Understanding the Basics of PCB Stackups
Definition and Importance
A PCB stackup is the sequence of layers that form a printed circuit board. It defines the order and arrangement of conductive copper layers, insulating dielectric layers, and other materials that make up the PCB. The stackup plays a crucial role in the performance, reliability, and manufacturability of the circuit board.
Layers in a PCB Stackup
A typical PCB stackup consists of the following layers:
-
Copper Layers: These are the conductive layers that carry electrical signals and power. The number of copper layers varies depending on the complexity of the design and the required functionality.
-
Dielectric Layers: Also known as insulating layers, these are non-conductive materials that separate the copper layers. Common dielectric materials include FR-4, Rogers, and polyimide.
-
Solder Mask: This layer is applied on top of the outer copper layers to protect against oxidation and prevent solder bridges during the assembly process. It also provides insulation and improves the aesthetics of the PCB.
-
Silkscreen: The silkscreen layer is used to print text, logos, and component designators on the PCB surface. It aids in the assembly and identification of components.
Types of PCB Stackups
There are several types of PCB stackups, each with its own characteristics and applications:
-
Single-Layer: A single-layer PCB has only one conductive layer, typically used for simple designs and low-cost applications.
-
Double-Layer: Double-layer PCBs have two conductive layers, one on each side of the dielectric material. They offer more routing options and are suitable for medium-complexity designs.
-
Multi-Layer: Multi-layer PCBs have three or more conductive layers, separated by dielectric layers. They provide increased routing density and are used for complex designs with high component counts.
-
High-Density Interconnect (HDI): HDI PCBs employ advanced manufacturing techniques to achieve finer trace widths, smaller via sizes, and higher layer counts. They are used in high-performance applications where miniaturization and signal integrity are critical.
Designing a PCB Stackup
Factors to Consider
When designing a PCB stackup, several factors must be taken into account to ensure optimal performance and manufacturability:
-
Electrical Requirements: Consider the signal integrity, power delivery, and electromagnetic compatibility (EMC) requirements of the design. The stackup should provide adequate insulation, controlled impedance, and minimize crosstalk and signal reflections.
-
Mechanical Strength: The stackup should provide sufficient mechanical strength to withstand the stresses of manufacturing, assembly, and operation. Factors such as layer thickness, dielectric material properties, and copper weight influence the mechanical integrity of the PCB.
-
Thermal Management: The stackup should facilitate efficient heat dissipation to prevent overheating of components. Thermal vias, copper planes, and appropriate dielectric materials can help in thermal management.
-
Manufacturing Capabilities: The stackup design must align with the capabilities of the PCB manufacturer. Consider the minimum trace width, via size, and layer count that the manufacturer can reliably produce.
Material Selection
Choosing the right materials for the PCB stackup is crucial for achieving the desired electrical and mechanical properties. Key considerations include:
-
Dielectric Material: Select a dielectric material with suitable electrical properties (e.g., dielectric constant, loss tangent) and mechanical strength. Common options include FR-4, Rogers, and polyimide.
-
Copper Weight: The copper weight determines the thickness of the conductive layers. Higher copper weights offer lower resistance and better current-carrying capacity but may increase the overall thickness of the board.
-
Solder Mask and Silkscreen: Choose solder mask and silkscreen materials that provide good insulation, durability, and legibility.
Stackup Configurations
There are various stackup configurations that can be used depending on the design requirements and manufacturing constraints. Some common configurations include:
-
Symmetric Stackup: In a symmetric stackup, the layers are arranged symmetrically around the center layer. This configuration helps in minimizing warpage and provides better signal integrity.
-
Asymmetric Stackup: An asymmetric stackup has an uneven distribution of layers, which can be useful for designs with specific electrical or mechanical requirements.
-
Hybrid Stackup: A hybrid stackup combines different dielectric materials or layer thicknesses to achieve specific electrical or mechanical properties.
Impedance Control
Controlling the impedance of the PCB traces is essential for maintaining signal integrity and preventing reflections. The stackup design plays a critical role in impedance control. Factors to consider include:
-
Trace Width and Spacing: The width and spacing of the traces affect their characteristic impedance. Appropriate trace geometry must be calculated based on the desired impedance and the dielectric properties of the substrate.
-
Dielectric Thickness: The thickness of the dielectric layers between the signal traces and the reference planes influences the impedance. Thinner dielectrics result in higher capacitance and lower impedance.
-
Reference Planes: Proper placement and spacing of reference planes (e.g., ground and power planes) are necessary for maintaining a consistent impedance throughout the signal path.
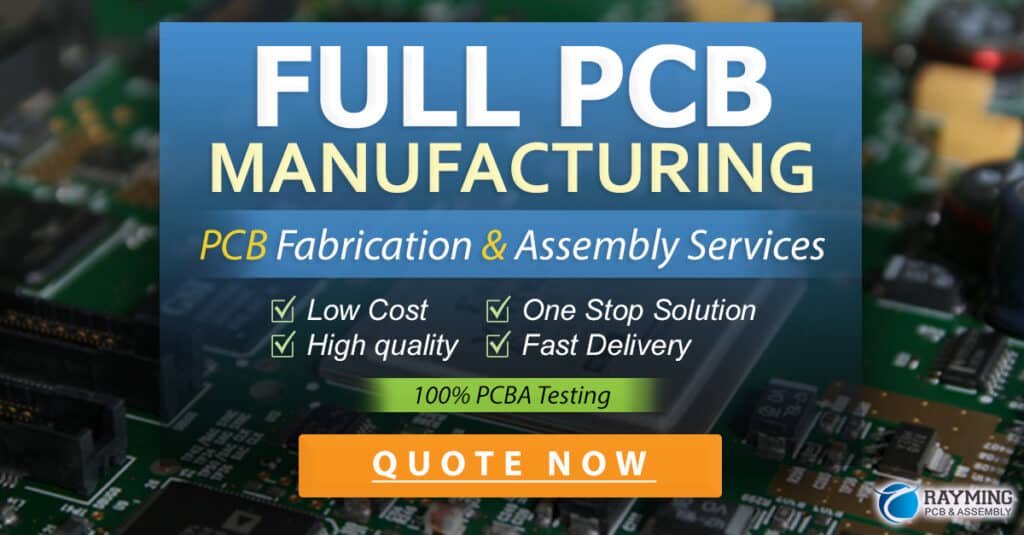
Manufacturing and Testing
PCB Fabrication Process
Once the PCB stackup is designed, it undergoes the fabrication process. The basic steps involved in PCB fabrication are:
-
Plotting and Etching: The designed circuit pattern is plotted onto the copper layers, and the unwanted copper is etched away.
-
Lamination: The etched copper layers are stacked and laminated together with the dielectric material under heat and pressure.
-
Drilling: Holes are drilled through the laminated board for vias, component mounting, and tooling.
-
Plating: The drilled holes are plated with copper to establish electrical connections between layers.
-
Solder Mask and Silkscreen: The solder mask and silkscreen layers are applied to protect the copper and provide component identification.
Testing and Inspection
After fabrication, the PCB undergoes various tests and inspections to ensure its quality and functionality. Some common tests include:
-
Continuity Test: This test verifies that all the intended electrical connections are intact and there are no open circuits.
-
Isolation Test: It checks for any short circuits or unintended connections between different parts of the circuit.
-
Impedance Test: The impedance of critical traces is measured to ensure they meet the specified values.
-
Visual Inspection: The PCB is visually inspected for any manufacturing defects, such as incorrect hole sizes, missing components, or solder bridges.
Best Practices and Guidelines
To ensure a robust and reliable PCB stackup, consider the following best practices and guidelines:
-
Follow Industry Standards: Adhere to industry standards and guidelines, such as IPC-2221 and IPC-4101, which provide recommendations for PCB design and material selection.
-
Collaborate with Manufacturers: Engage with PCB manufacturers early in the design process to ensure that your stackup is manufacturable and aligns with their capabilities.
-
Use Simulation Tools: Utilize PCB simulation tools to analyze signal integrity, power delivery, and thermal performance of the stackup before finalizing the design.
-
Document the Stackup: Clearly document the PCB stackup, including layer order, materials, thicknesses, and impedance requirements. This information is crucial for manufacturing and future reference.
-
Consider Manufacturing Tolerances: Account for manufacturing tolerances in the stackup design, such as variations in dielectric thickness and copper weight, to ensure the board meets the specified requirements.
Frequently Asked Questions (FAQ)
-
What is the difference between a single-layer and a double-layer PCB stackup?
A single-layer PCB has only one conductive layer, while a double-layer PCB has two conductive layers, one on each side of the dielectric material. Double-layer PCBs offer more routing options and are suitable for medium-complexity designs. -
How does the dielectric material affect the PCB stackup?
The dielectric material influences the electrical properties of the PCB, such as the dielectric constant and loss tangent. It also affects the mechanical strength and thermal performance of the board. Choosing the right dielectric material is crucial for achieving the desired characteristics of the PCB. -
What is impedance control, and why is it important in PCB stackup design?
Impedance control refers to the process of designing the PCB traces to have a specific characteristic impedance. It is important for maintaining signal integrity, preventing reflections, and ensuring proper termination of high-speed signals. The stackup design, including trace geometry and dielectric properties, plays a critical role in achieving controlled impedance. -
What tests are performed on a PCB after fabrication?
After fabrication, a PCB undergoes various tests to ensure its quality and functionality. Common tests include continuity test (to check for open circuits), isolation test (to check for short circuits), impedance test (to measure the impedance of critical traces), and visual inspection (to identify manufacturing defects). -
How can I ensure that my PCB stackup is manufacturable?
To ensure manufacturability, it is important to collaborate with PCB manufacturers early in the design process. Adhere to industry standards and guidelines, consider manufacturing tolerances, and clearly document the stackup specifications. Using PCB simulation tools can also help in identifying potential manufacturing issues before finalizing the design.
Conclusion
A well-designed PCB stackup is essential for the optimal performance, reliability, and manufacturability of a printed circuit board. By understanding the basics of PCB stackups, considering the design factors, selecting appropriate materials, and following best practices, designers can create robust and efficient PCBs that meet the specific requirements of their applications.
As technology advances and electronic devices become more complex, the importance of proper PCB stackup design will only continue to grow. By staying updated with the latest industry standards, collaborating with manufacturers, and leveraging simulation tools, designers can overcome the challenges and create PCBs that push the boundaries of innovation.
Layer Type | Material | Thickness |
---|---|---|
Silkscreen | Epoxy Ink | 0.1 mm |
Solder Mask | LPI | 0.03 mm |
Copper Layer 1 | Copper | 0.035 mm |
Dielectric Layer 1 | FR-4 | 0.2 mm |
Copper Layer 2 | Copper | 0.035 mm |
Dielectric Layer 2 | FR-4 | 0.2 mm |
Copper Layer 3 | Copper | 0.035 mm |
Solder Mask | LPI | 0.03 mm |
Silkscreen | Epoxy Ink | 0.1 mm |
Table 1: Example PCB Stackup Configuration
In conclusion, a well-designed PCB stackup is a critical aspect of PCB design that directly impacts the performance, reliability, and manufacturability of the final product. By carefully considering the electrical, mechanical, and thermal requirements, selecting appropriate materials, and following best practices and industry standards, designers can create optimized PCB stackups that meet the demands of today’s complex electronic devices.