What is Electronic Contract Manufacturing?
Electronic contract manufacturing is the process of outsourcing the production of electronic components, sub-assemblies, or complete products to a third-party company. The contract manufacturer is responsible for the entire manufacturing process, from sourcing raw materials to the final assembly and testing of the product. This allows the original equipment manufacturer (OEM) to focus on their core competencies, such as product design, marketing, and sales, while the CEM handles the manufacturing aspects.
Advantages of Electronic Contract Manufacturing
There are several advantages to outsourcing electronic manufacturing to a CEM:
-
Cost Reduction: CEMs often have economies of scale, which allows them to purchase components and raw materials at lower prices. They also have optimized manufacturing processes, which can lead to reduced labor costs and increased efficiency.
-
Flexibility: CEMs can quickly adapt to changes in demand, allowing OEMs to scale production up or down as needed. This is particularly useful for companies with seasonal or fluctuating demand.
-
Expertise: CEMs have specialized knowledge and experience in electronic manufacturing, which can lead to improved product quality and reliability.
-
Access to Technology: CEMs often invest in the latest manufacturing technologies and equipment, which can be costly for individual OEMs to acquire and maintain.
-
Time-to-Market: By outsourcing manufacturing, OEMs can reduce the time required to bring a product to market, as CEMs can work in parallel with the design and development process.
Services Provided by Contract Electronics Manufacturers
CEMs offer a wide range of services to support the entire product lifecycle, from design to distribution. Some of the key services include:
1. Design and Engineering Support
Many CEMs offer design and engineering services to help OEMs develop new products or improve existing ones. This can include:
- Schematic design
- PCB layout
- Component selection
- Prototype development
- Design for manufacturability (DFM) analysis
2. Prototyping and New Product Introduction (NPI)
CEMs can help OEMs bring new products to market by providing prototyping and NPI services. This includes:
- Rapid prototyping
- Proof-of-concept builds
- Pilot production runs
- Pre-production builds
- Design validation and testing
3. PCB Assembly
One of the core services provided by CEMs is printed circuit board (PCB) assembly. This involves soldering electronic components onto a PCB according to a specific design. CEMs offer various PCB assembly techniques, including:
- Surface mount technology (SMT)
- Through-hole technology (THT)
- Mixed-technology assembly
- Ball grid array (BGA) and chip scale package (CSP) assembly
- Flex circuit assembly
PCB Assembly Techniques | Description |
---|---|
Surface Mount Technology (SMT) | Components are mounted directly onto the surface of the PCB |
Through-Hole Technology (THT) | Components are inserted into drilled holes in the PCB and soldered |
Mixed-Technology Assembly | A combination of SMT and THT techniques |
BGA and CSP Assembly | Specialized techniques for mounting high-density components |
Flex Circuit Assembly | Assembly of flexible PCBs for applications requiring flexibility or space savings |
4. Cable and Wire Harness Assembly
CEMs also offer cable and wire harness assembly services, which involve the cutting, stripping, crimping, and soldering of wires and cables according to a specific design. This can include:
- Custom cable assemblies
- Wire harnesses
- Ribbon cables
- Coaxial cables
- Fiber optic cables
5. Box Build and System Integration
For OEMs requiring complete product assembly, CEMs provide box build and system integration services. This involves assembling all the components, sub-assemblies, and modules into a finished product, including:
- Enclosure fabrication and assembly
- Electro-mechanical assembly
- Hardware and software integration
- Functional testing
- Packaging and labeling
6. Testing and Quality Control
To ensure product quality and reliability, CEMs implement various testing and quality control measures throughout the manufacturing process. This can include:
- In-circuit testing (ICT)
- Functional testing
- Boundary scan testing
- X-ray inspection
- Automated optical inspection (AOI)
- Environmental testing (temperature, humidity, vibration, etc.)
Quality Control Techniques | Description |
---|---|
In-Circuit Testing (ICT) | Verifies the proper assembly and functionality of individual components on a PCB |
Functional Testing | Tests the complete product to ensure it meets the specified performance requirements |
Boundary Scan Testing | Tests the interconnections between components on a PCB |
X-Ray Inspection | Non-destructive testing method for detecting hidden defects or voids in solder joints |
Automated Optical Inspection (AOI) | Uses cameras and image processing software to detect surface-level defects on PCBs |
Environmental Testing | Exposes the product to various environmental conditions to ensure reliability and durability |
7. Supply Chain Management and Logistics
CEMs often provide supply chain management and logistics services to help OEMs manage their inventory and distribute their products. This can include:
- Component sourcing and procurement
- Inventory management
- Kanban and just-in-time (JIT) delivery
- Warehouse and distribution
- Order fulfillment and shipping
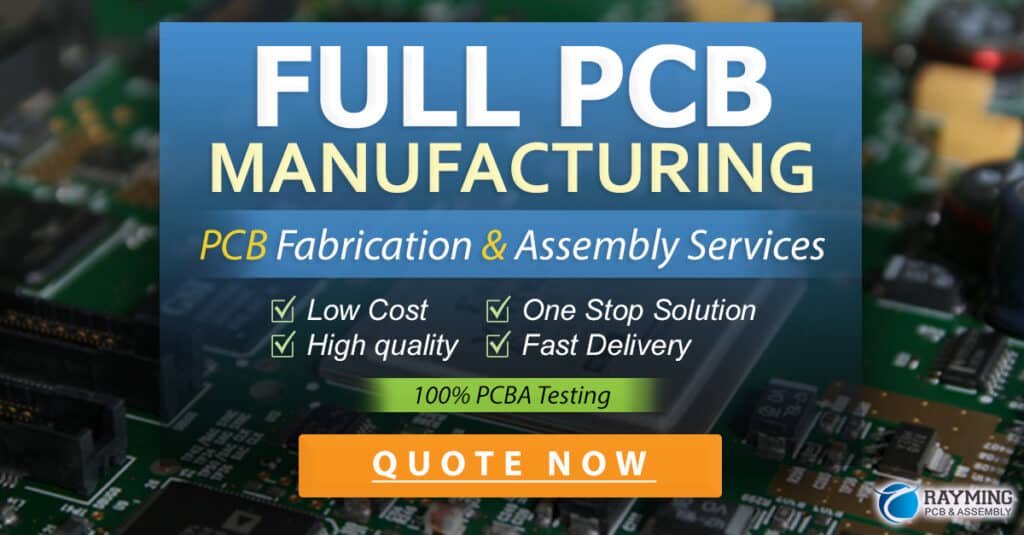
Factors to Consider When Choosing a Contract Electronics Manufacturer
When selecting a CEM, there are several factors to consider to ensure a successful partnership:
-
Technical Capabilities: Ensure that the CEM has the necessary equipment, expertise, and certifications to manufacture your product.
-
Quality Management: Look for a CEM with a robust quality management system, such as ISO 9001 or AS9100, to ensure consistent product quality.
-
Cost and Pricing: Compare pricing and cost structures among different CEMs, but also consider the value-added services they provide.
-
Communication and Collaboration: Choose a CEM that maintains open lines of communication and is willing to collaborate closely with your team.
-
Location and Logistics: Consider the CEM’s location and its ability to manage your supply chain and distribute your products efficiently.
-
Financial Stability: Assess the financial health of the CEM to ensure they can support your long-term manufacturing needs.
-
Reputation and References: Research the CEM’s reputation in the industry and ask for references from their existing customers.
Frequently Asked Questions (FAQ)
-
Q: What is the difference between a contract manufacturer and an original equipment manufacturer (OEM)?
A: An OEM is a company that designs and sells its own products, while a contract manufacturer is a company that manufactures products designed by other companies (OEMs). -
Q: Can a contract electronics manufacturer help with product design?
A: Yes, many CEMs offer design and engineering support services to help OEMs develop new products or improve existing ones. -
Q: How do I ensure the quality of the products manufactured by a CEM?
A: Look for a CEM with a robust quality management system, such as ISO 9001 or AS9100, and inquire about their testing and quality control processes. -
Q: What are the benefits of outsourcing electronic manufacturing to a CEM?
A: Outsourcing to a CEM can lead to cost reduction, increased flexibility, access to specialized expertise and technology, and faster time-to-market. -
Q: How do I select the right contract electronics manufacturer for my business?
A: Consider factors such as technical capabilities, quality management, cost and pricing, communication and collaboration, location and logistics, financial stability, and reputation when choosing a CEM.
Conclusion
Contract electronics manufacturing is a valuable service for companies looking to outsource the production of their electronic products. By partnering with a CEM, OEMs can benefit from cost reduction, increased flexibility, access to specialized expertise and technology, and faster time-to-market. CEMs offer a wide range of services, including design and engineering support, prototyping, PCB assembly, cable and wire harness assembly, box build and system integration, testing and quality control, and supply chain management and logistics.
When selecting a CEM, it is essential to consider factors such as technical capabilities, quality management, cost and pricing, communication and collaboration, location and logistics, financial stability, and reputation. By carefully evaluating these factors and choosing the right CEM, OEMs can ensure a successful partnership and bring high-quality electronic products to market efficiently and cost-effectively.