Introduction to Flex PCB Adhesives
Adhesives play a critical role in the construction of flex PCBs (flexible printed circuit boards). They bond the flexible material layers together and provide electrical isolation between conductors. The adhesive must withstand repeated dynamic flexing without cracking or losing bond strength. With the right adhesive, a flex PCB can achieve a long flex life span.
Flex PCBs use polyimide films like Kapton or UPILEX as the flexible dielectric layer. These films provide the flex capability but need adhesive to laminate multiple layers into a circuit board. The key requirements of the adhesive include:
- Flexible when cured
- Bonds strongly to polyimide films
- Electrically isolates conductors
- Tolerates processing chemicals and soldering temperatures
- Prevents copper wicking between layers
There are different classes of adhesives used in flex PCBs depending on the type of construction and performance requirements.
Types of Flex PCB Adhesives
Here are the three main types of adhesives used in flex PCB lamination:
Acrylic Adhesives
- Most common adhesive for rigid-flex PCBs
- Provide high bond strength between polyimide layers
- Soften and flow at lamination temperatures
- Cross-link during cure into a flexible thermoset polymer
- Excellent resistance to most chemicals
Epoxy Adhesives
- Two-part epoxies mixed just before lamination
- Lower moisture absorption than acrylics
- Recommended for tight-pitch components
- Withstand flexing but more rigid than acrylics
- Require freezer storage to extend pot life
Urethane Adhesives
- Single-part thermoplastic adhesives
- Moderate flexibility when cured
- Low water absorption properties
- Lower lamination temperatures
- Short shelf life of 6-12 months
Acrylic adhesives are most common due to good flex properties, while epoxies provide tight-pitch soldering capability. Urethanes fill niche applications.
Adhesive Film Types
The adhesive is applied as a partially cured dry film sandwiched between the polyimide layers. The films soften during lamination and then fully cure during the heat cycle. There are three types of adhesive films:
Unsupported Films
- Adhesive film without a carrier layer
- Thickness around 0.002″ (50 μm)
- Available in roll or sheet form
- Less stable, requires cold storage
- Bonds multiple layers for multilayer flex boards
Supported Films
- Adhesive film on one side of a polyimide carrier
- Total thickness around 0.005″ (125 μm)
- Stable at room temperature
- Allows double-sided lamination in one pass
Double-Treated Films
- Adhesive film on both sides of a polyimide carrier
- Total thickness around 0.007″ (175 μm)
- Allows simultaneous lamination of three layer flex stackup
- Cold storage may be needed for stability
Unsupported films allow greater layer count, while supported films simplify lamination.
Adhesive Properties
The adhesive must have the right properties to function successfully in a flex PCB over the product lifetime. Some key considerations:
Flexibility
The cured adhesive should be flexible enough to withstand repeated bending and dynamic flex cycles. Acrylics have the best flex performance.
Bond Strength
It must maintain a strong bond to the polyimide layers through the full range of movement without delamination or cracking.
Electrical Isolation
The adhesive needs to electrically isolate between conductors on adjacent layers with high insulation resistance.
Environmental Resistance
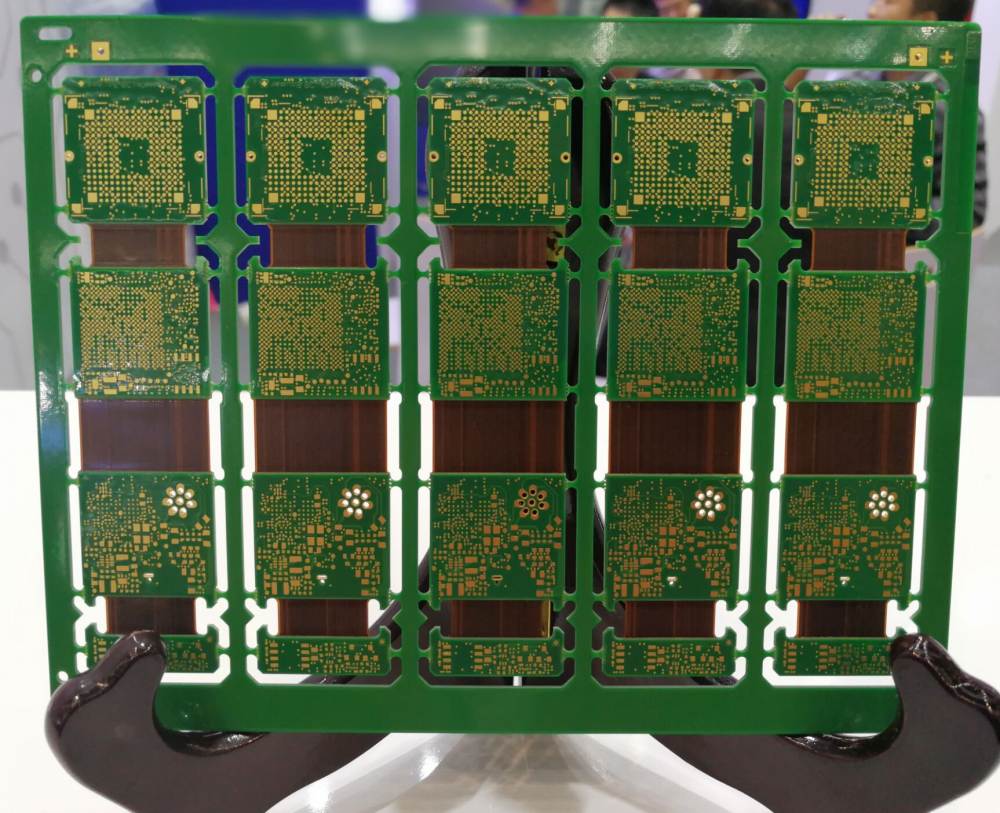
It must withstand moisture, thermal cycling, UV exposure, and processing chemicals without degrading performance.
Copper Wicking Prevention
The adhesive inhibits wicking action that can allow copper traces to grow between polyimide layers and create electrical shorts.
Dielectric Constant
A stable and low dielectric constant allows high frequency performance and controlled impedance traces.
Coefficient of Thermal Expansion (CTE)
A CTE matched to polyimide prevents separation or cracking from thermal cycling stress.
Flex PCB Lamination Process
The adhesive films are a key part of the multilayer lamination process for flex PCBs:
- Sheet Cutting – The adhesive films are cut into sheets sized for the PCB panel.
- Thaw – Frozen acrylic films are allowed to thaw if stored below freezing temperature.
- Layer Stackup – Conductive and adhesive layers are stacked in the press book to define the layer sequence.
- Vacuum Preparation – Air pockets are removed from the stack through vacuum holes.
- Lamination – The book is loaded in the heated press and pressure is applied for over an hour.
- Curing – The partially cured adhesive softens and flows during lamination, then fully cures during the heat cycle to form strong bonds.
- Cool Down – The bonded panel is cooled under low pressure before unloading from the press.
- PCB Fabrication – The panel then undergoes conventional PCB processes like drilling, plating, patterning etc.
Adhesive Selection Factors
Choosing the right adhesive involves evaluating multiple factors:
- Layer count – Thinner for more layer flex boards
- Flexibility needs – Acrylics better for dynamic flexing
- Environmental exposure – Epoxies resist harsh conditions
- Production volume – Additional film types for niche runs
- Shelf life – Supported films more stable than unsupported
- Copper wicking – Acrylics generally prevent better
- High frequency – Tight dielectric constant control
- Cost – Adhesive is around 15-25% of flex PCB cost
Test boards should be prototyped with adhesive options to validate performance for the application.
Flex PCB Adhesive Suppliers
Some leading companies supplying adhesive films for flex PCB applications include:
Rogers Corporation
- Offer R/flex 2000 series acrylic unsupported films
- Also supply supported and double-treat options
- Shelf life up to 1 year when frozen
- Films available in roll or sheet form
Epec LLC
- Provide Pyralux LF acrylic unsupported adhesive films
- Also offer LF C foil-supported films with PET carrier
- Products aimed at high layer count multilayer flex boards
Dow Chemical Company
- Manufacture Dow VORASTRONG flexible epoxy adhesives
- Used for applications requiring tight pitch components
- Offer film form and liquid/paste dispensable epoxies
FQA About Flex PCB Adhesives
Here are answers to some common questions about adhesives used in flex PCBs:
Q: Why are acrylic adhesives preferred over epoxies for typical flex PCB applications?
A: Acrylics offer better flexibility when cured, higher adhesion strength, more stable dielectric properties, easier handling, and longer shelf life compared to epoxies. The added flexibility allows acrylic bonded flex boards to better survive repeated bending motions.
Q: How is bonding strength measured between the adhesive and polyimide layers in a flex PCB?
A: A common test method is called the copper peel strength test. Copper is plated onto the polyimide surface and then pulled perpendicular to the bond interface. The measured force required to delaminate divided by the width gives the bond strength in psi or N/mm.
Q: Can solder mask be applied over the flexible bending areas of a flex PCB?
A: It is generally not recommended since most solder masks will crack during flexing. Flexible coatings like urethane or silicone conformal coating can be selectively applied to only the rigid areas.
Q: What is the typical thickness of the adhesive layer between two polyimide films in a multilayer flex PCB?
A: A standard thickness is around 0.0025-0.003 inches (25-50 μm). High layer count boards may use thinner 12 μm adhesive films while complex rigid-flex boards can use thicker films near 0.006 inches.
Q: How long can thawed unsupported adhesive films be kept at room temperature before deteriorating?
A: Maximum room temperature storage time is around 4-7 days once removed from freezer storage. The films will start to lose tack and bond strength as the B-stage adhesive partially advances.