Understanding the Basics of High TG PCBs
What Does “High TG” Mean?
The term “TG” in high TG PCB stands for “Glass Transition Temperature.” This is the temperature at which the PCB substrate transitions from a rigid, glassy state to a more flexible, rubbery state. In other words, it is the point at which the material begins to soften and lose its structural integrity.
Composition of High TG PCBs
High TG PCBs are typically made from a base material called FR-4, which is a composite of woven fiberglass cloth and epoxy resin. However, the epoxy resin used in high TG PCBs is specially formulated to withstand higher temperatures compared to standard FR-4 PCBs.
The table below compares the glass transition temperatures of standard FR-4 and high TG FR-4 PCBs:
PCB Material | Glass Transition Temperature (°C) |
---|---|
Standard FR-4 | 130-140 |
High TG FR-4 | 170-180 |
As evident from the table, high TG PCBs have a significantly higher glass transition temperature, making them suitable for applications that require greater thermal stability.
Benefits of Using High TG PCBs
Enhanced Thermal Stability
One of the primary advantages of using high TG PCBs is their enhanced thermal stability. With a higher glass transition temperature, these PCBs can withstand elevated temperatures without compromising their structural integrity. This is particularly important in applications where the PCB is exposed to high-temperature environments or generates significant heat during operation.
Improved Reliability
The increased thermal stability of high TG PCBs translates to improved reliability. These PCBs are less likely to experience delamination, warping, or other temperature-related failures, which can lead to device malfunction or premature failure. By using high TG PCBs, manufacturers can create more robust and reliable electronic products.
Compatibility with Lead-Free Soldering
In recent years, there has been a growing trend towards lead-free soldering in the electronics industry due to environmental and health concerns. High TG PCBs are well-suited for lead-free soldering processes, which typically require higher reflow temperatures compared to traditional lead-based soldering.
The table below shows the typical reflow temperatures for lead-based and lead-free soldering:
Soldering Type | Typical Reflow Temperature (°C) |
---|---|
Lead-based | 220-240 |
Lead-free | 240-260 |
As high TG PCBs can withstand temperatures up to 170-180°C, they can easily accommodate the higher reflow temperatures required for lead-free soldering without experiencing thermal damage.
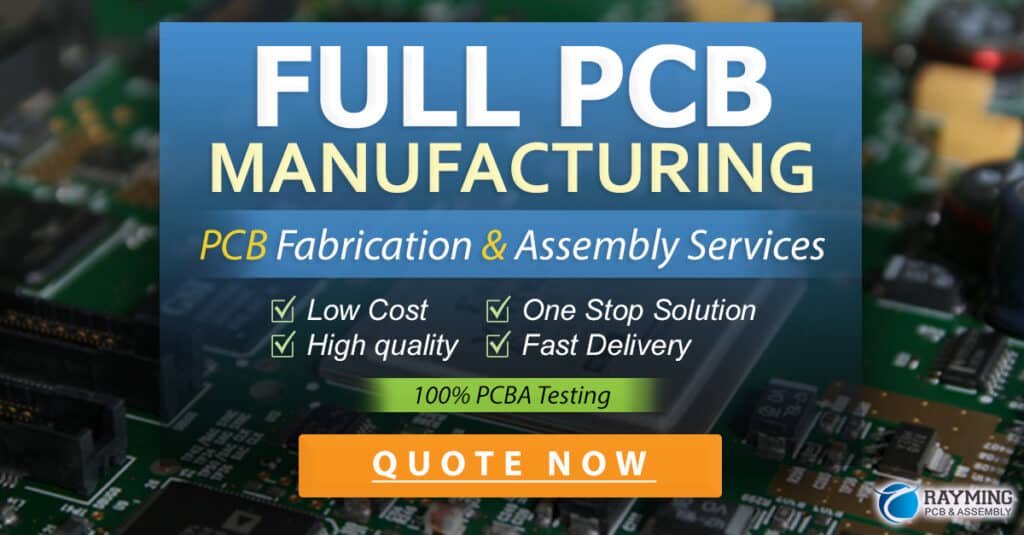
Applications of High TG PCBs
Automotive Electronics
The automotive industry is one of the primary users of high TG PCBs. Modern vehicles are equipped with numerous electronic systems, such as engine control units, infotainment systems, and advanced driver assistance systems (ADAS). These systems are often subjected to harsh environmental conditions, including high temperatures under the hood or in direct sunlight.
High TG PCBs provide the necessary thermal stability and reliability to ensure that these critical automotive electronic components function properly and safely, even in demanding conditions.
Industrial Equipment
Industrial equipment, such as power supplies, motor drives, and control systems, often operates in high-temperature environments. These devices also generate significant heat during operation, which can put stress on the PCBs inside.
By using high TG PCBs, industrial equipment manufacturers can create more durable and reliable products that can withstand the rigors of industrial environments. This translates to reduced downtime, lower maintenance costs, and improved overall system performance.
Aerospace and Defense
The aerospace and defense industries have stringent requirements for electronic components, as these devices must operate reliably in extreme conditions. High TG PCBs are often used in aerospace and defense applications due to their superior thermal stability and resistance to environmental stresses.
Examples of aerospace and defense applications that benefit from high TG PCBs include:
- Avionics systems
- Radar and communication equipment
- Satellite components
- Military-grade computers and electronics
High-Power LED Lighting
High-power LED lighting systems generate significant amounts of heat during operation, which can cause thermal stress on the PCBs that control and power the LEDs. High TG PCBs are well-suited for these applications, as they can withstand the elevated temperatures without experiencing thermal damage or delamination.
By using high TG PCBs, LED lighting manufacturers can create more reliable and long-lasting products, reducing the need for frequent replacements and maintenance.
Designing with High TG PCBs
Material Selection
When designing a PCB that requires high thermal stability, it is essential to select the appropriate high TG material. There are various high TG FR-4 laminates available, each with slightly different properties and glass transition temperatures.
Some common high TG FR-4 laminates include:
- Isola PCL370HR (TG: 180°C)
- Nelco N4000-13 SI (TG: 175°C)
- Ventec VT-481 (TG: 170°C)
It is important to consult with your PCB manufacturer and material supplier to determine the best high TG material for your specific application and design requirements.
Thermal Management Considerations
While high TG PCBs offer enhanced thermal stability, it is still crucial to implement proper thermal management techniques in your PCB design. This includes:
- Optimizing component placement to evenly distribute heat
- Using thermal vias to transfer heat from hot components to the opposite side of the PCB
- Incorporating heat sinks or other cooling solutions when necessary
- Selecting components with appropriate power ratings and temperature specifications
By combining the use of high TG PCBs with effective thermal management strategies, designers can create highly reliable and thermally stable electronic devices.
FAQ
-
Are high TG PCBs more expensive than standard FR-4 PCBs?
Yes, high TG PCBs typically cost more than standard FR-4 PCBs due to the specialized materials and manufacturing processes required. However, the increased cost is often justified by the improved thermal stability and reliability offered by high TG PCBs. -
Can high TG PCBs be used for multilayer designs?
Yes, high TG PCBs can be used for multilayer designs. In fact, many high-temperature applications require multilayer PCBs to accommodate complex circuitry and interconnections. The enhanced thermal stability of high TG materials makes them well-suited for multilayer designs in demanding environments. -
Are there any limitations to using high TG PCBs?
While high TG PCBs offer numerous benefits, there are a few limitations to consider. One potential limitation is the increased brittleness of high TG materials compared to standard FR-4. This can make high TG PCBs more susceptible to mechanical stress or impact damage. Additionally, high TG materials may have slightly different dielectric properties, which should be accounted for during the design process. -
How do I specify the need for a high TG PCB when ordering from a manufacturer?
When ordering high TG PCBs from a manufacturer, it is important to clearly specify your requirements in terms of the glass transition temperature (TG) and any other relevant material properties. Most PCB manufacturers will have a range of high TG materials available and can guide you in selecting the most appropriate option for your application. -
Can high TG PCBs be used in conjunction with other thermal management techniques?
Yes, high TG PCBs can and should be used in conjunction with other thermal management techniques to ensure optimal performance and reliability. This includes proper component placement, the use of thermal vias, heat sinks, and other cooling solutions as needed. By combining high TG materials with effective thermal management strategies, designers can create robust and reliable electronic devices that can withstand even the most demanding environments.
Conclusion
High TG PCBs have emerged as a valuable solution for applications that require enhanced thermal stability and reliability. By utilizing specialized materials with higher glass transition temperatures, these PCBs can withstand elevated temperatures and thermal stresses without compromising their structural integrity.
From automotive electronics and industrial equipment to aerospace and defense applications, high TG PCBs have proven their worth in a wide range of industries. As technology continues to advance and the demand for reliable, high-performance electronic devices grows, the use of high TG PCBs is likely to become even more widespread.
When designing with high TG PCBs, it is essential to carefully consider material selection, thermal management strategies, and other design factors to ensure optimal performance and longevity. By working closely with PCB manufacturers and material suppliers, designers can leverage the benefits of high TG PCBs to create innovative and reliable electronic products that push the boundaries of what is possible.
As the electronics industry continues to evolve, high TG PCBs will undoubtedly play a crucial role in enabling the development of next-generation devices that can withstand the challenges of increasingly demanding environments. By understanding the properties, benefits, and applications of high TG PCBs, designers and manufacturers can make informed decisions and stay at the forefront of this exciting and dynamic field.