Introduction to Annular Rings in PCB Design
In printed circuit board (PCB) design, an annular ring refers to the copper pad that surrounds a drilled hole or via. The annular ring serves several important purposes in PCB manufacturing and assembly. It provides mechanical support for component leads, allows for proper soldering, and ensures electrical connectivity between layers of a multi-layer board.
Key Functions of Annular Rings
The main functions of annular rings in PCB design include:
- Mechanical support for component leads
- Allowing for proper soldering
- Ensuring electrical connectivity between layers
- Meeting manufacturing tolerances
- Improving reliability and durability
Annular rings are a critical aspect of PCB design that impacts the manufacturability, reliability, and functionality of the final board. Understanding the role and requirements for annular rings is essential for creating robust PCB designs.
Mechanical Support for Component Leads
One of the primary purposes of annular rings is to provide mechanical support for the leads of through-hole components. When a component is inserted into a drilled hole on the PCB, the annular ring helps to hold it in place and prevent it from shifting or falling out during soldering and assembly.
Annular Ring Size and Lead Diameter
The size of the annular ring relative to the lead diameter is an important consideration. The ring should be large enough to allow the lead to pass through easily while still providing sufficient contact area for soldering.
Typical guidelines for annular ring size based on lead diameter are:
Lead Diameter | Minimum Annular Ring |
---|---|
≤ 0.8 mm | 0.1 mm |
0.8 – 1.5 mm | 0.15 mm |
1.5 – 2.5 mm | 0.2 mm |
> 2.5 mm | 0.25 mm |
Oversizing the annular ring too much can make soldering more difficult by creating a large thermal mass that makes it harder for the solder to flow properly. Conversely, undersizing the ring may not provide enough mechanical support or contact area.
Plated Through Holes (PTHs)
For plated through holes (PTHs) that provide electrical connectivity between layers, the annular ring also helps to anchor the hole plating and prevent it from detaching or flaking off. This is especially important in multilayer boards where the hole plating is the only path for current to flow between certain layers.
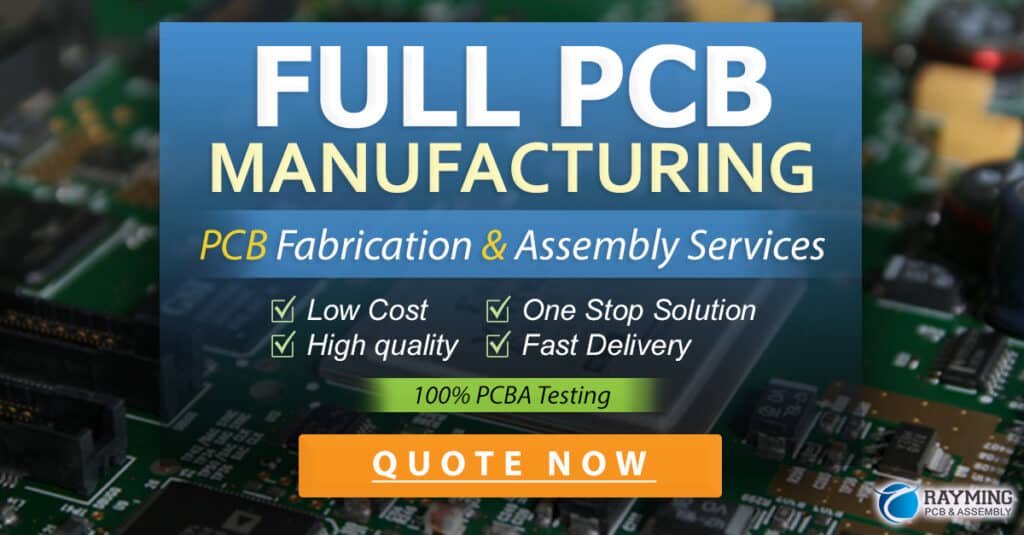
Allowing for Proper Soldering
Annular rings play a key role in allowing for proper soldering of through-hole components. The ring provides a surface for the molten solder to wet and adhere to, creating a strong mechanical and electrical bond between the component lead and the copper pad.
Solderability and Wetting
For good solderability, the annular ring needs to have a clean, oxide-free surface that allows the molten solder to flow and wet properly. Factors that can negatively impact solderability include:
- Surface contamination or oxidation
- Rough or pitted surfaces
- Improperly sized holes or rings
Ensuring the annular rings are properly designed and fabricated is critical for achieving reliable solder joints. Insufficient wetting can lead to weak joints that may crack or fail over time.
Thermal Relief Patterns
In some cases, large annular rings or copper pour areas can create a heat sink effect that makes it difficult for the soldering iron to bring the joint up to the necessary temperature for proper fusion. To mitigate this, thermal relief patterns may be used.
Thermal reliefs are small traces or spokes that connect the annular ring to the surrounding copper pour while limiting the direct contact area. This allows heat to flow more readily into the joint area for better wetting.
Ensuring Electrical Connectivity
In addition to their mechanical functions, annular rings are also critical for ensuring proper electrical connectivity in multilayer PCBs. The annular ring around a PTH provides a conductive path that allows current to flow between the different copper layers of the board.
Annular Rings and Multilayer Stackup
In a typical 4-layer PCB stackup, the annular rings on the outer layers will connect to the top and bottom copper layers, while the rings on the inner layers connect the two internal layers. For proper connectivity, it’s important that the annular rings on each layer are properly aligned and make good contact with the hole plating.
Misalignment or poor contact can lead to open circuits or high-resistance connections that may impede signal integrity or even prevent the circuit from functioning altogether. Careful control of layer registration and hole plating processes is necessary to avoid these issues.
Microvias and Blind/Buried Vias
Advances in PCB manufacturing have led to increasing use of microvias and blind/buried vias which connect only certain layers of the board, rather than passing all the way through like traditional PTHs. The annular rings for these vias follow the same basic principles but may have additional restrictions in terms of size and spacing due to the smaller geometries involved.
High-density interconnect (HDI) PCB designs make extensive use of microvias to achieve high routing density and signal integrity. The design and fabrication of microvia annular rings requires tighter tolerances and more precise control compared to traditional PTHs.
Meeting Manufacturing Tolerances
For an annular ring to fulfill its mechanical and electrical functions, it must be fabricated within certain tolerances for size, shape, and position relative to the drilled hole. Deviations from these tolerances can lead to issues with component fit, solderability, and reliability.
Annular Ring Tolerances
The key dimensions that define an annular ring are the inner diameter (ID) which is determined by the hole size, and the outer diameter (OD) which determines the ring width. The difference between the OD and ID is referred to as the annular ring size.
Typical tolerances for annular ring dimensions are:
Dimension | Tolerance |
---|---|
Hole Size | ± 0.1 mm |
Annular Ring Size | ± 0.05 mm |
Hole-to-Hole Pitch | ± 0.1 mm |
Meeting these tolerances requires careful control of the drilling and plating processes used in PCB fabrication. Factors such as drill bit wear, plating thickness variation, and material stability can all impact the final dimensions.
Breakout and Spacing Requirements
In addition to size tolerances, annular rings also have requirements for breakout and spacing. Breakout refers to the minimum distance between the edge of the annular ring and the edge of the copper pour or plane. Sufficient breakout is necessary to prevent the drill from clipping the pour which can create electrical shorts or weaken the mechanical structure.
Spacing requirements dictate the minimum distance between adjacent annular rings or other copper features. Adequate spacing is needed to prevent unintended electrical coupling or bridging, especially for high-voltage or high-frequency signals.
Breakout and spacing requirements vary depending on the PCB manufacturing class and the specific design requirements. As a general rule, tighter tolerances and smaller features will require more precise control and may incur higher fabrication costs.
Improving Reliability and Durability
Finally, properly designed and fabricated annular rings can contribute to the overall reliability and durability of the PCB. Robust annular rings help to ensure the mechanical and electrical integrity of the board over its intended lifetime, even in harsh environmental conditions.
Thermal Cycling and Expansion Mismatch
One of the key reliability challenges for PCBs is thermal cycling, where the board undergoes repeated heating and cooling during operation. This can lead to mechanical stresses due to the difference in thermal expansion coefficients between the PCB material, copper features, and component leads.
Annular rings can help to mitigate these stresses by providing a buffer zone around the hole that allows for some degree of movement and flexibility. The larger the annular ring, the more compliance it can provide to accommodate thermal expansion mismatches.
Vibration and Mechanical Shock
Another reliability concern is vibration and mechanical shock, which can cause components to become dislodged or solder joints to crack and fail. Robust annular rings with sufficient size and copper thickness can help to anchor components securely and prevent them from working loose over time.
In high-reliability applications such as aerospace or military equipment, additional measures such as strain relief or underfill may be used in conjunction with annular rings to provide even greater mechanical reinforcement.
Copper Thickness and Plating Quality
The durability of annular rings is also dependent on the copper thickness and plating quality. Thicker copper provides greater mechanical strength and current-carrying capacity, while high-quality plating ensures a strong, defect-free bond between the copper layers.
Typical copper thicknesses for annular rings range from 0.5 oz to 2 oz (18 to 70 μm), depending on the current requirements and mechanical stresses involved. Higher copper weights may be used in power electronics or high-reliability applications.
Plating quality is influenced by factors such as the plating chemistry, current density, and process control. Proper control of these variables is necessary to achieve a dense, uniform, and adherent plating layer that will hold up over the life of the product.
FAQ
What is the minimum annular ring size for a given hole diameter?
The minimum annular ring size depends on the lead diameter of the component being used. As a general guideline, the annular ring should be at least 0.1 mm larger than the lead diameter for small components (≤ 0.8 mm), and up to 0.25 mm larger for larger components (> 2.5 mm).
How do I calculate the annular ring dimensions for my PCB design?
To calculate the annular ring dimensions, you need to know the hole diameter and the desired annular ring size. The inner diameter (ID) of the ring is equal to the hole diameter, while the outer diameter (OD) is equal to the hole diameter plus twice the annular ring size.
For example, for a 0.8 mm hole with a 0.15 mm annular ring:
– ID = 0.8 mm
– OD = 0.8 mm + (2 x 0.15 mm) = 1.1 mm
What is breakout and why is it important?
Breakout refers to the minimum distance between the edge of the annular ring and the edge of the copper pour or plane. Sufficient breakout is necessary to prevent the drill from clipping the pour, which can create electrical shorts or weaken the mechanical structure. The amount of breakout required depends on the PCB manufacturing class and the specific design requirements.
Can I use different annular ring sizes for different components on the same PCB?
Yes, it’s common to use different annular ring sizes for different types of components on the same PCB. The size of the annular ring should be optimized based on the lead diameter and soldering requirements of each component. However, it’s important to ensure that the annular rings are properly sized and spaced to meet the manufacturing tolerances and design rules for the specific PCB fabrication process being used.
How do I ensure proper solderability of my annular rings?
To ensure proper solderability, the annular rings should have a clean, oxide-free surface that allows the molten solder to flow and wet properly. This can be achieved through proper surface preparation and storage prior to soldering.
Additionally, the size and shape of the annular rings should be designed to provide sufficient contact area and thermal mass for good solder wetting, without being so large as to create a heat sink effect. In some cases, thermal relief patterns may be used to improve solderability of large annular rings or copper pour areas.
Conclusion
Annular rings are a critical aspect of PCB design that serve multiple functions, including mechanical support, solderability, electrical connectivity, manufacturability, and reliability. By understanding the key requirements and best practices for annular ring design, PCB designers can create more robust and manufacturing-friendly layouts that meet the specific needs of their application.
While the specific dimensions and tolerances may vary depending on the PCB fabrication process and design requirements, the basic principles of annular ring design remain the same. Careful attention to annular ring size, shape, and spacing can help to ensure a successful PCB design that performs reliably over its intended lifetime.
As PCB technology continues to evolve with smaller features and higher densities, the importance of proper annular ring design will only continue to grow. By staying up-to-date with the latest guidelines and best practices, PCB designers can create cutting-edge designs that push the boundaries of what is possible while still maintaining high quality and reliability.