Printed Circuit Board (PCB) design and manufacturing involve a multitude of intricate details, each contributing to the overall functionality, reliability, and manufacturability of the final product. Among these details, tooling holes play a crucial role, yet they are often overlooked or misunderstood. Tooling holes are essential for ensuring precision during the manufacturing and assembly processes. This article provides a comprehensive guide to PCB tooling holes, explaining what they are, their purpose, types, placement guidelines, and best practices for incorporating them into your PCB design.
1. What Are PCB Tooling Holes?
1.1 Definition
Tooling holes, also known as fiducial markers or alignment holes, are non-plated or plated holes drilled into a PCB to aid in the manufacturing, assembly, and testing processes. These holes serve as reference points for machinery and equipment, ensuring accurate alignment and positioning of the PCB during various stages of production.
1.2 Purpose of Tooling Holes
Tooling holes are primarily used for:
- Alignment: Ensuring the PCB is correctly positioned during fabrication, assembly, and testing.
- Registration: Providing reference points for layer alignment during multi-layer PCB manufacturing.
- Mounting: Securing the PCB to fixtures or equipment during assembly and testing.
- Automation: Enabling automated machinery to handle and process the PCB accurately.
2. Types of Tooling Holes
Tooling holes can be categorized based on their purpose and placement. Below are the most common types:
2.1 Fiducial Markers
Fiducial markers are small, non-plated holes or pads used as reference points for optical alignment systems. They are typically placed on the outer layers of the PCB and are essential for automated assembly processes, such as pick-and-place machines.
2.2 Mounting Holes
Mounting holes are larger, plated or non-plated holes used to secure the PCB to enclosures, fixtures, or equipment. These holes are often located near the corners of the PCB and may include additional features such as countersinks or counterbores.
2.3 Registration Holes
Registration holes are used during the PCB fabrication process to align the different layers of a multi-layer PCB. These holes ensure that all layers are perfectly aligned before lamination.
2.4 Tooling Holes for Testing
Tooling holes can also be used during electrical testing to secure the PCB to test fixtures. These holes are typically non-plated and located in areas that do not interfere with the circuitry.
3. Placement Guidelines for Tooling Holes
The placement of tooling holes is critical to their effectiveness. Below are some general guidelines for placing tooling holes on a PCB:
3.1 Fiducial Markers
- Number: At least three fiducial markers are recommended for accurate alignment.
- Placement: Fiducial markers should be placed near the corners of the PCB, forming a triangular pattern. This ensures that the PCB can be aligned in both the X and Y axes.
- Size: Fiducial markers are typically 1-3 mm in diameter.
- Clearance: Ensure that there is adequate clearance around fiducial markers to avoid interference with components or traces.
3.2 Mounting Holes
- Number: The number of mounting holes depends on the size and weight of the PCB. Typically, four mounting holes are used, one near each corner.
- Placement: Mounting holes should be placed close to the edges of the PCB but not too close to the board outline to avoid mechanical stress.
- Size: The size of mounting holes depends on the screws or fasteners used. Common sizes range from 2.5 mm to 4.5 mm in diameter.
- Countersinks/Counterbores: If screws are used, consider adding countersinks or counterbores to ensure a flush fit.
3.3 Registration Holes
- Number: At least two registration holes are required for layer alignment.
- Placement: Registration holes should be placed diagonally across the PCB to ensure accurate alignment.
- Size: Registration holes are typically 2-4 mm in diameter.
3.4 Tooling Holes for Testing
- Number: The number of tooling holes for testing depends on the test fixture design.
- Placement: These holes should be placed in areas that do not interfere with components or traces.
- Size: The size of these holes depends on the test fixture pins. Common sizes range from 1.5 mm to 3 mm in diameter.
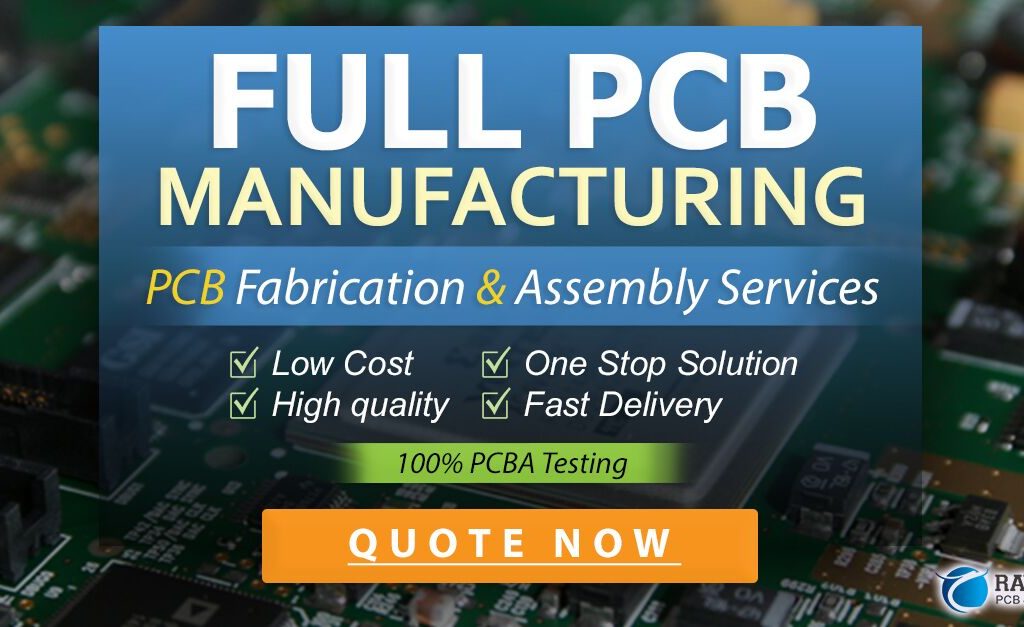
4. Design Considerations for Tooling Holes
4.1 Non-Plated vs. Plated Holes
- Non-Plated Holes: Non-plated tooling holes are typically used for mounting and testing. They are less expensive to manufacture and do not affect the electrical properties of the PCB.
- Plated Holes: Plated tooling holes are used when electrical connectivity is required, such as in registration holes for multi-layer PCBs.
4.2 Clearance and Keep-Out Areas
Ensure that tooling holes have adequate clearance from components, traces, and the board edge. This prevents mechanical stress and interference during assembly and testing.
4.3 Material and Finish
The material and finish of tooling holes should match the rest of the PCB. For example, if the PCB has a gold finish, the tooling holes should also have a gold finish to ensure consistency.
4.4 Tolerance and Precision
Tooling holes must be drilled with high precision to ensure accurate alignment and registration. Typical tolerances for tooling holes are ±0.05 mm to ±0.10 mm.
5. Best Practices for Incorporating Tooling Holes
5.1 Collaborate with Your Manufacturer
Work closely with your PCB manufacturer to understand their specific requirements for tooling holes. This ensures that your design is compatible with their equipment and processes.
5.2 Use Standard Sizes and Locations
Whenever possible, use standard sizes and locations for tooling holes. This simplifies the manufacturing process and reduces the risk of errors.
5.3 Document Tooling Holes Clearly
Include detailed information about tooling holes in your design files and manufacturing deliverables. This documentation should include:
- Location: Specify the exact location of each tooling hole.
- Size: Provide the diameter and tolerance for each hole.
- Type: Indicate whether the hole is plated or non-plated.
- Purpose: Describe the purpose of each tooling hole (e.g., fiducial, mounting, registration).
5.4 Perform Design for Manufacturability (DFM) Checks
Use DFM tools to verify that your tooling holes meet manufacturing requirements. These checks can help identify potential issues early in the design process.
6. Common Mistakes to Avoid
6.1 Insufficient Number of Tooling Holes
Using too few tooling holes can lead to alignment issues during manufacturing and assembly. Always include an adequate number of tooling holes based on the size and complexity of your PCB.
6.2 Incorrect Placement
Placing tooling holes too close to components, traces, or the board edge can cause mechanical stress and interference. Follow placement guidelines to avoid these issues.
6.3 Inadequate Documentation
Failing to document tooling holes clearly can lead to misunderstandings and errors during manufacturing. Ensure that all tooling holes are clearly specified in your design files.
7. Case Study: Tooling Holes in a High-Density PCB
To illustrate the importance of tooling holes, let’s examine a case study involving a high-density PCB used in a medical device.
7.1 Design Requirements
- Board Size: 100 mm x 150 mm
- Layers: 8
- Components: Over 500 surface-mount components
- Assembly: Automated pick-and-place assembly
7.2 Tooling Hole Challenges
- Alignment: The high component density required precise alignment during assembly.
- Registration: The multi-layer design required accurate layer registration.
- Testing: The PCB needed to be securely mounted to a test fixture for electrical testing.
7.3 Tooling Hole Solutions
- Fiducial Markers: Three fiducial markers were placed near the corners of the PCB for optical alignment.
- Registration Holes: Two registration holes were placed diagonally across the PCB for layer alignment.
- Mounting Holes: Four mounting holes were placed near the corners for securing the PCB to the test fixture.
7.4 Results
The final design met all alignment, registration, and testing requirements. The tooling holes ensured that the PCB was accurately assembled and tested, resulting in a reliable and high-quality product.
8. Conclusion
Tooling holes are a critical yet often overlooked aspect of PCB design and manufacturing. By understanding their purpose, types, placement guidelines, and best practices, you can ensure that your PCB is manufactured and assembled with precision and reliability. Whether you’re designing a simple single-layer PCB or a complex multi-layer board, incorporating well-planned tooling holes will contribute to the overall success of your project.
This guide provides a comprehensive overview of PCB tooling holes, including their purpose, types, placement guidelines, and best practices. By following the principles outlined here, you can design PCBs that are manufacturable, reliable, and meet the demands of modern electronics applications.