals can propagate through the traces with minimal resistance and loss, improving the overall performance and reliability of the circuit.
Cost-Effectiveness
Copper is relatively inexpensive compared to other conductive materials, such as gold or silver. This cost-effectiveness makes copper PCBs an attractive option for mass production and consumer electronics.
Durability and Reliability
Copper is a durable metal that can withstand the stresses and strains of everyday use. When properly designed and manufactured, copper PCBs can last for many years without significant degradation or failure.
Versatility
Copper PCBs can be manufactured in a wide range of sizes, shapes, and layer configurations, making them suitable for a variety of applications. They can be used in everything from simple LED circuits to complex multi-layer boards for high-speed digital systems.
Applications of Copper PCBs
Copper PCBs are used in virtually every electronic device and system, across various industries and applications. Some of the most common applications include:
Consumer Electronics
Copper PCBs are the backbone of consumer electronics, such as smartphones, tablets, laptops, televisions, and gaming consoles. They enable the complex circuitry and functionality that make these devices possible.
Industrial Automation
Copper PCBs are used extensively in industrial automation systems, such as programmable logic controllers (PLCs), sensors, and actuators. They provide the necessary connectivity and control for automated manufacturing processes and equipment.
Automotive Electronics
Modern automobiles rely heavily on electronic systems for everything from engine management to infotainment and safety features. Copper PCBs are used in various automotive applications, such as engine control units (ECUs), dashboard displays, and advanced driver assistance systems (ADAS).
Medical Devices
Copper PCBs are used in a wide range of medical devices, from patient monitoring systems and diagnostic equipment to implantable devices and prosthetics. They provide the necessary reliability and performance for these critical applications.
Aerospace and Defense
Copper PCBs are used extensively in aerospace and defense systems, such as avionics, radar, and communication equipment. They must meet stringent requirements for reliability, durability, and performance in harsh environments.
Frequently Asked Questions (FAQ)
1. What is the difference between copper PCBs and other types of PCBs?
Copper PCBs use copper as the primary conductive material for their traces and pads, while other types of PCBs may use different materials, such as aluminum or silver. Copper is chosen for its excellent conductivity, cost-effectiveness, and durability.
2. Can copper PCBs be recycled?
Yes, copper PCBs can be recycled to recover the valuable copper and other materials. The recycling process typically involves shredding the boards, separating the metals from the non-metallic components, and then refining the metals for reuse.
3. How long do copper PCBs last?
The lifespan of a copper PCB depends on various factors, such as the quality of the manufacturing process, the environmental conditions, and the specific application. When properly designed and manufactured, copper PCBs can last for many years, often exceeding the lifespan of the electronic device they are used in.
4. Are copper PCBs suitable for high-frequency applications?
Yes, copper PCBs can be used for high-frequency applications, such as radio frequency (RF) and microwave circuits. However, special design considerations must be taken into account, such as the use of controlled impedance traces and the minimization of signal reflections and crosstalk.
5. Can copper PCBs be customized for specific applications?
Yes, copper PCBs can be customized to meet the specific requirements of a given application. This customization can include the size and shape of the board, the number and configuration of layers, the type of surface finish, and the placement of components and connectors.
Conclusion
Copper PCBs are the foundation of modern electronics, enabling the complex circuitry and functionality that make our digital world possible. Their excellent conductivity, cost-effectiveness, durability, and versatility make them the preferred choice for a wide range of applications, from consumer electronics to industrial automation and aerospace systems.
As technology continues to advance, the demand for copper PCBs will only continue to grow. By understanding the basics of copper PCBs, their manufacturing process, advantages, and applications, engineers and designers can make informed decisions when developing new electronic products and systems.
Property | Value |
---|---|
Conductivity | 59.6 × 10^6 S/m |
Thermal Conductivity | 401 W/(m·K) |
Melting Point | 1084.62°C |
Density | 8.96 g/cm³ |
Tensile Strength | 220 MPa |
Young’s Modulus | 110 GPa |
Electrical Resistivity | 1.68 × 10^-8 Ω·m |
Temperature Coefficient of Resistance | 0.00393 /°C |
Table 1: Key properties of copper used in PCBs.
PCB Type | Layers | Typical Applications |
---|---|---|
Single-sided | 1 | Simple circuits, low-cost applications |
Double-sided | 2 | Moderately complex circuits, improved connectivity |
Multi-layer | 4-12+ | Complex circuits, high-density applications |
Flexible | 1-2 | Wearable electronics, compact devices |
Table 2: Common types of copper PCBs and their typical applications.
By leveraging the unique properties and advantages of copper PCBs, engineers and designers can create innovative and reliable electronic products that shape our world and improve our lives.