The telecommunications industry is undergoing a significant transformation with the advent of Open Radio Access Networks (ORANs). ORANs represent a paradigm shift in the way radio access networks (RANs) are designed, deployed, and managed. By promoting open interfaces, interoperability, and disaggregation, ORANs aim to reduce costs, enhance flexibility, and accelerate innovation in 5G and beyond. For PCB designers, this shift presents both opportunities and challenges. This article provides a comprehensive guide to ORANs, exploring their architecture, key components, design considerations, and the role of PCB designers in enabling this transformative technology.
1. What are Open Radio Access Networks (ORANs)?
1.1 Definition
Open Radio Access Networks (ORANs) are a new approach to designing and deploying radio access networks (RANs) that emphasize open standards, interoperability, and disaggregation. Unlike traditional RANs, which are often proprietary and tightly integrated, ORANs enable operators to mix and match components from different vendors, fostering competition and innovation.
1.2 Key Principles
- Open Interfaces: ORANs use standardized, open interfaces to enable interoperability between components from different vendors.
- Disaggregation: ORANs separate hardware and software, allowing operators to choose best-of-breed solutions for each component.
- Virtualization: ORANs leverage network function virtualization (NFV) and software-defined networking (SDN) to enhance flexibility and scalability.
1.3 Benefits of ORANs
- Cost Reduction: By promoting competition and reducing reliance on proprietary solutions, ORANs can lower capital and operational expenses.
- Flexibility: Operators can customize their networks to meet specific requirements, enabling faster deployment of new services.
- Innovation: Open standards and disaggregation encourage innovation, allowing new players to enter the market and offer innovative solutions.
2. ORAN Architecture
2.1 Key Components
The ORAN architecture consists of several key components, each with specific functions:
- Radio Unit (RU): Handles the transmission and reception of radio signals. The RU is typically located near the antenna and performs analog and digital signal processing.
- Distributed Unit (DU): Manages real-time baseband processing, including scheduling, encoding, and modulation. The DU is often located closer to the RU to minimize latency.
- Centralized Unit (CU): Handles non-real-time processing, such as packet routing, mobility management, and network slicing. The CU can be located further from the RU and DU, often in a centralized data center.
- ORAN Interfaces: Standardized interfaces, such as the eCPRI and F1 interfaces, enable communication between the RU, DU, and CU.
2.2 Functional Split
The ORAN architecture introduces a functional split between the RU, DU, and CU, allowing operators to optimize the placement of each component based on latency, bandwidth, and processing requirements. The 3GPP has defined several functional split options, each with different trade-offs between centralization and decentralization.
3. PCB Design Considerations for ORANs
3.1 High-Frequency Design
ORANs operate at high frequencies, particularly in the millimeter-wave (mmWave) bands used for 5G. PCB designers must consider:
- Signal Integrity: Minimize signal loss, reflection, and crosstalk by using controlled impedance traces, proper grounding, and low-loss materials.
- Material Selection: Choose PCB materials with low dielectric loss (low loss tangent) and stable dielectric constants, such as Rogers or PTFE-based materials.
- Thermal Management: High-frequency circuits generate significant heat, requiring effective thermal management through heat sinks, thermal vias, and proper component placement.
3.2 Power Integrity
ORAN components, particularly the RU and DU, require stable and efficient power delivery. PCB designers must:
- Decoupling Capacitors: Place decoupling capacitors close to power pins to filter high-frequency noise.
- Power Planes: Use dedicated power and ground planes to minimize impedance and ensure stable power delivery.
- Voltage Regulation: Implement efficient voltage regulation circuits to meet the power requirements of high-performance components.
3.3 Electromagnetic Compatibility (EMC)
ORANs must comply with stringent EMC regulations to avoid interference with other devices. PCB designers should:
- Shielding: Use shielding techniques, such as grounded metal enclosures or conductive coatings, to reduce electromagnetic interference (EMI).
- Filtering: Implement filtering circuits to suppress unwanted noise and harmonics.
- Layout Optimization: Optimize the PCB layout to minimize loop areas and reduce radiation.
3.4 Miniaturization and Integration
ORAN components, particularly the RU, must be compact and lightweight to facilitate deployment. PCB designers should:
- High-Density Interconnects (HDI): Use HDI technology to achieve higher component density and reduce the PCB size.
- Embedded Components: Consider embedding passive components, such as resistors and capacitors, within the PCB to save space.
- 3D Packaging: Explore 3D packaging techniques, such as system-in-package (SiP) or chip-on-board (CoB), to integrate multiple functions into a single module.
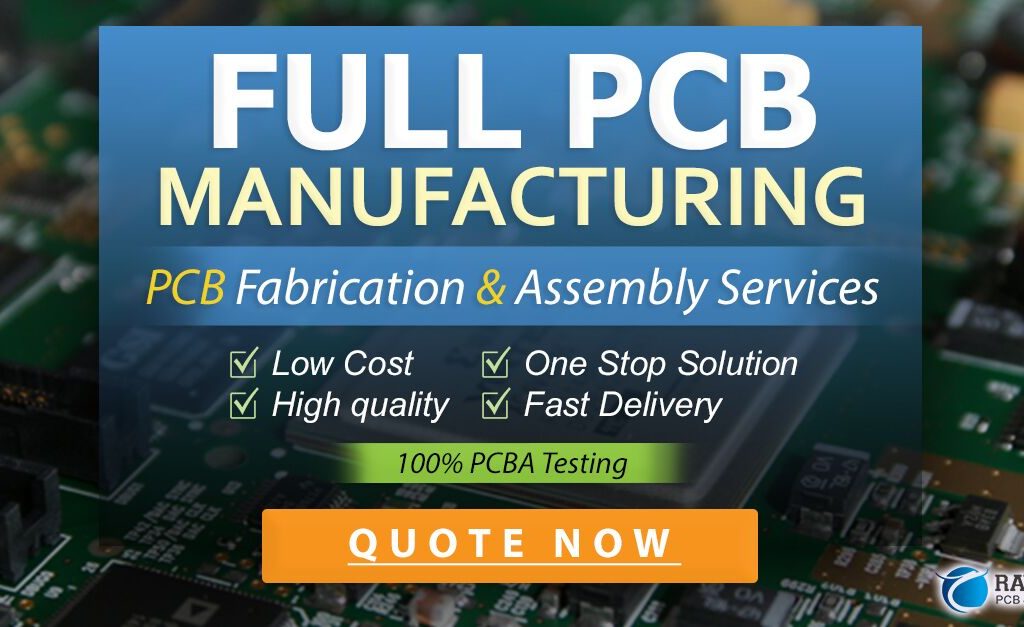
4. Key Challenges in ORAN PCB Design
4.1 Complexity
ORANs involve complex architectures and high-performance components, requiring advanced design techniques and tools. PCB designers must have a deep understanding of high-frequency design, signal integrity, and thermal management.
4.2 Interoperability
Ensuring interoperability between components from different vendors is a key challenge in ORANs. PCB designers must adhere to standardized interfaces and specifications to ensure compatibility.
4.3 Cost
While ORANs aim to reduce costs, achieving high performance and reliability can be expensive. PCB designers must balance performance requirements with cost constraints, particularly in high-volume production.
4.4 Testing and Validation
ORAN components must undergo rigorous testing and validation to ensure compliance with performance and regulatory requirements. PCB designers should collaborate closely with test engineers to develop comprehensive test plans and fixtures.
5. Best Practices for ORAN PCB Design
5.1 Collaborate with Stakeholders
Work closely with system architects, RF engineers, and software developers to understand the requirements and constraints of the ORAN design. Early collaboration can help identify potential issues and optimize the design.
5.2 Use Advanced Design Tools
Leverage advanced PCB design tools that support high-frequency design, signal integrity analysis, and thermal simulation. These tools can help optimize the design and reduce the risk of errors.
5.3 Follow Industry Standards
Adhere to industry standards and specifications, such as those defined by the O-RAN Alliance and 3GPP, to ensure interoperability and compliance.
5.4 Perform Design for Manufacturability (DFM) Checks
Use DFM tools to ensure that the design is manufacturable and meets the requirements of the chosen fabrication and assembly processes.
5.5 Test and Validate Prototypes
Thoroughly test and validate prototypes to ensure that they meet performance and regulatory requirements. This may involve electrical testing, thermal analysis, and EMC testing.
6. Case Study: ORAN PCB Design for a 5G Base Station
To illustrate the challenges and best practices in ORAN PCB design, let’s examine a case study involving a 5G base station.
6.1 Design Requirements
- Frequency Range: 24 GHz to 40 GHz (mmWave band).
- Performance: High signal integrity, low latency, and high power efficiency.
- Form Factor: Compact and lightweight for easy deployment.
6.2 Material Selection
The design team selected Rogers RO4350B, a low-loss material with a stable dielectric constant and low loss tangent, to minimize signal loss at high frequencies.
6.3 Design Optimization
- Signal Integrity: Optimized trace geometry and impedance matching to minimize signal loss and reflection.
- Thermal Management: Implemented thermal vias and a heat sink to dissipate heat generated by high-power components.
- Miniaturization: Used HDI technology and embedded components to achieve a compact design.
6.4 Testing and Validation
The design underwent rigorous testing, including signal integrity analysis, thermal testing, and EMC testing, to ensure compliance with performance and regulatory requirements.
6.5 Results
The final design met all performance and form factor requirements, enabling the successful deployment of the 5G base station. The optimized PCB design minimized signal loss, ensured reliable operation, and facilitated easy deployment.
7. Conclusion
Open Radio Access Networks (ORANs) represent a transformative shift in the telecommunications industry, offering new opportunities for cost reduction, flexibility, and innovation. For PCB designers, ORANs present both challenges and opportunities, requiring advanced design techniques and a deep understanding of high-frequency, high-performance electronics. By following best practices and leveraging advanced tools, PCB designers can play a critical role in enabling the success of ORANs and the future of 5G and beyond.
This guide provides a comprehensive overview of ORANs and the key considerations for PCB designers. By understanding the architecture, challenges, and best practices outlined here, you can design high-performance PCBs that meet the demands of ORANs and contribute to the advancement of telecommunications technology.