Introduction to PCB Trace Width Calculation
When designing a printed circuit board (PCB), one of the crucial factors to consider is the width of the traces. The trace width plays a significant role in determining the current-carrying capacity, signal integrity, and overall performance of the PCB. In this comprehensive article, we will dive into the process of calculating trace width for PCBs using a pcb trace width calculator and explore the various factors that influence this calculation.
What is PCB Trace Width?
PCB trace width refers to the thickness of the copper tracks that connect different components on a printed circuit board. These traces act as electrical pathways, allowing signals and power to flow between components. The width of the traces is typically measured in mils (thousandths of an inch) or millimeters.
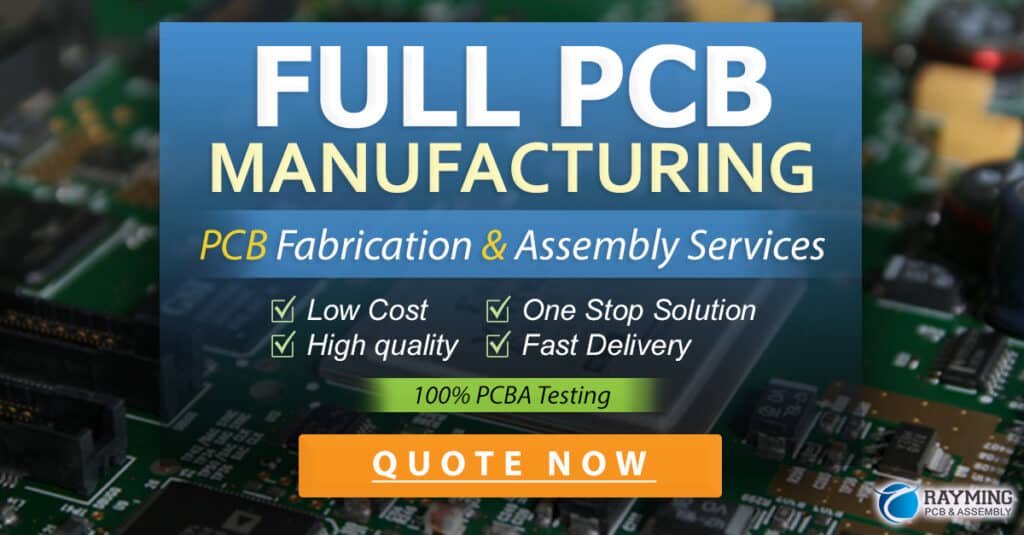
Why is PCB Trace Width Important?
The width of pcb traces is important for several reasons:
-
Current-Carrying Capacity: The trace width determines the maximum amount of current that can safely flow through the trace without causing excessive heating or damage to the PCB.
-
Signal Integrity: Trace width affects the impedance of the trace, which in turn influences the signal integrity. Proper trace width calculation ensures that signals maintain their quality and avoid issues like reflections, crosstalk, and signal distortion.
-
Manufacturing Constraints: The trace width must be within the manufacturing capabilities of the pcb fabrication process. Overly thin traces may be difficult to manufacture reliably, while excessively thick traces can lead to increased manufacturing costs.
Factors Affecting PCB Trace Width Calculation
Several factors need to be considered when calculating the appropriate trace width for a PCB:
1. Current Requirements
The amount of current flowing through a trace is a primary factor in determining the required trace width. Higher currents necessitate wider traces to prevent excessive heating and ensure reliable operation. The current-carrying capacity of a trace is influenced by factors such as the thickness of the copper layer, the ambient temperature, and the maximum allowable temperature rise.
2. Voltage Drop
Voltage drop occurs when current flows through a trace, resulting in a decrease in voltage along the length of the trace. Excessive voltage drop can lead to performance issues and signal degradation. The trace width must be sufficient to minimize voltage drop and ensure that the required voltage levels are maintained at the destination components.
3. PCB Layer and Copper Thickness
The thickness of the copper layer on the PCB directly impacts the current-carrying capacity of the traces. Thicker copper layers allow for higher current densities and enable the use of narrower traces. The standard copper thicknesses used in PCB manufacturing are typically expressed in ounces per square foot (oz/ft²), with common values being 0.5 oz/ft², 1 oz/ft², and 2 oz/ft².
4. Ambient Temperature and Thermal Considerations
The ambient temperature and the expected temperature rise during operation also influence the trace width calculation. Higher ambient temperatures and greater temperature rises require wider traces to dissipate heat effectively and prevent thermal damage to the PCB.
5. Signal Integrity and Impedance Matching
For high-speed signals and critical signal paths, trace width plays a crucial role in maintaining signal integrity and ensuring proper impedance matching. The trace width, along with other factors like dielectric thickness and substrate material, determines the characteristic impedance of the trace. Matching the trace impedance to the source and load impedances minimizes signal reflections and ensures optimal signal quality.
PCB Trace Width Calculation Methods
There are several methods and tools available for calculating PCB trace width:
1. IPC-2152 Standard
The IPC-2152 standard, developed by the Association Connecting Electronics Industries (IPC), provides guidelines for determining the current-carrying capacity and minimum trace width for PCBs. This standard takes into account factors such as copper thickness, temperature rise, and trace length to provide recommended trace widths for various current levels.
2. PCB Trace Width Calculators
PCB trace width calculators are software tools that simplify the process of determining the appropriate trace width based on user inputs. These calculators typically consider parameters such as current requirements, copper thickness, ambient temperature, and maximum allowable temperature rise. They provide quick and accurate results, making them a popular choice among pcb designers.
Some popular PCB trace width calculators include:
- Saturn PCB Toolkit
- EEWeb PCB Trace Width Calculator
- Advanced Circuits PCB Trace Width Calculator
- Digi-Key PCB Trace Width Calculator
3. Manual Calculation
For those who prefer a more hands-on approach, manual calculation of PCB trace width is possible using established formulas and equations. The most commonly used equation for trace width calculation is:
W = (I * ρ * L) / (ΔT * k * t)
Where:
– W = Trace width (mils or mm)
– I = Current (A)
– ρ = Resistivity of copper (Ω·mil)
– L = Trace length (mils or mm)
– ΔT = Maximum allowable temperature rise (°C)
– k = Thermal conductivity of the pcb material (W/m·°C)
– t = Copper thickness (mils or mm)
By plugging in the appropriate values for each variable, designers can manually calculate the required trace width for their specific PCB design.
PCB Trace Width Design Considerations
When designing PCB traces and determining their widths, there are several important considerations to keep in mind:
1. Manufacturer Capabilities
It’s essential to ensure that the chosen trace widths are within the manufacturing capabilities of the PCB fabrication facility. Different manufacturers may have varying limitations on minimum trace width, spacing, and copper thickness. Consulting with the manufacturer early in the design process can help avoid potential issues and ensure manufacturability.
2. Power and Ground Planes
For power and ground traces, it’s often recommended to use larger trace widths or even dedicated power and ground planes. These wider traces or planes provide low-impedance paths for current flow, minimize voltage drop, and improve overall power distribution on the PCB.
3. High-Speed Signals
When dealing with high-speed signals, trace width becomes critical for maintaining signal integrity. In addition to impedance matching, designers must consider factors such as trace length matching, spacing between traces, and the use of controlled impedance techniques. High-speed design often requires specialized knowledge and simulation tools to ensure optimal performance.
4. Trace Spacing and Clearance
In addition to trace width, the spacing between traces and the clearance from other components must be considered. Sufficient spacing helps prevent unintended coupling, crosstalk, and short circuits. Industry standards and manufacturer guidelines provide recommendations for minimum trace spacing based on factors such as voltage levels and PCB manufacturing capabilities.
Frequently Asked Questions (FAQ)
-
What is the minimum trace width for a PCB?
The minimum trace width depends on the PCB manufacturing capabilities and the specific design requirements. Typically, trace widths can range from 3 mils (0.075 mm) to 10 mils (0.254 mm) or more. It’s important to consult with the pcb manufacturer to determine their minimum trace width capabilities. -
How does copper thickness affect trace width calculation?
Copper thickness directly impacts the current-carrying capacity of a trace. Thicker copper layers allow for higher current densities and enable the use of narrower traces. When calculating trace width, the copper thickness must be taken into account to ensure adequate current-carrying capacity and prevent excessive heating. -
What is the difference between internal and external traces?
Internal traces are the copper tracks located within the inner layers of a multi-layer PCB, while external traces are the tracks on the outer layers (top and bottom) of the PCB. External traces are exposed to the environment and may require additional protection, such as solder mask or conformal coating. Internal traces are protected by the surrounding layers and have different design considerations compared to external traces. -
How do I calculate trace width for high-speed signals?
Calculating trace width for high-speed signals involves considering factors such as impedance matching, signal integrity, and controlled impedance techniques. High-speed design often requires specialized knowledge and simulation tools to ensure optimal performance. It’s recommended to consult with experienced high-speed PCB designers or use dedicated high-speed design tools to determine the appropriate trace widths for high-speed signals. -
Can I use different trace widths on the same PCB?
Yes, it’s common to use different trace widths on the same PCB depending on the specific requirements of each trace. For example, power traces may have wider widths compared to signal traces to handle higher currents. It’s important to ensure that the transitions between different trace widths are properly designed to maintain signal integrity and avoid impedance mismatches.
Conclusion
Calculating trace width is a critical step in PCB design to ensure proper current-carrying capacity, signal integrity, and overall performance. By considering factors such as current requirements, voltage drop, copper thickness, ambient temperature, and signal integrity, designers can determine the appropriate trace widths for their specific PCB layout.
Using established standards like IPC-2152, PCB trace width calculators, or manual calculations, designers can accurately determine the required trace widths. However, it’s essential to keep in mind additional design considerations such as manufacturer capabilities, power and ground planes, high-speed signals, and trace spacing.
By understanding the principles and techniques behind PCB trace width calculation, designers can create reliable and high-performance PCBs that meet the demands of modern electronic systems. Investing time in proper trace width calculation and following best practices in PCB design can lead to improved functionality, reduced manufacturing issues, and overall project success.