Introduction to 2 Layer PCBs
A two layer PCB, also known as a double-sided PCB or 2 layer printed circuit board, is a type of PCB that has conductive copper layers on both sides of the board substrate. The copper layers are used for interconnecting electronic components through conductive tracks, pads, and other features etched from copper sheets laminated onto a non-conductive substrate.
Advantages of 2 Layer PCBs vs Single Layer
Two layer PCBs offer several advantages over single layer pcbs:
Advantage | 2 Layer PCB | 1 Layer PCB |
---|---|---|
Component Density | High | Low |
Routing Flexibility | High | Limited |
Cost | Moderate | Low |
Durability | High | Moderate |
The additional copper layer allows for a higher density of components and traces compared to single layer boards. This makes 2 layer PCBs ideal for more complex circuits and applications where space is limited.
Having copper layers on both sides also provides much more flexibility in how traces can be routed between components. Traces can cross over each other using vias to connect the top and bottom layers. Single layer boards are restricted to single-sided routing.
While 2 layer PCBs cost more to manufacture than single layer, the improved density and routing flexibility makes them a cost-effective choice for many electronic products. The additional copper layer also makes the board more durable and resistant to damage.
How 2 Layer PCBs are Manufactured
The manufacturing process for a 2 layer PCB involves the following key steps:
-
Substrate Selection: A dielectric substrate material, typically FR-4 glass epoxy, is selected based on the required thickness, rigidity, and thermal properties for the application.
-
Copper Foil Lamination: Thin sheets of copper foil are laminated onto both sides of the substrate using heat and pressure. The standard copper thickness for outer layers is 1 oz (35 μm).
-
Drilling: Holes are drilled through the board for mounting through-hole components and vias that interconnect the top and bottom copper layers. High-speed CNC machines are used for precise drilling.
-
Electroless Copper Deposition: The drilled board is chemically treated to deposit a thin layer of copper onto the hole walls to provide electrical conductivity between the top and bottom layers through the vias.
-
Resist Pattern Imaging: The circuit pattern is transferred onto the copper layers using photoresist and exposure to UV light. The photoresist hardens where exposed, protecting the copper that will form the traces.
-
Etching: The board is exposed to a chemical etchant that removes the unprotected copper, leaving only the desired traces and pads. The hardened photoresist is then stripped away.
-
Soldermask Application: A layer of polymer soldermask is applied to the outer layers, exposing only the pads and other areas requiring soldering. This protects the traces from oxidation and prevents solder bridges.
-
Silkscreen: White silkscreen text is printed onto the component side to label components, test points, and other features for easier assembly and troubleshooting.
-
Surface Finish: The exposed pads are plated with a surface finish, typically hot air solder leveling (HASL), electroless nickel immersion gold (ENIG), or organic solderability preservatives (OSP) to prevent oxidation and enhance solderability.
-
Electrical Test: The completed board undergoes electrical testing, such as flying probe or bed of nails tests, to verify continuity and check for short circuits before the components are assembled.
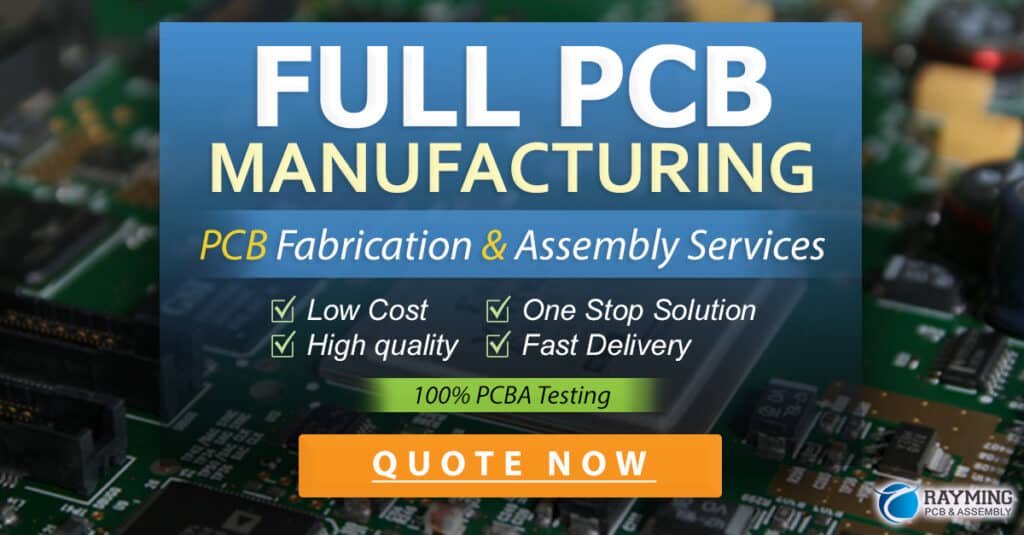
Designing a 2 Layer PCB Layout
Schematic Capture
The first step in designing a 2 layer PCB is capturing the schematic diagram of the circuit. This involves specifying the components and defining the electrical connections between them using schematic capture software such as OrCAD Capture or KiCad Eeschema.
Component Placement
With the netlist exported from the schematic, components are placed onto the board outline in the PCB layout software. Key considerations for component placement on a 2 layer PCB include:
- Placing components to minimize trace lengths and complexity
- Grouping related components together for easier routing
- Providing adequate clearance between components for assembly
- Orienting components to simplify soldering and inspection
- Placing decoupling capacitors close to IC power pins
Trace Routing
After components are placed, traces are routed to interconnect the components according to the netlist. On a 2 layer board, traces are routed on both the top and bottom layers. Some guidelines for routing traces include:
- Using an appropriate trace width based on the required current carrying capacity
- Providing adequate clearance between traces to prevent short circuits
- Avoiding sharp corners that could cause acid traps during manufacturing
- Routing power traces wider than signal traces
- Minimizing vias and layer changes where possible to reduce manufacturing cost
- Following controlled impedance guidelines for high-speed signals
Plane Layers
While 2 layer PCBs do not have dedicated plane layers, copper fills are often used to provide power distribution and reduce EMI. Some tips for using copper fills on 2 layer boards:
- Create a solid fill for ground on the bottom layer and stitch to the top with vias
- Provide a sufficiently wide trace or fill for power distribution on the top layer
- Separate analog and digital grounds to reduce noise coupling
- Provide a continuous ground fill under high-speed signals for impedance control
Design Rule Check (DRC)
Before sending the design for manufacturing, a design rule check (DRC) should be performed using the PCB layout software. This automated check verifies that the design meets the specified manufacturing constraints such as minimum trace width, clearance, and hole size. Completing a DRC ensures the design is manufacturable and helps avoid costly delays and rework.
2 Layer PCB Stackup
The stackup of a 2 layer PCB consists of the following layers:
Layer | Material | Thickness (mm) |
---|---|---|
Top Soldermask | Polymer film | 0.025 |
Top Copper | 1 oz (35 μm) Copper | 0.035 |
Core | FR-4 Glass Epoxy | 1.6 |
Bottom Copper | 1 oz (35 μm) Copper | 0.035 |
Bottom Soldermask | Polymer film | 0.025 |
The standard thickness for a 2 layer PCB is 1.6 mm, but thinner options down to 0.8 mm and thicker options up to 3.2 mm are available for applications with specific requirements for weight or rigidity.
For high-speed designs or impedance controlled applications, the thickness of the FR-4 core can be adjusted to achieve the desired characteristic impedance of the traces. Thinner cores provide higher impedance while thicker cores provide lower impedance.
2 Layer PCB Applications
Two layer PCBs are used in a wide range of electronic products across many industries. Some common applications include:
- Consumer electronics such as smartphones, tablets, digital cameras, and wearables
- Home appliances like coffee makers, microwave ovens, and washing machines
- Industrial controls for sensors, actuators, motors, and power supplies
- Medical devices such as blood glucose meters, pulse oximeters, and hearing aids
- Automotive electronics including infotainment systems, LED lighting, and electronic control units (ECUs)
- IoT devices like smart thermostats, security cameras, and wireless sensors
- LED lighting for residential, commercial, and industrial luminaires
Two layer boards provide an economical solution for many of these applications where the circuit complexity and density requirements can be met without needing additional layers. However, more complex designs may require 4 layer or higher multilayer PCBs.
2 Layer PCB Assembly
Assembling components onto a 2 layer PCB can be done manually for prototypes and low volumes or using automated assembly processes for higher volumes. The key steps in PCB assembly include:
-
Solder Paste Printing: Solder paste is applied to the pads on the PCB using a stencil or screen. The paste contains small spheres of solder suspended in flux.
-
Pick and Place: Surface mount (SMT) components are picked up from reels or trays and placed onto the solder paste using a pick and place machine. Smaller boards may be assembled manually.
-
Reflow Soldering: The board is heated in a reflow oven, melting the solder paste to form a permanent connection between the components and pads.
-
Through-Hole Assembly: Any through-hole components are inserted manually into the drilled holes and soldered from the opposite side using a wave soldering machine or hand soldering iron.
-
Inspection and Test: The assembled board is visually inspected and electrically tested to ensure proper connections and functionality before further integration or packaging.
Proper care must be taken during the assembly process to avoid common defects such as:
- Tombstoning: One end of a component lifts off the pad due to uneven heating
- Bridging: Solder bridges form between adjacent pads, causing a short circuit
- Cold joints: Insufficient heat or contamination prevents solder from bonding to the pad or lead
- Misalignment: Components are placed inaccurately, not centered on the pads
Following the recommended reflow profile and using a solder paste with the appropriate particle size and flux activity can help mitigate these issues and ensure a reliable assembly.
Frequently Asked Questions (FAQ)
- What is the difference between a 2 layer and 4 layer PCB?
A 2 layer PCB has copper layers on the top and bottom sides of the board, while a 4 layer PCB has two additional inner layers. 4 layer boards can accommodate more complex circuits with higher component density and provide dedicated power and ground planes for improved signal integrity.
- How much does a 2 layer PCB cost?
The cost of a 2 layer PCB depends on several factors such as the board size, quantity, materials, and surface finish. Typical prices can range from $0.10 to $1.00 per square inch in volumes of 1000 pieces or more. Smaller quantities will have a higher unit cost.
- What is the maximum size of a 2 layer PCB?
The maximum size of a 2 layer PCB is limited by the manufacturing equipment and handling capabilities of the pcb fabricator. Most manufacturers can produce 2 layer boards up to 18″ x 24″ (457 mm x 610 mm), but larger sizes may be possible with specialized equipment.
- How small can traces be on a 2 layer PCB?
The minimum trace width and spacing on a 2 layer PCB depends on the capabilities of the PCB manufacturer. Typical minimum trace widths are 0.006″ (0.15 mm) for inner layers and 0.004″ (0.10 mm) for outer layers. Smaller traces may be possible with advanced manufacturing processes.
- Can 2 layer PCBs be used for high-speed designs?
While 2 layer PCBs can be used for some high-speed designs, they have limitations compared to multilayer boards. The lack of dedicated plane layers for power and ground can result in higher noise and crosstalk. Impedance control is also more challenging with 2 layer stackups. 4 layer or higher boards are recommended for most high-speed applications above 1 GHz.
Conclusion
Two layer PCBs are a versatile and cost-effective solution for a wide range of electronic applications. By providing conductive layers on both sides of the board, they offer higher component density and routing flexibility compared to single layer designs.
When designing a 2 layer PCB, careful consideration must be given to component placement, trace routing, and manufacturability. Following best practices and performing a thorough design rule check (DRC) can help ensure a successful manufacturing outcome.
While 2 layer boards have some limitations for high-speed and complex designs, they remain a popular choice for many consumer, industrial, and IoT products where performance and cost requirements can be met without the need for additional layers.
As PCB manufacturing capabilities continue to advance, the density and performance of 2 layer designs will further improve, making them an even more attractive option for future electronic products.