Understanding Electromagnetic Interference (EMI) and Radio Frequency Interference (RFI)
Before we delve into the specifics of PCB shields, it’s essential to understand the phenomena of EMI and RFI and how they can affect electronic circuits.
Electromagnetic Interference (EMI)
EMI refers to the disruption of an electronic device’s operation due to electromagnetic radiation emitted by another device or source. This interference can cause various issues, such as signal distortion, data corruption, or even complete system failure. EMI can be generated by a wide range of sources, including:
- Power lines
- Motors and generators
- Switching power supplies
- Wireless communication devices
- Lightning strikes
EMI can be classified into two main categories:
- Conducted EMI: This type of EMI occurs when the interference is transmitted through physical connections, such as cables or PCB traces. Conducted EMI can be further divided into two subcategories:
- Common-mode EMI: Interference that appears on all conductors relative to ground
-
Differential-mode EMI: Interference that appears between two conductors
-
Radiated EMI: This type of EMI occurs when the interference is transmitted through the air as electromagnetic waves. Radiated EMI can be caused by various sources, such as antennas, high-speed digital circuits, or poorly shielded cables.
Radio Frequency Interference (RFI)
RFI is a specific type of EMI that occurs in the radio frequency spectrum, typically between 3 kHz and 300 GHz. RFI can be caused by intentional radiators, such as cell phones, Wi-Fi routers, or Bluetooth devices, as well as unintentional radiators, such as digital circuits or switch-mode power supplies.
RFI can cause various issues in electronic devices, including:
- Signal distortion
- Reduced sensitivity
- Increased noise levels
- Data corruption
To mitigate the effects of EMI and RFI, engineers employ various techniques, such as proper PCB layout, grounding, filtering, and shielding. PCB shields are one of the most effective methods for protecting sensitive circuits from these unwanted interferences.
Types of PCB Shields
PCB shields come in various forms, each designed to address specific shielding requirements. The most common types of PCB shields include:
1. One-Piece Shields
One-piece shields, also known as can shields, are simple, cost-effective solutions for shielding small to medium-sized components or circuits. These shields are typically made from a single piece of metal, such as aluminum or stainless steel, and are designed to fit over the components that require shielding. One-piece shields are often secured to the PCB using soldering, snap-fit features, or adhesives.
Advantages of one-piece shields:
– Simple and cost-effective
– Easy to install and remove
– Suitable for small to medium-sized components
Disadvantages of one-piece shields:
– Limited flexibility for complex PCB layouts
– May require additional height clearance
2. Two-Piece Shields
Two-piece shields consist of a frame and a removable cover, offering greater flexibility and accessibility compared to one-piece shields. The frame is typically soldered onto the PCB, while the cover can be attached using snap-fit features or screws. This design allows for easy access to the shielded components during testing, debugging, or maintenance.
Advantages of two-piece shields:
– Offers greater flexibility and accessibility
– Suitable for larger components or circuits
– Allows for easy maintenance and debugging
Disadvantages of two-piece shields:
– More expensive than one-piece shields
– Requires more assembly time
3. Molded Shields
Molded shields are custom-designed shields that are molded to fit specific PCB layouts and components. These shields are typically made from conductive plastics, such as conductive elastomers or thermoplastics, and can be shaped to accommodate complex geometries and multiple compartments.
Advantages of molded shields:
– Customizable to fit specific PCB layouts
– Can accommodate complex geometries and multiple compartments
– Lightweight and cost-effective for high-volume production
Disadvantages of molded shields:
– Higher upfront tooling costs
– Longer lead times for design and production
4. Board-Level Shields
Board-level shields are integrated directly into the PCB design, using conductive traces, vias, and ground planes to create shielding structures. These shields are typically used for high-frequency circuits, such as radio frequency (RF) or high-speed digital designs, where traditional metal shields may not provide adequate performance.
Advantages of board-level shields:
– Integrated directly into the PCB design
– Suitable for high-frequency circuits
– Eliminates the need for additional shield assembly
Disadvantages of board-level shields:
– Requires careful PCB layout and design
– May increase PCB complexity and cost
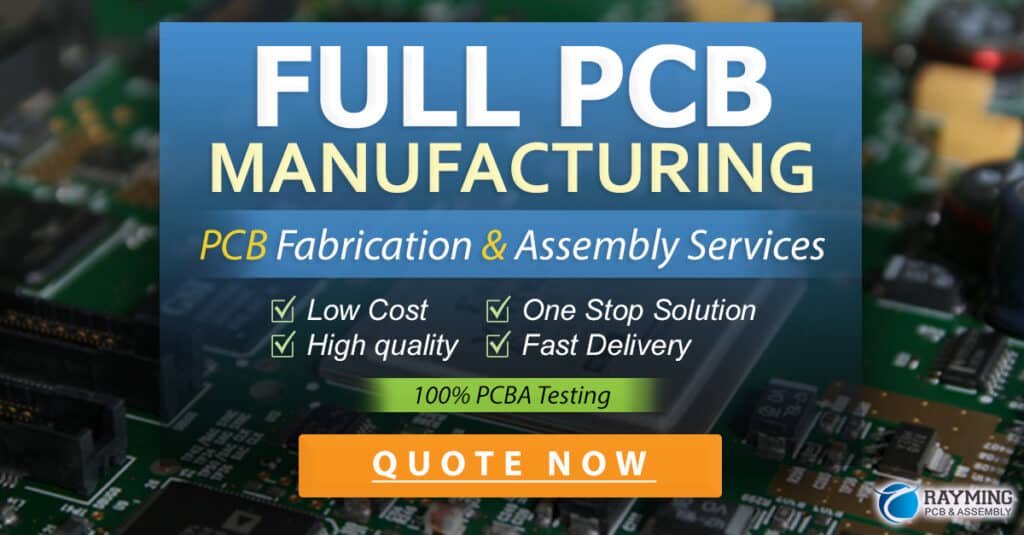
Materials Used for PCB Shields
The choice of material for a PCB shield depends on various factors, such as shielding effectiveness, cost, weight, and environmental considerations. The most common materials used for PCB shields include:
1. Aluminum
Aluminum is a popular choice for PCB shields due to its excellent electrical conductivity, low cost, and lightweight properties. Aluminum shields are typically stamped or formed from sheet metal and can be easily customized to fit specific PCB layouts. However, aluminum shields may not provide sufficient shielding effectiveness for high-frequency applications.
2. Stainless Steel
Stainless steel shields offer higher shielding effectiveness compared to aluminum, making them suitable for more demanding applications. Stainless steel is also more durable and resistant to corrosion, making it ideal for harsh environmental conditions. However, stainless steel shields are typically more expensive and heavier than aluminum shields.
3. Copper
Copper shields provide excellent shielding effectiveness, particularly for high-frequency applications. Copper’s high electrical conductivity and superior magnetic shielding properties make it an ideal choice for RF and high-speed digital circuits. However, copper shields are more expensive and heavier than aluminum or stainless steel shields.
4. Conductive Plastics
Conductive plastics, such as conductive elastomers or thermoplastics, are increasingly used for PCB shields due to their lightweight, flexible, and cost-effective properties. These materials are typically loaded with conductive fillers, such as carbon, nickel, or silver, to provide shielding effectiveness. Conductive plastic shields can be molded into complex shapes and are suitable for high-volume production.
Design Considerations for PCB Shields
When designing PCB shields, engineers must consider several factors to ensure optimal shielding effectiveness and overall system performance. Some key design considerations include:
1. Shielding Effectiveness
Shielding effectiveness (SE) is a measure of a shield’s ability to attenuate electromagnetic radiation. SE is typically expressed in decibels (dB) and is a function of the shield material, thickness, and frequency of the incident radiation. When selecting a shield material and designing its geometry, engineers must ensure that the SE meets the specific requirements of the application.
2. Grounding
Proper grounding is essential for effective shielding. PCB shields must be electrically connected to the PCB’s ground plane to provide a low-impedance path for interference currents. This is typically achieved through the use of conductive gaskets, spring fingers, or direct metal-to-metal contact. Inadequate grounding can result in reduced shielding effectiveness and potential EMI issues.
3. Apertures and Seams
Apertures and seams in PCB shields can compromise shielding effectiveness by allowing electromagnetic radiation to leak in or out of the shielded region. Engineers must minimize the size and number of apertures and ensure that seams are properly sealed using conductive gaskets or welding techniques. The maximum allowable aperture size depends on the frequency of the interference and the required SE.
4. Thermal Management
PCB shields can impact the thermal performance of the shielded components by restricting airflow and heat dissipation. Engineers must consider the thermal requirements of the shielded components and design the shield to allow for adequate cooling. This can be achieved through the use of vented shields, heat sinks, or thermal interface materials.
5. Mechanical Considerations
PCB shields must be designed to withstand the mechanical stresses encountered during assembly, handling, and operation. This includes considerations such as shield attachment methods, vibration resistance, and tolerance to thermal expansion and contraction. Engineers must also ensure that the shield does not interfere with other components on the PCB or the overall system packaging.
Importance of PCB Shields in Electronic Devices
PCB shields play a crucial role in ensuring the proper functioning, reliability, and compliance of electronic devices. Some of the key benefits of using PCB shields include:
1. Reduced EMI and RFI
PCB shields help to reduce the effects of EMI and RFI on sensitive electronic circuits, preventing signal distortion, data corruption, and system malfunctions. By enclosing and isolating specific areas of the PCB, shields minimize the coupling of unwanted electromagnetic energy between components and circuits.
2. Improved Signal Integrity
In high-speed digital and RF applications, PCB shields help to maintain signal integrity by reducing crosstalk, reflections, and other signal quality issues. By providing a controlled electromagnetic environment, shields enable designers to achieve higher signal speeds and better overall system performance.
3. Compliance with EMC Regulations
Electronic devices must comply with various electromagnetic compatibility (EMC) regulations, such as FCC Part 15 in the United States or CE marking in the European Union. PCB shields help to ensure that devices meet these regulatory requirements by reducing electromagnetic emissions and improving immunity to external interference.
4. Enhanced Product Reliability
By protecting sensitive circuits from EMI and RFI, PCB shields contribute to the overall reliability and longevity of electronic devices. Shielded devices are less likely to experience intermittent failures, data corruption, or premature component degradation due to electromagnetic interference.
5. Enabling Advanced Applications
PCB shields enable the development of advanced electronic applications, such as wireless communication devices, high-speed digital systems, and sensitive measurement equipment. By providing a controlled electromagnetic environment, shields allow designers to push the boundaries of performance and functionality in these demanding applications.
FAQ
-
Q: What is the difference between EMI and RFI?
A: EMI (electromagnetic interference) refers to any electromagnetic disturbance that can disrupt the operation of an electronic device, while RFI (radio frequency interference) specifically refers to interference in the radio frequency spectrum, typically between 3 kHz and 300 GHz. -
Q: How do I choose the right material for my PCB shield?
A: The choice of material for a PCB shield depends on factors such as shielding effectiveness, cost, weight, and environmental considerations. Common materials include aluminum, stainless steel, copper, and conductive plastics. Consider the specific requirements of your application when selecting a shield material. -
Q: Can PCB shields affect the thermal performance of my device?
A: Yes, PCB shields can impact the thermal performance of shielded components by restricting airflow and heat dissipation. When designing a PCB shield, consider the thermal requirements of the components and incorporate features such as vents, heat sinks, or thermal interface materials to ensure adequate cooling. -
Q: How do I ensure proper grounding of my PCB shield?
A: Proper grounding is essential for effective shielding. Ensure that your PCB shield is electrically connected to the PCB’s ground plane using conductive gaskets, spring fingers, or direct metal-to-metal contact. Inadequate grounding can result in reduced shielding effectiveness and potential EMI issues. -
Q: Can I use PCB shields for high-frequency applications?
A: Yes, PCB shields can be used for high-frequency applications, such as RF and high-speed digital circuits. However, the choice of shield material, design, and grounding becomes more critical at higher frequencies. Consider using materials with higher shielding effectiveness, such as copper, and pay close attention to apertures, seams, and grounding to ensure optimal performance.
Conclusion
PCB shields are essential components in modern electronic devices, providing a critical line of defense against electromagnetic interference and radio frequency interference. By understanding the types, materials, design considerations, and importance of PCB shields, engineers can develop more robust, reliable, and high-performance electronic systems.
As technology continues to advance, the demand for effective PCB shielding solutions will only grow. From consumer electronics to industrial automation, automotive systems to medical devices, PCB shields will play an increasingly vital role in ensuring the proper functioning and compliance of electronic devices in an ever-more connected and electromagnetic world.
By staying up-to-date with the latest developments in PCB shielding technologies and best practices, engineers can continue to push the boundaries of electronic design and innovation, creating the next generation of advanced, reliable, and electromagnetically compatible devices.