Introduction
High-Density Interconnect (HDI) Printed Circuit Boards (PCBs) are at the forefront of modern electronics design, enabling the development of smaller, faster, and more efficient devices. As consumer electronics, medical devices, automotive systems, and aerospace technologies continue to evolve, the demand for HDI PCBs has grown significantly. HDI PCBs offer higher wiring density, improved signal integrity, and enhanced performance compared to traditional PCBs. However, designing HDI PCBs requires a deep understanding of advanced design techniques, materials, and manufacturing processes.
This article provides a comprehensive guide to HDI PCB design, covering the fundamentals, benefits, design considerations, and best practices for creating high-performance HDI PCBs.
What is HDI PCB?
Definition
HDI PCBs are a type of printed circuit board that features higher wiring density per unit area than conventional PCBs. This is achieved through the use of finer lines and spaces, smaller vias, and higher connection pad density. HDI PCBs typically incorporate microvias, blind vias, and buried vias, which allow for more complex routing and compact designs.
Key Features of HDI PCBs
- Microvias: Microvias are small vias with diameters typically less than 150 microns. They are used to create connections between different layers of the PCB, enabling higher density and more complex routing.
- Blind and Buried Vias: Blind vias connect an outer layer to one or more inner layers, while buried vias connect inner layers without reaching the outer layers. These vias help reduce the overall size of the PCB and improve signal integrity.
- Fine Lines and Spaces: HDI PCBs use finer trace widths and spacing, allowing for more connections in a smaller area.
- High Layer Count: HDI PCBs often have a higher number of layers compared to traditional PCBs, enabling more complex designs and better signal routing.
- Advanced Materials: HDI PCBs use advanced materials with better electrical properties, such as low dielectric constant and low loss tangent, to improve signal integrity and performance.
Benefits of HDI PCB Design
1. Miniaturization
One of the primary benefits of HDI PCBs is the ability to create smaller and more compact electronic devices. The use of microvias, fine lines, and high layer counts allows designers to pack more functionality into a smaller footprint. This is particularly important for portable devices like smartphones, wearables, and IoT devices.
2. Improved Signal Integrity
HDI PCBs offer improved signal integrity due to shorter signal paths, reduced parasitic capacitance and inductance, and better impedance control. This is crucial for high-speed digital and RF applications, where signal integrity is critical for performance.
3. Enhanced Performance
The higher wiring density and advanced materials used in HDI PCBs contribute to enhanced electrical performance. This includes better power distribution, reduced electromagnetic interference (EMI), and improved thermal management.
4. Increased Reliability
HDI PCBs are designed with reliability in mind. The use of advanced materials and manufacturing processes results in PCBs that are more robust and less prone to failure. Additionally, the reduced number of interconnects and shorter signal paths minimize the risk of signal degradation and failure.
5. Cost Efficiency
While HDI PCBs may have higher initial design and manufacturing costs, they can lead to cost savings in the long run. The reduced size and weight of HDI PCBs can lower material and shipping costs. Additionally, the improved performance and reliability can reduce the need for costly redesigns and repairs.
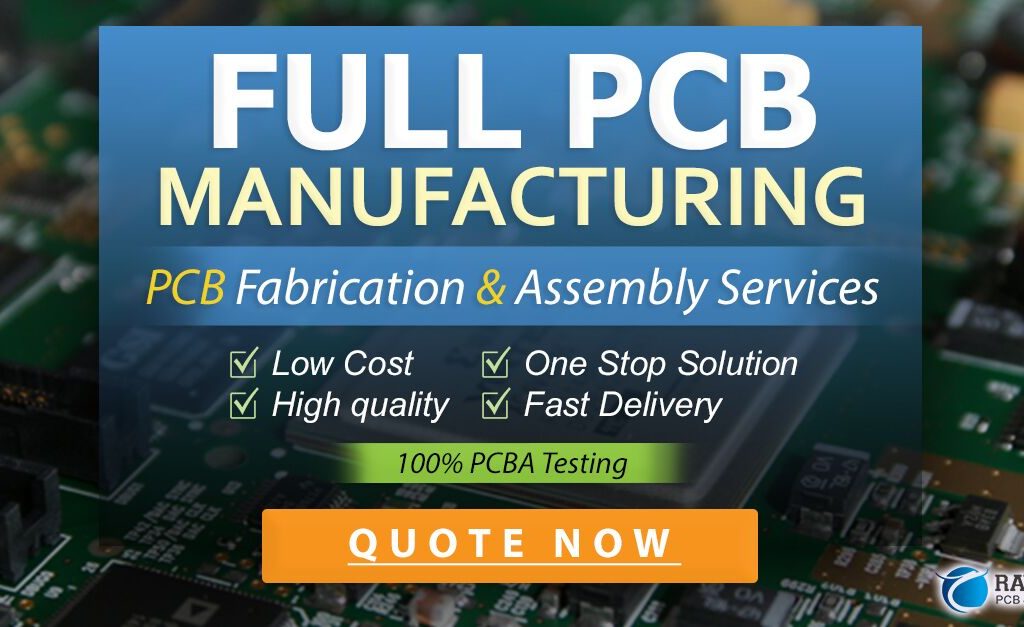
HDI PCB Design Considerations
1. Layer Stackup
The layer stackup is a critical aspect of HDI PCB design. It determines the arrangement of signal, power, and ground layers, as well as the placement of microvias, blind vias, and buried vias. Key considerations for layer stackup include:
- Signal Integrity: Ensure that signal layers are properly separated by ground or power planes to minimize crosstalk and EMI.
- Impedance Control: Design the stackup to achieve the desired impedance for high-speed signals.
- Thermal Management: Consider the thermal properties of the materials and the placement of thermal vias to manage heat dissipation.
2. Via Types and Placement
The choice and placement of vias are crucial for HDI PCB design. Common via types used in HDI PCBs include:
- Microvias: Used for high-density interconnects, typically with diameters less than 150 microns.
- Blind Vias: Connect an outer layer to one or more inner layers without passing through the entire board.
- Buried Vias: Connect inner layers without reaching the outer layers, allowing for more complex routing.
Key considerations for via placement include:
- Signal Routing: Use vias to optimize signal routing and minimize signal path lengths.
- Thermal Management: Place thermal vias near heat-generating components to improve heat dissipation.
- Manufacturability: Ensure that via placement complies with manufacturing capabilities and design rules.
3. Trace Width and Spacing
HDI PCBs use finer trace widths and spacing to achieve higher wiring density. Key considerations for trace width and spacing include:
- Current Carrying Capacity: Ensure that trace widths are sufficient to carry the required current without excessive heating.
- Impedance Matching: Design trace widths and spacing to achieve the desired impedance for high-speed signals.
- Manufacturability: Ensure that trace widths and spacing comply with manufacturing capabilities and design rules.
4. Material Selection
The choice of materials is critical for HDI PCB performance. Key considerations for material selection include:
- Dielectric Constant: Choose materials with a low dielectric constant to minimize signal delay and loss.
- Loss Tangent: Select materials with a low loss tangent to reduce signal attenuation at high frequencies.
- Thermal Properties: Consider the thermal conductivity and coefficient of thermal expansion (CTE) of materials to manage heat dissipation and ensure reliability.
- Mechanical Properties: Ensure that materials have the necessary mechanical strength and flexibility for the intended application.
5. Signal Integrity
Signal integrity is a critical consideration for HDI PCBs, especially in high-speed and RF applications. Key considerations for signal integrity include:
- Impedance Control: Design trace widths, spacing, and layer stackup to achieve the desired impedance for high-speed signals.
- Crosstalk: Minimize crosstalk by properly spacing signal traces and using ground or power planes as shields.
- Reflections: Use proper termination techniques to minimize signal reflections and ensure clean signal transitions.
- EMI: Implement shielding and filtering techniques to reduce electromagnetic interference.
6. Power Integrity
Power integrity is essential for ensuring stable and reliable power delivery to all components on the PCB. Key considerations for power integrity include:
- Power Distribution Network (PDN): Design a robust PDN with low impedance to ensure stable voltage levels and minimize noise.
- Decoupling Capacitors: Place decoupling capacitors near power pins to filter high-frequency noise and provide local energy storage.
- Voltage Drop: Ensure that trace widths and lengths are sufficient to minimize voltage drop and ensure adequate power delivery.
7. Thermal Management
Thermal management is critical for ensuring the reliability and performance of HDI PCBs. Key considerations for thermal management include:
- Heat Dissipation: Use thermal vias, heat sinks, and thermal pads to dissipate heat from high-power components.
- Material Selection: Choose materials with good thermal conductivity to improve heat dissipation.
- Component Placement: Place heat-generating components away from sensitive components and ensure adequate airflow.
8. Manufacturability
Designing for manufacturability is essential for ensuring that HDI PCBs can be produced reliably and cost-effectively. Key considerations for manufacturability include:
- Design Rules: Follow the design rules and guidelines provided by the PCB manufacturer to ensure that the design can be manufactured.
- Tolerances: Account for manufacturing tolerances in the design, including trace widths, spacing, and via sizes.
- Testing: Include test points and design for testability (DFT) to facilitate testing and debugging during manufacturing.
Best Practices for HDI PCB Design
1. Collaborate with Manufacturers
Collaborate closely with PCB manufacturers early in the design process to ensure that the design meets their capabilities and requirements. This includes discussing layer stackup, via types, material selection, and design rules.
2. Use Advanced Design Tools
Use advanced PCB design tools that support HDI design features, such as microvias, blind vias, and buried vias. These tools can help optimize the design for signal integrity, power integrity, and manufacturability.
3. Optimize Layer Stackup
Optimize the layer stackup to achieve the desired electrical performance, thermal management, and manufacturability. Consider using simulation tools to analyze the impact of different stackup configurations on signal integrity and power integrity.
4. Minimize Signal Path Lengths
Minimize signal path lengths by using direct routing and placing components close to their connections. This helps reduce signal delay, reflections, and crosstalk.
5. Implement Proper Grounding
Implement proper grounding techniques, including the use of ground planes, ground vias, and star grounding, to minimize noise and ensure stable reference voltages.
6. Use Simulation and Analysis Tools
Use simulation and analysis tools to evaluate the design for signal integrity, power integrity, and thermal performance. This can help identify and address potential issues before manufacturing.
7. Follow Design for Manufacturability (DFM) Guidelines
Follow DFM guidelines to ensure that the design can be manufactured reliably and cost-effectively. This includes adhering to design rules, tolerances, and testing requirements.
8. Conduct Prototype Testing
Conduct prototype testing to validate the design and identify any issues that may not have been apparent during simulation and analysis. This includes electrical testing, thermal testing, and environmental testing.
Conclusion
HDI PCB design is a complex and challenging process that requires a deep understanding of advanced design techniques, materials, and manufacturing processes. By following the principles and best practices outlined in this guide, designers can create high-performance HDI PCBs that meet the demands of modern electronic devices. Whether you’re designing for consumer electronics, medical devices, automotive systems, or aerospace applications, the key to successful HDI PCB design lies in careful planning, collaboration with manufacturers, and the use of advanced design tools and simulation techniques.
As technology continues to evolve, the importance of HDI PCBs will only grow. By staying informed about the latest trends, materials, and design techniques, you can stay ahead of the curve and create innovative, reliable, and high-performance HDI PCBs that push the boundaries of what’s possible in electronics design