What is Contract Manufacturing?
Contract manufacturing is an arrangement in which a company (the client) outsources the production of its products or components to another company (the contract manufacturer). The contract manufacturer is responsible for producing the goods according to the client’s specifications, while the client retains control over the design, intellectual property, and distribution of the final product.
Advantages of Contract Manufacturing
- Cost Savings: By outsourcing production to a contract manufacturer, companies can reduce their capital expenditure on equipment, facilities, and labor.
- Scalability: Contract manufacturers can quickly scale up or down production based on the client’s needs, allowing for greater flexibility in response to market demands.
- Expertise: Contract manufacturers often specialize in specific production processes or industries, bringing valuable expertise and experience to the table.
- Focus on Core Competencies: Outsourcing production allows companies to focus on their core competencies, such as research and development, marketing, and sales.
Disadvantages of Contract Manufacturing
- Loss of Control: When outsourcing production, companies may have less control over the manufacturing process and quality control.
- Intellectual Property Risks: Sharing sensitive information and designs with a third party can increase the risk of intellectual property theft or infringement.
- Communication Challenges: Working with an external manufacturer can lead to communication issues, particularly if there are language or cultural barriers.
- Supply Chain Complexity: Outsourcing production adds another layer to the supply chain, which can increase complexity and potential for disruptions.
What is OEM?
OEM stands for Original Equipment Manufacturer. In this arrangement, a company designs and specifies the product, but the actual manufacturing is carried out by another company (the OEM). The OEM produces the product according to the client’s specifications, and the final product is sold under the client’s brand name.
Advantages of OEM
- Branding: The client retains full control over the branding and marketing of the product, even though it is manufactured by a third party.
- Design Control: The client has complete control over the product design and specifications, ensuring that the final product meets their requirements.
- Manufacturing Expertise: OEMs often have specialized manufacturing capabilities and expertise, allowing them to produce high-quality products efficiently.
- Reduced Investment: By partnering with an OEM, companies can reduce their investment in manufacturing infrastructure and resources.
Disadvantages of OEM
- Dependence on the OEM: The client is heavily dependent on the OEM for the production of their products, which can be a risk if the OEM experiences operational or financial issues.
- Limited Customization: While the client has control over the product design, they may have limited ability to customize the manufacturing process itself.
- Potential for Competition: If the OEM also produces similar products for other clients or under their own brand, there is a risk of competition in the market.
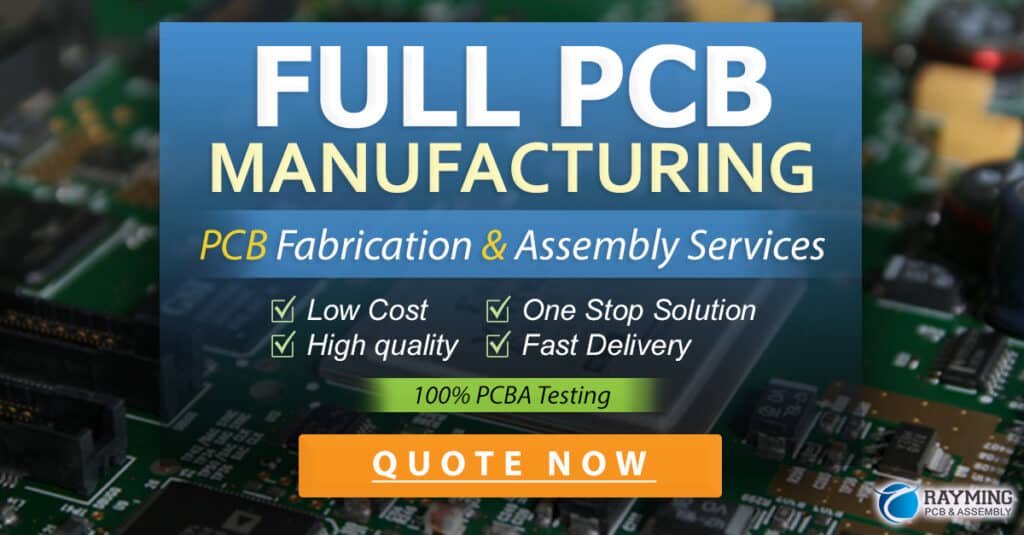
Contract Electronic Manufacturing
Contract electronic manufacturing is a specific type of contract manufacturing that focuses on the production of electronic components, assemblies, and products. This can include printed circuit board (PCB) assembly, electronics box build, cable and wire harness assembly, and more.
Advantages of Contract Electronic Manufacturing
- Access to Advanced Technology: Electronic contract manufacturers often invest in state-of-the-art equipment and processes to stay competitive, giving clients access to the latest technology without the need for significant capital investment.
- Regulatory Compliance: Electronic products are subject to various regulations and standards, such as RoHS, REACH, and UL. Contract electronic manufacturers are well-versed in these requirements and can ensure that products are compliant.
- Supply Chain Management: Contract electronic manufacturers often have established relationships with component suppliers and can help clients navigate supply chain challenges, such as component shortages or obsolescence.
- Testing and Quality Control: Electronic products require rigorous testing and quality control to ensure reliability and performance. Contract electronic manufacturers have the necessary equipment and expertise to perform these tasks.
Challenges in Contract Electronic Manufacturing
- Intellectual Property Protection: Electronic products often involve sensitive intellectual property, such as circuit designs and firmware. Ensuring the protection of this intellectual property is crucial when working with a contract manufacturer.
- Supply Chain Disruptions: The electronic component supply chain is complex and can be subject to disruptions due to various factors, such as natural disasters, geopolitical events, or pandemics. Contract electronic manufacturers must have robust risk management strategies in place to mitigate these disruptions.
- Skilled Labor Availability: The production of electronic products requires skilled labor, such as electronics engineers and technicians. In some regions, there may be a shortage of these skilled workers, which can impact production capacity and lead times.
- Rapid Technological Change: The electronics industry is characterized by rapid technological change, with new components and processes constantly emerging. Contract electronic manufacturers must stay up-to-date with these changes to remain competitive and meet client needs.
Comparison Table: Contract Manufacturing vs. OEM
Aspect | Contract Manufacturing | OEM |
---|---|---|
Production | Outsourced to a third party | Outsourced to a third party |
Design Control | Client retains control | Client retains control |
Branding | Client’s brand | Client’s brand |
Manufacturing Process Control | Contract manufacturer has control | OEM has control |
Customization | Possible, but may be limited | Limited |
Intellectual Property | Shared with contract manufacturer | Shared with OEM |
Supply Chain Management | Contract manufacturer may assist | OEM may assist |
Investment in Infrastructure | Reduced for client | Reduced for client |
Frequently Asked Questions (FAQ)
-
Q: Can a company use both contract manufacturing and OEM?
A: Yes, a company can use both contract manufacturing and OEM for different products or components, depending on their specific needs and requirements. -
Q: How do I choose between contract manufacturing and OEM?
A: The choice between contract manufacturing and OEM depends on various factors, such as the level of control you need over the manufacturing process, your branding strategy, and your investment in manufacturing infrastructure. Consider your specific needs and priorities when making this decision. -
Q: What should I look for in a contract electronic manufacturer?
A: When choosing a contract electronic manufacturer, look for factors such as their experience and expertise in your industry, their manufacturing capabilities and technology, their quality control processes, and their ability to protect your intellectual property. Additionally, consider their location, communication skills, and financial stability. -
Q: How can I ensure the quality of products produced by a contract manufacturer or OEM?
A: To ensure product quality, establish clear quality standards and specifications, conduct regular audits and inspections of the manufacturing facility, and implement robust quality control processes. Additionally, maintain open communication with your contract manufacturer or OEM and address any issues promptly. -
Q: What are the risks associated with outsourcing manufacturing to a foreign country?
A: Outsourcing manufacturing to a foreign country can involve risks such as intellectual property theft, communication challenges, cultural differences, and geopolitical instability. Additionally, there may be longer lead times and potential supply chain disruptions due to the distance and complexity of international logistics. Carefully evaluate these risks and develop mitigation strategies before outsourcing to a foreign manufacturer.
Conclusion
While contract manufacturing and OEM share similarities in outsourcing production to a third party, they differ in the level of control over the manufacturing process and the relationship between the client and the manufacturer. Contract electronic manufacturing is a specialized form of contract manufacturing that focuses on the production of electronic components and products.
When deciding between contract manufacturing and OEM, companies must consider their specific needs, priorities, and risks. Factors such as control over the manufacturing process, branding strategy, intellectual property protection, and supply chain management should be carefully evaluated.
Ultimately, the choice between contract manufacturing and OEM depends on the unique circumstances of each company and product. By understanding the advantages, disadvantages, and challenges associated with each approach, companies can make informed decisions that optimize their production processes, reduce costs, and maintain a competitive edge in the market.