Introduction
As electronic devices continue to evolve, their power densities and thermal loads have increased significantly. Effective thermal management is crucial to ensure the reliability, performance, and longevity of electronic equipment. Active cooling systems, which require external energy to operate, are widely used to manage heat dissipation in high-power and high-density electronic systems. This article provides a comprehensive comparison of various active cooling systems and techniques, exploring their principles, advantages, disadvantages, and applications.
Understanding Active Cooling Systems
What is Active Cooling?
Active cooling refers to thermal management techniques that use external energy to remove heat from electronic components. Unlike passive cooling, which relies on natural convection, radiation, and conduction, active cooling systems employ fans, pumps, or other mechanical means to enhance heat dissipation.
Importance of Active Cooling
Active cooling is essential for:
- Preventing Overheating: Ensuring that electronic components operate within their safe temperature ranges.
- Maintaining Performance: Preventing thermal throttling and maintaining optimal performance.
- Extending Lifespan: Reducing thermal stress and extending the lifespan of electronic components.
- Ensuring Reliability: Minimizing the risk of thermal-induced failures and ensuring reliable operation.
Types of Active Cooling Systems
Air Cooling
Principles
Air cooling uses fans or blowers to circulate air over heat sinks or directly onto electronic components. The moving air absorbs heat from the components and dissipates it into the surrounding environment.
Advantages
- Simplicity: Easy to design and implement.
- Cost-Effective: Generally lower cost compared to other active cooling methods.
- Maintenance: Minimal maintenance required.
- Versatility: Suitable for a wide range of applications, from consumer electronics to industrial equipment.
Disadvantages
- Noise: Fans can generate noise, which may be undesirable in certain applications.
- Limited Cooling Capacity: Less effective for very high-power or high-density systems.
- Dust Accumulation: Fans can draw dust into the system, potentially leading to clogging and reduced efficiency.
Applications
- Computers and Servers: CPU and GPU cooling.
- Consumer Electronics: Gaming consoles, set-top boxes.
- Industrial Equipment: Control panels, power supplies.
Liquid Cooling
Principles
Liquid cooling uses a liquid coolant (usually water or a water-glycol mixture) to absorb heat from electronic components. The heated coolant is then circulated through a radiator or heat exchanger, where it is cooled before being recirculated.
Advantages
- High Cooling Capacity: More effective at dissipating large amounts of heat compared to air cooling.
- Efficiency: Better thermal conductivity of liquids allows for more efficient heat transfer.
- Compact Design: Can be more compact than air cooling systems for the same cooling capacity.
- Quiet Operation: Generally quieter than air cooling systems.
Disadvantages
- Complexity: More complex design and installation compared to air cooling.
- Cost: Higher initial and maintenance costs.
- Leakage Risk: Potential for coolant leakage, which can damage electronic components.
- Maintenance: Requires regular maintenance to ensure proper operation and prevent coolant degradation.
Applications
- High-Performance Computing: Data centers, supercomputers.
- Gaming PCs: High-end gaming systems with overclocked components.
- Electric Vehicles: Battery and power electronics cooling.
- Industrial Machinery: High-power motor drives, laser systems.
Thermoelectric Cooling (Peltier Cooling)
Principles
Thermoelectric cooling uses the Peltier effect, where an electric current is passed through a thermoelectric module to create a temperature difference. One side of the module absorbs heat (cooling the electronic component), while the other side dissipates heat.
Advantages
- Compact Size: Small and lightweight, suitable for space-constrained applications.
- Precision Cooling: Can achieve precise temperature control.
- No Moving Parts: No fans or pumps, resulting in quiet operation and reduced mechanical wear.
- Reversibility: Can be used for both cooling and heating by reversing the current.
Disadvantages
- Efficiency: Generally less efficient than other cooling methods, especially for large heat loads.
- Power Consumption: Requires a significant amount of electrical power.
- Heat Dissipation: Requires an effective method to dissipate heat from the hot side of the module.
- Cost: Higher cost compared to air cooling.
Applications
- Medical Devices: Cooling of diagnostic equipment, sample storage.
- Consumer Electronics: Compact cooling solutions for small devices.
- Aerospace: Thermal management in avionics and satellite systems.
- Laboratory Equipment: Precision temperature control in scientific instruments.
Refrigeration Cooling
Principles
Refrigeration cooling uses a refrigeration cycle, similar to that in air conditioners and refrigerators, to remove heat from electronic components. The cycle involves compressing and expanding a refrigerant to absorb and dissipate heat.
Advantages
- High Cooling Capacity: Capable of removing large amounts of heat.
- Low Temperature: Can achieve temperatures below ambient, suitable for extreme cooling requirements.
- Efficiency: Effective for high-power and high-density systems.
Disadvantages
- Complexity: Complex design and installation.
- Cost: High initial and operational costs.
- Maintenance: Requires regular maintenance and refrigerant replenishment.
- Size and Weight: Generally larger and heavier than other cooling methods.
Applications
- High-Performance Computing: Extreme cooling for overclocked systems.
- Military and Aerospace: Cooling of high-power radar and communication systems.
- Industrial Equipment: Cooling of high-power lasers and machining systems.
- Medical Imaging: Cooling of MRI and CT scan equipment.
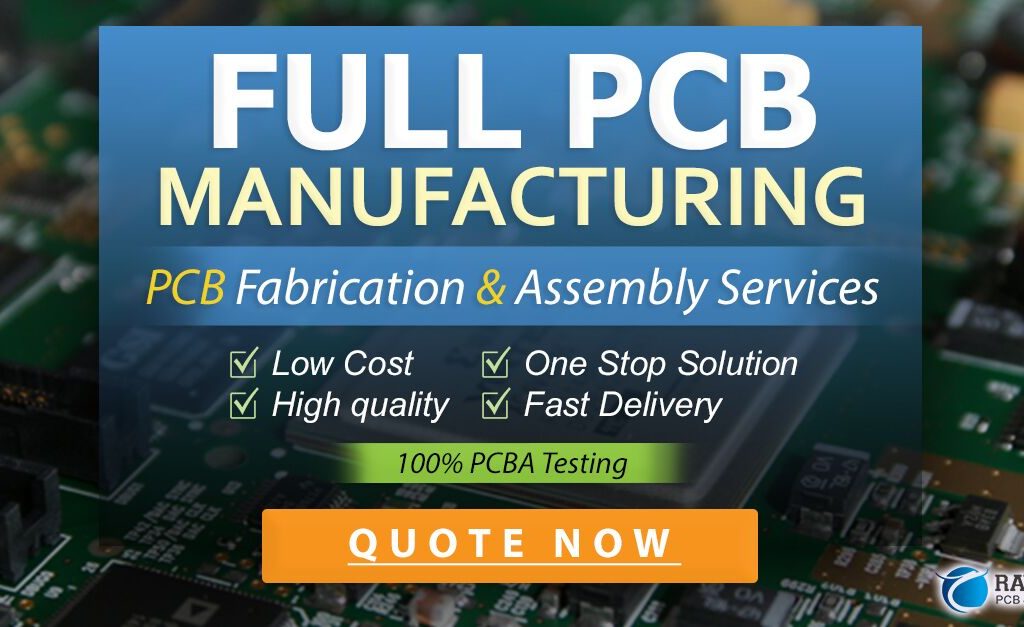
Phase-Change Cooling
Principles
Phase-change cooling uses the latent heat of vaporization of a refrigerant to absorb heat from electronic components. The refrigerant evaporates at the heat source, absorbing heat, and then condenses in a heat exchanger, releasing the heat.
Advantages
- High Cooling Capacity: Effective at removing large amounts of heat.
- Efficiency: High heat transfer efficiency due to the phase-change process.
- Compact Design: Can be more compact than other cooling methods for the same cooling capacity.
Disadvantages
- Complexity: Complex design and installation.
- Cost: High initial and operational costs.
- Maintenance: Requires regular maintenance and refrigerant replenishment.
- Leakage Risk: Potential for refrigerant leakage.
Applications
- High-Performance Computing: Cooling of high-power CPUs and GPUs.
- Aerospace: Thermal management in avionics and satellite systems.
- Industrial Equipment: Cooling of high-power lasers and machining systems.
- Electric Vehicles: Battery and power electronics cooling.
Comparison of Active Cooling Systems
Cooling Capacity
- Air Cooling: Suitable for low to moderate heat loads.
- Liquid Cooling: Effective for moderate to high heat loads.
- Thermoelectric Cooling: Suitable for small to moderate heat loads.
- Refrigeration Cooling: Capable of handling very high heat loads.
- Phase-Change Cooling: Effective for very high heat loads.
Efficiency
- Air Cooling: Moderate efficiency.
- Liquid Cooling: High efficiency.
- Thermoelectric Cooling: Lower efficiency, especially for large heat loads.
- Refrigeration Cooling: High efficiency.
- Phase-Change Cooling: Very high efficiency.
Complexity and Cost
- Air Cooling: Simple and cost-effective.
- Liquid Cooling: Moderate complexity and cost.
- Thermoelectric Cooling: Moderate complexity and higher cost.
- Refrigeration Cooling: High complexity and cost.
- Phase-Change Cooling: High complexity and cost.
Noise Level
- Air Cooling: Can be noisy due to fans.
- Liquid Cooling: Generally quieter than air cooling.
- Thermoelectric Cooling: Quiet operation.
- Refrigeration Cooling: Can be noisy due to compressors.
- Phase-Change Cooling: Generally quiet operation.
Maintenance
- Air Cooling: Minimal maintenance.
- Liquid Cooling: Requires regular maintenance.
- Thermoelectric Cooling: Minimal maintenance.
- Refrigeration Cooling: Requires regular maintenance.
- Phase-Change Cooling: Requires regular maintenance.
Best Practices for Implementing Active Cooling Systems
Assess Thermal Requirements
- Heat Load: Determine the total heat load that needs to be dissipated.
- Temperature Limits: Identify the maximum allowable temperatures for critical components.
- Environmental Conditions: Consider the operating environment, including ambient temperature and airflow.
Select Appropriate Cooling Method
- Match Cooling Capacity: Choose a cooling method that can handle the heat load and maintain component temperatures within safe limits.
- Consider Application Constraints: Factor in space, weight, noise, and cost constraints.
- Evaluate Efficiency: Select a cooling method that provides the required efficiency without excessive power consumption.
Optimize System Design
- Component Placement: Arrange components to facilitate effective heat dissipation.
- Heat Sink Design: Use optimized heat sinks to enhance heat transfer.
- Airflow Management: Ensure proper airflow within the enclosure to prevent hot spots.
- Thermal Interface Materials: Use high-quality thermal interface materials to improve heat transfer between components and heat sinks.
Implement Monitoring and Control
- Temperature Sensors: Install temperature sensors to monitor component temperatures.
- Fan Speed Control: Use variable speed fans to adjust cooling based on thermal load.
- Automated Control Systems: Implement automated control systems to optimize cooling performance and energy efficiency.
Perform Testing and Validation
- Thermal Testing: Conduct thermal testing to verify that the cooling system meets the design requirements.
- Environmental Testing: Perform environmental testing to ensure reliable operation under various conditions.
- Long-Term Reliability Testing: Conduct long-term reliability testing to identify potential failure modes and ensure durability.
Case Studies
Case Study 1: Data Center Cooling
Application: Cooling of High-Density Servers in a Data Center
Challenges:
- High heat load due to dense server racks
- Need for efficient and reliable cooling
- Minimizing energy consumption and operational costs
Solution:
- Implemented liquid cooling with chilled water systems
- Used hot aisle/cold aisle containment to optimize airflow
- Installed temperature sensors and automated control systems for efficient cooling management
Outcome:
- Effective cooling of high-density servers
- Reduced energy consumption and operational costs
- Improved reliability and performance of data center operations
Case Study 2: Electric Vehicle Battery Cooling
Application: Thermal Management of Battery Packs in an Electric Vehicle
Challenges:
- High heat load from battery packs during charging and discharging
- Need for compact and lightweight cooling solutions
- Ensuring safety and reliability in a mobile environment
- Solution:
- Implemented liquid cooling with a water-glycol coolant
- Used cold plates integrated into the battery pack for efficient heat transfer
- Installed temperature sensors and control systems to monitor and manage battery temperature
Outcome:
- Effective thermal management of battery packs
- Compact and lightweight cooling solution suitable for electric vehicles
- Enhanced safety and reliability of battery operation
Case Study 3: High-Performance Gaming PC Cooling
Application: Cooling of Overclocked CPU and GPU in a Gaming PC
Challenges:
- High heat load from overclocked components
- Need for efficient and quiet cooling
- Space constraints within the PC case
Solution:
- Implemented liquid cooling with a custom loop
- Used high-performance radiators and fans for efficient heat dissipation
- Installed temperature sensors and fan speed control for optimized cooling performance
Outcome:
- Effective cooling of overclocked CPU and GPU
- Quiet operation with minimal noise
- Compact and efficient cooling solution within the PC case
Conclusion
Active cooling systems are essential for managing the thermal loads of modern electronic equipment, ensuring reliable performance and longevity. By understanding the principles, advantages, and disadvantages of various active cooling techniques, engineers can select and implement the most appropriate cooling solution for their specific applications. Whether cooling high-performance computing systems, electric vehicle batteries, or gaming PCs, effective thermal management is crucial for achieving optimal performance and reliability. By following best practices and leveraging advanced cooling technologies, engineers can design and implement efficient and reliable active cooling systems that meet the demands of today’s high-power and high-density electronic devices.