Understanding PCB Impedance
Printed Circuit Board (PCB) impedance is a critical factor in the design and performance of high-speed electronic circuits. It refers to the opposition to the flow of alternating current (AC) in a PCB trace, which is a combination of resistance, capacitance, and inductance. Accurate calculation of PCB impedance is essential to ensure proper signal integrity, minimize signal reflections, and maintain the desired characteristic impedance of the transmission line.
What is PCB Impedance?
PCB impedance is the measure of the total opposition to the flow of alternating current in a PCB trace. It is a complex quantity that includes both resistance and reactance (capacitance and inductance). The impedance of a PCB trace depends on various factors, such as the trace width, thickness, spacing, dielectric constant of the substrate material, and the frequency of the signal.
Why is PCB Impedance Important?
Maintaining the correct PCB impedance is crucial for several reasons:
-
Signal Integrity: Proper impedance matching ensures that the signal transmitted through the PCB trace reaches its destination without significant distortion or loss of quality.
-
Reflection Reduction: When there is an impedance mismatch between the source, trace, and load, signal reflections occur, leading to signal degradation and potential errors in data transmission.
-
Electromagnetic Compatibility (EMC): Controlling PCB impedance helps minimize electromagnetic interference (EMI) and reduces the risk of signal crosstalk between adjacent traces.
-
High-Speed Performance: As signal frequencies increase, the impact of PCB impedance becomes more pronounced. Maintaining the correct impedance is essential for high-speed applications to prevent signal integrity issues and ensure reliable performance.
Factors Affecting PCB Impedance
Several factors influence the impedance of a PCB trace:
- Trace Geometry:
- Width: The wider the trace, the lower the impedance.
- Thickness: Thicker traces have lower impedance compared to thinner traces.
-
Length: Longer traces have higher impedance than shorter traces.
-
Substrate Properties:
- Dielectric Constant (Dk): The dielectric constant of the substrate material affects the capacitance of the trace. A higher Dk value results in lower impedance.
-
Substrate Thickness: The thickness of the substrate between the trace and the reference plane impacts the impedance. Thicker substrates increase the impedance.
-
Trace Spacing:
- Trace-to-Trace Spacing: The spacing between adjacent traces affects the coupling capacitance and inductance, impacting the impedance.
-
Trace-to-Plane Spacing: The distance between the trace and the reference plane (ground or power plane) influences the impedance.
-
Signal Frequency:
- As the frequency of the signal increases, the impact of capacitance and inductance becomes more significant, affecting the overall impedance of the trace.
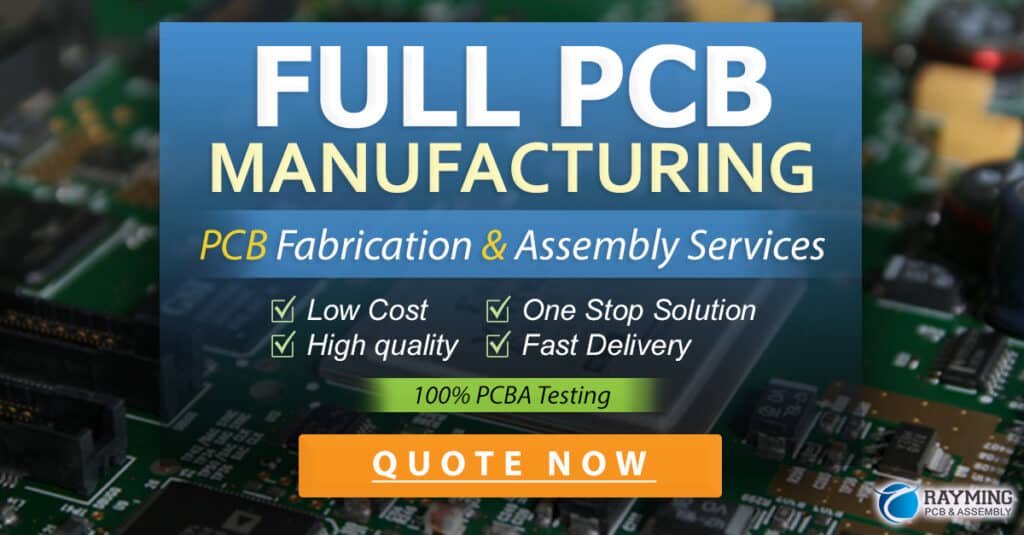
Calculating PCB Impedance
To calculate the impedance of a PCB trace, you can use various methods and tools, including impedance calculators and simulation software. Here are a few common methods:
1. Characteristic Impedance Formula
The characteristic impedance (Z0) of a PCB trace can be calculated using the following formula:
Z0 = (87 / √(ɛr + 1.41)) * ln(5.98 * h / (0.8 * w + t))
Where:
– ɛr = Dielectric constant of the substrate material
– h = Substrate thickness (mm)
– w = Trace width (mm)
– t = Trace thickness (mm)
This formula assumes a microstrip trace configuration, where the trace is on the top layer of the PCB, and there is a ground plane beneath it.
2. Online Impedance Calculators
There are various online impedance calculators available that simplify the process of calculating PCB impedance. These calculators typically require you to input the trace geometry, substrate properties, and desired impedance, and they provide the necessary trace dimensions to achieve the target impedance.
Some popular online impedance calculators include:
3. Simulation Software
For more accurate and comprehensive impedance analysis, you can use simulation software tools. These tools take into account the complex interactions between traces, substrate, and other components, providing a more detailed and reliable impedance calculation.
Some widely used simulation software for PCB impedance analysis include:
- Ansys HFSS (High-Frequency Structure Simulator)
- Keysight ADS (Advanced Design System)
- Mentor Graphics HyperLynx
These software tools offer advanced features like 3D electromagnetic simulation, multi-layer PCB analysis, and the ability to simulate the impact of signal rise time and frequency on impedance.
Impedance Control Techniques
To achieve the desired impedance in a PCB design, several techniques can be employed:
-
Trace Width Adjustment: By varying the width of the trace, you can control its impedance. Wider traces have lower impedance, while narrower traces have higher impedance.
-
Dielectric Thickness: Adjusting the thickness of the substrate between the trace and the reference plane can impact the impedance. Increasing the substrate thickness leads to higher impedance.
-
Dielectric Material Selection: Choosing a substrate material with the appropriate dielectric constant (Dk) can help achieve the desired impedance. Materials with higher Dk values result in lower impedance.
-
Differential Pair Routing: When routing differential pairs, maintaining symmetry and equal length between the traces is crucial for impedance matching and signal integrity.
-
Reference Plane Placement: Proper placement of reference planes (ground or power) near the signal traces helps control impedance and minimize signal distortion.
-
Termination Techniques: Implementing appropriate termination techniques, such as series termination or parallel termination, can help match the impedance of the source and load to the trace impedance, reducing reflections.
Impedance Measurement
After fabricating the PCB, it is essential to verify the actual impedance of the traces to ensure they meet the desired specifications. Impedance measurement can be performed using specialized equipment called Time Domain Reflectometers (TDRs) or Vector Network Analyzers (VNAs).
TDRs measure the impedance by sending a fast-rising pulse through the trace and analyzing the reflected waveform. By measuring the amplitude and timing of the reflections, the impedance profile of the trace can be determined.
VNAs, on the other hand, measure the impedance by sweeping a range of frequencies and analyzing the S-parameters (scattering parameters) of the trace. VNAs provide more detailed information about the impedance behavior across different frequencies.
PCB Impedance Design Considerations
When designing PCBs with controlled impedance, consider the following guidelines:
-
Define the target impedance based on the system requirements, such as the desired characteristic impedance (e.g., 50 ohms, 75 ohms) and the frequency range of operation.
-
Choose an appropriate substrate material with the desired dielectric constant (Dk) and dissipation factor (Df) to achieve the required impedance.
-
Use impedance calculators or simulation tools to determine the trace geometry (width, thickness, and spacing) that yields the target impedance.
-
Follow good PCB layout practices, such as minimizing trace lengths, avoiding sharp bends, and maintaining consistent trace widths and spacings.
-
Consider the impact of vias on impedance. Vias can introduce discontinuities and affect the impedance of the trace. Use via optimization techniques, such as via stitching or back-drilling, to minimize their impact.
-
Perform impedance simulations and analysis to verify the design before fabrication. Simulation tools can help identify potential impedance mismatches and optimize the design accordingly.
-
Specify the impedance requirements clearly in the PCB fabrication files and communicate them to the manufacturer. Provide necessary information, such as the target impedance, trace geometry, and substrate specifications.
-
Conduct impedance measurements on the fabricated PCB to validate the actual impedance values and ensure they meet the specified tolerances.
Frequently Asked Questions (FAQ)
- What is the difference between characteristic impedance and differential impedance?
-
Characteristic impedance (Z0) refers to the impedance of a single-ended trace with respect to a reference plane, such as a ground plane. It is the ratio of the voltage to the current in a transmission line. Differential impedance, on the other hand, is the impedance between two traces in a differential pair. It is the ratio of the voltage difference between the two traces to the current flowing through them.
-
How does the dielectric constant affect PCB impedance?
-
The dielectric constant (Dk) of the substrate material directly impacts the capacitance of the trace, which in turn affects the impedance. A higher Dk value results in higher capacitance and lower impedance. Conversely, a lower Dk value leads to lower capacitance and higher impedance. The choice of substrate material with the appropriate Dk is crucial for achieving the desired impedance.
-
What is the impact of trace thickness on PCB impedance?
-
Trace thickness has an inverse relationship with impedance. As the trace thickness increases, the impedance decreases. Thicker traces have lower resistance and higher capacitance, resulting in lower impedance. However, increasing the trace thickness also affects the manufacturing process and the overall PCB thickness. It is important to strike a balance between the desired impedance and the manufacturing constraints.
-
How can I control impedance in a multi-layer PCB?
-
Controlling impedance in a multi-layer PCB involves careful design and layer stack-up planning. Some techniques include:
- Using dedicated signal layers and ground planes to create controlled impedance environments.
- Adjusting the dielectric thickness between layers to achieve the desired impedance.
- Employing differential pair routing techniques to maintain consistent impedance for differential signals.
- Using simulation tools to analyze the impedance behavior of multi-layer structures and optimize the design accordingly.
-
What are the common impedance values used in PCB design?
- The most common impedance values used in PCB design are 50 ohms and 75 ohms. These values are widely used in various applications, such as:
- 50 ohms: Commonly used in digital systems, high-speed communication interfaces (e.g., USB, HDMI), and RF circuits.
- 75 ohms: Commonly used in video and cable television (CATV) applications, as well as in some analog and RF circuits.
- Other impedance values, such as 28 ohms, 100 ohms, or 110 ohms, may be used in specific applications or standards.
Conclusion
Calculating and controlling PCB impedance is a critical aspect of high-speed PCB design. It ensures signal integrity, minimizes reflections, and maintains the desired characteristic impedance of the transmission lines. By understanding the factors that affect PCB impedance, such as trace geometry, substrate properties, and signal frequency, designers can make informed decisions to achieve the target impedance.
Using impedance calculators, simulation tools, and following good PCB layout practices, designers can effectively design and optimize PCBs for controlled impedance. Impedance measurement techniques, such as TDR and VNA, help validate the actual impedance values and ensure they meet the specified tolerances.
By carefully considering impedance requirements and collaborating with PCB manufacturers, designers can create robust and reliable PCBs that deliver optimal performance in high-speed applications.
Impedance Control Technique | Description |
---|---|
Trace Width Adjustment | Varying the width of the trace to control impedance |
Dielectric Thickness | Adjusting the substrate thickness between the trace and reference plane |
Dielectric Material Selection | Choosing a substrate material with the appropriate dielectric constant |
Differential Pair Routing | Maintaining symmetry and equal length between traces in differential pairs |
Reference Plane Placement | Placing reference planes (ground or power) near signal traces |
Termination Techniques | Implementing series or parallel termination to match source and load impedance |
Common Impedance Values | Application |
---|---|
50 ohms | Digital systems, high-speed communication interfaces (USB, HDMI), RF circuits |
75 ohms | Video and cable television (CATV) applications, analog and RF circuits |
28 ohms, 100 ohms, 110 ohms | Specific applications or standards |