The Role of PCBs in Electronics
PCBs are essential components in virtually all modern electronic devices, from smartphones and computers to medical equipment and industrial machinery. They provide a reliable and efficient means of connecting electronic components, allowing for complex circuits to be created in a compact and organized manner.
The main advantages of using PCBs in electronic devices include:
- Miniaturization: PCBs allow for the creation of smaller, more compact devices by efficiently utilizing space and minimizing the need for bulky wiring.
- Reliability: The structured nature of PCBs reduces the risk of errors and improves the overall reliability of the electronic device.
- Mass production: PCBs are designed for automated assembly processes, enabling the efficient mass production of electronic devices.
- Cost-effectiveness: The use of PCBs streamlines the manufacturing process, reducing labor costs and material waste.
The pcb assembly process
The PCB assembly process consists of several key steps, each contributing to the creation of a functional electronic device. These steps include:
1. PCB Design and Fabrication
Before the assembly process can begin, the PCB must be designed and fabricated. This involves creating a schematic diagram of the electronic circuit, which is then translated into a physical layout of the PCB. The layout determines the placement of components and the routing of the conductive traces that connect them.
Once the design is finalized, the PCB is fabricated using a multi-step process that typically includes:
- Printing the circuit pattern onto a copper-clad substrate using photolithography
- Etching away the unwanted copper to create the conductive traces
- Drilling holes for component leads and vias
- Applying a protective solder mask and silkscreen layer for component labeling
2. Component Placement
With the fabricated PCB in hand, the next step is to place the electronic components onto the board. This process is typically automated using pick-and-place machines, which can rapidly and accurately position components based on the PCB layout.
The components are supplied to the pick-and-place machine on reels or trays, and the machine uses a vacuum nozzle or gripper to pick up each component and place it onto the PCB. The placement process is guided by fiducial markers on the PCB, which serve as reference points for the machine’s vision system.
3. Soldering
After the components are placed, they must be securely attached to the PCB using solder. Soldering is the process of melting a metal alloy (solder) to create a permanent electrical and mechanical connection between the component leads and the PCB’s conductive traces.
There are two primary methods of soldering in PCB assembly:
-
Wave soldering: The PCB is passed over a molten wave of solder, which wicks up through the holes in the board to create a connection between the component leads and the traces.
-
Reflow soldering: A solder paste, containing a mixture of solder and flux, is applied to the PCB prior to component placement. After placement, the entire board is heated in a reflow oven, causing the solder paste to melt and form a connection.
Reflow soldering is the more common method for surface mount components, while wave soldering is often used for through-hole components.
4. Inspection and Testing
Once the soldering process is complete, the PCB assembly undergoes a series of inspections and tests to ensure its quality and functionality. These may include:
-
Visual inspection: A manual or automated visual check of the PCB for any obvious defects, such as missing components, incorrect placement, or solder bridges.
-
Automated Optical Inspection (AOI): A machine-vision system that compares the assembled pcb to the original design files, identifying any discrepancies or defects.
-
X-ray inspection: Used to detect hidden defects, such as voids in solder joints or components with internal damage.
-
In-Circuit Testing (ICT): A test that verifies the electrical connectivity and component functionality by applying test signals to specific points on the PCB.
-
Functional testing: A test of the complete PCB assembly to ensure it performs as intended in its final application.
Any defects or issues identified during the inspection and testing phase are addressed through rework or repair processes before the PCB assembly is considered complete.
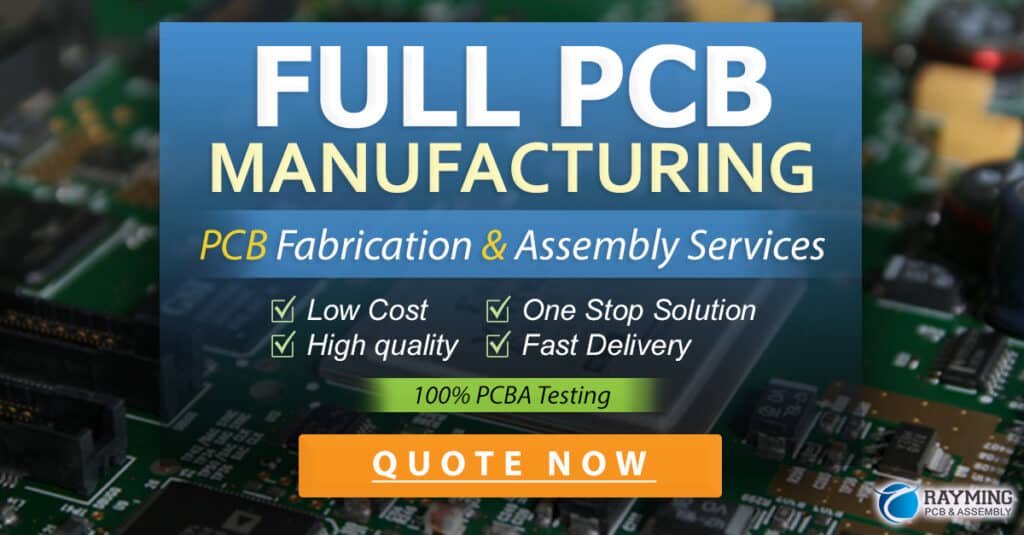
Types of PCB Assembly
There are two main types of PCB assembly, distinguished by the type of components used and the methods employed in their assembly:
1. Through-Hole Assembly
Through-hole assembly involves the use of components with long leads that are inserted through holes drilled in the PCB. The leads are then soldered to pads on the opposite side of the board. Through-hole components are typically larger and more robust than surface mount components, making them suitable for applications that require high mechanical strength or power handling capabilities.
The main advantages of through-hole assembly include:
- Mechanical strength: Through-hole components are anchored to the board by their leads, providing a strong mechanical connection.
- Ease of manual assembly: Through-hole components are easier to handle and place manually, making them suitable for low-volume or prototype production.
- Accessibility: Through-hole components are accessible from both sides of the board, making them easier to test, repair, or replace.
However, through-hole assembly has some disadvantages compared to surface mount assembly:
- Larger footprint: Through-hole components occupy more space on the PCB, limiting the potential for miniaturization.
- Higher cost: Drilling holes in the PCB and the manual placement of components can increase manufacturing costs.
- Slower assembly: The manual placement of through-hole components is slower than automated surface mount assembly.
2. Surface Mount Assembly
Surface mount assembly involves the use of components that are placed directly onto pads on the surface of the PCB, without the need for drilled holes. Surface mount components are typically smaller and more compact than through-hole components, allowing for higher component density and smaller overall PCB sizes.
The main advantages of surface mount assembly include:
- Miniaturization: Surface mount components enable the creation of smaller, more compact electronic devices.
- Automated assembly: Surface mount components are well-suited for automated pick-and-place assembly, reducing labor costs and increasing production speed.
- Lower cost: The elimination of drilled holes and the use of automated assembly processes can reduce manufacturing costs.
However, surface mount assembly also has some disadvantages:
- Reduced mechanical strength: Surface mount components rely on solder joints for mechanical stability, which may be less robust than through-hole connections.
- Difficulty of manual assembly: The small size of surface mount components makes manual placement and soldering more challenging.
- Limited accessibility: Surface mount components are typically only accessible from one side of the board, making testing and repair more difficult.
In many cases, PCB assemblies will use a combination of through-hole and surface mount components to balance the advantages and disadvantages of each method.
pcb assembly services
Given the complexity and precision required for successful PCB assembly, many companies choose to outsource this process to specialized PCB assembly services. These services offer a range of capabilities and benefits, including:
- Expertise: PCB assembly services employ skilled technicians and engineers with extensive experience in the assembly process, ensuring high-quality results.
- Advanced equipment: Assembly services invest in state-of-the-art equipment, such as automated pick-and-place machines and reflow ovens, to ensure consistent and reliable assembly.
- Scalability: Outsourcing PCB assembly allows companies to scale their production up or down as needed, without the need to invest in their own assembly infrastructure.
- Cost-effectiveness: By leveraging economies of scale and efficient assembly processes, PCB assembly services can often provide a more cost-effective solution than in-house assembly.
- Quality control: Reputable PCB assembly services employ strict quality control measures, including inspections and testing, to ensure that the final product meets the required specifications.
When selecting a PCB assembly service, it is essential to consider factors such as their experience, capabilities, quality control processes, and customer support. Additionally, the service should be able to handle the specific requirements of your project, such as the type of components used, the volume of production, and any special considerations like lead-free soldering or RoHS compliance.
The Future of PCB Assembly
As electronic devices continue to evolve and advance, so too does the PCB assembly process. Some of the key trends and developments shaping the future of PCB assembly include:
-
Miniaturization: The demand for smaller, more compact electronic devices is driving the development of advanced component packaging and assembly techniques, such as 3D packaging and embedded components.
-
Flexible and stretchable electronics: The emergence of flexible and stretchable PCBs is enabling new applications in wearable technology, medical devices, and robotics.
-
Automation and AI: Advances in automation and artificial intelligence are streamlining the PCB assembly process, improving efficiency, and reducing the potential for human error.
-
Sustainability: There is a growing emphasis on sustainable PCB assembly practices, including the use of lead-free solders, recyclable materials, and energy-efficient processes.
-
Industry 4.0: The integration of smart sensors, IoT technologies, and data analytics into the PCB assembly process is enabling real-time monitoring, predictive maintenance, and continuous process improvement.
By staying at the forefront of these developments, PCB assembly services can continue to provide cutting-edge solutions for the electronics industry.
FAQs
-
Q: What is the difference between pcb fabrication and PCB assembly?
A: PCB fabrication is the process of creating the bare PCB, including printing the circuit pattern, etching the copper, and applying the protective layers. PCB assembly is the process of attaching components to the fabricated PCB to create a functional electronic device.
-
Q: What are the main types of components used in PCB assembly?
A: The two main types of components used in PCB assembly are through-hole components, which have leads that are inserted through holes in the PCB, and surface mount components, which are placed directly onto pads on the surface of the PCB.
-
Q: What is the purpose of soldering in PCB assembly?
A: Soldering is used to create a permanent electrical and mechanical connection between the component leads and the conductive traces on the PCB. It ensures that the components are securely attached and can function as intended.
-
Q: How are PCB assemblies tested for quality and functionality?
A: PCB assemblies undergo a series of inspections and tests, including visual inspection, automated optical inspection (AOI), X-ray inspection, in-circuit testing (ICT), and functional testing. These processes help identify any defects or issues that may affect the performance of the final product.
-
Q: What are the benefits of outsourcing PCB assembly to a specialized service?
A: Outsourcing PCB assembly to a specialized service offers several benefits, including access to expertise and advanced equipment, scalability, cost-effectiveness, and quality control. These services can help companies produce high-quality PCB assemblies efficiently and reliably.
Characteristic | Through-Hole Assembly | Surface Mount Assembly |
---|---|---|
Component placement | Inserted through holes in the PCB | Placed directly onto pads on the PCB surface |
Component size | Larger, more robust | Smaller, more compact |
Assembly method | Manual or automated insertion, wave soldering | Automated pick-and-place, reflow soldering |
Mechanical strength | Strong, anchored by leads | Less robust, relies on solder joints |
Accessibility | Accessible from both sides of the PCB | Typically accessible from one side only |
Miniaturization potential | Limited by component size and hole drilling | Enables higher component density and smaller PCBs |
Cost | Higher due to drilling and manual placement | Lower due to automated processes and fewer holes |
Production speed | Slower, especially with manual placement | Faster, thanks to automated assembly |
In conclusion, PCB assembly is a critical process in the creation of electronic devices, involving the attachment of components to a fabricated PCB through various methods such as soldering. The choice between through-hole and surface mount assembly depends on factors such as the desired level of miniaturization, mechanical strength, and production efficiency. By understanding the PCB assembly process and partnering with experienced assembly services, companies can ensure the successful development and production of their electronic products.