Introduction to Single Layer PCBs
A printed circuit board (PCB) is the foundation of nearly all modern electronic devices. It provides mechanical support and electrical connectivity for electronic components using conductive pathways, tracks or signal traces etched from copper sheets laminated onto a non-conductive substrate. PCBs can be single sided (one copper layer), double sided (two copper layers on both sides of one substrate layer), or multi-layer (outer and inner layers of copper, alternating with layers of substrate material).
The simplest type of PCB is the single layer or one layer PCB. As the name suggests, a single layer PCB has only one layer of base material or substrate. One side of the base material is coated with a thin layer of metal, usually copper. The circuit layout or trace is printed on the copper layer. Components are attached to the copper side, usually by soldering.
Single layer PCBs are also known as single sided PCBs or one layer PCBs. They offer several advantages in terms of simplicity, cost-effectiveness, and ease of design and manufacturing. In this article, we’ll take an in-depth look at single layer PCBs, their construction, applications, advantages, and design considerations.
Construction of a Single Layer PCB
A single layer PCB consists of a flat sheet of insulating material which acts as a base or substrate. One side of this base material is completely covered with a thin layer of metal, usually copper. The copper layer is laminated to the substrate.
Substrate Materials
The base material or substrate used in single layer PCBs is usually made from:
-
FR-4: A composite material composed of woven fiberglass fabric with an epoxy resin binder. FR-4 is the most widely used insulating substrate material.
-
CEM-1 or CEM-3: Composite epoxy materials consisting of a layer of woven glass fabric combined with layers of non-woven glass mats impregnated with epoxy resin. CEM is less expensive than FR-4.
-
Phenolics: Also known as Phenolic Cotton Paper (PC board), these are made from paper and phenolic resin. They have lower mechanical strength and moisture resistance compared to FR-4.
-
Polyimide: Used for high temperature applications. Polyimide PCBs can withstand temperatures up to 400°C.
The choice of substrate material depends on the intended application, required mechanical strength, electrical properties, thermal resistance, and cost considerations.
Copper Layer
The copper layer provides the conductive pathways for the mounted electronic components. The thickness of the copper layer is expressed in ounces per square foot (oz/ft²). Some common copper weights used in PCBs are:
Copper Thickness (oz/ft²) | Copper Thickness (μm) |
---|---|
0.5 oz | 17 μm |
1 oz | 35 μm |
2 oz | 70 μm |
3 oz | 105 μm |
The choice of copper thickness depends on the current carrying capacity and power handling requirements. Thicker copper layers can handle higher currents but make the PCB less flexible. Thinner copper layers are more flexible but have lower current carrying capacity.
Solder Mask
A solder mask is a thin layer of polymer applied on top of the copper layer. It acts as an insulating and protective layer, preventing solder bridges and short circuits. Solder mask also provides protection against oxidation and corrosion of the copper tracks. The solder mask is usually green in color but other colors like red, blue, black, white, and yellow are also available.
Silkscreen
The silkscreen is the white text and symbols printed on top of the solder mask. It is used to identify components, connectors, test points, and other features of the PCB. The silkscreen makes it easier for assembly, testing, and repairs. The silkscreen ink is usually white but other colors are also available.
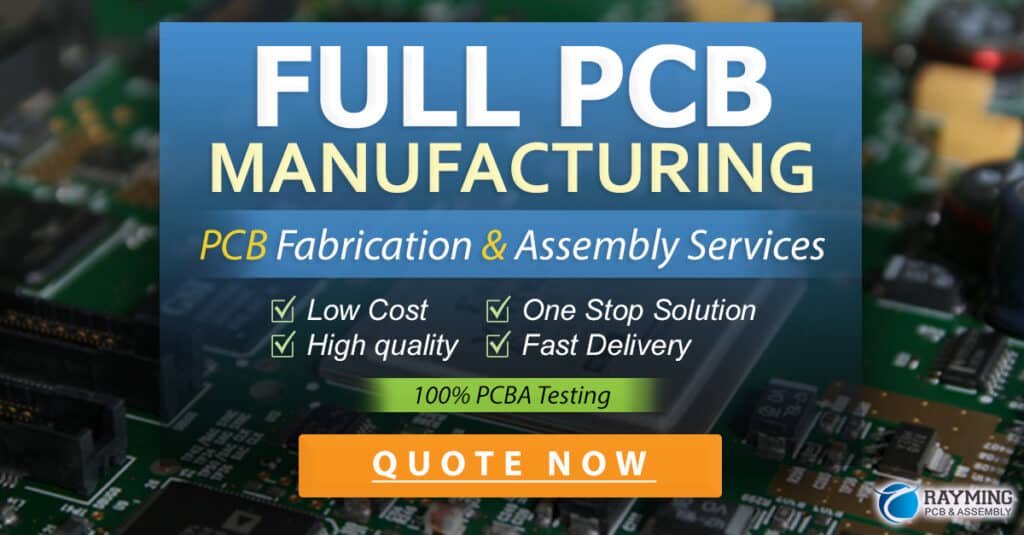
Single Layer PCB Manufacturing Process
The manufacturing process for single layer PCBs involves several steps:
-
Design: The PCB design is created using Electronic Design Automation (EDA) software. The design includes schematic capture, component placement, and PCB layout.
-
Film Generation: The PCB design files are used to generate photoplots or film. The photoplots are used to expose the photoresist on the copper clad laminate.
-
Exposure and Development: The copper clad laminate is coated with a layer of photoresist. The photoplots are placed on top of the photoresist and exposed to ultraviolet (UV) light. The exposed areas of the photoresist harden while the unexposed areas remain soft. The soft photoresist is then removed using a chemical developer solution, leaving behind the hardened photoresist in the desired circuit pattern.
-
Etching: The developed board is then immersed in an etchant solution, usually ferric chloride or ammonium persulfate. The etchant removes the copper from the areas not protected by the hardened photoresist, leaving behind the desired copper traces.
-
Stripping: The hardened photoresist is then stripped off using a chemical stripper, leaving behind the bare copper traces.
-
Solder Mask Application: A layer of solder mask ink is applied over the copper traces and exposed to UV light to harden it. The solder mask provides insulation and protection for the copper traces.
-
Silkscreen Printing: The silkscreen legends and symbols are printed on top of the solder mask using a silkscreen printer.
-
Surface Finish: The exposed copper pads are coated with a layer of surface finish to prevent oxidation and improve solderability. Common surface finishes include Hot Air Solder Leveling (HASL), Organic Solderability Preservative (OSP), Electroless Nickel Immersion Gold (ENIG), and Immersion Silver.
-
Drilling: Holes are drilled in the PCB for through-hole components and vias using a CNC drilling machine.
-
Cutting and Routing: The individual PCBs are routed out of the larger production panel using a CNC routing machine.
-
Electrical Testing: The finished PCBs undergo electrical testing to ensure that there are no short circuits or open circuits.
Advantages of Single Layer PCBs
Single layer PCBs offer several advantages over double layer and multi-layer PCBs:
-
Lower Cost: Single layer PCBs are the most cost-effective type of PCB. They require less raw material, fewer manufacturing steps, and shorter processing times compared to double layer and multi-layer PCBs.
-
Simpler Design: Single layer PCBs have a simpler design compared to multi-layer PCBs. The circuit layout is easier to create and verify. There are fewer chances of design errors and signal integrity issues.
-
Easier Assembly: Single layer PCBs are easier to assemble compared to multi-layer PCBs. All the components are placed on one side of the board, making it easier to solder and inspect.
-
Faster Turnaround Time: Single layer PCBs have a shorter manufacturing time compared to multi-layer PCBs. The simpler design and fewer manufacturing steps result in faster production and shorter lead times.
-
Higher Yield: Single layer PCBs have a higher production yield compared to multi-layer PCBs. The simpler construction and fewer manufacturing steps result in fewer defects and higher quality.
Disadvantages of Single Layer PCBs
Despite their advantages, single layer PCBs have some limitations:
-
Limited Routing Space: Single layer PCBs have limited routing space compared to double layer and multi-layer PCBs. The circuit traces have to be routed on one side of the board, which can lead to longer traces and larger board sizes.
-
Lower Component Density: Single layer PCBs have lower component density compared to multi-layer PCBs. The components have to be placed on one side of the board, which limits the number of components that can be accommodated.
-
Lower Power Handling: Single layer PCBs have lower power handling capability compared to multi-layer PCBs. The limited copper thickness and routing space restrict the amount of current that can be carried by the traces.
-
Higher Electromagnetic Interference (EMI): Single layer PCBs are more susceptible to EMI compared to multi-layer PCBs. The longer traces and lack of ground planes can result in higher levels of radiated and conducted EMI.
Applications of Single Layer PCBs
Despite their limitations, single layer PCBs are widely used in various applications:
-
Low-Cost Consumer Electronics: Single layer PCBs are commonly used in low-cost consumer electronic devices such as toys, calculators, remote controls, and small appliances.
-
Prototype and Hobbyist Projects: Single layer PCBs are popular for prototype and hobbyist projects due to their low cost and ease of design and assembly.
-
Educational and Training Kits: Single layer PCBs are used in educational and training kits for teaching electronics and circuit design.
-
Low-Power and Low-Frequency Applications: Single layer PCBs are suitable for low-power and low-frequency applications such as LED lighting, simple sensors, and basic control circuits.
Design Considerations for Single Layer PCBs
When designing single layer PCBs, several factors need to be considered:
-
Trace Width and Spacing: The trace width and spacing should be selected based on the current carrying requirements and the minimum feature size of the PCB manufacturer. Wider traces can carry more current but occupy more space. Narrower traces occupy less space but have lower current carrying capacity.
-
Component Placement: Components should be placed to minimize the length of the traces and to avoid crossing traces. Components should also be placed to allow for easy soldering and inspection.
-
Grounding: Proper grounding is essential for reducing EMI and ensuring signal integrity. A ground plane should be used whenever possible to provide a low-impedance return path for the signals.
-
Solder Mask and Silkscreen: The solder mask and silkscreen should be designed to provide clear and accurate marking of components and test points. The solder mask openings should be sized appropriately for the component pads.
-
Manufacturing Constraints: The design should adhere to the manufacturing constraints of the pcb fabricator, such as minimum hole size, minimum trace width and spacing, and maximum board size.
FAQ
-
What is the difference between a single layer PCB and a double layer PCB?
A single layer PCB has copper traces on only one side of the substrate, while a double layer PCB has copper traces on both sides of the substrate. -
Can single layer PCBs be used for high-frequency applications?
Single layer PCBs are not recommended for high-frequency applications due to their higher susceptibility to EMI and signal integrity issues. Multi-layer PCBs with proper grounding and shielding are preferred for high-frequency applications. -
What is the maximum current carrying capacity of a single layer PCB?
The current carrying capacity of a single layer PCB depends on the thickness of the copper layer and the width of the traces. As a general rule of thumb, a 1 oz copper trace can carry about 500 mA per 0.1 inch of trace width. -
Can single layer PCBs be used for surface mount components?
Yes, single layer PCBs can be used for surface mount components. However, the component placement and trace routing may be more challenging compared to through-hole components. -
What is the typical turnaround time for single layer PCB manufacturing?
The turnaround time for single layer PCB manufacturing depends on the complexity of the design and the PCB fabricator. Typical turnaround times range from 1-2 weeks for standard designs to 3-4 weeks for more complex designs.
Conclusion
Single layer PCBs are the simplest and most cost-effective type of PCB. They consist of a single substrate layer with copper traces on one side. Single layer PCBs offer advantages such as lower cost, simpler design, easier assembly, faster turnaround time, and higher yield compared to multi-layer PCBs. However, they have limitations such as limited routing space, lower component density, lower power handling, and higher EMI susceptibility.
Despite their limitations, single layer PCBs are widely used in various applications such as low-cost consumer electronics, prototype and hobbyist projects, educational and training kits, and low-power and low-frequency applications.
When designing single layer PCBs, several factors need to be considered such as trace width and spacing, component placement, grounding, solder mask and silkscreen, and manufacturing constraints.
In conclusion, single layer PCBs are a viable option for many applications that require a simple, cost-effective, and easy-to-manufacture solution. However, for more complex and high-performance applications, multi-layer PCBs may be necessary.