Electromagnetic Interference (EMI) is a pervasive challenge in modern electronics, particularly in high-speed and high-frequency PCB designs. EMI can cause signal integrity issues, degrade performance, and lead to non-compliance with regulatory standards. Addressing EMI issues early in the PCB design stage is critical to ensuring the reliability and functionality of electronic devices. EMIStream, a specialized tool for EMI analysis and mitigation, empowers designers to identify and resolve EMI problems during the design phase, reducing the risk of costly redesigns and delays. This article provides a comprehensive guide to EMIStream, exploring its features, benefits, and best practices for addressing EMI issues early in the PCB design process.
1. What is EMIStream?
1.1 Definition
EMIStream is an advanced EMI analysis tool integrated into PCB design software, such as Zuken’s CR-8000 and Cadence Allegro. It enables designers to simulate and analyze electromagnetic emissions from PCB layouts, identifying potential EMI issues before prototyping or manufacturing.
1.2 Key Features
- EMI Simulation: Simulates electromagnetic emissions from PCB traces, vias, and components.
- Frequency Domain Analysis: Analyzes EMI across a wide frequency range, from DC to GHz.
- Current Distribution Analysis: Visualizes current flow and identifies high-current areas that may contribute to EMI.
- Decoupling Capacitor Optimization: Recommends optimal placement and values of decoupling capacitors to reduce EMI.
- Regulatory Compliance: Ensures compliance with EMI standards such as FCC, CISPR, and MIL-STD.
1.3 Benefits of EMIStream
- Early Detection: Identifies EMI issues during the design stage, reducing the need for costly redesigns.
- Improved Signal Integrity: Enhances signal integrity by minimizing electromagnetic emissions.
- Regulatory Compliance: Ensures that the PCB meets EMI regulatory standards.
- Time and Cost Savings: Reduces development time and costs by addressing EMI issues early.
2. Why Address EMI Issues Early in the Design Stage?
2.1 Cost of Late-Stage EMI Fixes
Addressing EMI issues after prototyping or manufacturing can be extremely costly. Late-stage fixes often require:
- Redesigns: Modifying the PCB layout, which can delay the project timeline.
- Additional Components: Adding shielding, filters, or ferrites to mitigate EMI.
- Testing and Certification: Repeating EMI testing and certification processes.
2.2 Impact on Signal Integrity
EMI can cause signal integrity issues, such as crosstalk, reflections, and noise, which degrade the performance of high-speed and high-frequency circuits. Early detection and mitigation of EMI ensure reliable signal transmission.
2.3 Regulatory Compliance
Electronic devices must comply with EMI regulations, such as FCC Part 15 and CISPR 22, to be marketed and sold. Addressing EMI issues early ensures compliance and avoids costly penalties or recalls.
2.4 Competitive Advantage
Designing EMI-compliant PCBs early in the process provides a competitive advantage by reducing time-to-market and improving product reliability.
3. How EMIStream Works
3.1 Integration with PCB Design Tools
EMIStream integrates seamlessly with popular PCB design tools, allowing designers to perform EMI analysis directly within their design environment. This integration enables real-time feedback and iterative design improvements.
3.2 EMI Simulation Process
The EMI simulation process in EMIStream involves the following steps:
- Model Setup: Define the PCB stack-up, material properties, and component placements.
- Current Distribution Analysis: Simulate current flow across the PCB to identify high-current areas.
- Frequency Domain Analysis: Analyze electromagnetic emissions across a specified frequency range.
- EMI Hotspot Identification: Identify areas of the PCB that contribute to high EMI.
- Mitigation Recommendations: Provide recommendations for reducing EMI, such as optimizing trace routing, adding decoupling capacitors, or modifying the ground plane.
3.3 Key Analysis Capabilities
- Radiated Emissions: Simulate and analyze radiated electromagnetic emissions from the PCB.
- Conducted Emissions: Analyze conducted emissions through power and signal lines.
- Near-Field Analysis: Evaluate near-field electromagnetic emissions, which are critical for identifying localized EMI sources.
- Far-Field Analysis: Simulate far-field emissions to assess compliance with regulatory standards.
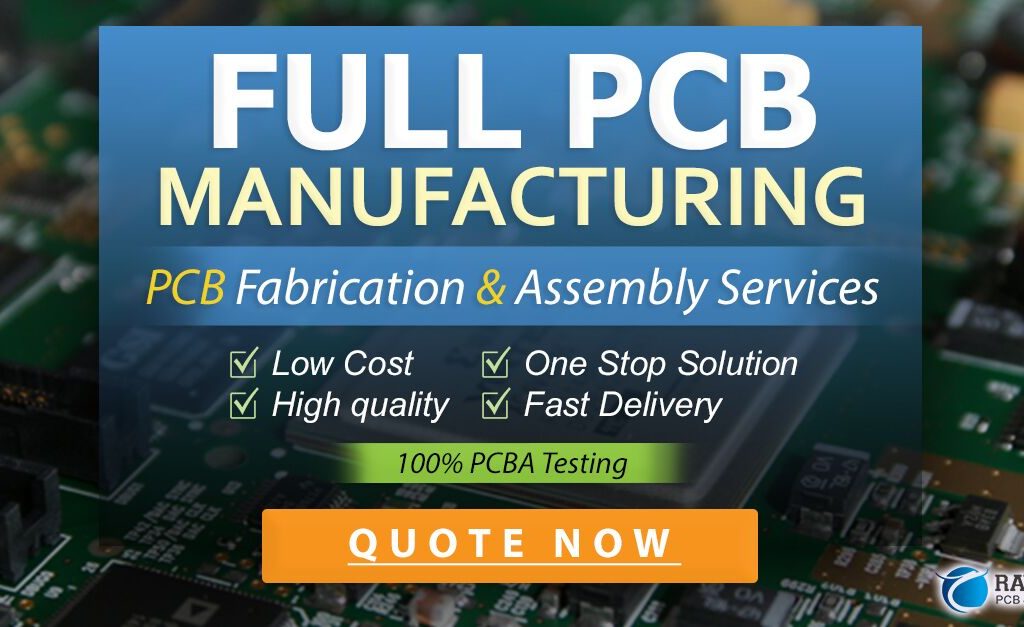
4. Best Practices for Using EMIStream
4.1 Start Early in the Design Process
Incorporate EMIStream into the early stages of the PCB design process to identify and address EMI issues before they become critical. Early analysis allows for iterative design improvements and reduces the risk of late-stage fixes.
4.2 Optimize PCB Layout
- Trace Routing: Minimize the length of high-speed traces and avoid sharp bends to reduce EMI.
- Ground Planes: Use solid ground planes to provide a low-impedance return path for currents and reduce EMI.
- Component Placement: Place high-speed components and connectors away from sensitive areas to minimize EMI coupling.
4.3 Use Decoupling Capacitors Effectively
- Placement: Place decoupling capacitors close to power pins of ICs to reduce high-frequency noise.
- Value Selection: Choose capacitor values that effectively filter noise at the target frequencies.
4.4 Perform Frequency Domain Analysis
Conduct frequency domain analysis to identify EMI hotspots and optimize the design for specific frequency ranges. This is particularly important for high-speed and high-frequency circuits.
4.5 Validate with Real-World Testing
While EMIStream provides valuable insights, validate the design with real-world EMI testing to ensure compliance with regulatory standards and performance requirements.
5. Case Study: Using EMIStream in a High-Speed PCB Design
To illustrate the effectiveness of EMIStream, let’s examine a case study involving a high-speed PCB for a networking application.
5.1 Design Requirements
- Data Rate: 10 Gbps.
- Signal Integrity: Minimal EMI and crosstalk.
- Regulatory Compliance: Compliance with FCC Part 15 and CISPR 22.
5.2 EMI Analysis with EMIStream
The design team used EMIStream to analyze the PCB layout and identify potential EMI issues. Key steps included:
- Current Distribution Analysis: Identified high-current areas near high-speed connectors.
- Frequency Domain Analysis: Detected high EMI emissions at specific frequencies.
- EMI Hotspot Identification: Pinpointed areas of the PCB contributing to high EMI.
5.3 Mitigation Strategies
Based on EMIStream’s recommendations, the team implemented the following mitigation strategies:
- Optimized Trace Routing: Reduced the length of high-speed traces and avoided sharp bends.
- Enhanced Ground Planes: Added solid ground planes and ground vias to reduce EMI.
- Decoupling Capacitors: Placed decoupling capacitors close to power pins of high-speed ICs.
5.4 Results
The final design met all performance and regulatory requirements, with minimal EMI emissions. The use of EMIStream enabled the team to address EMI issues early, reducing the need for costly redesigns and ensuring timely project completion.
6. Conclusion
EMIStream is a powerful tool for addressing EMI issues early in the PCB design stage, enabling designers to create high-performance, EMI-compliant circuits. By integrating EMIStream into the design process, designers can identify and mitigate EMI issues before they become critical, reducing development time and costs. Whether you’re designing high-speed digital circuits, RF modules, or consumer electronics, EMIStream provides the insights and tools needed to ensure signal integrity and regulatory compliance.
This guide provides a comprehensive overview of EMIStream and its role in addressing EMI issues early in the PCB design stage. By applying the principles and best practices outlined here, you can leverage EMIStream to design reliable, high-performance PCBs that meet the demands of modern electronics.