Introduction
Printed circuit boards (PCBs) are essential components in nearly all modern electronics, from computers and smartphones to medical devices and industrial equipment. Rigid-flex PCBs, which combine rigid and flexible PCB materials in one design, offer unique advantages for many applications with their ability to flex and bend. For companies developing new electronics, having fast turnaround rigid flex PCB prototypes is critical for meeting tight product development schedules and accelerating time-to-market.
This article looks at what makes rigid-flex PCBs well suited for fast prototyping and rapid iterations, key considerations when selecting a rigid flex PCB manufacturer, and how advancements in design software, manufacturing processes, and assembly technologies enable fast turn rigid flex PCB production. With the right approach, rigid flex PCB prototypes can be obtained in as little as 5-7 days, significantly compressing product development timelines.
What Makes Rigid Flex PCBs Suitable for Fast Turn Prototypes
Several inherent properties of rigid-flex PCBs make them well suited for fast turnaround prototyping:
Flexibility and 3D configuration
The bendable sections of rigid-flex PCBs allow the rigid sections to be oriented at different angles, allowing the PCB to fold into unique 3D configurations. This eliminates the need to interconnect separate rigid PCBs to create 3D electronics. For prototypes, a single rigid-flex design simplifies interconnections and accelerates assembly.
Layer stackup variety
Rigid flex PCBs utilize different materials than traditional rigid boards. This allows for more variety in layer stackups. With the ability to combine thin, flexible layers with thicker, more rigid layers, designers can optimize electrical performance, thermal dissipation, and mechanical properties across a single design.
Miniaturization
By consolidating interconnections into a single flexing assembly, rigid-flex PCBs enable product miniaturization not achievable with rigid PCBs alone. This makes rigid-flex PCBs ideal for small, portable electronics where space is extremely limited.
Lower cost
With faster assembly and fewer separate rigid PCBs to interconnect, rigid-flex PCB prototypes can have lower costs than alternatives. This reduces budget requirements during the prototyping stage.
Key Considerations for Fast Turn Rigid Flex PCBs
To leverage the benefits of rigid-flex PCBs for fast prototype needs, product development teams should keep the following considerations in mind:
Selecting a qualified manufacturer
Not all rigid-flex PCB manufacturers have the specialized expertise and capabilities required for short lead time production. Selecting a qualified manufacturer who meets key criteria is essential:
- Extensive rigid-flex technology experience
- In-house engineering support
- Domestic and offshore manufacturing facilities
- Production scale to meet demand
- Responsiveness to prototype requests
Design for manufacturability
To avoid delays, rigid-flex PCB prototypes should be designed with manufacturing processes in mind. A strong working relationship with engineers at the manufacturer is invaluable for optimizing designs. Critical areas to review include:
- Layer stackup construction
- Maintaining minimum bend radii in flex areas
- Accommodating tolerances in panel designs
- Breakout tab designs
Validating performance
The first prototype iteration reveals important information about the design. RF, thermal, mechanical, and functional testing early in the process allows performance issues to be identified and corrected in subsequent versions.
Planning future iterations
Fast turn prototypes enable multiple iterations in quick succession. Working with the manufacturer early on to map out a prototype development schedule and budget can streamline the process.
Enabling Technologies and Techniques for Fast Turn Rigid Flex PCBs
Several advancements in PCB solutions have enhanced the abilities of manufacturers to deliver rigid-flex PCB prototypes with very short lead times:
PCB design software
Powerful PCB design programs like Altium and Cadence have robust rigid-flex design capabilities built-in. This allows engineers to design complex rigid-flex PCBs much faster.
Direct imaging (DI)
DI PCB processes utilize laser imaging to selectively remove dry film photoresist and expose copper. Compared to traditional photographic methods, DI enables faster imaging with no chemical processing. This saves days in prototype manufacturing.
Automated optical inspection (AOI)
AOI systems use advanced camera systems to automatically scan bare PCBs and populated boards. This captures defects early, increases testing thoroughness, and eliminates reliance on human inspectors.
Parallel assembly
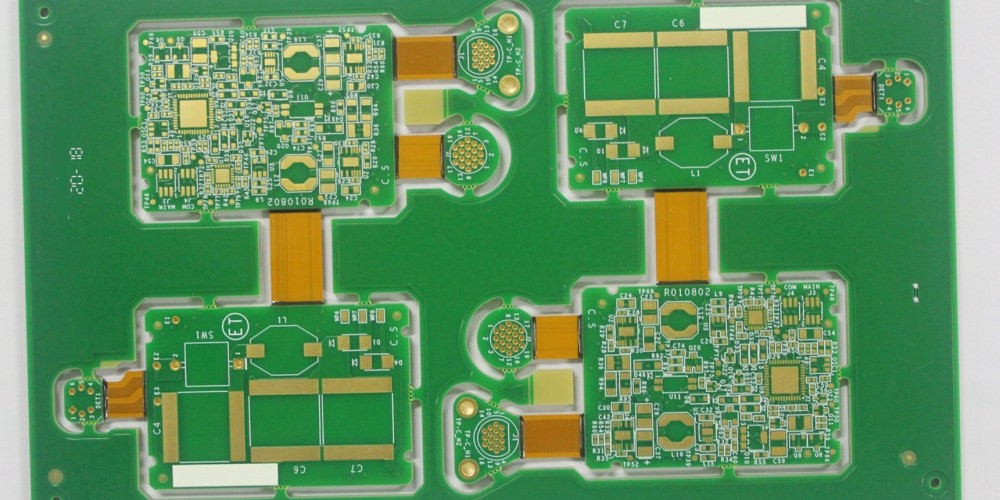
Fast prototype assembly requires the latest techniques like bottom terminated components and multi-up panel designs. Parallel assembly with automated pick-and-place simultaneously populates multiple boards to multiply throughput.
FQA
What are some typical applications suitable for fast turn rigid flex PCBs?
Fast turn rigid flex PCBs are ideal for products where flexibility is a key requirement like wearables, medical devices, robotics, foldable displays, defense systems, etc. The rapid prototyping abilities can help accelerate time-to-market in any industry.
What lead times can be expected for rigid flex PCB prototypes?
With a streamlined prototyping process, rigid flex PCB prototypes can be delivered by a qualified manufacturer in 5-7 days from design approval. More complex designs with challenging requirements or large quantities may require 10-15 days.
What are some key factors impacting the cost of rigid flex PCB prototypes?
The number of layers, flex layer requirements, board size, quantity needed, and assembly complexity primarily drive the cost. Working closely with your PCB partner during the design stage to optimize these parameters can help manage prototype costs.
Can functional testing be performed on the initial prototype iterations?
Yes, initial prototypes can and should be functionally tested during evaluation. This provides feedback to improve performance in follow-on iterations. Both simple benchtop tests and environmental stress screening can be completed by the manufacturer.
How many prototype iterations are typical before moving to production?
Most organizations require 2-4 rigid-flex PCB prototype iterations to verify all aspects of the design. More complex products with tighter tolerances or advanced functionality may undergo 5-6 prototyping rounds or more before release.
Conclusion
Rigid-flex PCBs provide an ideal solution for enabling fast turnaround times for new product prototypes. Their flexible construction simplifies designing 3D configurations, provides advanced layer stackups, and allows for product miniaturization. When combined with the latest in PCB design software, direct imaging manufacturing, automated inspection, and parallel assembly, rigid-flex PCB prototypes can be obtained in just 5-7 days. By selecting a qualified rigid-flex PCB production partner and taking key design and planning considerations into account, product teams can leverage fast turn rigid-flex prototypes to accelerate new product development schedules and reduce time-to-market.