The demand for smaller, lighter, and more powerful electronic devices is driving increased adoption of flexible printed circuit boards (flex PCBs). Flex PCBs provide valuable advantages over rigid PCBs for many applications due to their ability to bend and flex. As products continue getting more complex and miniaturized, having the capability to rapidly iterate on flex PCB designs is becoming critical for reducing time-to-market. This article explores the benefits of fast turn flex PCB prototypes and low volume production.
What are Fast Turn Flex PCBs?
Fast turn flex PCBs refer to the ability to quickly fabricate prototype and low volume production flexible PCBs from design files in just a few days. This is made possible through advancements in flex PCB manufacturing processes as well as optimized order fulfillment workflows between designers and manufacturers.
Traditional rigid PCB prototype lead times are often 2-4 weeks. In contrast, fast turn flex PCBs can ship in just 3-5 days from receiving manufacturing files. This enables designers to validate and iterate on their flex PCB designs much faster. For products on tight development timelines, the ability to shave weeks off the design process can be invaluable.
Benefits of Fast Turn Flex PCB Capabilities
The key benefits offered by fast turn flex PCBs include:
Faster Design Iteration
Fast turnaround on flex PCB prototypes enables multiple design iterations in parallel. Errors and improvements can be incorporated much quicker without long waits for manufacturing.
Accelerated Product Development
Getting functioning flex PCB samples in hand rapidly accelerates overall product development. Rather than wait weeks for each design revision, engineers can progress to software integration, testing, certification, etc much sooner.
Reduced Time-to-Market
For products with short lifecycles, minimizing the duration from design to launch is critical. Fast turn flex PCBs support more design iterations in compressed timeframes, allowing companies to deliver innovative products faster.
Earlier Verification of Manufacturing Quality
The ability to evaluate manufacturing quality and verify acceptable yields with a few quick turns lowers program risks. Potential issues can be identified early rather than downstream during high volume production.
Broader Design Exploration
When turnaround times are long, designers may be more reluctant to explore different design approaches. Fast turnaround on flex PCBs enables trying out more options to arrive at an optimal design.
Agility to Respond to Shifting Requirements
Requirements often change during product development forcing alterations to the PCB design. Rapid flex PCB turns permit adapting to evolving product specs in an agile fashion.
Applications Benefitting from Fast Turn Flex PCBs
Fast turn flex PCB capabilities provide significant advantages across a wide range of applications:
Consumer Electronics
Products like smartphones, wearables, tablets, IoT devices, etc operate on rapid lifecycles so the ability to fabricate flex PCB prototypes and initial production volumes quickly is extremely beneficial.
Automotive Electronics
Auto manufacturers need to continually integrate the latest electronics into new vehicle models under development. Fast flex PCB turns allow automakers to prototype the newest designs faster.
Medical Devices
Medical device makers need to bring innovative products to market quickly while adhering to stringent quality and regulatory requirements. Fast flex PCB turns help accelerate development timelines.
Defense Electronics
Defense programs require electronics that meet rugged specifications often in compact form factors. Quick-turn flex PCBs allow faster iteration of high reliability and ruggedized flex circuit designs.
Robotics
Robots integrate multiple flex PCBs enabling movement capabilities. Faster flex PCB turns lead to quicker design validation and deployment of advanced robots.
Enabling Technologies for Fast Turn Flex PCBs
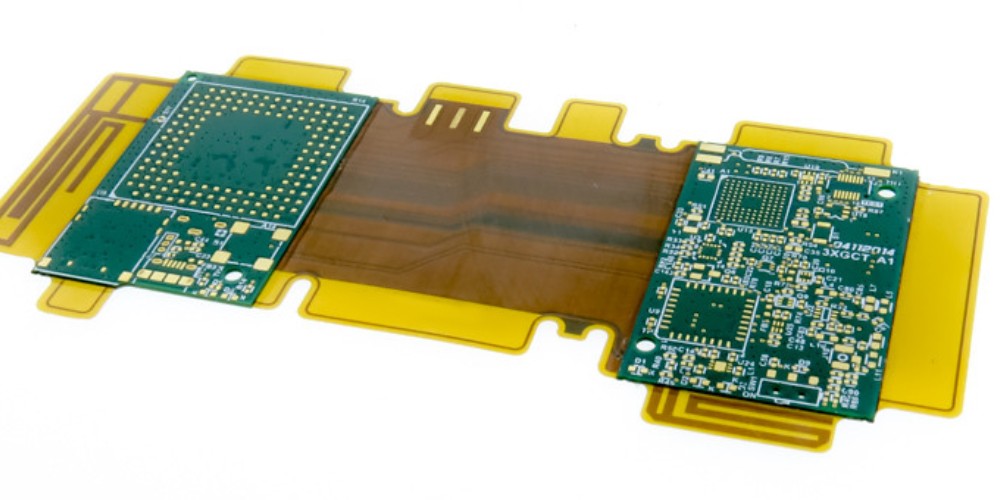
Several advances in flex PCB manufacturing and workflow processes make fast turnaround possible:
H2: LIMS Software
LIMS (laboratory information management system) software integration optimizes order processing and manufacturing workflow orchestration between designer and manufacturer enabling faster delivery.
H2: Advanced DFM Checks
Sophisticated DFM (design for manufacturing) review tools verify manufacturing viability and identify any issues needing resolution for fast prototype fabrication.
H2: Panel Design Capabilities
Manufacturing multiple PCB designs on a panel lowers production costs and allows assembling fast turn boards in parallel for quicker shipment.
H2: Direct Imaging (DI)
DI photo-patterning produces fine line resolution and consistency critical for multilayer flex PCBs while avoiding delays of traditional lithographic exposure.
H2: Laser Direct Structuring (LDS)
LDS laser activation of special copper surfaces enables ultra-fine circuit traces vital in dense flex PCB designs to be fabricated reliably in fast-turnaround.
H2: Advanced Registration Capabilities
Precise alignment of flex material layers during lamination is key for high yield when rapidly processing complex, multilayer flex boards.
H2: Testing Automation
Automated testing routines for parameters like impedance, continuity, shorts, etc enable comprehensive quality verification of fast turn flex PCBs.
Fast Turn Flex PCB Technology Comparison
There are a few distinct technology options each with their own advantages when making fast turn flex PCBs:
Technology | Description | Benefits | Limitations |
---|---|---|---|
Single Sided Flex | One conductive copper layer | Lower cost, simpler | Limited connectivity |
Double Sided Flex | Two conductive copper layers | Increased connectivity | More complex, higher cost |
Multilayer Flex | 3+ conductive copper layers | High density interconnects | Challenging fabrication, high cost |
Rigid-Flex | Combines rigid and flex boards | Maximizes strengths of each | Complex design constraints |
Single sided flex PCBs provide the fastest and most cost effective option for basic designs. For more complex circuits requiring greater connectivity, double sided and multilayer flex implements the needed routing while still enabling fast turnaround relative to the complexity. Rigid-flex is ideal when a design requires the durability and rigidity of a standard PCB along with the flexibility of an FPC.
H2: Flex PCB Fast Turn Capabilities Questions
Below are answers to commonly asked questions related to fast turn flex PCB capabilities:
What are typical fast turn flex PCB lead times?
For 2-6 layer designs without complex requirements, fast turn lead times can be as fast as 24-72 hours. More complex designs can ship in 3-5 days. For comparison, standard lead times range from 2-4 weeks.
How many flex PCB design revisions can be supported on fast turn?
To accelerate product development, often 5-10 fast turn iterations will progress a design from initial prototype to finalized for production. More complex products may require 15 or more revisions.
What are limitations on fast turn flex PCB complexity?
There are few hard limitations, but designs over 8 layers or with very dense interconnect or construction requirements may not be feasible on the fastest lead times. Active engagement with the manufacturer is recommended for more complex flex boards.
Can fast turn support low volume production?
Once a prototype is finalized, fast turn services support building small production batches to verify manufacturing processes and quality before full ramp up. Quantities from 10-100 units can be produced on accelerated lead times.
How is reliability assured with fast flex PCB turns?
While delivered quickly, quality standards remain high. All boards receive the same fabrication processing controls and automated testing as any order. Complex designs just require additional verification reviews by engineers before manufacturing.
Conclusion
The need for fast product development cycles across diverse markets is driving greater adoption of quick-turn flex PCB capabilities. As new products integrate more flex circuits, having access to advanced flex PCB manufacturers capable of delivering prototypes and initial production volumes in just days provides invaluable development acceleration and competitive advantage.
With innovative manufacturing technologies and optimized workflow processes, top flex PCB vendors are meeting the growing demand for fast turn services that compress time-to-market for products with tight development schedules. Engineers leveraging fast turn flex PCB capabilities see a marked improvement in design cycle times and development velocity over those waiting weeks for rigid boards.
As the complexity of emerging electronic products continues to increase, these fast turn flex circuit capabilities will only become more vital for rapidly progressing from design concepts to functioning prototypes to production-ready products. Companies that partner with the right flex PCB manufacturer position themselves at the forefront of technology innovation by harnessing the full power of fast turn flex circuit development