Characteristics of Microwave PCBs
High-Frequency Operation
Microwave PCBs are designed to handle high-frequency signals, which require special considerations in terms of material selection, trace geometry, and component placement. The high frequencies used in microwave applications can cause signal integrity issues, such as impedance mismatches, crosstalk, and signal attenuation.
Low-Loss Materials
To minimize signal loss and maintain signal integrity, microwave PCBs are manufactured using low-loss dielectric materials, such as PTFE (polytetrafluoroethylene), Rogers materials, or ceramic substrates. These materials have a low dissipation factor and a stable dielectric constant over a wide frequency range, which helps reduce signal attenuation and distortion.
Controlled Impedance
Maintaining a consistent characteristic impedance throughout the PCB is crucial for microwave applications. Impedance mismatches can cause signal reflections, leading to signal degradation and power loss. Microwave PCBs are designed with controlled impedance traces, which are achieved by carefully selecting the dielectric material, trace width, and trace spacing.
Shielding and Grounding
Effective shielding and grounding techniques are essential in microwave PCBs to minimize electromagnetic interference (EMI) and ensure signal integrity. This can be achieved through the use of ground planes, via fencing, and proper component placement. Shielding can also be implemented using metal enclosures or compartments to isolate sensitive circuits from external interference.
Design Considerations for Microwave PCBs
Transmission Line Structures
Microwave PCBs often employ transmission line structures, such as microstrip, stripline, or coplanar waveguide, to guide high-frequency signals. These structures are designed to maintain a constant characteristic impedance and minimize signal reflections. The choice of transmission line structure depends on factors such as frequency, substrate thickness, and circuit density.
Via Design
Vias, which are used to connect different layers of the PCB, can introduce discontinuities and signal reflections in microwave circuits. To minimize these effects, special via designs, such as buried vias, blind vias, or via fencing, are employed. These techniques help maintain signal integrity and reduce unwanted resonances.
Component Selection
Selecting the appropriate components for microwave PCBs is crucial for optimal performance. Surface-mount devices (SMDs) are commonly used due to their small size and low parasitics. Components with low parasitic inductance and capacitance, such as chip resistors and capacitors, are preferred to minimize high-frequency effects. Special microwave components, such as RF connectors, filters, and amplifiers, may also be required.
Simulation and Modeling
Due to the complex nature of microwave circuits, simulation and modeling tools are essential in the design process. Electromagnetic (EM) simulation software, such as HFSS, CST, or ADS, is used to analyze the behavior of microwave structures, optimize component placement, and verify signal integrity. These tools help designers identify and mitigate potential issues before fabrication.
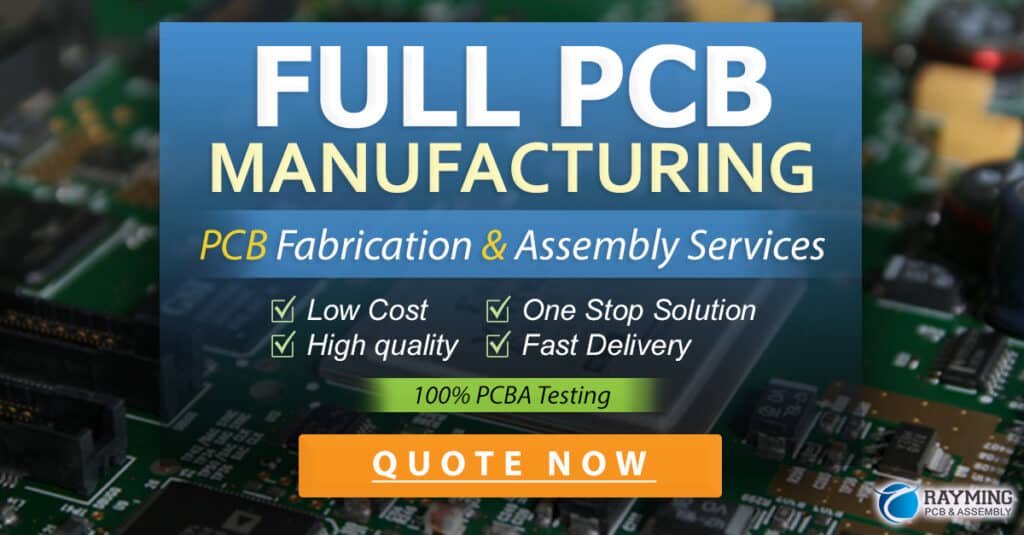
Manufacturing Processes for Microwave PCBs
Material Selection
The choice of dielectric material is critical in the manufacturing of microwave PCBs. Low-loss materials, such as PTFE or Rogers laminates, are commonly used due to their excellent high-frequency properties. The substrate thickness and dielectric constant are carefully selected based on the desired impedance and frequency range.
Fabrication Techniques
Microwave PCBs require precise fabrication techniques to ensure tight tolerances and maintain signal integrity. High-resolution photolithography is used to create fine trace geometries and accurate feature sizes. Controlled etching processes, such as wet etching or plasma etching, are employed to achieve consistent trace widths and avoid over-etching.
Multilayer Construction
Microwave PCBs often employ multilayer construction to accommodate complex circuitry and provide shielding between layers. The layers are laminated together using a high-pressure, high-temperature process to ensure proper bonding and minimize air gaps. Blind and buried vias are used to interconnect different layers while minimizing signal discontinuities.
Surface Finish
The choice of surface finish is important for microwave PCBs to ensure reliable connections and minimize signal loss. Common surface finishes include immersion silver, immersion tin, and electroless nickel/immersion gold (ENIG). The surface finish should have low insertion loss, good solderability, and be compatible with the selected components.
Testing and Verification
Rigorous testing and verification procedures are essential to ensure the performance and reliability of microwave PCBs. High-frequency testing, such as network analyzer measurements, is used to characterize the PCB’s S-parameters, insertion loss, and return loss. Time-domain reflectometry (TDR) is employed to identify impedance discontinuities and signal integrity issues. Environmental testing, such as thermal cycling and vibration testing, may also be performed to validate the PCB’s robustness.
Applications of Microwave PCBs
Microwave PCBs find applications in various industries and systems that require high-frequency signal processing. Some common applications include:
Application | Description |
---|---|
Telecommunications | Microwave PCBs are used in cellular base stations, satellite communications, and wireless networks for high-speed data transmission. |
Radar Systems | Microwave PCBs are essential components in radar systems for object detection, tracking, and imaging applications. |
Medical Devices | Microwave PCBs are used in medical imaging systems, such as MRI machines, and in microwave ablation devices for cancer treatment. |
Aerospace and Defense | Microwave PCBs are employed in avionics systems, missile guidance, and electronic warfare applications. |
Automotive Radar | Microwave PCBs are used in automotive radar systems for collision avoidance, adaptive cruise control, and parking assistance. |
Challenges and Future Trends
Designing and manufacturing microwave PCBs presents several challenges, such as:
- Increasing demand for higher frequencies and broader bandwidths
- Miniaturization and high-density packaging requirements
- Signal integrity and power integrity management
- EMI and electromagnetic compatibility (EMC) compliance
- Cost and time-to-market pressures
To address these challenges, researchers and industry professionals are exploring new materials, design techniques, and manufacturing processes. Some future trends in microwave PCB technology include:
- Adoption of advanced low-loss materials, such as liquid crystal polymers (LCPs) and high-frequency laminates
- 3D printing and additive manufacturing techniques for rapid prototyping and complex structures
- Integration of active and passive components within the PCB substrate (embedded components)
- Use of artificial intelligence (AI) and machine learning (ML) for design optimization and predictive modeling
- Development of advanced packaging solutions, such as system-in-package (SiP) and wafer-level packaging (WLP)
Frequently Asked Questions (FAQ)
-
What is the difference between a microwave PCB and a standard PCB?
Microwave PCBs are designed to operate at high frequencies (300 MHz to 300 GHz) and require special considerations in terms of material selection, trace geometry, and component placement. Standard PCBs, on the other hand, are designed for lower frequencies and have less stringent requirements. -
What materials are commonly used for microwave PCBs?
Low-loss dielectric materials, such as PTFE (polytetrafluoroethylene), Rogers materials, or ceramic substrates, are commonly used for microwave PCBs. These materials have a low dissipation factor and a stable dielectric constant over a wide frequency range, which helps reduce signal attenuation and distortion. -
Why is controlled impedance important in microwave PCBs?
Maintaining a consistent characteristic impedance throughout the PCB is crucial for microwave applications to minimize signal reflections and power loss. Impedance mismatches can cause signal degradation and reduce the overall performance of the system. -
What are some common transmission line structures used in microwave PCBs?
Common transmission line structures used in microwave PCBs include microstrip, stripline, and coplanar waveguide. These structures are designed to maintain a constant characteristic impedance and minimize signal reflections. -
How are microwave PCBs tested and verified?
Microwave PCBs undergo rigorous testing and verification procedures, such as high-frequency testing using network analyzers to characterize S-parameters, insertion loss, and return loss. Time-domain reflectometry (TDR) is used to identify impedance discontinuities and signal integrity issues. Environmental testing, such as thermal cycling and vibration testing, may also be performed to validate the PCB’s robustness.
In conclusion, microwave PCBs are specialized printed circuit boards designed to handle high-frequency signals in various applications, such as telecommunications, radar systems, and medical devices. These PCBs require careful design considerations, low-loss materials, controlled impedance, and advanced manufacturing processes to ensure optimal performance and signal integrity. As the demand for high-frequency systems continues to grow, microwave PCB technology will play a crucial role in enabling the development of cutting-edge applications and driving innovation across industries.