Introduction
In the realm of printed circuit board (PCB) design and manufacturing, aspect ratios play a pivotal role in determining the performance, reliability, and manufacturability of multi-layered PCBs. As electronic devices continue to evolve, becoming more compact and complex, the demand for high-density interconnects (HDI) and multi-layered PCBs has surged. Understanding aspect ratios and their implications is crucial for engineers and designers aiming to optimize their PCB designs for both functionality and manufacturability.
This article delves into the concept of aspect ratios, their significance in multi-layered PCBs, and the challenges and considerations associated with them. By the end of this comprehensive exploration, readers will have a thorough understanding of how aspect ratios influence PCB design and manufacturing processes.
Understanding Aspect Ratios
Definition of Aspect Ratio
The aspect ratio in the context of PCBs refers to the ratio of the thickness of the PCB to the diameter of a drilled hole. Mathematically, it is expressed as:
[ \text{Aspect Ratio} = \frac{\text{Thickness of the PCB}}{\text{Diameter of the Drilled Hole}} ]
For instance, if a PCB has a thickness of 1.6 mm and a drilled hole diameter of 0.2 mm, the aspect ratio would be 8:1.
Importance of Aspect Ratio in PCB Design
The aspect ratio is a critical parameter in PCB design because it directly impacts the manufacturability and reliability of the board. A higher aspect ratio indicates a thicker board relative to the hole diameter, which can pose challenges during the drilling and plating processes. Conversely, a lower aspect ratio suggests a thinner board relative to the hole diameter, which is generally easier to manufacture but may not meet the design requirements for certain applications.
Multi-Layered PCBs: An Overview
What are Multi-Layered PCBs?
Multi-layered PCBs are circuit boards that consist of three or more conductive layers laminated together with insulating material between them. These layers are interconnected through vias, which are plated through-holes that facilitate electrical connections between different layers.
Advantages of Multi-Layered PCBs
- Increased Circuit Density: Multi-layered PCBs allow for a higher density of circuits, enabling more complex and compact designs.
- Improved Signal Integrity: By providing dedicated ground and power planes, multi-layered PCBs can reduce electromagnetic interference (EMI) and improve signal integrity.
- Enhanced Thermal Management: The additional layers can help dissipate heat more effectively, improving the thermal performance of the PCB.
- Reduced Size and Weight: Multi-layered PCBs enable the integration of more components in a smaller footprint, reducing the overall size and weight of the electronic device.
The Role of Aspect Ratios in Multi-Layered PCBs
Drilling and Plating Challenges
One of the primary challenges associated with high aspect ratios in multi-layered PCBs is the drilling and plating of vias. As the aspect ratio increases, the difficulty of drilling precise and consistent holes also increases. High aspect ratio holes are more prone to drilling defects such as smearing, nail heading, and hole wall roughness.
Plating these high aspect ratio holes is equally challenging. Ensuring uniform copper deposition throughout the depth of the hole is critical for reliable electrical connections. Inadequate plating can lead to voids, cracks, and other defects that compromise the integrity of the via.
Signal Integrity and Electrical Performance
Aspect ratios also influence the electrical performance of multi-layered PCBs. High aspect ratio vias can introduce parasitic inductance and capacitance, which can affect signal integrity, especially in high-frequency applications. Designers must carefully consider the aspect ratio to minimize these parasitic effects and ensure optimal electrical performance.
Thermal Management
Thermal management is another critical consideration in multi-layered PCBs. High aspect ratio vias can act as thermal vias, helping to dissipate heat from the inner layers to the outer layers or heat sinks. However, the effectiveness of thermal vias depends on their aspect ratio and the quality of the plating. Poorly plated vias can impede heat transfer, leading to thermal hotspots and potential failure of the PCB.
Manufacturability and Cost
The aspect ratio directly impacts the manufacturability and cost of multi-layered PCBs. High aspect ratio PCBs require more advanced drilling and plating techniques, which can increase manufacturing complexity and cost. Additionally, the yield of high aspect ratio PCBs may be lower due to the increased likelihood of defects, further driving up costs.
Designers must strike a balance between the desired aspect ratio and the associated manufacturing challenges to ensure a cost-effective and reliable PCB design.
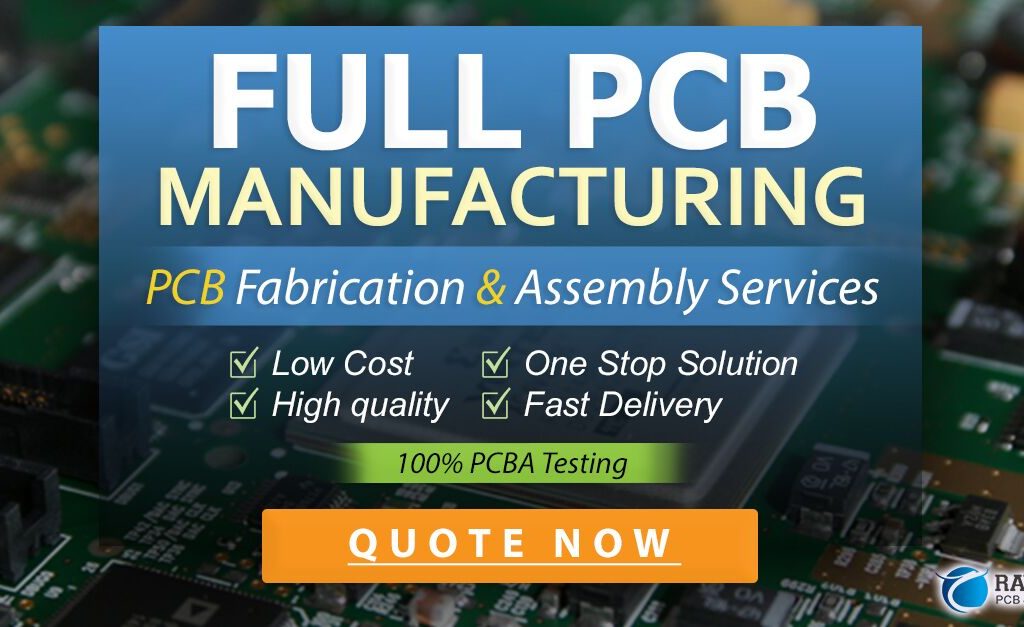
Design Considerations for Aspect Ratios in Multi-Layered PCBs
Material Selection
The choice of materials plays a significant role in determining the achievable aspect ratio. Different materials have varying thermal, mechanical, and electrical properties that can influence the drilling and plating processes. For instance, high-performance materials such as FR-4, polyimide, and Rogers materials offer different trade-offs in terms of thermal stability, dielectric constant, and mechanical strength.
Via Design
The design of vias is critical in managing aspect ratios. Designers must consider the following factors:
- Via Size: Smaller vias allow for higher aspect ratios but are more challenging to drill and plate. Designers must balance the via size with the manufacturability and reliability requirements.
- Via Shape: The shape of the via, whether through-hole, blind, or buried, can impact the aspect ratio and the overall PCB design. Blind and buried vias can help reduce the aspect ratio by limiting the depth of the via.
- Via Placement: The placement of vias relative to other components and traces can influence signal integrity and thermal management. Proper via placement can help mitigate parasitic effects and improve thermal dissipation.
Drilling and Plating Techniques
Advanced drilling and plating techniques are essential for achieving high aspect ratios in multi-layered PCBs. Some of the key techniques include:
- Laser Drilling: Laser drilling offers higher precision and consistency compared to mechanical drilling, making it suitable for high aspect ratio vias.
- Electroless Copper Plating: Electroless copper plating provides a uniform copper deposition, even in high aspect ratio vias, ensuring reliable electrical connections.
- Pulse Plating: Pulse plating can improve the quality of copper deposition in high aspect ratio vias by reducing the likelihood of voids and cracks.
Design for Manufacturability (DFM)
Design for Manufacturability (DFM) is a critical consideration in multi-layered PCB design. DFM principles emphasize designing PCBs that are easy to manufacture, reducing the likelihood of defects and improving yield. Key DFM considerations for aspect ratios include:
- Aspect Ratio Limits: Designers should adhere to the aspect ratio limits recommended by the PCB manufacturer to ensure manufacturability and reliability.
- Panelization: Proper panelization can help optimize the use of materials and reduce manufacturing costs. Designers should consider the aspect ratio when planning the panel layout.
- Testing and Inspection: Incorporating testing and inspection points in the design can help identify and address potential issues early in the manufacturing process.
Case Studies: Aspect Ratios in Real-World Applications
High-Density Interconnect (HDI) PCBs
High-Density Interconnect (HDI) PCBs are a prime example of the importance of aspect ratios in modern PCB design. HDI PCBs feature finer lines and spaces, smaller vias, and higher layer counts, enabling the integration of more components in a compact form factor.
In HDI PCBs, aspect ratios are critical for achieving the desired circuit density and signal integrity. Designers often use microvias, which have smaller diameters and lower aspect ratios compared to traditional through-hole vias. Microvias allow for higher density interconnects and improved electrical performance, making them ideal for applications such as smartphones, tablets, and wearable devices.
Automotive Electronics
Automotive electronics present unique challenges for PCB design, including harsh operating environments, stringent reliability requirements, and the need for compact and lightweight designs. Aspect ratios play a crucial role in addressing these challenges.
In automotive PCBs, high aspect ratio vias are often used to provide robust electrical connections and effective thermal management. However, the harsh operating conditions, such as temperature fluctuations and vibrations, can exacerbate the challenges associated with high aspect ratio vias. Designers must carefully consider the aspect ratio and employ advanced materials and manufacturing techniques to ensure the reliability and durability of automotive PCBs.
Aerospace and Defense
Aerospace and defense applications demand PCBs that can withstand extreme conditions, including high temperatures, radiation, and mechanical stress. Aspect ratios are a critical consideration in these applications, as they impact the PCB’s thermal performance, signal integrity, and reliability.
In aerospace and defense PCBs, high aspect ratio vias are often used to provide effective thermal management and reliable electrical connections. However, the stringent reliability requirements necessitate rigorous testing and inspection to ensure the integrity of the vias. Designers must also consider the impact of aspect ratios on the PCB’s weight and size, as these factors are critical in aerospace applications.
Future Trends and Innovations
Advanced Materials
The development of advanced materials is expected to play a significant role in addressing the challenges associated with high aspect ratios in multi-layered PCBs. Materials with improved thermal stability, mechanical strength, and dielectric properties can enable higher aspect ratios while maintaining reliability and performance.
For instance, the use of low-loss dielectric materials can help mitigate the parasitic effects of high aspect ratio vias, improving signal integrity in high-frequency applications. Similarly, materials with enhanced thermal conductivity can improve heat dissipation, reducing the risk of thermal hotspots in high aspect ratio PCBs.
Additive Manufacturing
Additive manufacturing, also known as 3D printing, is emerging as a promising technology for PCB fabrication. Additive manufacturing techniques can enable the creation of complex geometries and high aspect ratio vias with greater precision and consistency.
By layering conductive and insulating materials, additive manufacturing can produce multi-layered PCBs with intricate designs and high aspect ratio vias. This technology has the potential to revolutionize PCB manufacturing, enabling the production of highly customized and high-performance PCBs for a wide range of applications.
Miniaturization and Integration
The trend towards miniaturization and integration is driving the demand for higher aspect ratios in multi-layered PCBs. As electronic devices become smaller and more complex, the need for high-density interconnects and compact designs is increasing.
Future innovations in PCB design and manufacturing are likely to focus on achieving higher aspect ratios while maintaining reliability and performance. This may involve the development of new drilling and plating techniques, as well as the integration of advanced materials and additive manufacturing technologies.
Conclusion
Aspect ratios are a critical consideration in the design and manufacturing of multi-layered PCBs. They influence the manufacturability, reliability, and performance of the PCB, impacting everything from signal integrity to thermal management. As electronic devices continue to evolve, the demand for higher aspect ratios is expected to grow, driving innovations in materials, manufacturing techniques, and design practices.
By understanding the importance of aspect ratios and the challenges associated with them, engineers and designers can optimize their PCB designs for both functionality and manufacturability. As the industry continues to advance, the ability to achieve higher aspect ratios while maintaining reliability and performance will be key to meeting the demands of modern electronic devices.