Introduction to Online PCB Design
Online PCB (Printed Circuit Board) design has revolutionized the way engineers and hobbyists create electronic circuits. With the advent of powerful online tools and resources, designing PCBs has become more accessible, efficient, and cost-effective than ever before. In this comprehensive guide, we’ll explore the world of online PCB design, providing you with the knowledge and resources necessary to embark on your own PCB design journey.
What is PCB Design?
Before diving into online PCB design, let’s first understand what PCB design entails. PCB design is the process of creating a layout for the electronic components and the connections between them on a printed circuit board. The design process involves several stages, including schematic capture, component placement, routing, and verification.
PCB design is crucial for the proper functioning and reliability of electronic devices. A well-designed PCB ensures optimal signal integrity, minimizes electromagnetic interference, and facilitates efficient manufacturing.
Advantages of Online PCB Design
Online PCB design offers several advantages over traditional desktop-based design tools. Here are some key benefits:
-
Accessibility: Online PCB design tools are accessible from anywhere with an internet connection, allowing you to work on your designs remotely and collaborate with team members seamlessly.
-
Cost-effectiveness: Many online PCB design platforms offer free or low-cost options, making it affordable for individuals and small businesses to access professional-grade design tools.
-
Ease of use: Online PCB design tools often have user-friendly interfaces and intuitive workflows, making it easier for beginners to get started with PCB design.
-
Collaboration: Online platforms enable real-time collaboration, allowing multiple designers to work on the same project simultaneously, streamlining the design process.
-
Instant feedback: Online PCB design tools provide instant feedback on design rules violations, helping you catch and fix errors early in the design process.
Getting Started with Online PCB Design
Now that we understand the basics of PCB design and the advantages of online tools, let’s explore how to get started with online PCB design.
Choosing an Online PCB Design Tool
The first step is to choose an online PCB design tool that suits your needs and budget. Here are some popular options:
-
EasyEDA: EasyEDA is a free, web-based PCB design tool that offers schematic capture, PCB layout, and simulation capabilities. It has a user-friendly interface and supports collaboration.
-
Upverter: Upverter is another web-based PCB design platform that provides schematic capture, PCB layout, and version control features. It offers both free and paid plans.
-
CircuitMaker: CircuitMaker is a free, community-driven PCB design tool from Altium. It provides a comprehensive set of features for schematic capture and PCB layout.
-
PCBWeb Designer: PCBWeb Designer is a browser-based PCB design tool that offers schematic capture, PCB layout, and 3D visualization. It has a clean interface and supports import/export of various file formats.
Consider factors such as ease of use, feature set, pricing, and community support when choosing an online PCB design tool.
Learning PCB Design Fundamentals
Before diving into online PCB design, it’s essential to have a solid understanding of PCB design fundamentals. Here are some key concepts to familiarize yourself with:
-
Schematic capture: Schematic capture involves creating a graphical representation of the electronic circuit using symbols and interconnections.
-
Component placement: Component placement is the process of arranging the electronic components on the PCB layout in a logical and efficient manner.
-
Routing: Routing involves creating the copper traces that connect the components on the PCB. It requires consideration of signal integrity, manufacturing constraints, and design rules.
-
Design rules: Design rules are guidelines that ensure the manufacturability and reliability of the PCB. They include specifications for trace width, clearance, hole size, and more.
There are numerous online resources, tutorials, and courses available to help you learn PCB design fundamentals. Some popular resources include:
- SparkFun Electronics’ PCB Design Tutorial
- KiCad’s Getting Started Guide
- Altium Academy’s PCB Design Courses
- EEVblog’s PCB Design Tutorial Series
Investing time in learning PCB design fundamentals will provide a strong foundation for your online PCB design journey.
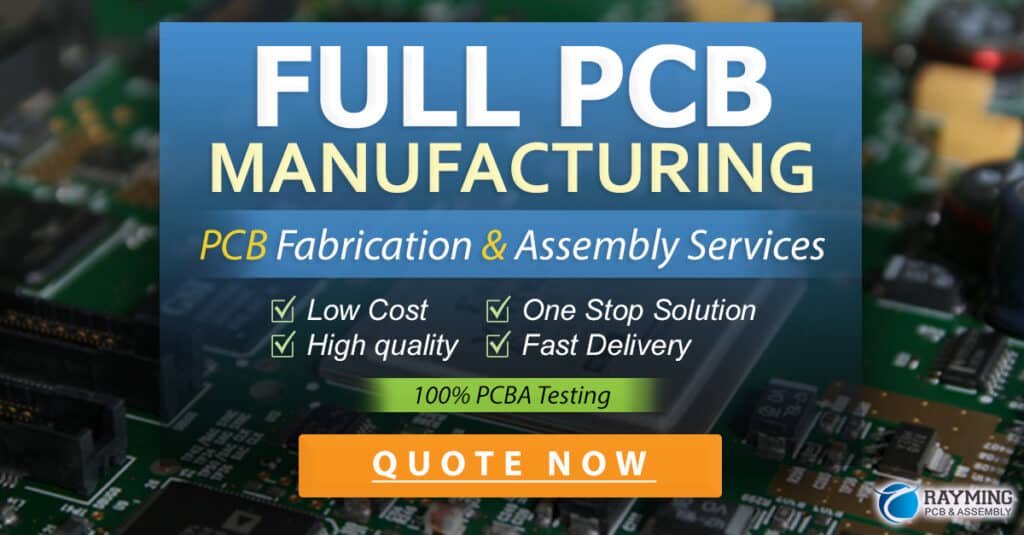
Online PCB Design Workflow
Once you have chosen an online PCB design tool and familiarized yourself with the fundamentals, it’s time to dive into the design workflow. Here’s a typical online PCB design workflow:
1. Schematic Capture
The first step in online PCB design is to create a schematic diagram of your electronic circuit. The schematic captures the logical connections between components using symbols and nets.
Here are some best practices for schematic capture:
- Use consistent and clear naming conventions for components and nets
- Organize the schematic into logical sections or hierarchies
- Add appropriate annotations and notes for clarity
- Perform a thorough review of the schematic for errors and inconsistencies
2. Component Placement
After completing the schematic, the next step is to place the components on the PCB layout. Component placement plays a crucial role in the overall performance and manufacturability of the PCB.
Consider the following guidelines when placing components:
- Group related components together to minimize trace lengths and improve signal integrity
- Consider the mechanical constraints and enclosure requirements
- Ensure proper clearances between components for manufacturing and assembly
- Optimize component placement for thermal management and electromagnetic compatibility
Online PCB design tools often provide automatic component placement features, but it’s essential to review and refine the placement manually for optimal results.
3. Routing
Once the components are placed, the next step is to route the connections between them using copper traces. Routing is a critical stage in PCB design, as it directly impacts signal integrity and manufacturability.
Here are some routing best practices:
- Follow the design rules specified by the manufacturing process and the online PCB design tool
- Use appropriate trace widths and clearances based on the signal requirements and current carrying capacity
- Minimize the use of vias and layer changes to improve signal integrity and manufacturing yield
- Consider the return current paths and maintain proper grounding techniques
- Perform a design rule check (DRC) to identify and resolve any rule violations
Online PCB design tools provide automated routing features, such as auto-routing and push-and-shove routing, which can significantly speed up the routing process. However, it’s crucial to review and manually refine the routing for critical signals and high-speed interfaces.
4. Verification and Output Generation
Before finalizing your PCB design, it’s essential to perform a thorough verification to ensure the design meets all requirements and is ready for manufacturing. Online PCB design tools provide various verification features, such as:
- Design rule checking (DRC) to identify any rule violations
- Electrical rule checking (ERC) to verify the schematic and PCB connectivity
- 3D visualization to check for mechanical clearances and component fit
- Simulation tools to analyze signal integrity and power delivery
Once the design is verified, the final step is to generate the output files required for manufacturing. Online PCB design tools typically support the generation of the following files:
- Gerber files: These are the industry-standard files used for PCB fabrication, containing information about the copper layers, solder mask, and silkscreen.
- Drill files: These files specify the location and size of the holes on the PCB for component mounting and vias.
- Bill of Materials (BOM): The BOM lists all the components used in the PCB design, along with their quantities and part numbers.
- Assembly drawings: These drawings provide instructions for PCB assembly, indicating component placement and orientation.
Collaborating in Online PCB Design
One of the significant advantages of online PCB design is the ability to collaborate with team members seamlessly. Online platforms enable real-time collaboration, version control, and project management features.
Here are some tips for effective collaboration in online PCB design:
- Use clear and consistent naming conventions for files, components, and nets
- Establish a version control system to track changes and maintain a history of the design
- Use comments and annotations to communicate design decisions and updates with team members
- Leverage online collaboration features, such as real-time editing and chat, to streamline communication and decision-making
- Define roles and responsibilities within the team to ensure efficient workflow and avoid conflicts
Collaboration in online PCB design allows teams to work together efficiently, regardless of their geographical location, leading to faster design iterations and improved project outcomes.
Advanced Topics in Online PCB Design
As you gain experience in online PCB design, you may encounter more advanced topics and techniques. Here are a few areas to explore:
High-Speed PCB Design
Designing PCBs for high-speed applications, such as high-frequency digital interfaces or RF circuits, requires additional considerations. High-speed PCB design techniques include:
- Impedance matching and controlled impedance routing
- Signal integrity analysis and simulation
- Electromagnetic compatibility (EMC) considerations
- Use of advanced materials, such as low-loss dielectrics and high-frequency laminates
Online PCB design tools often provide simulation and analysis features to support high-speed design, helping you optimize signal integrity and minimize electromagnetic interference.
Flexible and Rigid-Flex PCB Design
Flexible and rigid-flex PCBs offer unique advantages in terms of packaging and mechanical flexibility. Designing these types of PCBs requires additional considerations, such as:
- Material selection and stack-up design
- Bend radius and bend area design
- Strain relief and mechanical support
- Manufacturing constraints and design rules
Online PCB design tools may provide specific features and libraries for flexible and rigid-flex PCB design, enabling you to create layouts that meet the mechanical and electrical requirements of your application.
Design for Manufacturing (DFM)
Design for Manufacturing (DFM) is the practice of designing PCBs with manufacturing considerations in mind. DFM techniques help improve the manufacturability, reliability, and cost-effectiveness of your PCB design.
Some key DFM considerations include:
- Adhering to the manufacturing process design rules
- Optimizing component placement and orientation for assembly
- Using standard component packages and footprints
- Minimizing the use of vias and layer changes
- Incorporating testability features, such as test points and boundary scan
Online PCB design tools often provide DFM analysis and feedback, helping you identify and resolve manufacturing issues early in the design process.
Resources and Community
As you embark on your online PCB design journey, it’s essential to tap into the vast resources and community available to support your learning and growth. Here are some valuable resources:
- Online forums and communities, such as EEVblog Forum, StackExchange Electronics, and Reddit’s /r/PrintedCircuitBoard
- PCB design blogs and tutorials, such as Hackaday, Dangerous Prototypes, and Sparkfun’s PCB Design Tutorial
- Online courses and training, such as Coursera’s Introduction to PCB Design and Udemy’s PCB Design Courses
- Reference designs and open-source hardware projects, such as Arduino and Raspberry Pi
- Manufacturer resources and design guidelines, such as Altium’s Design Hub and Texas Instruments’ PCB Design Resources
Engaging with the PCB design community allows you to learn from experienced designers, seek advice, and stay updated with the latest trends and techniques in online PCB design.
Frequently Asked Questions (FAQ)
-
What is the best online PCB design tool for beginners?
EasyEDA and CircuitMaker are popular choices for beginners due to their user-friendly interfaces and extensive learning resources. However, the best tool depends on your specific needs and preferences. -
Can I design complex PCBs using online tools?
Yes, online PCB design tools have evolved to support complex designs, including high-speed interfaces, flexible PCBs, and advanced manufacturing techniques. However, for highly specialized applications, desktop-based tools may offer more advanced features and customization options. -
How do I ensure my PCB design is manufacturable?
To ensure manufacturability, follow the design rules provided by your chosen manufacturing process and online PCB design tool. Perform design rule checks (DRC) and review your design with a manufacturability mindset. Engage with the manufacturer early in the design process to address any specific requirements or constraints. -
Can I import and export PCB designs between different online tools?
Most online PCB design tools support common file formats, such as Gerber and ODB++, allowing you to import and export designs between different tools. However, it’s essential to verify the compatibility and ensure the design integrity is maintained during the transfer process. -
How can I learn advanced PCB design techniques?
To learn advanced PCB design techniques, explore online resources such as tutorials, courses, and forums dedicated to PCB design. Engage with the PCB design community, attend workshops and conferences, and work on progressively complex projects to gain hands-on experience and expertise.
Conclusion
Online PCB design has revolutionized the way engineers and hobbyists create electronic circuits, offering accessibility, cost-effectiveness, and collaborative features. By understanding the fundamentals of PCB design, choosing the right online tools, and following best practices, you can embark on your own PCB design journey and bring your electronic ideas to life.
Remember to continuously learn and explore advanced topics, engage with the PCB design community, and leverage the vast resources available online. With dedication and practice, you can master the art of online PCB design and create innovative and reliable electronic products.
Happy designing!
PCB Design Stage | Key Considerations |
---|---|
Schematic Capture | – Consistent naming conventions – Logical organization and hierarchy – Thorough review for errors and inconsistencies |
Component Placement | – Grouping related components – Mechanical constraints and enclosure requirements – Proper clearances and thermal management |
Routing | – Design rule adherence – Appropriate trace widths and clearances – Minimizing vias and layer changes – Proper grounding techniques |
Verification | – Design rule checking (DRC) – Electrical rule checking (ERC) – 3D visualization for mechanical clearances – Simulation for signal integrity and power delivery |
Output Generation | – Gerber files for PCB fabrication – Drill files for holes and vias – Bill of Materials (BOM) – Assembly drawings for component placement |