Introduction
Flexible printed circuits (FPCs), also known as flex circuits or flex PCBs, are a vital component in many of today’s modern electronics. As devices continue getting smaller and more compact, flexible circuits provide the perfect interconnect solution where traditional rigid boards just won’t fit. With their ability to fold and bend, flex circuits can adapt to the most complex packaging requirements.
But the benefits of flexible PCBs go far beyond just enabling miniaturization. Their flexible and dynamic nature allows them to be configured in 3D arrangements, saving space and component real estate. The elasticity of the circuits also provides mechanical isolation against vibration and shock. In short, flex circuits deliver connectivity, power and signals – all while withstanding the tortures of today’s modern devices.
However, as with any customized electronic component, the quality and reliability of your flex circuits depend greatly on choosing the right manufacturing partner. With years of experience and expertise under their belt, a good flex PCB manufacturer will help ensure your circuits meet your exact electrical and mechanical needs. They will also build your boards efficiently, on-time and on-budget.
This article provides an in-depth overview of flex PCB technology, compares different flexible circuit laminates and cover-lays, and outlines the most important factors in selecting a flexible circuit board manufacturer. Let’s get started!
What are Flexible Printed Circuits?
Flexible printed circuits are thin, lightweight circuit boards that are made of flexible insulating substrate materials such as polyimide or polyester. Rather than being rigid like conventional FR-4 circuit boards, FPCs can bend and twist to accommodate unique form factors and space requirements.
The flexible substrate or base material is usually layered or “sandwiched” between thin copper foil conductors. The layers are bonded together with heat and adhesive pressure in a process called lamination. Etching is then used to chemically remove unwanted copper, leaving behind the desired circuit traces and features.
Components are soldered directly to the flex board traces to form a complete flexible printed circuit assembly. Connectors or crimped terminals can also be incorporated for integration with other system boards and components.
Flex circuits allow dynamic interconnections where wiring harnesses would be difficult to implement. They are very popular in consumer electronics, medical devices, industrial equipment, aerospace, and automotive applications.
Key Properties and Features
- Extremely thin profile – as low as 1 mil (0.001”) for the flex substrate
- Can twist, bend and fold to accommodate complex geometries
- Dynamic flexing over millions of cycles
- Lightweight and flexible for reduced mass and easier routing
- Low signal loss at high frequencies
- Excellent thermal performance for managing heat
- Withstands shock, vibration and flexing forces
- Allows layering and 3D configuration of circuits
- Suitable for high density component mounting
- Enables miniaturization of products
- Easier assembly than rigid boards or wire harnesses
Flex Circuit Materials and Construction
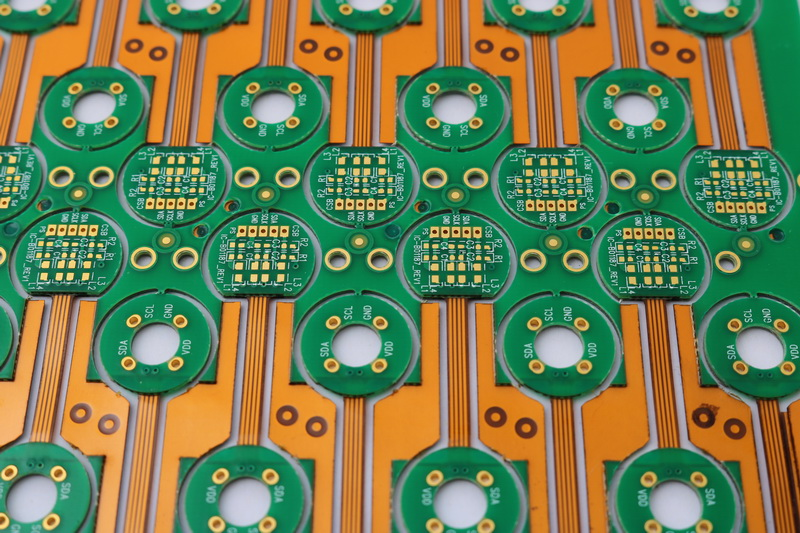
There are several important design choices that go into manufacturing a high-quality, reliable flexible circuit board. These include:
Flexible Substrate Materials
The flexible base material, also called the dielectric substrate, is the foundation of the circuit board. The substrate isolates and separates the conductive copper traces while allowing flexible bending and folding. Common options include:
- Polyimide (PI) – Most common flex substrate. Known for its heat resistance and mechanical strength. Can withstand very high temperatures.
- Polyester (PET) – More economical but has lower maximum temperature. Easy to punch and form.
- Polyethylene Naphthalate (PEN) – Related to PET but with higher temperature rating. Offers good chemical resistance.
- Fluoropolymers (PTFE) – Extremely high heat and chemical resistance. Can handle 260°C continuously.
Cover Layer Materials
Cover layers, also called coverlay or cover film, are laminated over the top and/or bottom of the circuitry to provide protection from the environment. Common options are:
- LCP (Liquid Crystal Polymer) – Extremely stable, low moisture absorption. Withstands high temps. Expensive.
- Polyimide – Provides excellent protection against scratches and abrasion. Flexible.
- Acrylic – More economical. Softens at higher temperatures. Easy to laser ablate.
Copper Foil Type
The copper foils act as the conductive element of the flex board. Varying thickness is used depending on current demands.
- Rolled Annealed – Most common, economical option. Good flex characteristics.
- Electrodeposited – Very smooth surface for fine traces. Allows smaller gaps between traces.
- Reverse Treated – Rolled copper with nodular surface for better adhesion to substrate.
Adhesive Selection
Choosing the right adhesive is key to providing a robust bond between layers. Options include:
- Acrylic – Most common. Provides good bond strength and flexibility.
- Epoxy – Strongest adhesion but more rigid. Can withstand higher temps.
- Phenolic Butyral – Flexible at low temps but becomes rigid at high temps.
Key Considerations When Choosing a Flex PCB Manufacturer
Selecting the right flexible circuit board manufacturer is critical to achieving success with your flex PCB project. Here are some of the most important factors to evaluate:
Experience and Expertise
Look for manufacturers that have extensive knowledge and experience with flexible PCB technology. They should understand the right materials to use, circuit design rules, specialized assembly processes, and testing procedures to build robust, reliable flex boards. Ask about their history and years in business.
Range of Capabilities
Your flex circuit supplier should be able to support the needs of your application with their capabilities. Do they offer:
- Various base materials, adhesives, cover films?
- Different copper weights and trace spacing/width?
- Fine line circuitry and spacing (<3 mil lines/spaces)?
- Buried and blind vias? Flex-to-rigid capabilities?
- Solder mask and legend printing options?
- Assembly services?
Quality and Certifications
Reputable flex circuit manufacturers will have certifications such as ISO 9001, IPC, or ITAR registered. They should follow strict quality processes with quality assurance testing and inspection at every stage. Ask about their capabilities in DFM, DFT and DPMO.
Customer Service and Support
Look for excellent customer service right from the start. Do they listen closely to your requirements? Are they responsive with quotes and questions? A good PCB partner will offer design support, prototyping, risk mitigation advice, and be committed to your project’s success.
Cost and Delivery
Balance costs along with capabilities and quality. The lowest cost board may be tempting but could result in extra costs later from reworks and fixes. Reasonable lead times, on-time delivery, and flexibility to meet urgent needs are also vital. Communication is key here.
Location and Logistics
If geographic proximity is important, look for domestic manufacturers. For global production, evaluate their supply chains and logistics pipelines. How do they ensure consistency across different factories? This is especially important for high-mix, low-volume flex builds.
Key Questions to Ask Prospective Flex PCB Manufacturers
Here are some suggested questions to ask potential flex circuit board manufacturers during initial discussions:
- How long have you been in the flex PCB manufacturing business? What is your core expertise?
- What types of customers do you typically work with? Do you have experience with my application industry?
- What variety of flexible materials, copper weights, and manufacturing capabilities do you offer?
- Do you have dedicated flex PCB production lines or mix with rigid PCBs? What is your minimum/maximum panel size?
- What design, simulation, DFM, and prototyping services do you provide?
- How do you ensure consistent quality across different production lots? Describe your quality processes.
- Can you meet my preliminary quantity, timeline, and budget requirements? Are there ways to optimize?
- How will you communicate during the build process and address any production issues?
- Do you offer flex-to-rigid PCB capabilities as well as flex circuit assembly?
- What type of inspection, testing, and certification services do you provide?
- Do you maintain confidentiality agreements and IP protection processes?
Carefully selecting a flexible circuit manufacturing partner based on their expertise, capabilities, quality, and service allows you to get the most value out of your flex PCB project. Investing the time upfront to evaluate prospective suppliers will pay dividends down the road with smooth manufacturing and high-quality circuit boards.
Frequently Asked Questions About Flex PCB Manufacturing
Here are answers to some commonly asked questions about flexible printed circuit boards and working with flex PCB manufacturers:
What are the typical steps in the flex PCB fabrication process?
The main steps are:
- Schematic design and layout
- Sourcing flex materials and preparing tooling
- Creating phototools of the circuit
- Laminating copper foil and dielectric layers
- Exposing and developing the photoresist
- Etching to remove unwanted copper
- Stripping photoresist
- Electrical testing and inspection
- Singulation into individual circuits
- Final functional testing
How long does it take to manufacture flex circuits?
Lead times can range from 2-8 weeks typically. Simple 2-layer flex boards can be faster with 2-3 week turnarounds, while complex multilayer circuits require longer. Ask potential suppliers for their estimated lead times.
What types of testing are performed on flex PCBs?
Standard tests include electrical continuity tests, visual inspection at multiple stages, dimensional checks, and testing of any functional elements like switches or buttons. Some other optional tests are flammability testing, flex cycle life testing, peel strength testing, and IST/netlist testing.
How are components assembled onto FPCs?
Soldering is a common method. SMT components are used and reflow or hand soldering techniques applied. Other assembly techniques include press-fit pins, heat staking, conductive epoxies, and mechanical attachments.
What file formats do I need to provide the manufacturer?
Gerber files are standard for layouts along with a bill of materials, assembly files, and any special instructions. It helps to also provide a PDF or hard copy for reference. Maintain clear communication.
How are flexible PCBs handled and stored?
Flex boards usually come rolled or folded into a compact size. Store lying flat whenever possible or with an inside bend radius larger than the minimum specified bend radius. Avoid kinking or creasing the flex board when handling it.
Conclusion
Flexible printed circuits deliver unique interconnect solutions not possible with traditional rigid circuit boards. By bending, twisting and folding into tight spaces, FPCs bring mobility, flexibility and reliability to modern electronic products.
However, successfully leveraging flex PCB technology requires choosing the right materials and construction methods along with an experienced, capable manufacturing partner. As highlighted in this guide, considerations like substrate selection, lamination expertise, and quality processes all factor into building robust, high-performing flexible circuits.
Do your due diligence to find the right flex circuit supplier. Ask questions, learn about their capabilities and process controls, request prototyping samples, and evaluate their responsiveness and communication style. The ideal flex circuit manufacturer will become an extension of your team to ensure manufacturing success. With their knowledge and capabilities supporting your product’s needs, flex PCBs provide endlessly adaptable interconnects to turn innovative ideas into reality.