Printed Circuit Boards (PCBs) are the backbone of modern electronics, serving as the foundation for virtually every electronic device we use today. From smartphones and laptops to industrial machinery and medical equipment, PCBs play a critical role in ensuring the functionality and reliability of electronic systems. However, the PCB manufacturing process is complex and involves numerous steps, each of which can introduce nuances that may affect the final product’s quality, performance, and reliability. Eliminating these nuances is essential to achieving consistent, high-quality PCB production.
This article delves into the intricacies of the PCB manufacturing process, identifies common nuances that can arise, and explores strategies to eliminate them. By understanding and addressing these challenges, manufacturers can improve efficiency, reduce costs, and deliver superior products to their customers.
Understanding the PCB Manufacturing Process
Before addressing the nuances, it is essential to understand the key steps involved in PCB manufacturing. The process typically includes the following stages:
- Design and Layout: The process begins with the design of the PCB using specialized software. The layout includes the placement of components, routing of traces, and definition of layers.
- Material Selection: The choice of materials, such as the substrate (e.g., FR-4), copper foil, and solder mask, significantly impacts the PCB’s performance.
- Printing the Design: The design is transferred onto the PCB substrate using a process called photolithography. This involves applying a photosensitive layer and exposing it to UV light through a photomask.
- Etching: Unwanted copper is removed from the substrate using chemical etching, leaving behind the desired circuit pattern.
- Drilling: Holes are drilled into the PCB for through-hole components and vias.
- Plating: The drilled holes are plated with copper to establish electrical connections between layers.
- Solder Mask Application: A protective layer is applied to prevent short circuits and protect the copper traces from oxidation.
- Silkscreen Printing: Labels, component identifiers, and other markings are printed onto the PCB for assembly and troubleshooting.
- Surface Finish: A surface finish, such as HASL (Hot Air Solder Leveling) or ENIG (Electroless Nickel Immersion Gold), is applied to protect the copper and improve solderability.
- Testing and Inspection: The finished PCB undergoes rigorous testing and inspection to ensure it meets quality standards.
- Assembly: Components are mounted onto the PCB using soldering techniques such as reflow or wave soldering.
- Final Testing: The assembled PCB is tested to verify its functionality and performance.
Each of these steps presents opportunities for nuances to arise, which can lead to defects, inefficiencies, or suboptimal performance. Let’s explore these nuances and how to eliminate them.
Common Nuances in PCB Manufacturing
1. Design-Related Nuances
- Inadequate Design for Manufacturability (DFM): Poorly designed PCBs can be difficult or impossible to manufacture efficiently. For example, traces that are too close together may cause short circuits, while insufficient clearance around components can lead to assembly issues.
- Incorrect Layer Stackup: Improper layer stackup can result in signal integrity issues, impedance mismatches, or thermal problems.
- Lack of Testing Provisions: Failing to include test points or accessibility for debugging can complicate quality control and troubleshooting. Solution: Implement robust DFM guidelines and collaborate closely with design engineers to ensure the PCB layout is optimized for manufacturing. Use simulation tools to validate the design before production.
2. Material-Related Nuances
- Inconsistent Material Quality: Variations in the quality of substrates, copper, or solder mask can lead to performance issues or defects.
- Incorrect Material Selection: Using materials that are not suited for the intended application (e.g., high-frequency or high-temperature environments) can compromise the PCB’s reliability. Solution: Source materials from reputable suppliers and conduct thorough quality checks. Select materials based on the specific requirements of the application.
3. Photolithography and Etching Nuances
- Over- or Under-Etching: Improper etching can result in traces that are too thin or too thick, affecting electrical performance.
- Misalignment: Misalignment during photolithography can cause shorts or open circuits. Solution: Maintain precise control over the etching process and regularly calibrate equipment. Use advanced alignment techniques to ensure accuracy.
4. Drilling and Plating Nuances
- Drilling Errors: Incorrect hole sizes or misplaced holes can render the PCB unusable.
- Poor Plating Quality: Inadequate plating can lead to weak electrical connections or via failures. Solution: Use high-precision drilling machines and inspect holes for accuracy. Ensure proper plating thickness and uniformity through rigorous quality control.
5. Solder Mask and Silkscreen Nuances
- Incomplete Coverage: Gaps in the solder mask can expose copper traces to oxidation or short circuits.
- Misprinted Silkscreen: Incorrect or unclear markings can cause assembly errors or complicate troubleshooting. Solution: Apply the solder mask evenly and inspect for coverage. Use high-resolution printing techniques for silkscreen markings.
6. Surface Finish Nuances
- Uneven Surface Finish: Variations in the surface finish can affect solderability and component adhesion.
- Contamination: Contaminants on the surface can lead to poor solder joints or corrosion. Solution: Ensure consistent application of the surface finish and clean the PCB thoroughly before and after the process.
7. Testing and Inspection Nuances
- Inadequate Testing: Skipping or insufficient testing can allow defects to go undetected.
- False Positives/Negatives: Incorrect test results can lead to unnecessary rework or missed defects. Solution: Implement comprehensive testing protocols, including automated optical inspection (AOI), X-ray inspection, and functional testing. Regularly calibrate testing equipment to ensure accuracy.
8. Assembly-Related Nuances
- Component Misplacement: Incorrect placement of components can cause electrical failures.
- Soldering Defects: Issues such as cold joints, bridging, or voids can compromise the PCB’s functionality. Solution: Use automated pick-and-place machines for accurate component placement. Optimize soldering processes and inspect solder joints for quality.
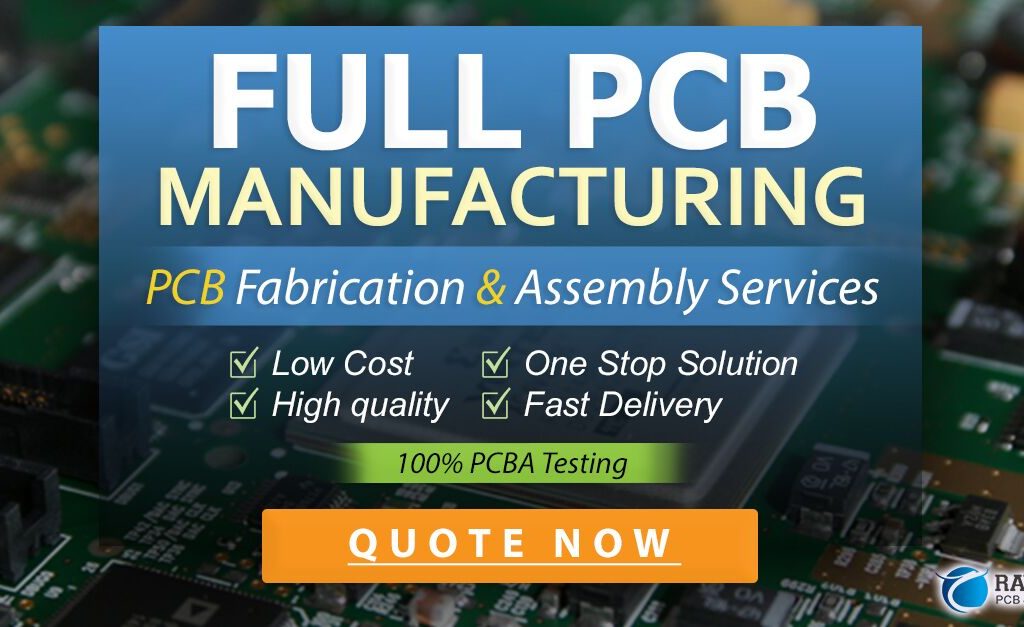
Strategies for Eliminating Nuances in PCB Manufacturing
To eliminate nuances in the PCB manufacturing process, manufacturers must adopt a proactive and systematic approach. Here are some key strategies:
1. Standardization
- Develop and adhere to standardized processes and procedures for each stage of manufacturing.
- Use industry standards, such as IPC (Association Connecting Electronics Industries), as a benchmark for quality and reliability.
2. Automation
- Invest in automated equipment for tasks such as drilling, plating, and component placement to reduce human error and improve consistency.
- Implement automated inspection systems to detect defects early in the process.
3. Process Control
- Monitor and control critical process parameters, such as temperature, pressure, and chemical concentrations, to ensure consistency.
- Use statistical process control (SPC) techniques to identify and address variations.
4. Training and Skill Development
- Provide comprehensive training for operators and technicians to ensure they understand the processes and can identify potential issues.
- Encourage continuous learning and skill development to keep up with advancements in technology.
5. Collaboration and Communication
- Foster collaboration between design, engineering, and manufacturing teams to address potential issues early in the design phase.
- Maintain open communication channels to quickly resolve any problems that arise during production.
6. Quality Assurance
- Implement a robust quality assurance program that includes regular audits, inspections, and testing.
- Use root cause analysis to identify and address the underlying causes of defects.
7. Continuous Improvement
- Regularly review and analyze manufacturing processes to identify areas for improvement.
- Adopt lean manufacturing principles to eliminate waste and optimize efficiency.
8. Supplier Management
- Work closely with suppliers to ensure the quality and consistency of materials.
- Conduct regular audits of suppliers to verify compliance with quality standards.
The Role of Technology in Eliminating Nuances
Advancements in technology have played a significant role in addressing nuances in PCB manufacturing. Some of the key technologies include:
1. Advanced Design Software
- Modern PCB design tools offer features such as real-time DFM checks, signal integrity analysis, and thermal simulation, helping designers create more manufacturable and reliable PCBs.
2. High-Precision Equipment
- State-of-the-art drilling, plating, and assembly machines offer unparalleled accuracy and repeatability, reducing the likelihood of errors.
3. Automated Inspection Systems
- AOI, X-ray inspection, and other automated systems can detect defects that are invisible to the human eye, ensuring higher quality and reliability.
4. IoT and Data Analytics
- The Internet of Things (IoT) and data analytics enable real-time monitoring of manufacturing processes, allowing for quick identification and resolution of issues.
5. Artificial Intelligence (AI)
- AI-powered systems can analyze vast amounts of data to identify patterns and predict potential problems, enabling proactive measures to prevent defects.
Conclusion
Eliminating nuances in the PCB manufacturing process is essential for producing high-quality, reliable, and cost-effective products. By understanding the complexities of the process, identifying potential issues, and implementing robust strategies and technologies, manufacturers can achieve consistent results and meet the ever-increasing demands of the electronics industry. As technology continues to evolve, the ability to address and eliminate these nuances will become even more critical, paving the way for innovation and excellence in PCB manufacturing.