In the world of modern electronics, Surface Mount Device (SMD) components have become the standard due to their compact size, high performance, and compatibility with automated assembly processes. Double-sided PCB designs, which utilize both sides of the board to accommodate more components, are increasingly common in high-density applications. However, double-sided PCB assembly, particularly reflow soldering, presents unique challenges that require careful planning and execution.
Reflow soldering is the most widely used method for attaching SMD components to PCBs. It involves applying solder paste to the board, placing components, and then heating the assembly in a reflow oven to melt the solder and form reliable electrical and mechanical connections. When working with double-sided PCBs, the process becomes more complex because components on both sides of the board must be soldered without compromising the integrity of the first side during the second reflow cycle.
This article explores the best design practices for double-sided PCB reflow soldering with SMD parts, covering everything from component placement and thermal management to solder paste selection and process optimization. By following these guidelines, you can ensure high-quality, reliable solder joints and minimize defects in your double-sided PCB assemblies.
Understanding Double-Sided PCB Reflow Soldering
Double-sided PCB reflow soldering involves two separate reflow cycles—one for each side of the board. The process typically follows these steps:
- First Side Reflow:
- Apply solder paste to the first side of the PCB.
- Place SMD components on the first side.
- Pass the board through the reflow oven to melt the solder and form connections.
- Second Side Reflow:
- Flip the board and apply solder paste to the second side.
- Place SMD components on the second side.
- Pass the board through the reflow oven again to solder the second side.
The primary challenge in double-sided reflow soldering is ensuring that components on the first side do not fall off or become damaged during the second reflow cycle. This requires careful consideration of component placement, thermal profiles, and solder paste properties.
Best Design Practices for Double-Sided PCB Reflow Soldering
To achieve successful double-sided PCB reflow soldering, follow these best practices:
1. Component Placement and Orientation
Proper component placement is critical for double-sided PCB assembly. Here are some guidelines:
- Heavier Components on the Bottom Side: Place larger and heavier components (e.g., connectors, transformers) on the bottom side of the board. This reduces the risk of these components detaching during the second reflow cycle due to gravity.
- Smaller Components on the Top Side: Place smaller and lighter components (e.g., resistors, capacitors, ICs) on the top side. These components are less likely to fall off during the second reflow cycle.
- Avoid Overlapping Components: Ensure that components on the top and bottom sides do not overlap. Overlapping components can interfere with solder paste application and reflow, leading to defects.
- Orientation for Thermal Balance: Orient components to distribute heat evenly across the board. This minimizes thermal stress and prevents warping or damage during reflow.
2. Thermal Management
Thermal management is crucial for double-sided reflow soldering. The following practices can help:
- Thermal Relief Pads: Use thermal relief pads for components with large ground or power planes. These pads reduce heat dissipation and ensure proper solder reflow.
- Balanced Thermal Mass: Design the board with a balanced thermal mass on both sides. Uneven thermal mass can lead to uneven heating and solder defects.
- Thermal Vias: Use thermal vias to dissipate heat from components on the bottom side during the second reflow cycle. This prevents overheating and damage to the first side’s components.
3. Solder Paste Selection and Application
Solder paste plays a critical role in reflow soldering. Consider the following:
- Solder Paste Type: Choose a solder paste with the appropriate alloy composition (e.g., SAC305 for lead-free soldering) and particle size (Type 3 or Type 4 for fine-pitch components).
- Stencil Design: Use a high-quality stencil with the correct aperture size and shape for solder paste application. Ensure proper alignment to avoid bridging or insufficient solder.
- Solder Paste Volume: Apply the correct amount of solder paste to each pad. Too much paste can cause bridging, while too little can result in weak joints.
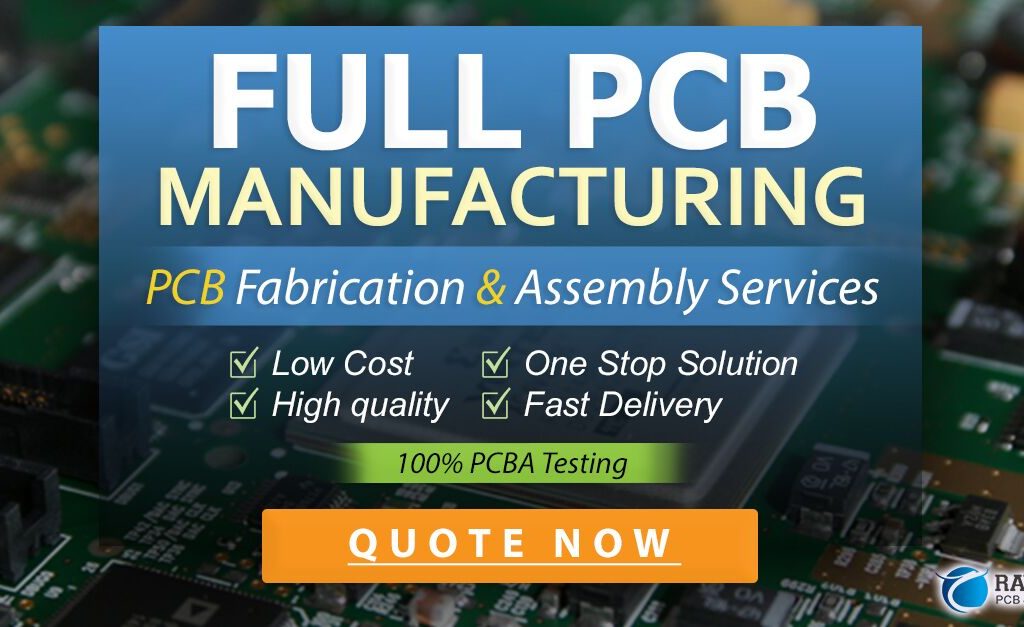
4. Reflow Profile Optimization
The reflow profile is the temperature curve that the PCB follows during the reflow process. Optimizing the profile is essential for double-sided soldering:
- Preheat Phase: Gradually heat the board to activate the flux and remove moisture. Avoid rapid heating, which can cause thermal shock.
- Soak Phase: Maintain a stable temperature to ensure even heat distribution across the board.
- Reflow Phase: Heat the board to the peak temperature to melt the solder. Ensure that the peak temperature is high enough to form reliable joints but not so high that it damages components.
- Cooling Phase: Cool the board gradually to prevent thermal stress and warping.
For double-sided PCBs, the second reflow cycle should use a lower peak temperature to minimize the risk of re-melting the first side’s solder joints.
5. Component Securing Techniques
To prevent components on the first side from falling off during the second reflow cycle, consider these techniques:
- Adhesive Bonding: Use a high-temperature adhesive to secure larger components on the first side before the second reflow cycle.
- Mechanical Fixtures: Use fixtures or clamps to hold components in place during the second reflow cycle.
- Selective Soldering: For critical components, use selective soldering instead of reflow to avoid re-melting the first side’s joints.
6. Design for Manufacturability (DFM)
Designing for manufacturability ensures that your PCB can be assembled efficiently and reliably:
- Panelization: Design the PCB in panels to facilitate handling during assembly. Include breakaway tabs or mouse bites for easy separation after soldering.
- Fiducial Marks: Add fiducial marks to the PCB to assist with component placement accuracy.
- Test Points: Include test points for in-circuit testing (ICT) and functional testing after assembly.
7. Inspection and Quality Control
Inspection and quality control are essential for identifying and addressing defects:
- Automated Optical Inspection (AOI): Use AOI to check for solder paste application, component placement, and solder joint quality.
- X-Ray Inspection: For hidden joints (e.g., under BGA components), use X-ray inspection to verify solder integrity.
- Functional Testing: Perform functional testing to ensure the assembled PCB meets performance specifications.
Common Challenges and Solutions
Double-sided PCB reflow soldering can present several challenges. Here are some common issues and their solutions:
1. Component Falling Off During Second Reflow
- Cause: Gravity and re-melting of solder joints on the first side.
- Solution: Use adhesive bonding, mechanical fixtures, or selective soldering for larger components.
2. Tombstoning
- Cause: Uneven heating or solder paste application causing one end of a component to lift.
- Solution: Ensure balanced thermal mass and even solder paste application.
3. Solder Bridging
- Cause: Excessive solder paste or misaligned stencil.
- Solution: Optimize stencil design and solder paste volume.
4. Insufficient Solder Joints
- Cause: Insufficient solder paste or poor reflow profile.
- Solution: Adjust solder paste volume and optimize the reflow profile.
Conclusion
Double-sided PCB reflow soldering with SMD parts is a complex but essential process for modern electronics manufacturing. By following the best design practices outlined in this article, you can overcome the challenges associated with double-sided assembly and achieve high-quality, reliable solder joints.
Key considerations include proper component placement, thermal management, solder paste selection, reflow profile optimization, and design for manufacturability. Additionally, securing components during the second reflow cycle and implementing robust inspection and quality control processes are critical for success.
As electronics continue to evolve, mastering double-sided PCB reflow soldering will remain a valuable skill for engineers and manufacturers. By adhering to these best practices, you can ensure the success of your double-sided PCB assemblies and deliver high-performance electronic products to market.