Flexible printed circuit boards (flex PCBs) are made from different types of flexible materials that can bend and flex repeatedly without breaking. Choosing the right flex PCB material is crucial for designing a circuit board that can withstand the mechanical stresses of constant motion and vibration. This article provides an overview of the most common materials used for manufacturing flex PCBs and their key properties and applications.
Common Flex PCB Materials
There are several types of flexible materials that can be used to fabricate flex PCBs. The most common options include:
Polyimide
Polyimide film is the most widely used base material for flex PCBs. The two main types of polyimide used are:
- Kapton – Developed by DuPont, Kapton polyimide offers excellent mechanical, electrical, and high temperature properties. It has high tensile strength and can withstand repeated bending.
- Apical – An alternative to Kapton, Apical polyimide provides similar benefits in terms of flexibility, durability, and heat resistance. It is generally cheaper than Kapton.
Key properties and applications:
- Withstands high temperatures (up to 400°C)
- Chemically inert and resistant to solvents
- High tensile strength and dielectric strength
- Used for dynamic flexing applications like medical devices, aerospace, and consumer electronics
Polyester
Polyester films like PET (polyethylene terephthalate) provide good flexibility and dielectric strength. However, they have lower maximum operating temperatures compared to polyimide. The key types of polyester films are:
- PET (Polyethylene terephthalate) – Most common polyester film used for flex PCBs. Offers good flexibility.
- PEN (Polyethylene naphthalate) – Modified version of PET that can withstand higher temperatures.
Key properties and applications:
- Inexpensive and easily available
- Softens at higher temperatures (~150°C)
- Withstands repeated bending and flexing
- Used for low-cost consumer electronics and LCD displays
Polyurethane
Polyurethane films have rubber-like properties. They are extremely flexible and elastic. Some of the key properties include:
- Can withstand repeated bending and stretching
- Excellent chemical and abrasion resistance
- Typically coated with acrylic adhesive to bond with copper
- Used for applications requiring high elasticity like wearable devices
LCP (Liquid Crystal Polymer)
LCP films have highly ordered polymer chains that provide superior mechanical properties. Some key characteristics:
- Withstands very high temperatures (up to 250°C)
- Low moisture absorption and high chemical resistance
- Expensive compared to other flex PCB materials
- Used in advanced electronics in defense, aerospace, and automotive industries
Comparison Between Materials
Here is a comparison of some key properties of the common flex PCB materials:
Material | Maximum Temperature | Dielectric Strength | Cost |
---|---|---|---|
Polyimide (Kapton) | 400°C | Excellent | Moderate |
Polyester (PET) | 120-150°C | Moderate | Low |
Polyurethane | 130°C | Good | Moderate |
LCP | 250°C | Excellent | High |
Factors for Selecting Flex PCB Materials
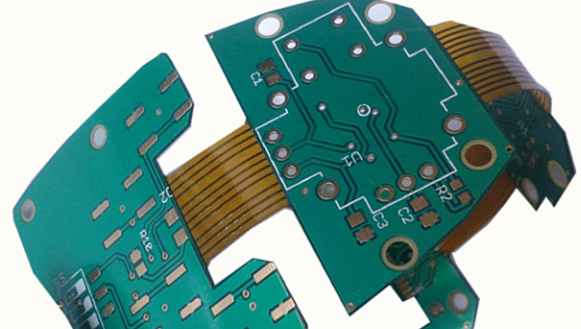
Some key considerations when selecting materials for flex PCB design:
- Operating temperature – The material should withstand max operating temps without losing structural integrity. Polyimide works for high temperature apps.
- Flexibility – If the circuit will undergo constant bending stress, material should have high flex life like polyurethane.
- Chemical resistance – Applications with exposure to chemicals and solvents require chemically resistant films like polyimide or LCP.
- Dielectric strength – Materials should have sufficient insulation resistance for reliable performance.
- Cost – Polyester is suitable for low-cost consumer electronics. For advanced apps, polyimide or LCP may be preferred despite higher costs.
- Adhesion – The material must bond properly with conductive copper traces. Adhesion promoters may be required.
- Mechanical properties – Important parameters like tensile strength, elongation, tear resistance need consideration for dynamic flexing.
- Production factors – Compatibility with processing methods like etching, plating, lamination. Ease of handling and machining.
Conclusion
Polyimide films dominate the flex PCB market due to their exceptional mechanical properties and high heat tolerance. But materials like polyester and polyurethane work well for cost-sensitive and highly elastic applications respectively. The trends point toward wider adoption of advanced materials like LCPs for miniaturized electronics. The material choice ultimately depends on the application requirements like temperature range, flexibility needs, chemical exposure, and cost. As flex PCBs become integral to more products, manufacturers are developing innovative materials with improved properties to enable their continuing evolution.
Frequently Asked Questions
Q1. What are some pros and cons of Kapton polyimide film?
Some key pros and cons of Kapton polyimide film:
Pros:
- Withstands very high temperatures up to 400°C.
- Excellent tensile strength and tear resistance.
- Good chemical resistance and electrical insulation properties.
- High flex life supporting dynamic bending applications.
- Relatively low moisture absorption compared to other polymers.
Cons:
- Expensive compared to other flex PCB materials like polyester.
- Requires adhesive coating or surface treatment to improve copper adhesion.
- Kapton tape adhesive can leave residue during removal.
- More complex processing compared to thermoplastic films like PET or TPU.
Q2. When should I use polyester or PET instead of polyimide?
Here are some reasons to consider polyester (PET) instead of polyimide:
- For applications with lower temperature requirements below 150°C where polyimide is overkill.
- If the flex PCB will not undergo too much dynamic flexing or bending stress. Polyester has lower flex life than polyimide.
- For consumer electronics where cost is a major driving factor. Polyester is cheaper than polyimide.
- If the circuit will not be exposed to chemicals like solvents that can damage polyester. Polyimide offers better chemical resistance.
- For static flex PCB applications like membrane switch keypads where high flex life is not needed.
- For simpler flex PCB fabrication since polyester processing has fewer steps compared to polyimide.
Q3. How are flexible PCBs laminated?
There are three main lamination methods used in manufacture of flex PCBs:
Thermal Lamination: Uses heat and adhesive films to bond flex layer materials. Layers are stacked along with adhesive films and heated under pressure to bond them. Allows bonding different materials.
Thermal Adhesiveless Lamination: Uses combination of heat and pressure without adhesive films. Materials must be thermoplastic like polyimide. Lower cost, but only compatible materials can be bonded.
Ultrasonic Lamination: Uses ultrasonic acoustic vibrations to create bond between layers. Energy director geometries are etched into layers to focus energy. Allows lower temperature bonding but requires complex tooling.
Factors like lamination temperature, pressure levels, and time durations must be optimized for each material combination. Cleanliness is critical for achieving reliable lamination quality.
Q4. How can flex PCB reliability be improved?
Here are some ways to improve reliability of flex PCBs:
- Use base materials like polyimide that can withstand bending stresses.
- Optimize board thickness – thinner more flexible boards bend easier without cracking.
- Eliminate sharp corners and edges with smooth curves and rounded joints.
- Anchor flexible sections of the PCB to relieve stresses.
- Adopt tear-stop features like copper filled vias at stress points.
- Implement redundant traces in high-flex areas for redundancy.
- Use elastic conductive adhesives to reduce cracks in joints.
- Implement test coupons with serpentine conductors to validate flex life.
- Perform cyclic bending tests to qualify design performance under flexing.
- Avoid use of brittle solders; use flexible solder-free assembly methods.
- Improve adhesion between material layers through surface treatments.
Q5. What are some emerging trends in flexible PCB materials?
Some emerging trends include:
- Development of nano-materials like graphene to enable thinner, stronger flexible circuits.
- Using stretchable inks to print elastic interconnects on flexible substrates.
- Adopting flexible glass materials like willow glass for optoelectronic flex circuits.
- Using flexible hybrid electronics (FHE) integrating flex PCBs with silicon ICs.
- Embedding actuation capabilities through smart materials like shape memory polymers.
- Interest in bio-degradable materials for environmentally friendly transient electronics.
- Expanding use of flex-rigid PCBs combining thin polyimide with rigid FR4 substrates.
- Leveraging metal foils and films as alternative conductors to copper traces.
- Commercialization of liquid crystal polymer (LCP) films for high frequency and extreme environment applications.