The Importance of PCB Prototyping
PCB prototyping is crucial for several reasons:
-
Design Validation: Prototyping allows designers to physically test their PCB layouts and ensure that they function as intended. This helps identify any design flaws or potential issues early in the development process.
-
Cost Savings: By identifying and resolving issues during the prototyping phase, companies can avoid costly mistakes and rework during mass production.
-
Functionality Testing: Prototypes enable engineers to test the PCB’s functionality, including signal integrity, power distribution, and component compatibility.
-
Iterative Improvement: Based on the feedback and results obtained from prototype testing, designers can make iterative improvements to their PCB layouts, enhancing the overall performance and reliability of the final product.
The PCB Prototyping Process
The PCB prototyping process typically involves the following steps:
1. Schematic Design
The first step in PCB prototyping is to create a schematic diagram of the electronic circuit. This diagram represents the electrical connections and components required for the PCB to function as intended. Designers use electronic design automation (EDA) software to create the schematic, which serves as a blueprint for the PCB layout.
2. PCB Layout Design
Once the schematic is complete, designers proceed to create the PCB layout. This involves arranging the components and routing the traces on the PCB according to the schematic. The layout design must consider various factors, such as component placement, signal integrity, power distribution, and manufacturability. EDA software is used to create the PCB layout, which is then exported as Gerber files for manufacturing.
3. PCB Fabrication
The Gerber files generated from the PCB layout design are sent to a PCB manufacturer for fabrication. The manufacturer uses these files to create the physical PCB prototype. The fabrication process involves several steps, including:
- Printing the Circuit Pattern: The circuit pattern is printed onto a copper-clad laminate using a photoresist and exposure to UV light.
- Etching: The unwanted copper is etched away, leaving only the desired circuit pattern.
- Drilling: Holes are drilled into the PCB for through-hole components and vias.
- Plating: The holes are plated with copper to establish electrical connections between layers.
- Solder Mask Application: A protective solder mask is applied to the PCB to insulate the copper traces and prevent short circuits.
- Silkscreen Printing: Text and symbols are printed onto the PCB for component identification and assembly guidance.
4. PCB Assembly
After the PCB fabrication is complete, the prototype is assembled with the required components. This process can be done manually or using automated assembly machines, depending on the complexity of the design and the quantity of prototypes required. The components are soldered onto the PCB, either through-hole or surface-mount, according to the layout design.
5. Testing and Validation
Once the PCB prototype is assembled, it undergoes thorough testing and validation to ensure that it functions as intended. This may include:
- Power-on Testing: Checking if the PCB powers on and if the power distribution is correct.
- Functional Testing: Verifying that the PCB performs all the intended functions and meets the design requirements.
- Signal Integrity Testing: Ensuring that the signals are transmitted correctly and without interference or distortion.
- Environmental Testing: Subjecting the PCB to various environmental conditions, such as temperature, humidity, and vibration, to assess its reliability and durability.
Any issues or defects identified during testing are documented, and the necessary changes are made to the PCB design. The prototyping process may be repeated until the design is finalized and ready for mass production.
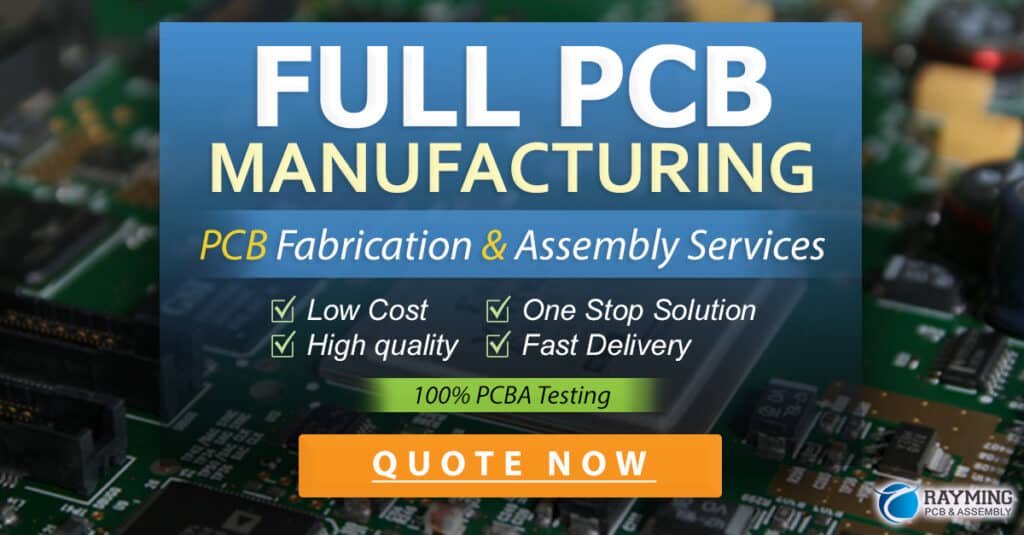
PCB Prototyping Techniques
There are several techniques used for PCB prototyping, depending on the complexity of the design, the required turnaround time, and the available resources. Some common PCB prototyping techniques include:
1. Breadboarding
Breadboarding is a quick and easy way to prototype simple electronic circuits. It involves using a breadboard, which is a reusable plastic board with holes for inserting components and jumper wires. Breadboarding allows designers to quickly test and modify their circuits without the need for soldering. However, it is not suitable for complex designs or high-frequency circuits.
2. Perfboard Prototyping
Perfboard prototyping involves using a perforated board with pre-drilled holes to assemble the PCB prototype. The components are inserted into the holes and soldered together using jumper wires. This technique is suitable for simple to moderately complex designs and allows for easier modification compared to breadboarding. However, it can be time-consuming and may not be suitable for high-frequency circuits.
3. Printed Circuit Board (PCB) Milling
pcb milling is a subtractive manufacturing process that uses a computer-controlled milling machine to remove copper from a pre-coated PCB substrate, creating the desired circuit pattern. This technique is suitable for low-volume prototyping and allows for quick turnaround times. However, it has limitations in terms of trace width, spacing, and the number of layers that can be milled.
4. rapid pcb prototyping Services
Rapid PCB prototyping services, also known as quick-turn PCB fabrication, are offered by specialized PCB manufacturers who can produce high-quality PCB prototypes in a short timeframe, often within a few days. These services use advanced manufacturing techniques, such as automated assembly and high-speed drilling, to streamline the prototyping process. They are suitable for complex designs and can handle a wide range of PCB specifications.
Choosing the Right PCB Prototyping Method
When selecting a PCB prototyping method, consider the following factors:
-
Design Complexity: Simple designs can be prototyped using breadboarding or perfboard, while complex designs may require PCB milling or rapid prototyping services.
-
Turnaround Time: If time is a critical factor, rapid prototyping services may be the best option, as they offer the fastest turnaround times.
-
Cost: Breadboarding and perfboard prototyping are the most cost-effective methods, while PCB milling and rapid prototyping services are more expensive.
-
Quantity: For low-volume prototyping, breadboarding, perfboard, or PCB milling may be sufficient. For higher volumes, rapid prototyping services are more suitable.
-
Design Requirements: Consider the specific requirements of your design, such as trace width, spacing, number of layers, and component density, when choosing a prototyping method.
Common PCB Prototyping Materials
PCB prototypes are typically made using a variety of materials, depending on the specific requirements of the design. Some common PCB prototyping materials include:
1. FR-4
FR-4 is a flame-retardant, glass-reinforced epoxy laminate that is widely used in PCB fabrication. It offers good mechanical and electrical properties, making it suitable for a wide range of applications. FR-4 is available in various thicknesses and copper weights, allowing for flexibility in design.
2. Aluminum
aluminum pcbs are used in applications that require high thermal conductivity, such as power electronics and LED lighting. The aluminum substrate helps dissipate heat more efficiently, improving the performance and reliability of the circuit.
3. Flexible PCBs
Flexible PCBs are made using thin, flexible substrate materials, such as polyimide or polyester. They are used in applications that require the PCB to bend or conform to a specific shape, such as wearable electronics or compact devices.
4. High-Frequency Materials
For high-frequency applications, such as RF and microwave circuits, specialized PCB materials with low dielectric loss and stable dielectric constants are used. These materials, such as Rogers or Teflon, help maintain signal integrity and minimize signal loss at high frequencies.
PCB Prototyping Design Considerations
When designing a PCB prototype, consider the following factors to ensure the best possible performance and manufacturability:
-
Component Placement: Arrange components in a logical and efficient manner, considering signal flow, power distribution, and thermal management.
-
Trace Routing: Route traces efficiently, minimizing trace length and avoiding sharp angles or crossovers. Consider signal integrity and impedance matching for high-frequency designs.
-
Power Distribution: Ensure proper power distribution by using appropriate trace widths, copper weights, and power planes. Use decoupling capacitors to minimize noise and voltage fluctuations.
-
Grounding: Implement a solid grounding strategy, using ground planes and proper ground connections to minimize noise and ensure signal integrity.
-
Design for Manufacturing (DFM): Follow DFM guidelines to ensure that your PCB design is manufacturable and cost-effective. Consider factors such as minimum trace width, spacing, hole size, and component clearances.
Frequently Asked Questions (FAQ)
-
What is the difference between PCB prototyping and PCB manufacturing?
PCB prototyping is the process of creating a small number of physical PCBs for testing and validation purposes, while PCB manufacturing involves the mass production of PCBs for commercial use. Prototyping is typically done before manufacturing to ensure that the design is functional and meets the required specifications. -
How long does PCB prototyping take?
The time required for PCB prototyping depends on the complexity of the design, the chosen prototyping method, and the manufacturer. Simple designs using breadboarding or perfboard can be prototyped in a matter of hours, while complex designs using rapid prototyping services may take several days. -
How much does PCB prototyping cost?
The cost of PCB prototyping varies depending on factors such as the design complexity, the prototyping method, the materials used, and the quantity of prototypes required. Breadboarding and perfboard prototyping are the most cost-effective methods, while rapid prototyping services are more expensive but offer higher quality and faster turnaround times. -
What are the benefits of using rapid PCB prototyping services?
Rapid PCB prototyping services offer several benefits, including: - Fast turnaround times, often within a few days
- High-quality PCB fabrication using advanced manufacturing techniques
- Ability to handle complex designs with fine trace widths and small component sizes
- Automated assembly options for faster prototyping
-
Access to a wide range of PCB materials and specifications
-
Can I prototype a PCB at home?
Yes, it is possible to prototype simple PCBs at home using breadboarding or perfboard techniques. However, for more complex designs or higher-quality prototypes, it is recommended to use professional PCB prototyping services to ensure the best results.
In conclusion, PCB prototyping is a critical step in the development of electronic devices, allowing designers to test and validate their designs before committing to mass production. By using the appropriate prototyping techniques, materials, and design considerations, engineers can create high-quality PCB prototypes that meet their specific requirements and help bring their products to market faster and more efficiently.
PCB Prototyping Technique | Complexity | Turnaround Time | Cost | Suitable for |
---|---|---|---|---|
Breadboarding | Simple | Hours | Low | Quick testing and modification of simple circuits |
Perfboard Prototyping | Simple to Moderate | Days | Low to Moderate | Simple to moderately complex designs, easier modification compared to breadboarding |
PCB Milling | Moderate to Complex | Days | Moderate | Low-volume prototyping, quick turnaround times, limited trace width and spacing |
Rapid PCB Prototyping Services | Complex | Days | High | Complex designs, fine trace widths, small component sizes, automated assembly |