What are PCB test points?
PCB test points are small, exposed pads or vias on a printed circuit board that are specifically designed for testing and debugging purposes. These points are typically labeled or marked on the PCB silkscreen to make them easily identifiable. Test points allow direct access to specific signals or nodes on the board, which can be probed using test equipment such as oscilloscopes, multimeters, or logic analyzers.
Types of PCB test points
There are several types of test points commonly used on PCBs:
-
Surface mount test points: These are small, flat pads on the surface of the PCB that can be easily probed with test equipment. They are often used for quick access to signals during testing or debugging.
-
Through-hole test points: These test points are implemented using plated through-holes (PTHs) that extend from the surface of the PCB to the opposite side. They provide a more robust connection for test probes and can be used for more permanent testing fixtures.
-
Edge connector test points: Some PCBs feature test points along the edge of the board, allowing for easy access when the board is mounted in a connector or chassis.
-
Bed-of-nails test points: These test points are designed to work with a bed-of-nails testing fixture, which consists of an array of spring-loaded pins that make contact with the test points on the PCB. This type of testing is often used for high-volume manufacturing testing.
Importance of PCB test points
Test points serve several crucial functions in the design, manufacturing, and maintenance of electronic devices:
Design verification
During the design phase, test points enable engineers to verify the functionality of individual components and circuits on the PCB. By probing test points and measuring signals, designers can ensure that the board performs as intended and meets the specified requirements.
Manufacturing testing
In the manufacturing process, test points are used to perform various tests on the assembled PCBs. These tests may include:
- Continuity testing: Verifying that all connections on the board are intact and there are no short circuits or open connections.
- Functional testing: Checking that the board functions as designed by stimulating inputs and measuring outputs at the test points.
- Boundary scan testing: Utilizing test points in conjunction with boundary scan techniques (such as JTAG) to test complex digital circuits and interconnects.
By thoroughly testing the PCBs at the manufacturing stage, companies can identify and address any issues before the boards are integrated into the final product, reducing the risk of field failures and warranty claims.
Troubleshooting and repair
Test points play a vital role in troubleshooting and repairing faulty PCBs. When a device malfunctions, technicians can use the test points to isolate the problem by measuring voltages, waveforms, and other parameters at various points on the board. This helps narrow down the source of the issue and guides the repair process.
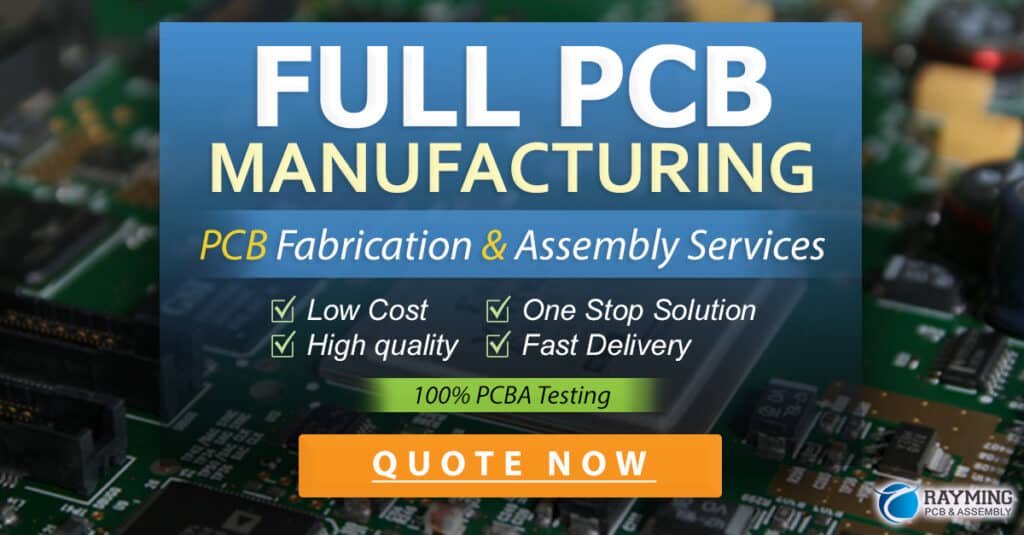
Designing PCBs with test points
When designing a PCB, it’s essential to consider the placement and accessibility of test points. Here are some best practices for incorporating test points into your PCB design:
-
Strategic placement: Position test points near critical components, power rails, and signal paths that are likely to require testing or debugging. Ensure that the test points are easily accessible with test probes or fixtures.
-
Clear labeling: Label the test points clearly on the PCB silkscreen using descriptive names or abbreviations. This helps technicians quickly identify the correct points during testing and troubleshooting.
-
Adequate spacing: Provide sufficient space around the test points to accommodate test probes or fixtures without interfering with nearby components or traces.
-
Signal integrity: Consider the impact of test points on signal integrity, especially for high-speed or sensitive signals. Place test points on less critical signals or use non-intrusive probing methods to minimize the effect on signal quality.
-
Standardization: Establish a consistent naming convention and placement strategy for test points across your PCB designs. This makes it easier for technicians to work with different boards and reduces the likelihood of errors during testing.
Test point documentation
Proper documentation is crucial for effectively using test points during manufacturing, testing, and maintenance. When creating documentation for your PCB, include the following information related to test points:
- A list of all test points on the board, including their names, locations, and functions.
- Schematic diagrams highlighting the test points and their connections to the circuit.
- Test procedures detailing the steps for testing the board using the test points, including the expected voltages, waveforms, or logic levels at each point.
- Troubleshooting guides that reference the test points and provide guidance on how to diagnose common issues based on measurements taken at those points.
Comprehensive and up-to-date documentation ensures that technicians and engineers have the information they need to efficiently test, debug, and repair the PCBs.
Test equipment for PCB test points
To effectively utilize test points, it’s essential to have the appropriate test equipment. Some common tools used for probing test points include:
-
Multimeters: Used for measuring voltages, currents, and resistances at test points. Multimeters are essential for verifying the presence of correct DC voltages and checking for short circuits or open connections.
-
Oscilloscopes: Used for visualizing and measuring time-varying signals at test points. Oscilloscopes are invaluable for debugging and characterizing the behavior of analog and digital circuits.
-
Logic analyzers: Used for capturing and analyzing digital signals at test points. Logic analyzers are particularly useful for troubleshooting complex digital systems and observing the timing relationships between multiple signals.
-
Frequency counters: Used for measuring the frequency of periodic signals at test points. Frequency counters are helpful for verifying clock signals and ensuring that oscillators are functioning correctly.
-
Probes and test clips: Various types of probes and test clips are used to connect the test equipment to the test points on the PCB. These accessories come in different sizes and configurations to suit different test point layouts and probing requirements.
By having the right test equipment and accessories, engineers and technicians can efficiently probe test points and gather the data needed to verify, debug, and troubleshoot PCBs.
Best practices for using PCB test points
To get the most out of PCB test points, follow these best practices:
-
Use ESD protection: Always use electrostatic discharge (ESD) protection measures when handling PCBs and probing test points. This includes wearing an ESD wrist strap, using grounded test equipment, and working on an ESD-safe surface.
-
Follow the test procedure: Adhere to the established test procedures and guidelines when probing test points. This ensures consistency and reduces the risk of damage to the board or components.
-
Use the correct probes: Select the appropriate probes or test clips for the test points you are working with. Using the wrong type of probe can lead to inaccurate measurements or damage to the PCB.
-
Minimize probe loading: Be aware of the loading effect of your test probes on the circuit. High-impedance probes or active probes can minimize the impact on the signal being measured.
-
Document your findings: Keep detailed records of the measurements and observations made at each test point. This documentation can be valuable for future reference, troubleshooting, or process improvement.
By following these best practices, you can ensure accurate and reliable testing results while minimizing the risk of damage to the PCB.
FAQ
-
Q: What is the purpose of test points on a PCB?
A: Test points on a PCB provide access to specific signals or nodes, allowing engineers and technicians to measure voltages, monitor signals, and diagnose issues during the manufacturing process or troubleshooting. -
Q: How do I identify test points on a PCB?
A: Test points are typically labeled or marked on the PCB silkscreen, making them easily identifiable. The documentation for the PCB should also include a list of test points, their locations, and functions. -
Q: Can test points affect the signal integrity of a PCB?
A: Yes, test points can potentially impact signal integrity, especially for high-speed or sensitive signals. To minimize this effect, place test points on less critical signals or use non-intrusive probing methods. -
Q: What equipment do I need to probe test points on a PCB?
A: Common equipment used for probing test points includes multimeters, oscilloscopes, logic analyzers, and frequency counters. Additionally, you’ll need appropriate probes or test clips to connect the equipment to the test points. -
Q: Are there any safety precautions I should take when working with test points?
A: Yes, always use ESD protection measures when handling PCBs and probing test points. This includes wearing an ESD wrist strap, using grounded test equipment, and working on an ESD-safe surface to prevent damage to the PCB or components.
Conclusion
Test points are a crucial aspect of PCB design, manufacturing, and maintenance. They provide access to specific signals and nodes, enabling engineers and technicians to verify functionality, diagnose issues, and troubleshoot problems. By strategically placing test points on a PCB and following best practices for their use, companies can improve the efficiency and reliability of their testing and repair processes.
When designing PCBs, it’s essential to consider the placement, labeling, and accessibility of test points. Proper documentation, including test point lists, schematics, and test procedures, is also critical for effective utilization of test points. By investing in the right test equipment and training technicians on best practices, organizations can maximize the benefits of PCB test points and ensure the quality and reliability of their electronic products.