Introduction
When designing a Flexible printed circuit board (Flex PCB), one of the key considerations is determining the right copper thickness for the application. The copper thickness impacts the durability, conductivity, current carrying capacity, weight, flexibility, and cost of the Flex PCB. This article provides a detailed overview of the factors to consider when selecting copper thickness for Flex PCBs and recommends thickness values based on common applications.
What is Flex PCB Copper Thickness?
The copper thickness of a Flex PCB refers to the thickness of the copper foil used to create the conductive traces and pads on the flexible circuit board. It is typically measured in ounces per square foot (oz/ft2) or micrometers (μm). Some common copper weights used in Flex PCB design include:
- 1 oz (35 μm)
- 1⁄2 oz (18 μm)
- 1⁄4 oz (9 μm)
- 1⁄8 oz (5 μm)
Thinner copper provides maximum flexibility and minimum weight, while thicker copper offers higher durability and current carrying capacity.
Key Factors in Choosing Flex PCB Copper Thickness
Several important factors should be considered when selecting the appropriate copper thickness for a Flex PCB design:
Durability
Thicker copper foil is more durable and resistant to damage during handling and repeated flexing. It is less prone to cracking over time.
Conductivity and Current Carrying Capacity
Thicker copper has higher conductivity allowing more current to flow without overheating. This provides higher current carrying capacity.
Flexibility
Thinner copper allows tighter bending radiuses and greater flexibility of the circuit board.
Weight
Thinner copper is lighter in weight. This is important for lightweight and wearable devices.
Cost
Thicker copper is more expensive, increasing material costs.
Manufacturability
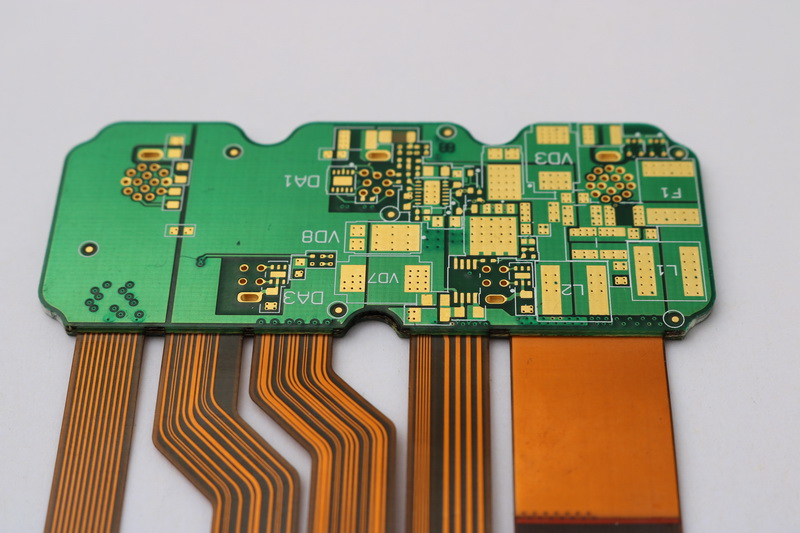
Very thin copper below 1⁄4 oz may be more prone to handling damage during manufacturing.
Recommended Copper Thickness Based on Application
The optimal copper thickness depends on the specific application and requirements of the Flex PCB design.
Application | Recommended Thickness |
---|---|
Wearable devices | 1/8 to 1/4 oz (5 to 9 μm) |
Dynamic flexing circuits | 1/4 to 1/2 oz (9 to 18 μm) |
High current/power devices | 1/2 to 1 oz (18 to 35 μm) |
Extreme flexibility required | 1/8 oz (5 μm) |
Minimal weight critical | 1/8 to 1/4 oz (5 to 9 μm) |
Low cost consumer electronics | 1/4 to 1/2 oz (9 to 18 μm) |
Here are some typical copper thickness usages:
- Medical wearables: 1/8 oz
- IoT devices: 1/4 to 1/2 oz
- Mobile consumer electronics: 1/2 oz
- High power LED lighting: 1 oz
- Server/computer flex circuits: 1 oz
Design Guidelines for Different Copper Weights
Follow these best practice design guidelines for different copper foil thicknesses in your Flex PCB layouts:
1/8 oz Copper
- Use for simplest single-sided circuits only
- Avoid small cutouts and openings
- Simplify routing without dense traces or complex geometries
- Use large bend radii over 0.125” (3mm)
- Reduce handling during assembly and allow for rework
1⁄4 oz Copper
- Suitable for double-sided flexible circuits
- Moderate bend radii down to 0.075” (2mm) are possible
- Small cutouts under 0.2” (5mm) should be avoided
- Some dense routing acceptable
1⁄2 oz Copper
- Ideal for multilayer flex circuits
- Tight bend radii down to 0.05” (1.3mm) achievable
- Dense routing, small cutouts, and complex geometry okay
- Can withstand more assembly and testing handling
1 oz Copper
- Used for maximum durability in high-wear applications
- Extreme bending or dynamic flexing still requires larger radii
- Allows very dense routing and intricate layouts
- Withstands rugged use in automotive, military, aerospace
Frequently Asked Questions
What is the most common copper thickness used in Flex PCBs?
1/2 oz (18 μm) copper thickness is the most commonly used across many consumer and industrial Flex PCB applications, providing a good balance of flexibility, durability, and cost. High volume consumer electronics often use thinner 1/4 or 1/8 oz copper.
How thin can Flex PCB copper go?
Extremely thin copper down to 0.5 oz (7 μm) is possible, however handling, manufacturability, and reliability may suffer. Most designers use 1/8 oz (5 μm) as the practical lower limit.
Can different copper thicknesses be used in one Flex PCB?
Yes, it is possible to use different copper weights in different areas of the same Flex PCB design, allowing optimization for durability, current capacity, or flexibility in specific regions. This adds complexity.
Does thicker copper increase manufacturing costs?
Yes, using thicker copper does result in a higher material cost. However, the extra durability and reliability often justify the small additional cost for many applications.
Can you solder components to thin 1/8 oz copper?
Soldering to very thin 1/8 oz copper is possible but requires care to avoid damage or lifting pads. Consider using adhesive or clamping connections with thin copper circuits. Rework is also challenging.
Conclusion
Selecting the appropriate copper thickness in Flex PCB design requires balancing flexibility, weight, cost, manufacturability, and electrical performance. Typical thickness values range from 1/8 oz (5 μm) for extremely flexible wearables up to 1 oz (35 μm) for maximum durability and current capacity. Following the recommendations and guidelines in this article will help ensure you choose the right copper thickness for your next Flex PCB design.