Characteristics of High Frequency PCBs
1. Material Selection
The choice of substrate material is critical for high frequency PCBs. The most common materials used are:
- Rogers RO4000 series: These materials offer excellent high-frequency performance, low dielectric loss, and good thermal stability.
- PTFE (Polytetrafluoroethylene): PTFE, also known as Teflon, is a popular choice for high-frequency applications due to its low dielectric constant and loss tangent.
- Isola IS680: This material is known for its low dissipation factor and good thermal stability, making it suitable for high-frequency designs.
2. Controlled Impedance
Maintaining controlled impedance is crucial for high frequency PCBs to ensure proper signal integrity and minimize reflections. The characteristic impedance of a transmission line is determined by factors such as the dielectric constant of the substrate, the width of the trace, and the thickness of the dielectric layer.
Common controlled impedance values for high frequency PCBs include:
Impedance (Ω) | Application |
---|---|
50 | RF circuits, coaxial cables |
75 | Video transmission, cable television |
90 | High-speed digital circuits, Ethernet |
100 | Differential signaling, USB, PCIe |
3. Trace Geometry
The geometry of the traces on a high frequency PCB plays a significant role in signal integrity. Some key considerations include:
- Trace width: Narrower traces have higher characteristic impedance and are preferred for high-frequency signals.
- Trace spacing: Adequate spacing between traces helps reduce crosstalk and electromagnetic interference (EMI).
- Trace length matching: Matching the length of traces for critical signals minimizes timing skew and ensures proper signal synchronization.
4. Ground Planes and Shielding
Incorporating ground planes and shielding techniques is essential for high frequency PCBs to minimize EMI and ensure signal integrity. Some common practices include:
- Solid ground planes: Using a solid ground plane provides a low-impedance return path for high-frequency signals and helps reduce EMI.
- Stripline and microstrip: These transmission line structures offer controlled impedance and help contain electromagnetic fields.
- Via stitching: Adding closely spaced vias along the edges of a ground plane creates a Faraday cage, effectively shielding the signals from external interference.
Design Considerations for High Frequency PCBs
1. Signal Integrity Analysis
Performing signal integrity analysis is crucial for high frequency PCB design. This involves simulating and analyzing the behavior of signals on the board, considering factors such as:
- Reflections: Mismatched impedances can cause signal reflections, leading to signal distortion and degradation.
- Crosstalk: Electromagnetic coupling between adjacent traces can cause crosstalk, affecting signal quality.
- Attenuation: High-frequency signals experience attenuation due to dielectric and conductor losses, which must be accounted for in the design.
2. Power Integrity Analysis
Ensuring proper power delivery is critical for high frequency PCBs. Power integrity analysis involves:
- Decoupling capacitors: Placing decoupling capacitors close to power pins of ICs helps minimize power supply noise and maintain signal integrity.
- Power plane segmentation: Splitting power planes for different supply voltages or isolating noisy sections can help reduce interference.
- Voltage drop analysis: Ensuring that the voltage drop across the board is within acceptable limits to maintain proper device operation.
3. Thermal Management
High frequency PCBs often generate significant heat due to the high-speed switching of components. Effective thermal management strategies include:
- Thermal vias: Placing thermal vias near heat-generating components helps transfer heat to the opposite side of the board or to a heatsink.
- Heatsinks and fans: Attaching heatsinks to high-power components and incorporating fans for active cooling can help dissipate heat.
- Material selection: Choosing PCB materials with good thermal conductivity, such as metal-core substrates, can enhance heat dissipation.
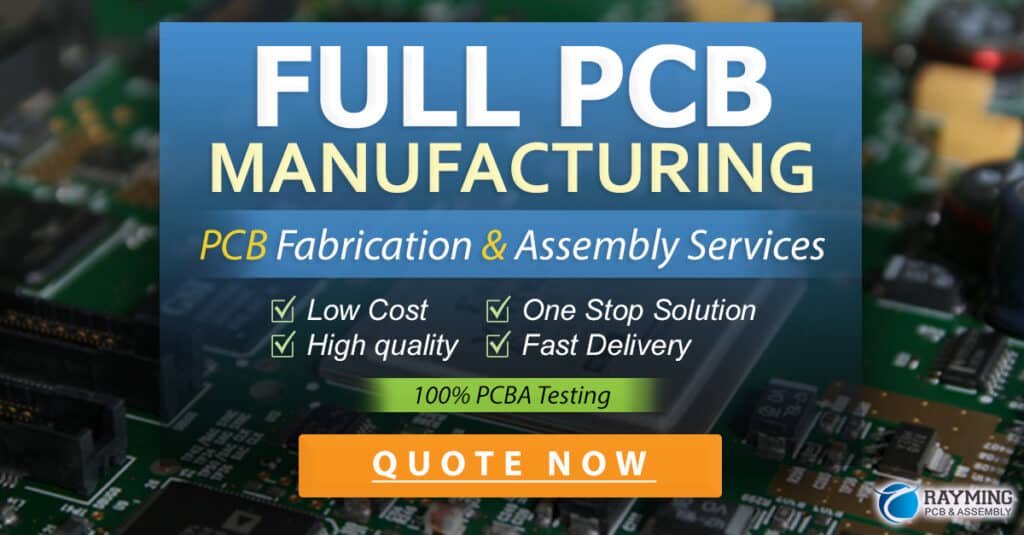
Manufacturing Considerations for High Frequency PCBs
1. Material Handling
High frequency PCB materials require special handling during manufacturing to maintain their integrity. Some key considerations include:
- Moisture control: Materials like PTFE are sensitive to moisture absorption, which can affect their dielectric properties. Proper storage and handling are essential.
- Lamination process: The lamination process for high-frequency materials may require specific temperature and pressure profiles to ensure proper bonding and minimize material stress.
2. Fabrication Techniques
Manufacturing high frequency PCBs demands precise fabrication techniques to achieve the required trace geometries and tolerances. Some common techniques include:
- High-resolution photolithography: Using high-resolution photomasks and advanced etching processes enables the creation of fine-pitch traces and tight tolerances.
- Laser drilling: Laser drilling is often used for creating small, precise vias in high frequency PCBs.
- Controlled depth milling: Milling techniques with depth control are employed to create cavities, steps, and other features on the PCB surface.
3. Quality Control and Testing
Stringent quality control and testing procedures are essential for high frequency PCBs to ensure their performance and reliability. Some key aspects include:
- Impedance testing: Measuring the characteristic impedance of traces to verify that they meet the specified values.
- Time-domain reflectometry (TDR): Using TDR to analyze the impedance profile along a trace and identify discontinuities or reflections.
- X-ray inspection: Employing X-ray imaging to inspect the internal structure of the PCB, checking for voids, delamination, or manufacturing defects.
Applications of High Frequency PCBs
High frequency PCBs find applications in various industries and products, such as:
- Telecommunications:
- 5G networks
- Cellular base stations
-
Satellite communication systems
-
Radar and Sensing:
- Automotive radar systems
- Aerospace and defense radar
-
Medical imaging equipment
-
High-Speed Digital Systems:
- High-performance computing
- Data centers and servers
-
High-speed networking equipment
-
IoT and Wireless Devices:
- Wireless sensors and actuators
- Smart home devices
- Wearable technology
Challenges and Future Trends
Designing and manufacturing high frequency PCBs come with several challenges, including:
- Signal integrity at higher frequencies: As frequencies continue to increase, maintaining signal integrity becomes more challenging due to increased losses and potential for signal distortion.
- Thermal management: Higher operating frequencies lead to increased power dissipation, requiring advanced thermal management solutions.
- Manufacturing complexity: Fabricating high frequency PCBs with tighter tolerances and smaller features demands more sophisticated manufacturing processes and quality control measures.
Future trends in high frequency PCBs include:
- Adoption of advanced materials: Ongoing research into new materials with improved dielectric properties and thermal performance will enable the design of PCBs for even higher frequencies.
- Integration of embedded components: Embedding active and passive components within the PCB substrate can help reduce parasitic effects and improve signal integrity at high frequencies.
- 3D packaging technologies: Utilizing 3D packaging techniques, such as through-silicon vias (TSVs) and package-on-package (PoP), can enable higher-density interconnects and improved high-frequency performance.
Frequently Asked Questions (FAQ)
-
What is the difference between high frequency PCBs and regular PCBs?
High frequency PCBs are designed to operate at frequencies above 500 MHz, while regular PCBs are typically used for lower frequency applications. High frequency PCBs require specialized materials, controlled impedance, and precise trace geometries to ensure proper signal integrity at high frequencies. -
What materials are commonly used for high frequency PCBs?
Common materials used for high frequency PCBs include Rogers RO4000 series, PTFE (Polytetrafluoroethylene), and Isola IS680. These materials offer low dielectric loss, good thermal stability, and suitable dielectric properties for high-frequency operation. -
Why is controlled impedance important for high frequency PCBs?
Controlled impedance is crucial for high frequency PCBs to ensure proper signal integrity and minimize reflections. By matching the characteristic impedance of the traces to the source and load impedances, signal reflections and distortions can be minimized, resulting in better signal quality. -
What are some techniques used for shielding high frequency PCBs?
Techniques used for shielding high frequency PCBs include using solid ground planes, implementing stripline or microstrip transmission line structures, and employing via stitching to create a Faraday cage. These techniques help contain electromagnetic fields and reduce interference. -
How can thermal management be addressed in high frequency PCB design?
Thermal management in high frequency PCB design can be addressed by using thermal vias to transfer heat, attaching heatsinks to high-power components, incorporating fans for active cooling, and selecting PCB materials with good thermal conductivity. Proper thermal management helps dissipate heat generated by high-speed components and ensures reliable operation.