What is a PCB?
PCB stands for “printed circuit board.” It is the base board that provides electrical connections and mechanical support for electronic components. A PCB starts as a non-conductive substrate, typically made of fiberglass (FR4), with a thin layer of copper foil laminated to one or both sides. The copper is etched away in a specific pattern, leaving behind conductive copper traces that form a circuit.
Some key characteristics of PCBs include:
- Substrate material (FR4, polyimide, etc.)
- Number of copper layers (single-sided, double-sided, multi-layer)
- Copper weight/thickness (measured in ounces per square foot)
- Minimum trace width and spacing
- Surface finish (HASL, ENIG, OSP, etc.)
Here is a table summarizing common PCB materials and their properties:
Material | Dielectric Constant | Dissipation Factor | Temperature Resistance |
---|---|---|---|
FR-4 | 4.5 @ 1 MHz | 0.02 @ 1 MHz | 130°C |
Polyimide | 3.5 @ 1 GHz | 0.002 @ 1 GHz | 260°C |
PTFE (Teflon) | 2.1 @ 10 GHz | 0.001 @ 10 GHz | 260°C |
Ceramic | 9.8 @ 1 MHz | < 0.002 @ 1 MHz | > 260°C |
PCBs can be classified based on the number of conductive layers:
-
Single-sided: Copper traces on one side of the substrate only. Components are placed on the opposite side. Lowest cost but limited wiring density.
-
Double-sided: Copper layers on both sides of the substrate. Plated through-holes allow circuits on opposite sides to connect. Higher wiring density than single-sided.
-
Multi-layer: Three or more copper layers alternating with insulating layers. Adjacent layers connect through vias. Allows very high wiring density and circuit complexity. Typically 4-12 layers, but can exceed 50 layers in some applications.
PCB Design Process
The PCB design process typically involves the following steps:
-
Schematic capture: Creating a symbolic representation of the circuit in an electronic design automation (EDA) tool.
-
Component placement: Arranging components on the board for optimal performance, manufacturing, and assembly.
-
Routing: Defining the path of copper traces to electrically connect components according to the schematic.
-
Design rule check (DRC): Verifying the design meets manufacturing constraints and electrical requirements.
-
Output generation: Producing the files needed for PCB fabrication, such as Gerber files, drill files, and bill of materials (BOM).
What is PCBA?
PCBA stands for “printed circuit board assembly.” It refers to the PCB after components have been soldered onto it. The bare PCB is transformed into a functional circuit through the assembly process.
PCBA involves several key steps:
-
Solder paste application: Depositing solder paste onto the PCB’s exposed pads using a stencil or screen.
-
Component placement: Placing components onto the PCB, either manually or with automated pick-and-place machines. Surface mount devices (SMDs) are positioned directly onto the solder paste.
-
Reflow soldering: Passing the populated PCB through a reflow oven to melt the solder, forming permanent electrical connections.
-
Through-hole component insertion: Inserting leads of through-hole components into plated holes and soldering them, typically using wave soldering.
-
Inspection and quality control: Verifying proper assembly with automated optical inspection (AOI), X-ray inspection, or electrical testing.
The type of components used and their packaging influences the PCBA process:
-
Surface mount technology (SMT): Components are soldered directly onto the surface of the PCB. Allows high component density and automated assembly.
-
Through-hole technology (THT): Component leads are inserted through holes in the PCB and soldered on the opposite side. Provides strong mechanical bonds but lower density than SMT.
-
Mixed technology: PCBAs containing both SMT and THT components. Requires additional processing steps compared to all-SMT designs.
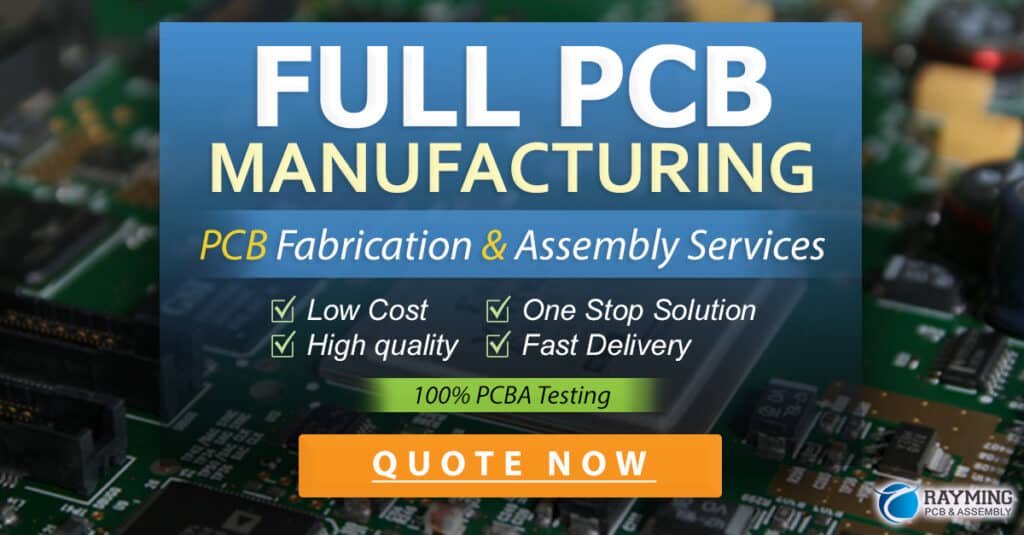
Comparing PCB vs PCBA
While a PCB and PCBA are closely related, they represent different stages of the electronics manufacturing process. Here’s a comparison table highlighting key differences:
Aspect | PCB | PCBA |
---|---|---|
Definition | Bare circuit board with etched copper traces | Assembled board with components soldered |
Components | None | SMT and/or THT components |
Functionality | Provides electrical connectivity and mechanical support | Performs the intended electronic function |
Manufacturing Steps | Designing, etching, drilling, plating, coating | PCB fabrication + component assembly and soldering |
Testing | Continuity, resistance, and isolation tests | Functional, in-circuit, and system-level tests |
Cost | Lower than PCBA | Higher due to added components and assembly |
Lead Time | Shorter than PCBA | Longer due to additional assembly processes |
In summary, a PCB is the bare board that provides the foundation for an electronic circuit, while a PCBA is the fully assembled and functional board with components soldered onto it.
PCB and PCBA Applications
PCBs and PCBAs are used in virtually every electronic device and system. Some common applications include:
- Consumer electronics (smartphones, tablets, laptops)
- Automotive electronics (infotainment systems, engine control units)
- Industrial control systems
- Medical devices
- Aerospace and defense systems
- IoT devices and smart home appliances
- Power electronics and renewable energy systems
The choice between a PCB or PCBA depends on the specific needs of the application. For example, a PCB designer might order bare boards for prototyping and testing, while a device manufacturer would source complete PCBAs for production.
PCBA Manufacturing Considerations
When designing a PCBA, several factors influence manufacturability and cost:
-
Component selection: Choosing components that are readily available, have compatible packaging, and meet performance requirements.
-
Design for manufacturing (DFM): Adhering to design rules and guidelines that ensure reliable, high-yield manufacturing. This includes considerations such as pad size, trace width, and component spacing.
-
Panelization: Grouping multiple PCBs into a larger panel for more efficient fabrication and assembly.
-
Test strategy: Defining the methods and coverage for verifying PCBA functionality and quality, such as boundary scan testing, functional testing, and burn-in.
-
Supply chain management: Coordinating procurement, inventory, and logistics for PCBs, components, and assembled boards.
Effective communication between design and manufacturing teams is essential to optimize the PCBA process and avoid costly delays or re-spins.
Future Trends in PCB and PCBA Technology
As electronics continue to advance, so do PCB and PCBA technologies. Some notable trends and developments include:
-
High-density interconnect (HDI): PCBs with finer traces, smaller vias, and higher layer counts to accommodate miniaturization and increased functionality.
-
Flexible and rigid-flex PCBs: Boards that can bend or fold to fit in compact or irregularly shaped spaces.
-
Embedded components: Placing components within the layers of a PCB to save space and improve performance.
-
3D printing: Additive manufacturing techniques for creating PCBs and even complete PCBAs.
-
Advanced materials: Adoption of high-performance substrates, such as polyimide, PTFE, and ceramic, for demanding applications.
-
Eco-friendly manufacturing: Implementing lead-free soldering, halogen-free materials, and recycling programs to reduce environmental impact.
As these technologies mature, they will enable new possibilities for PCB and PCBA design and manufacturing.
Frequently Asked Questions
1. Can a PCB function without components?
No, a bare PCB does not function as an electronic circuit. It needs components to be soldered onto it (turning it into a PCBA) to perform its intended function.
2. Are all PCBAs also PCBs?
Yes, all PCBAs contain a PCB as the base board. The PCB is an integral part of the PCBA.
3. What is the most common type of PCB?
FR-4 is the most widely used PCB material due to its good mechanical and electrical properties and cost-effectiveness. Multi-layer PCBs are common in complex electronic devices.
4. How long does it take to manufacture a PCBA?
PCBA lead times vary depending on factors such as design complexity, materials, and production volume. Simple PCBAs can be manufactured in a few days, while complex, high-volume orders may take several weeks.
5. What is the difference between PTH and SMT assembly?
PTH (plated through-hole) assembly involves inserting component leads through holes in the PCB and soldering them on the opposite side. SMT (surface mount technology) assembly mounts components directly onto the surface of the PCB using solder paste and reflow soldering. SMT allows for higher component density and automated assembly compared to PTH.
In conclusion, understanding the difference between PCBs and PCBAs is crucial for anyone involved in electronics design, manufacturing, or procurement. While a PCB provides the physical foundation for a circuit, the PCBA brings it to life with soldered components. Advances in materials, manufacturing processes, and design tools continue to push the boundaries of what’s possible with PCB and PCBA technology.