Flexible printed circuit boards (flex PCBs) provide unique capabilities for bending and dynamic flexing in electronic devices. But what is the cost for these versatile boards? The pricing for flex PCBs depends on several key factors.
Flex Circuit Cost Factors
The main drivers of cost for flex PCBs are:
- Layer count – number of conductive layers
- Quantity – volume of boards required
- Size – dimensions of the flex circuit
- Thickness – overall thickness of the board
- Material – type of flexible substrate used
- Tolerance – precision of trace spacing and features
- Flexibility – degree of dynamic bending needed
- Reliability – environmental robustness and life cycling
- Testing – level of quality verification required
- Certifications – specialized qualifications like medical or military
Optimizing these factors allows flex PCB sourcing at the most competitive price point.
How Layer Count Impacts Cost
The number of conductive layers is typically the biggest contributor to flex PCB pricing. Each additional layer adds cost for materials, lamination, and production processes.
Single Layer Flex PCBs
These are the most cost effective. Pricing is in the range of:
- Prototyping – $100 to $500
- Low volume – $20 to $100 per board
- Medium volume – $10 to $50 per board
- High volume – Below $10 per board
Two Layer Flex PCBs
With two conductive layers, costs increase approximately 30-50% over single layer boards.
- Prototyping – $150 to $600
- Low volume – $30 to $150 per board
- Medium volume – $15 to $75 per board
- High volume – Below $15 per board
Multilayer Flex PCBs
Additional layers add cost at an increasing rate. Expect approximately 50-90% more per layer.
- 4-6 Layers – $250 to $800 prototyping. $50 to $250 per board in volume.
- 8+ Layers – $500 to $2000 prototyping. $100 to $500 per board in volume.
So layer count is generally the biggest factor determining flex PCB pricing.
Quantity Impact on Flex PCB Cost
Economies of scale play a major role in pricing for flex PCB production. Larger quantities see dramatic reductions in cost. Some example pricing at different volumes:
Quantity | Single Layer Cost | Two Layer Cost |
---|---|---|
1-10 boards | $250-500 each | $400-800 each |
10-50 boards | $100-200 each | $150-300 each |
50-100 boards | $50-100 each | $75-150 each |
100-500 boards | $20-50 each | $30-75 each |
500-1,000 boards | $10-20 each | $15-30 each |
1,000+ boards | Below $10 each | Below $15 each |
Pricing drops significantly going from prototyping to pilot builds to volume production runs.
Flex Circuit Size and Cost Relations
Larger board sizes do tend to cost more due to higher material usage. However, for a given board size, more compact layouts with tighter trace spacing and via pitch can cost more due to higher fab tolerances. Some size and cost examples:
- Small board (<50mm x 50mm) – $100 to $200 each in medium volumes
- Medium board (50mm x 100mm) – $150 to $300 each in medium volumes
- Large board (100mm x 150mm) – $200 to $400 each in medium volumes
- Extra large board (150mm x 200mm) – $300 to $500 each in medium volumes
But a compact complex layout can cost much more than a simple layout of the same size. Dense flex PCBs require higher fabrication precision.
Flex Circuit Thickness and Cost
Thinner flex circuits allow tighter dynamic bending, but thicker boards provide more rigidity. Here are some thickness and cost examples in medium volumes:
- 25 micron (1 mil) – $200 to $300 per board
- 50 micron (2 mil) – $150 to $250 per board
- 75 micron (3 mil) – $100 to $200 per board
- 100 micron (4 mil) – $75 to $150 per board
The specialized materials and handling for thinner flex PCBs adds cost. Thicker boards tend to be lower cost.
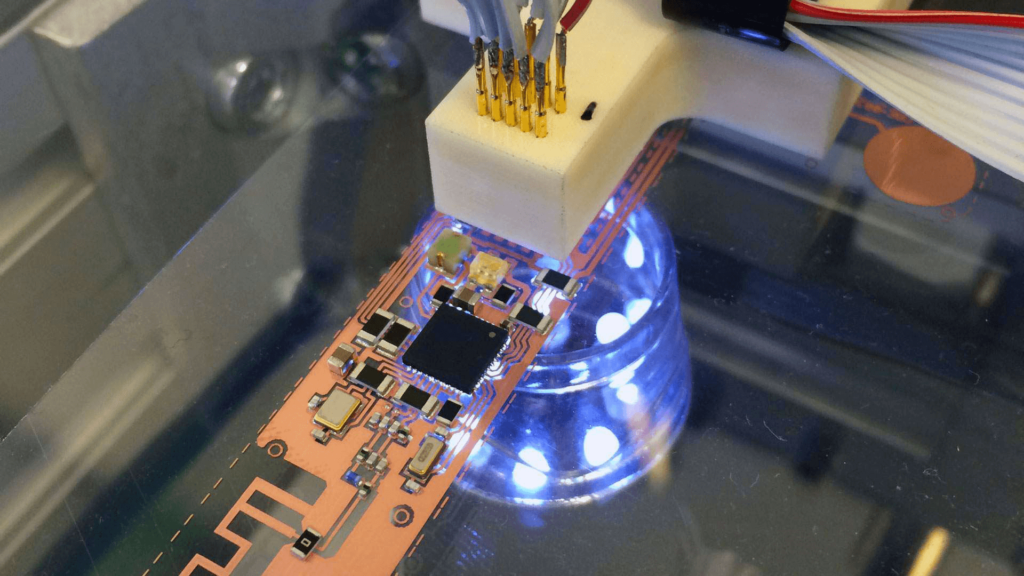
Flexible Materials and Cost Implications
The flexible substrate material also impacts cost:
- Polyimide (Kapton) – Most common flex material offers good value.
- Polyester (PET) – More economical but with lower temperature rating.
- PI Composite – Reinforced polyimide for ruggedness at added cost.
- Peek – High temp polymer with excellent chemical resistance but expensive.
- Liquid Crystal Polymer (LCP) – Extremely durable with tight tolerances but higher cost.
Selecting the right flex material is key. Paying more for LCP may be justified for harsh environments, while PET can reduce cost in benign applications.
Tolerance Effects on Flex PCB Expenses
Tighter tolerances for trace spacing, line width, hole size, and registration add cost for flex PCB production requiring more precise fabrication and measurement. Some examples:
- Standard tolerances (~+/- 0.1mm) – Base pricing
- Tight tolerances (~+/- 0.05mm) – 25-50% cost increase
- Ultra-fine tolerances (~+/- 0.02mm) – 100-200% cost increase
It’s critical to specify only the tolerance needed rather than overspecifying. Work with your flex PCB partner on the right tolerances.
Flexible Circuit Cost Per Layer
Analyzing cost on a per layer basis helps optimize designs. Typical ranges for small/medium volume production:
- Rigid PCBs – $100 to $200 per layer
- Flex PCBs – $300 to $500 per layer
- Rigid-Flex PCBs – $200 to $300 per layer
So flex layer costs are higher than rigid PCB layers due to specialized materials and processes. Rigid-flex offers a cost optimization.
Effects of Flexing Requirements on Price
More extreme dynamic flexing capabilities increase costs. Key considerations:
- Standard flexibility – Small premium for flex PCB
- Tight bend radii – Moderate cost increase
- Motorized flexing – Significant cost impact
- Low cycle life (>100k) – Base pricing
- High cycle life (>1M) – Major added cost
It’s critical to carefully specify only the flexing needed for the application rather than “overflexing.”
Reliability Effects on Flex PCB Costs
Mission-critical flex PCBs requiring high reliability and durability involve additional costs for design, materials, testing, and process controls. Some examples:
- Consumer electronics – Low cost
- Automotive – Moderate added cost
- Medical devices – Major cost increase
- Aerospace/defense – Highest cost
Reliability standards like IPC 6013 for space, defense, and aerospace applications require the most rigorous quality systems at added expense.
Testing and Certification Impacts on Expense
Extensive testing and formal certifications like UL recognition can increase costs but also reduce risks. Some examples:
- Standard quality testing – Base cost
- IPC testing per IPC 6013 – 25% cost increase
- UL recognition – 50-100% cost increase
- ISO certification – 10-25% cost increase
- IATF 16949 (automotive) – 25-50% cost increase
Consider the value of testing, inspection, and certification vs. the costs.
Additional Factors Influencing Flex PCB Expenses
Some other considerations affecting cost include:
- Special requirements – Outgassing, low smoke/fumes, contamination control
- IP considerations – NREs for custom IP, non-recurring engineering
- Low volume challenges – Higher costs for prototypes, small batches
- Design complexity – High component density, blind/buried vias
- Component integration – Embedding actives and passives
- Aftermarket – Inventory stocking, custom packaging, global delivery
Careful consideration of these factors allows cost optimization of flex PCB designs and production.
Frequently Asked Questions on Flex PCB Pricing
What is a typical cost per flex PCB?
For medium volumes, typical per board pricing is $200 to $500 for rigid-flex, $150 to $300 for two layer flex, and $50 to $150 for single layer flex. Costs drop significantly in high volume.
What factors most impact flex PCB costs?
The number of conductive layers, order volume, board size, flex circuit thickness, materials, tolerances, flexing requirements, and reliability needs most affect cost.
How much more does flex PCB cost vs rigid PCB?
In general, flex PCBs cost about 2-3 times as much as rigid boards on a per layer basis due to specialized materials and processes. But reduced interconnects can offset this.
Can flex PCBs cost less than rigid PCBs?
In some cases, yes for very high layer count boards. The ability to fabricate complex rigid-flex PCBs as a single integrated unit can lower cost compared to using multiple rigid boards with connectors.
How can I reduce costs for my flex PCB?
Ways to lower cost include reducing layers, design complexity, tolerances, flexing requirements, and performance testing as appropriate. Increased volumes will also dramatically lower pricing.
Conclusion
While flex PCB fabrication does involve higher costs than standard rigid boards, the benefits of these extremely versatile circuits justify the additional expenses in many applications. By optimizing design, production, and testing processes with an experienced flex PCB partner, overall costs can be effectively managed.CopyRetry