Flexible printed circuit boards (flex PCBs) provide a versatile interconnect solution for electronics in applications where rigid printed circuit boards are impractical. Their flexible construction allows flex PCBs to bend and flex to accommodate space constraints and allow dynamic movement in products. However, with increased capability comes increased cost. This article will provide a detailed breakdown of the factors that contribute to flex PCB pricing.
Flex PCB Base Material Cost
The flexible base material is a major contributor to overall flex PCB cost. There are many types of flex circuit base materials available, with polyimide being one of the most common.
Polyimide Flex Material
Polyimide (PI) films like Kapton provide an excellent flexible base for printed circuits. However, polyimide is more expensive than the rigid FR-4 substrates commonly used for rigid PCBs.
Polyimide Film Thickness vs. Cost
Thickness | Typical Cost |
---|---|
25 μm | $1.00/dm^2 |
50 μm | $2.00/dm^2 |
75 μm | $3.00/dm^2 |
100 μm | $4.00/dm^2 |
In general, thicker polyimide films provide better mechanical support but come at a higher cost.
Other Flexible Substrate Materials
Other flexible substrate materials include:
- PET (Polyethylene terephthalate): Lower cost but less heat resistant than polyimide.
- PEN (Polyethylene naphthalate): Similar properties to PET but with better temperature resistance.
- PEEK (Polyether ether ketone): Excellent thermal properties but more expensive.
- Fluoropolymer films: Expensive but with excellent chemical resistance.
The base material choice will depend on the application requirements. Low volume and prototype runs may use cheaper materials like PET, while high reliability flex circuits will justify premium polyimide or fluoropolymer films.
Flex PCB Layer Count
Increasing the layer count of a flex PCB allows more complex circuitry but also increases cost. Each additional conductive copper layer must be separated by a dielectric adhesive material. More layers require more process steps during fabrication.
Typical Flex PCB Layer Cost
Layer Count | Typical Cost |
---|---|
1 Layer | $100-200 |
2 Layers | $150-300 |
4 Layers | $250-450 |
6 Layers | $350-550 |
High layer count flex PCBs approaching 8 to 10 layers are possible but quite expensive due to the additional process complexity.
Flex PCB Size
Larger flex PCB sizes are generally more expensive than smaller boards, since more base material is required. However, the pricing is not linear, since setup costs and minimum charges will factor in.
For example, a simple 2 layer 75mm x 75mm flex PCB may cost $50 while a 150mm x 150mm board of the same design may cost $90. The area increased by 4X but the cost less than doubled.
There are other factors like panel utilization where smaller PCBs are grouped together to maximize the area used. So flex PCB size should be optimized to balance cost and the design requirements.
Flex PCB Shape
Unusual flex PCB shapes can increase cost due to challenges associated with manufacturing processes and material utilization. Simple rectangular boards are the most cost effective. Here are some examples:
- Rectangular boards: Lowest cost option
- Circular boards: Requires additional fabrication steps
- Complex shapes: Drive up cost through material waste
When possible, choose a standard rectangular PCB outline and orientation to minimize cost. 3D flex PCBs or complex shapes may be necessary in some applications but expect a price premium.
Flex PCB Tolerances
Holding tight tolerances on flex PCB features adds to fabrication time and cost. Typically the board tolerances scale with the part size.
Typical Flex PCB Tolerance Guidelines
Feature | Tolerance |
---|---|
Board Dimensions | ±0.2mm |
Line Width/Spacing | ±0.1mm |
Hole Size | ±0.1mm |
Hole to Hole | ±0.2mm |
Hole to Pad | ±0.1mm |
Tighter tolerances can often be achieved but usually involve additional cost. Communicate any tolerance requirements to your flex PCB manufacturer early in the design process.
Flex PCB Bend Radii
Flexing a PCB repeatedly induces stresses which can cause traces to crack. Minimum bend radii guidelines must be followed to build in adequate flexibility. Using a larger bend radius than the minimum increases reliability but also increases material use and cost.
Common Flex PCB Minimum Bend Radii
Flex Type | Inside Bend Radius | Outside Bend Radius |
---|---|---|
Dynamic | 3X Material Thickness | 5X Material Thickness |
Static | 1X Material Thickness | 3X Material Thickness |
A dynamic application with frequent flexing needs a larger bend radius than a static installation to prevent conductor cracking.
Flex PCB Stiffeners
Discrete stiffeners made from materials like acrylic or polyimide are often added to flex PCBs. They provide mechanical support to certain areas while allowing others to remain flexible.
Typical Flex PCB Stiffener Cost Considerations
- Material cost
- Additional fabrication to mount stiffeners
- Potential for increased board layers
- Can reduce minimum bend radii
While stiffeners provide an important reinforcement function, they also increase cost through added materials, process steps, and complexity.
Flex PCB Covers and Encapsulation
Protective covers, encapsulation, and coatings safeguard flex PCB traces from environmental damage. Options range from simple solder mask overcoat to complete silicone potting.
Typical Protective Covering Costs
- Conformal coating: $0.08 – $0.40 per square inch
- Solder masking: $0.12 – $0.24 per square inch
- Kapton tape: $0.25 – $0.50 per square inch
- Silicone potting: $0.50 – $1.00 per square inch
As expected, liquid potting and thick covers like silicone represent the highest material cost. But the additional process steps must also be accounted for.
Flex PCB Design Complexity
More complex flex PCB designs require longer fabrication times and additional process considerations. Here are some examples:
- Fine features like small traces and spaces
- High layer counts
- Plated through holes
- Controlled material thickness and heavy copper
Expect to pay a premium for high density interconnects (HDI) using microvias, blind vias, and other technologies pushing flex PCB capabilities.
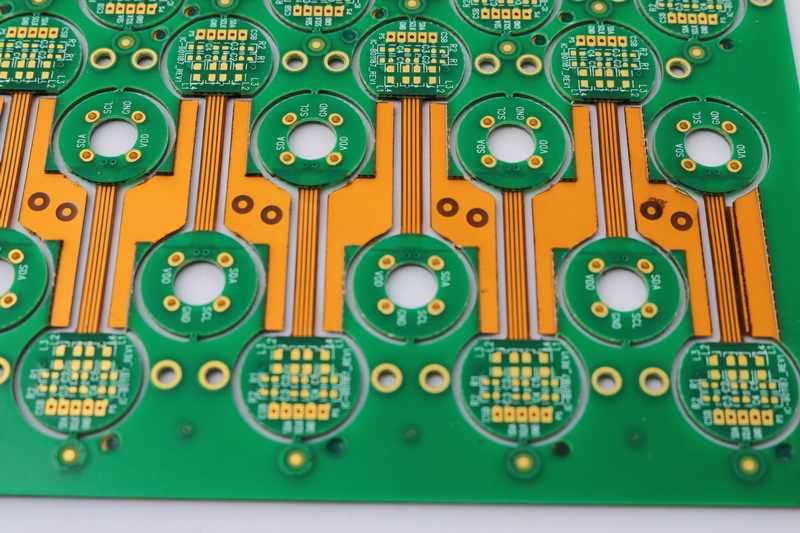
Flex PCB Quantity Ordered
As with any PCB fabrication, flex circuit pricing is dependent on quantity. Typically, a larger order volume provides some economy of scale savings.
Sample Flex PCB Costs
Quantity | Cost per board |
---|---|
1-10 boards | $200-300 |
10-25 boards | $100-150 |
50-100 boards | $75-125 |
100+ boards | $50-100 |
Note that NRE (non-recurring engineering) costs involve the initial design setup, which is independent of quantity. Amortizing these costs over a larger production run reduces the cost per flex PCB board.
Prototype vs. Production Flex PCB Fabrication
Prototype and low volume flex PCB production involves additional handling considerations that increase cost when compared to high volume production:
- Manual material handling steps
- Multiple machine setups
- Lower panel utilization efficiency
- More inspection and testing overhead
Even with the same design, expect prototype and short run prices to be 50-100% higher than large production orders.
Optimizing Flex PCB Cost Through Design and Supply Chain
There are opportunities throughout the design and manufacturing processes to optimize flex PCB cost. Here are some key strategies:
Simplify Layout and Limit Layers
Denser flex PCB layouts with more layers add fabrication complexity and cost but aren’t always necessary. Look for ways to simplify the schematic circuitry and layout while still achieving system functionality. Be mindful of manufacturers’ minimum feature size capabilities.
Design With Standard Materials and Geometries
Optimize design rules, copper weights, and coverlay materials for the flex PCB supplier’s standard offerings. Custom materials, thick copper, and tolerances that push manufacturing capabilities will add cost. Design within their “sweet spot”.
Build in Margin on Bend Radii
Use larger bend radii than the bare minimum needed for flexibility. This adds reliability margin without significantly increasing cost. Avoid tight bend radii that will incur special handling.
Utilize Flex-Rigid Technology
Consider using rigid sections on the flex PCB in areas that don’t require dynamic flexing. Rigid sections allow higher density circuitry at lower cost compared to flexible regions.
Partner With the Right Manufacturer
Find a flex PCB supplier equipped with the latest manufacturing capabilities and skilled at cost optimization. Leverage their DFM guidance early in the design process. Cultivate the relationship for collaborative continuous improvement.
Plan Ahead for Lower Cost Prototypes
Get prototype pricing feedback from manufacturers during the design phase. Budget for multiple prototype iterations to perfect the design before larger production runs.
Evaluate Design Reuse Opportunities
Assess the potential for reusing flex PCB designs or portions of designs across product lines and generations. Reuse saves on NRE costs.
Consolidate Orders for Volume Discounts
Consolidate projects requiring flex PCBs into fewer larger orders to maximize volume discounts. However, be mindful of inventory carrying costs if units are not required immediately.
Challenge Vendors on Cost Improvement
Treat manufacturing partners as extensions of your team. Challenge them to identify ways to take cost out of flex PCB fabrication and pass along savings.
Flex PCB Cost FQA
Here are answers to some frequently asked questions about the factors that influence the cost of flexible printed circuit boards:
What is the main cost driver for flex PCBs?
The flexible substrate material is typically the largest cost contributor, with polyimide films like Kapton being far more expensive than rigid PCB materials like FR4.
How can I estimate flex PCB costs for budgeting purposes early in the design phase?
Reach out to prospective flex PCB suppliers as early as possible in the design process to get feedback on how to optimize for cost. Many provide design for manufacturing (DFM) guidance and prototyping cost estimates that can inform budget decisions.
What design factors can help reduce the overall flex PCB expense?
Some ways to reduce cost include simplifying layer count, minimizing feature sizes, standardizing materials and geometries, building in adequate but not excessive bend radii margin, utilizing rigid-flex, and designing for manufacturability.
Should I expect a significant price difference between low volume prototypes vs. higher volume production?
Yes, due to factors like manual handling, machine setup costs, and lower efficiency, prototypes and short runs often cost 50-100% more per board than higher volume production for the same design.
How can I obtain the best possible pricing from my flex PCB supplier?
Develop a strong partnership with your chosen manufacturer. Make them part of the design team and solicit their DFM advice early on. Consolidate orders to maximize volume discounts. Challenge them to find ways to reduce cost over the long term.