Introduction
In the competitive world of electronics, Printed Circuit Board (PCB) designers are constantly striving to improve their designs, reduce costs, and enhance performance. One of the most effective ways to achieve these goals is through benchmarking. Benchmarking is the process of comparing your PCB designs, processes, and performance metrics against industry standards or best practices to identify areas for improvement. This comprehensive guide will delve into the benchmarking practices and processes that PCB designers can adopt to stay ahead in the industry.
Understanding Benchmarking in PCB Design
What is Benchmarking?
Benchmarking is a systematic process of measuring and comparing your products, services, and processes against those of industry leaders or competitors. The goal is to identify best practices, set performance standards, and implement changes that lead to improved performance and efficiency.
Importance of Benchmarking for PCB Designers
- Performance Improvement: Benchmarking helps identify gaps in performance and areas for improvement, leading to better PCB designs.
- Cost Reduction: By adopting best practices, PCB designers can reduce costs associated with materials, manufacturing, and testing.
- Innovation: Benchmarking encourages innovation by exposing designers to new technologies, methodologies, and design techniques.
- Competitive Advantage: Staying ahead of industry standards and competitors can provide a significant competitive advantage.
- Quality Assurance: Benchmarking ensures that your designs meet or exceed industry quality standards, leading to higher customer satisfaction.
Types of Benchmarking
1. Internal Benchmarking
Internal benchmarking involves comparing different departments, teams, or projects within the same organization. This type of benchmarking is useful for identifying best practices within the company and promoting knowledge sharing.
- Advantages: Easy access to data, promotes internal collaboration, and identifies internal best practices.
- Disadvantages: Limited to the organization’s current knowledge and practices, may not reveal industry-leading innovations.
2. Competitive Benchmarking
Competitive benchmarking involves comparing your PCB designs and processes against those of direct competitors. This type of benchmarking helps identify areas where your competitors are outperforming you and provides insights into their strategies.
- Advantages: Provides direct comparison with competitors, highlights competitive strengths and weaknesses.
- Disadvantages: Difficult to obtain detailed competitor data, may lead to reactive rather than proactive improvements.
3. Functional Benchmarking
Functional benchmarking involves comparing your processes and performance metrics with those of companies in different industries but with similar functions. For example, a PCB designer might benchmark their supply chain management against a company in the automotive industry.
- Advantages: Encourages cross-industry innovation, provides fresh perspectives and ideas.
- Disadvantages: May require significant effort to adapt practices from different industries, less direct relevance.
4. Generic Benchmarking
Generic benchmarking involves comparing your processes and performance metrics against industry-wide best practices, regardless of the industry. This type of benchmarking is useful for identifying universal best practices that can be applied across various sectors.
404: 02-20 09:25:58
- Advantages: Broadens the scope of improvement, identifies universal best practices.
- Disadvantages: May lack specific relevance to PCB design, requires careful adaptation of practices.
Benchmarking Process for PCB Designers
Step 1: Define Objectives and Scope
The first step in the benchmarking process is to define the objectives and scope of the benchmarking study. Clearly outline what you aim to achieve through benchmarking and identify the specific areas of PCB design and processes that will be evaluated.
- Objectives: Improve design efficiency, reduce costs, enhance performance, etc.
- Scope: Design processes, material selection, manufacturing techniques, testing procedures, etc.
Step 2: Identify Benchmarking Partners
Identify the organizations, competitors, or industry leaders that you will benchmark against. These can be internal teams, direct competitors, or companies from different industries with similar functions.
- Internal: Different design teams within your organization.
- Competitive: Direct competitors in the PCB design industry.
- Functional: Companies in different industries with similar processes.
- Generic: Industry-wide best practices.
Step 3: Collect Data
Gather data on the performance metrics, processes, and practices of the benchmarking partners. This can include design cycle times, material costs, manufacturing yields, defect rates, and customer satisfaction scores.
- Data Sources: Industry reports, competitor websites, customer feedback, internal records, etc.
- Data Collection Methods: Surveys, interviews, site visits, literature review, etc.
Step 4: Analyze Data
Analyze the collected data to identify gaps, best practices, and areas for improvement. Compare your performance metrics against those of the benchmarking partners and determine where you stand in relation to industry standards.
- Gap Analysis: Identify performance gaps between your designs and those of the benchmarking partners.
- Best Practices: Highlight the best practices that lead to superior performance.
- Root Cause Analysis: Determine the underlying causes of performance gaps.
Step 5: Develop Improvement Plans
Based on the analysis, develop actionable improvement plans to address the identified gaps and adopt best practices. Set specific, measurable, achievable, relevant, and time-bound (SMART) goals for improvement.
- Action Items: Specific steps to improve design processes, reduce costs, enhance performance, etc.
- Resource Allocation: Allocate resources (time, budget, personnel) to implement the improvement plans.
- Timeline: Set a timeline for achieving the improvement goals.
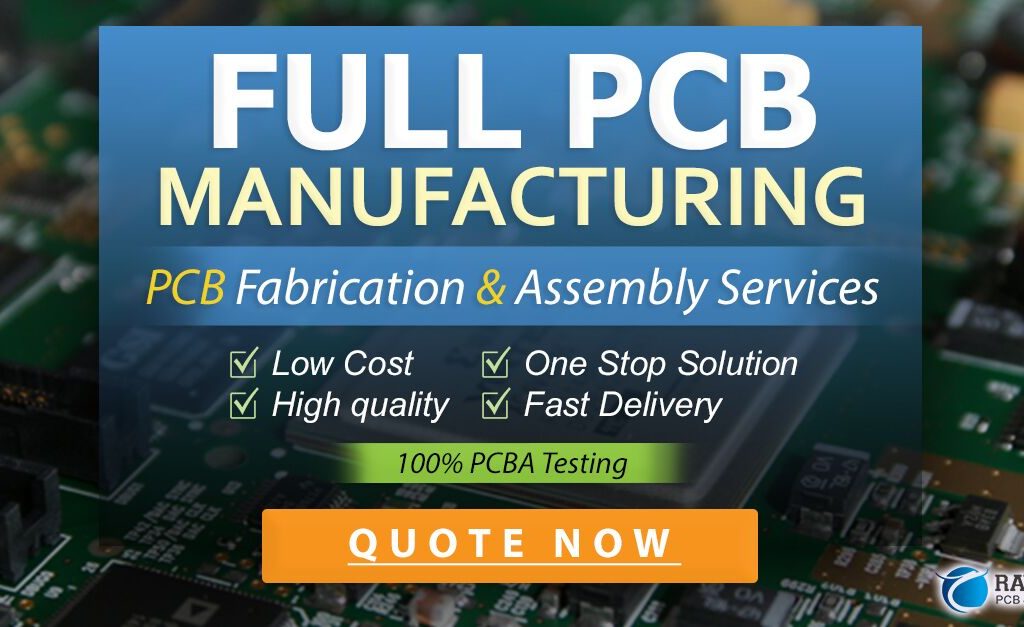
Step 6: Implement Changes
Implement the improvement plans and make the necessary changes to your PCB design processes. This may involve adopting new technologies, revising design guidelines, training staff, or optimizing supply chain management.
- Change Management: Ensure smooth implementation of changes through effective communication and training.
- Monitoring: Continuously monitor the implementation process to ensure adherence to the improvement plans.
Step 7: Evaluate Results
Evaluate the results of the implemented changes to determine their effectiveness. Compare the new performance metrics against the previous ones and assess whether the improvement goals have been achieved.
- Performance Metrics: Measure key performance indicators (KPIs) such as design cycle time, cost reduction, defect rates, etc.
- Feedback: Gather feedback from stakeholders, including designers, manufacturers, and customers.
- Adjustments: Make any necessary adjustments to the improvement plans based on the evaluation results.
Step 8: Continuous Improvement
Benchmarking is an ongoing process. Continuously monitor industry trends, update your benchmarking studies, and strive for continuous improvement in your PCB design processes.
- Regular Reviews: Conduct regular reviews of your benchmarking studies and improvement plans.
- Stay Updated: Stay informed about new technologies, methodologies, and industry standards.
- Innovate: Encourage innovation and experimentation to stay ahead of the competition.
Best Practices for Benchmarking in PCB Design
1. Focus on Key Performance Indicators (KPIs)
Identify and focus on the KPIs that are most relevant to your PCB design processes. Common KPIs include design cycle time, cost per unit, defect rates, and customer satisfaction scores.
2. Use a Structured Approach
Follow a structured and systematic approach to benchmarking to ensure consistency and accuracy. Use standardized data collection methods, analysis techniques, and reporting formats.
3. Involve Stakeholders
Involve key stakeholders, including designers, engineers, manufacturers, and customers, in the benchmarking process. Their input and feedback are valuable for identifying areas for improvement and ensuring buy-in for the improvement plans.
4. Leverage Technology
Use technology and software tools to streamline the benchmarking process. Data analysis software, simulation tools, and project management platforms can enhance the efficiency and accuracy of your benchmarking studies.
5. Learn from Multiple Sources
Benchmark against multiple sources, including internal teams, competitors, and companies from different industries. This broadens your perspective and provides a more comprehensive understanding of best practices.
6. Document and Share Findings
Document the findings of your benchmarking studies and share them with relevant stakeholders. This promotes knowledge sharing and ensures that the insights gained from benchmarking are effectively utilized.
7. Foster a Culture of Continuous Improvement
Encourage a culture of continuous improvement within your organization. Promote the importance of benchmarking and provide the necessary resources and support for ongoing improvement initiatives.
Common Challenges in Benchmarking for PCB Designers
1. Data Availability
Obtaining accurate and relevant data for benchmarking can be challenging, especially when benchmarking against competitors. Ensure that you use reliable data sources and validate the data before analysis.
2. Resistance to Change
Implementing changes based on benchmarking findings may face resistance from stakeholders. Effective communication, training, and change management strategies are essential to overcome this challenge.
3. Resource Constraints
Benchmarking requires time, effort, and resources. Ensure that you allocate sufficient resources to the benchmarking process and prioritize the most critical areas for improvement.
4. Adapting Best Practices
Adapting best practices from different industries or organizations may require significant effort and customization. Carefully evaluate the relevance and feasibility of adopting these practices in your PCB design processes.
5. Maintaining Momentum
Maintaining momentum and commitment to continuous improvement can be challenging. Regularly review and update your benchmarking studies, and celebrate successes to keep the team motivated.
Conclusion
Benchmarking is a powerful tool for PCB designers to improve their designs, reduce costs, and enhance performance. By following a structured benchmarking process, focusing on key performance indicators, and adopting best practices, PCB designers can stay ahead in the competitive electronics industry. Overcoming common challenges and fostering a culture of continuous improvement will ensure that your benchmarking efforts lead to sustained success and innovation. With this comprehensive guide, you are well-equipped to embark on your benchmarking journey and achieve excellence in PCB design.