Introduction to IMS PCBs
An Insulated Metal Substrate PCB (IMS PCB), also known as a metal core PCB (MCPCB), is a specialized type of printed circuit board that offers superior thermal performance compared to traditional FR-4 PCBs. IMS PCBs are designed to efficiently dissipate heat generated by electronic components, making them ideal for applications that require high power density or operate in environments with elevated temperatures.
The key feature of an IMS PCB is its multi-layer structure, which typically consists of a metal base layer (usually aluminum), a thin dielectric layer, and a copper circuit layer. This unique construction allows heat to be quickly conducted away from electronic components and dissipated through the metal substrate, preventing overheating and ensuring reliable performance.
Advantages of Using IMS PCBs
1. Enhanced Thermal Management
The primary benefit of using an IMS PCB is its superior thermal management capabilities. The metal substrate, usually made of aluminum, acts as an efficient heat spreader, quickly conducting heat away from electronic components. This helps to maintain lower operating temperatures, increasing the reliability and lifespan of the components and the overall system.
2. Improved Power Handling Capacity
IMS PCBs can handle higher power densities compared to traditional FR-4 PCBs. The metal substrate’s excellent thermal conductivity allows for more efficient heat dissipation, enabling the use of high-power components such as LEDs, power amplifiers, and motor drivers. This makes IMS PCBs well-suited for applications that require high power output, such as automotive electronics, power converters, and LED lighting systems.
3. Reduced Size and Weight
The efficient thermal management properties of IMS PCBs allow for more compact designs. As heat is dissipated more effectively, components can be placed closer together without the risk of overheating. This enables the creation of smaller, more lightweight electronic devices, which is particularly advantageous in space-constrained applications such as consumer electronics and aerospace systems.
4. Cost-Effective Solution
While the initial cost of an IMS PCB may be higher than a standard FR-4 PCB, the long-term cost benefits can be significant. The enhanced thermal performance and increased reliability of IMS PCBs can lead to reduced system failures, lower maintenance costs, and extended product lifetimes. Additionally, the ability to use smaller heat sinks or even eliminate them altogether can result in cost savings in terms of material and assembly expenses.
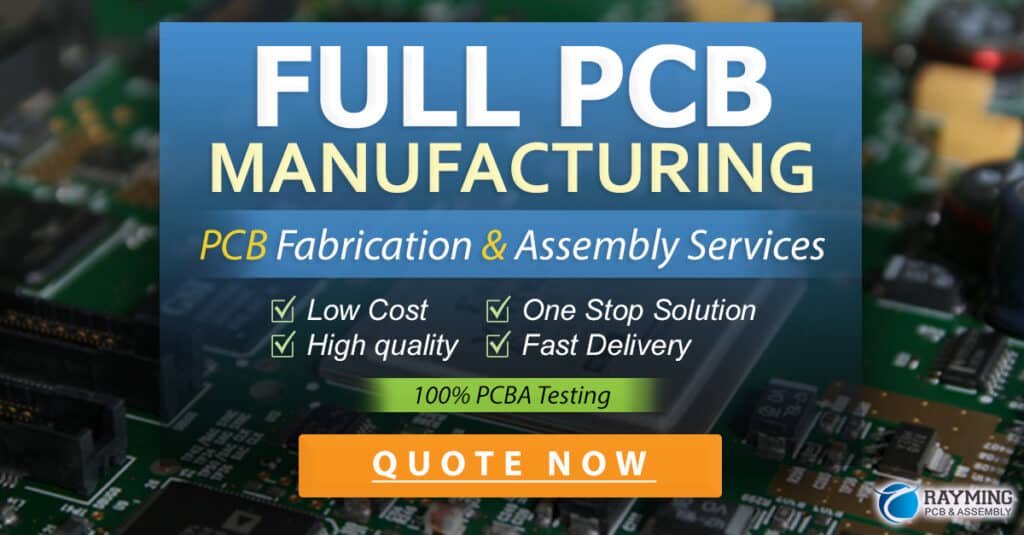
IMS PCB Structure and Materials
1. Metal Base Layer
The metal base layer is the foundation of an IMS PCB and is responsible for its excellent thermal conductivity. Aluminum is the most commonly used material for the metal substrate due to its high thermal conductivity, low weight, and relatively low cost. Other metals, such as copper or brass, may be used in specific applications that require even better thermal performance or different mechanical properties.
2. Dielectric Layer
The dielectric layer is a thin, electrically insulating material that separates the metal base layer from the copper circuit layer. Its primary function is to provide electrical isolation while allowing efficient heat transfer. The dielectric layer is typically made of a thermally conductive material, such as:
-
Alumina (Al2O3): Alumina is a ceramic material with good thermal conductivity and excellent electrical insulation properties. It offers high dielectric strength and is suitable for high-voltage applications.
-
Aluminum Nitride (AlN): Aluminum nitride is another ceramic material with even better thermal conductivity than alumina. It is often used in high-power applications that demand the best possible thermal performance.
-
Epoxy-based thermal interface materials (TIMs): These materials are polymer composites filled with thermally conductive particles, such as boron nitride or aluminum oxide. They offer a balance of good thermal conductivity, electrical insulation, and ease of processing.
3. Copper Circuit Layer
The copper circuit layer is where the electronic components are mounted and interconnected. It is similar to the copper layer in a standard FR-4 PCB, with the same etching and plating processes used to create the desired circuit pattern. The thickness of the copper layer can vary depending on the specific application and power requirements.
IMS PCB Manufacturing Process
The manufacturing process for IMS PCBs is similar to that of standard FR-4 PCBs, with a few key differences to accommodate the unique materials and structure.
-
Substrate Preparation: The aluminum substrate is cleaned and surface-treated to ensure good adhesion with the dielectric layer.
-
Dielectric Layer Application: The dielectric layer, either in the form of a prepreg or a thin film, is laminated onto the aluminum substrate using heat and pressure.
-
Copper Foil Lamination: A copper foil is laminated onto the dielectric layer, again using heat and pressure.
-
Circuit Pattern Etching: The desired circuit pattern is transferred onto the copper layer using photolithography and etching processes.
-
Drilling and Plating: Holes are drilled through the PCB, and the walls of the holes are plated with copper to create electrical connections between layers if required.
-
Surface Finishing: A surface finish, such as HASL, ENIG, or OSP, is applied to protect the exposed copper and provide a solderable surface.
-
Solder Mask Application: A solder mask is applied to protect the copper traces and prevent solder bridges during component assembly.
-
Silkscreen Printing: Component designators, labels, and other markings are printed onto the PCB using silkscreen printing.
-
Singulation: The panel is cut into individual PCBs using routing or punching methods.
Applications of IMS PCBs
IMS PCBs are used in a wide range of industries and applications where thermal management is critical. Some common applications include:
-
LED Lighting: High-power LED modules generate significant amounts of heat, which must be dissipated to ensure optimal performance and longevity. IMS PCBs are widely used in LED lighting applications, from automotive headlights to architectural lighting systems.
-
Automotive Electronics: Modern vehicles incorporate numerous electronic systems that generate heat, such as engine control units, power inverters, and LED lighting. IMS PCBs are used to ensure reliable operation in the harsh automotive environment.
-
Power Electronics: Power converters, motor drives, and other power electronics applications benefit from the enhanced thermal management provided by IMS PCBs. They help to reduce the size and weight of the overall system while ensuring reliable operation.
-
Aerospace and Defense: Aerospace and defense applications often require high-reliability electronics that can operate in extreme temperatures and harsh environments. IMS PCBs are used in avionics, radar systems, and satellite communications equipment.
-
Medical Devices: Medical equipment, such as imaging systems and surgical instruments, requires reliable, high-performance electronics. IMS PCBs are used to ensure proper thermal management and maintain the accuracy and reliability of these critical devices.
-
Industrial Automation: Industrial control systems, sensors, and actuators often operate in high-temperature environments. IMS PCBs help to ensure reliable operation and extend the lifespan of these components.
Frequently Asked Questions (FAQ)
1. What is the difference between an IMS PCB and a standard FR-4 PCB?
The main difference between an IMS PCB and a standard FR-4 PCB lies in their thermal management capabilities. IMS PCBs have a metal substrate, usually aluminum, that provides excellent thermal conductivity, allowing for efficient heat dissipation from electronic components. FR-4 PCBs, on the other hand, are made of a glass-reinforced epoxy laminate, which has poor thermal conductivity. IMS PCBs are used in applications that require superior thermal management, while FR-4 PCBs are suitable for general-purpose electronics.
2. Can IMS PCBs be multilayer?
Yes, IMS PCBs can be designed as multilayer boards. The multilayer structure typically consists of alternating layers of dielectric material and copper, with the metal substrate serving as the base layer. Multilayer IMS PCBs offer the same benefits as single-layer boards, with the added advantage of increased circuit density and more complex routing options.
3. How does the thermal conductivity of an IMS PCB compare to other PCB materials?
The thermal conductivity of an IMS PCB depends on the specific materials used, but in general, they offer significantly better thermal performance than traditional FR-4 PCBs. Here’s a comparison of thermal conductivity values for common PCB materials:
Material | Thermal Conductivity (W/mK) |
---|---|
FR-4 | 0.3 – 0.4 |
Aluminum (IMS PCB substrate) | 150 – 200 |
Copper (IMS PCB substrate) | 400 |
Alumina (Al2O3) dielectric | 20 – 30 |
Aluminum Nitride (AlN) dielectric | 150 – 180 |
As evident from the table, the metal substrates used in IMS PCBs have thermal conductivity values several orders of magnitude higher than FR-4, enabling much more efficient heat dissipation.
4. Are there any limitations or challenges associated with using IMS PCBs?
While IMS PCBs offer many benefits, there are some limitations and challenges to consider:
-
Cost: IMS PCBs are generally more expensive than standard FR-4 PCBs due to the specialized materials and manufacturing processes involved.
-
Design Constraints: The metal substrate in an IMS PCB can affect signal integrity and electromagnetic compatibility (EMC) if not properly designed. Careful layout and grounding techniques are required to minimize these issues.
-
Manufacturing Complexity: The unique structure and materials used in IMS PCBs can make the manufacturing process more complex and require specialized equipment and expertise.
-
Limited Flexibility: The metal substrate in an IMS PCB makes the board less flexible than a standard FR-4 PCB. This can be a limitation in applications that require a degree of mechanical flexibility.
5. How do I select the right IMS PCB for my application?
Selecting the right IMS PCB for your application involves considering several factors:
-
Thermal Requirements: Determine the amount of heat generated by your electronic components and the maximum operating temperature of your system. This will help you select an IMS PCB with the appropriate thermal conductivity and dielectric material.
-
Electrical Requirements: Consider the voltage, current, and frequency requirements of your circuit. Ensure that the dielectric material and copper thickness of the IMS PCB are suitable for your electrical needs.
-
Mechanical Requirements: Assess the physical constraints of your application, such as size, weight, and mounting requirements. Consider the mechanical properties of the metal substrate and dielectric materials when making your selection.
-
Cost and Availability: Evaluate the cost implications of different IMS PCB materials and manufacturers. Consider lead times and minimum order quantities to ensure that your selected IMS PCB is feasible for your project timeline and budget.
-
Manufacturing Capabilities: Verify that your chosen IMS PCB manufacturer has the necessary expertise and equipment to produce your design. Discuss any special requirements or challenges with the manufacturer early in the design process.
By carefully considering these factors and working closely with an experienced IMS PCB manufacturer, you can select the optimal IMS PCB solution for your specific application.
Conclusion
IMS PCBs offer a powerful solution for electronics applications that demand superior thermal management and high power density. By combining a metal substrate with a thin dielectric layer and a copper circuit layer, IMS PCBs enable efficient heat dissipation, improved reliability, and more compact designs. As electronic systems continue to push the boundaries of performance and miniaturization, IMS PCBs will play an increasingly critical role in ensuring their success.
When considering an IMS PCB for your next project, it is essential to carefully evaluate your thermal, electrical, and mechanical requirements. Collaborate closely with an experienced IMS PCB manufacturer to select the most appropriate materials, design, and manufacturing processes for your specific application. With the right approach, IMS PCBs can unlock new levels of performance, reliability, and innovation in a wide range of industries, from automotive and aerospace to medical devices and industrial automation.