What does PCB stand for in lighting?
Introduction to PCB in lighting
PCB stands for “Printed Circuit Board” and refers to the electronic circuit boards inside LED lights and other lighting fixtures. The PCB controls and powers the LEDs or other light sources.
As lighting has transitioned to using more electronic components, PCBs have become an integral part of most lighting these days. Understanding what PCB means for lighting helps choose quality fixtures and troubleshoot issues.
Key roles of PCBs in lighting
Some of the key roles PCB boards play in lighting like LED bulbs and fixtures are:
- Powering the LEDs or other light sources by stepping down and transforming the AC input voltage to appropriate levels
- Controlling light output like dimming, color tuning, timing/schedules etc through integrated circuits
- Protecting the light sources and drivers from voltage spikes and anomalies
- Enabling communication and control integration with lighting control systems and protocols like DMX, DALI etc.
- Dissipating heat from the high power electronics efficiently to enhance product life
PCB Types Used in Lighting
There are a few common types of PCB used within LED lighting based on design, layout and installation position.
Metal PCBs
As the name suggests these have a metal layer sandwiched into or deposited atop the board material during manufacturing. These are better at conducting heat which lighting PCBs have to dissipate well.
Common metal PCB types are:
PCB Type | Description |
---|---|
Aluminum PCBs | Have a layer of aluminum bonded to the PCB |
Insulated Metal PCBs | Have a thin insulating layer on top of the metal base before copper tracks are laid out |
Ceramic PCBs | Use ceramic materials like Alumina or Aluminum Nitride instead of FR-4 fiberglass |
Benefits
- Better thermal performance for LED lights due to metal layer
- More rugged with reduced chance of cracking
- Resilient to higher operating temperatures
Drawbacks
- More expensive than regular PCBs
- Heavier weight
They work very well for high power LED lighting which requires good thermal design.
Flexible PCBs
These use flexible base materials instead of rigid fiberglass allowing them to bend, twist and flex during use without damage. Common flexible PCB materials are polyimide and polyester.
Benefits
- Can fit into tight spaces and small lighting enclosures
- Move dynamically without fatigue or cracks
- Easy to manufacture in higher quantities
Drawbacks
- Less rugged than standard PCB material
- Needs careful stress relief and strain protection near connections
Flexible PCBs accommodate dynamic form factors and portable lighting applications.
Rigid PCBs
The regular fiberglass PCBs with copper layers make up majority of lighting PCBs due to their durability and design flexibility. Rigid PCBs use standard FR-4 fiberglass or higher temp rated materials as base.
They can accommodate a wide variety of circuit and component complexity levels in lighting – from simple low power LED strips to complex tunable white engines. Rigid PCBs can also have portions made flexible by etching around them.
Benefits
- Rugged and durable for static installations
- Cost effective and easy to manufacture
- Supports complex multilayer circuits & tracking
Drawbacks
- Lacks flexibility for dynamic shapes
- More prone to cracking versus flex PCBs
Rigid PCBs are ubiquitous across all lighting types – from household bulbs to commercial highbay fixtures and streetlights.
Other Specialty PCBs
Some other less common but specialty PCB types seen in advanced lighting include:
Metal Core PCBs – Have dielectric layers bonded onto a metal plate which allows embedding components directly into the board while aiding heat dissipation.
CERamic PCBs – Use ceramic materials like Aluminum nitride instead of FR4 fiberglass as substrate for better thermal performance.
Aluminum Clad PCBs – Have a thick aluminum plate as the bottom layer upon which the dielectric and copper layers are added. This again helps in heat spreading.
These help meet demands of niche high power and specialty lighting like stage lights.
PCB Manufacturing Process for Lighting
Modern PCB manufacturing utilizes various chemical, mechanical and imaging processes to “print” the circuit substrates in layers which are then combined to form the boards. Understanding the manufacturing process enables better design choices and quality considerations when sourcing lighting PCBs.
Here are the key steps in fabrication of PCBs:
1. Design and Layout
The lighting circuit requirements are analyzed by PCB designers to create the schematic diagrams and board layouts using EDA (electronic design automation) software tools. These layouts prototype the traces, pads, and drill holes that transfer electricity between the different components.
2. Film Printing
The board layouts are printed on film sheets that help transfer the patterns onto the copper laminated dielectric substrate materials like FR4. These films act like photo masks shielding different areas.
3. Etching Circuit Layers
The substrate board material coated with copper foils are first cleaned and then the film is applied on top to mask off areas that will remain copper tracks. The unmasked areas are chemically etched away leaving just the desired copper traces behind.
4. Laminating Circuit Layers
Multiple etched layers with copper traces are then precisely aligned and laminated together using bonding sheets. They may be encapsulated with protective coats as well. Holes are drilled at connection points between layers and plated with conducting materials.
5. Component Assembly
Electronic components like ICs, resistors, capacitors, LEDs are then assembled on the PCB using solder paste and reflow/wave soldering techniques. Additional points are manually soldered afterward. Testing ensures quality before boards ship out.
Key Failure Modes
While LED lighting PCBs are generally reliable, some common failure modes over their lifetime include:
Thermal Stress Failures
Repeated heating and cooling cycles during LED lighting operation creates expansion/contraction stresses over time. This can crack solder joints, cause layer delamination or copper track breaks. Improper heat sinking accelerates this.
Voltage Transients
Spikes from the power lines or lightning strikes can destroy components or short delicate traces from the current surge if not adequately protected by surge suppressors.
Vibration Fatigue
In lighting applications with vibration and shocks like automotive usage, wind noise etc the shaking motion over time can crack PCBs.
Manufacturing Defects
Impurities, drilling errors, misalignment of layers and faulty component mounting during PCB fabrication can also shorten lifespan despite standard quality control checks.
Optimizing Lighting PCBs
PCB choice, design and manufacturing discipline significantly impact the costs, form factors and reliability ultimately impacting lighting product performance and field lifespan.
Here are some tips for optimizing PCBs for lighting:
Thermal Management
Prioritize thermal design with enough copper weights, thermal pads/vias. Ensure the PCB can conduct and dissipate heat adequately for LED power levels without overheating.
Protection Components
Incorporate fuses, surge suppressors, voltage regulators etc into the PCB design so transients in power line voltage do not damage the sensitive control electronics or LED arrays.
Conformal Coating
Protect the PCB surface using standard clear conformal coats. This blocks dust and moisture ingress while enhancing PCB insulation and surface mounted parts reliability. Use them for outdoor or humid area lighting.
Quality Checks
Perform design rule checks and quality inspections during PCB manufacturing process. Review signal integrity, thermal scans, solder joints, tolerances at multiple steps to screen defects early.
Modularity
Break up complex lighting PCBAs into discrete modules with interconnects. This allows replacing only the faulty module without scrapping entire PCBs during field failures besides enabling upgrades.
Future of Lighting PCBs
Lighting PCB technology continues to evolve improving miniaturization, thermal performance and intelligence integration.
Here are some trends reshaping lighting PCB landscape:
1. Embedded PCBs
Also called buried PCB technology helps embed components within the PCB layers instead of surface mounting. This shrinks thickness profile while accommodating more smart LED modules.
**2. Metal Core PCBs **
Their growing adoption addresses evolving thermal demands as LED lighting output powers increase continuously.
3. PCB Functional Integration
In addition to electrical connectivity PCBs will integrate other capabilities like light sensing, antennas for wireless controls and EV charging coils.
4. Modular Light Engines
Light engines with replaceable smart PCB modules enable upgrading luminare capabilities without full replacement.
5. Flexible and Stretchable PCBs
Curved, rollable and stretchable PCBs help realize unconventional luminaire and lighting fixture form factors.
6. Improved Reliability Testing
Test coverage expands to cover wider environments, AC voltage conditions and viral/microbial resistance matched to field deployments.
With the next generation of smarter and specialized lighting, PCB technology plays an even more significant role.
Frequently Asked Questions
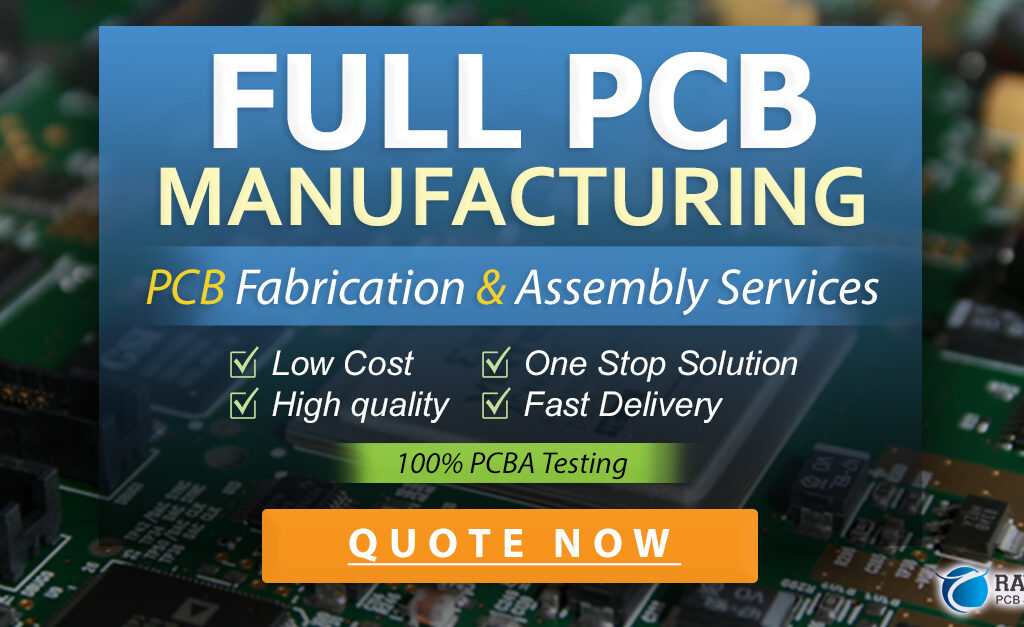
Here are some common queries regarding PCBs in LED lighting answered:
Q1. Why do LED lights use PCBs?
PCBs help power and control LED chips by transforming AC supply voltage, regulating current and enabling features like dimming, tunable color etc through integrated circuits. They also help dissipate heat from high power LED arrays.
Q2. What components make up an LED PCB?
Typical components are – LED arrays, voltage regulators, rectifiers, filters, transformers, resistors, capacitors, fuses, integrated circuits and protection devices like surge suppressors. There are also thermal pads, interconnects and structural layers.
Q3. Can damaged LED PCBs be repaired?
For low cost LED bulbs and smaller lighting, replacing the entire module/bulb is easier. But larger LED fixtures and custom luminaires are worth repairing using replacement PCBs or re-soldering joints. Modularity allows replacing individual PCB sub-assemblies as well.
Q4. Does LED PCB emit any radiation?
Properly designed LED lighting PCBs generate negligible EMI and do not emit harmful radiation as they operate under SELV (Safety Extra Low Voltage) conditions below 60V DC internal voltages complying to safety standards.
Q5. What are the best PCB materials for LED lighting?
FR-4 boards with TG130-140° c ratings are good for indoor lighting while metal core PCBs, Ceramic PCBs and thick aluminum/copper boards work very well for outdoor and highbay lighting which require superior heat conduction.