Introduction
Printed Circuit Boards (PCBs) are the backbone of modern electronics. They are used in virtually every electronic device, from smartphones and laptops to medical equipment and aerospace systems. The PCB manufacturing process is a complex and precise operation that involves multiple steps and specialized equipment. In this ultimate guide, we will explore the PCB manufacturing process in detail, from design to final assembly.
What is a PCB?
A PCB is a flat board made of insulating material, such as fiberglass or plastic, with conductive copper traces printed on one or both sides. These traces connect various electronic components, such as resistors, capacitors, and integrated circuits (ICs), to form a functional circuit. PCBs can be single-sided (with traces on one side only), double-sided (with traces on both sides), or multi-layered (with traces on multiple layers).
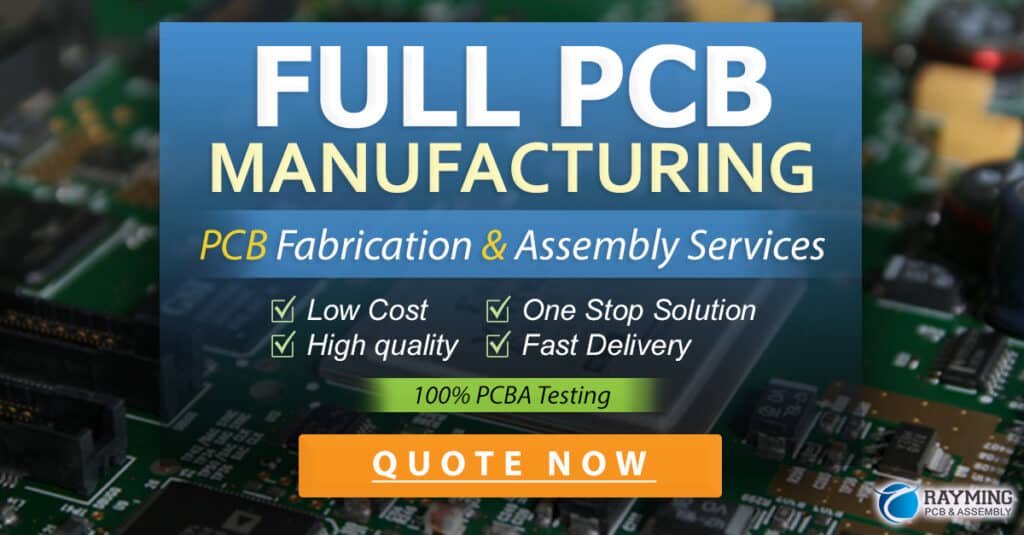
PCB Design
The PCB manufacturing process begins with the design phase. This involves creating a schematic diagram of the circuit and then laying out the physical components and traces on the PCB. There are several key considerations in PCB design:
Schematic Design
The schematic diagram is a graphical representation of the electronic circuit. It shows the components and their interconnections using standardized symbols. The schematic is created using electronic design automation (EDA) software, such as KiCad, Eagle, or Altium Designer.
pcb layout
Once the schematic is complete, the next step is to create the PCB layout. This involves arranging the components and traces on the physical board while adhering to various design rules and constraints. Some key considerations in PCB layout include:
- Component placement: Components should be placed in a way that minimizes the length of traces and reduces signal interference.
- Trace routing: Traces should be routed efficiently to minimize resistance and avoid signal integrity issues.
- Via placement: Vias (holes drilled through the board to connect traces on different layers) should be placed strategically to minimize signal reflections and crosstalk.
- Ground planes: Solid copper planes should be used for ground and power distribution to reduce noise and improve signal integrity.
Design Rule Check (DRC)
Before finalizing the PCB layout, it is important to run a design rule check (DRC) to ensure that the design meets all manufacturing and electrical requirements. The DRC checks for issues such as minimum trace width, minimum clearance between traces, and minimum drill size for vias.
pcb fabrication
Once the PCB design is complete and has passed the DRC, it is ready for fabrication. The fabrication process involves several steps:
Material Selection
The first step in PCB fabrication is to select the appropriate material for the board. The most common materials used for PCBs are:
Material | Description | Advantages | Disadvantages |
---|---|---|---|
FR-4 | Fiberglass-reinforced epoxy laminate | Low cost, good mechanical strength, good electrical insulation | Limited high-frequency performance |
Rogers | High-frequency laminate | Excellent high-frequency performance, low dielectric loss | High cost, limited availability |
Polyimide | High-temperature laminate | Excellent thermal stability, good mechanical strength | High cost, limited availability |
Copper Cladding
The next step is to apply a layer of copper foil to the board material. This is typically done using a process called electroless copper plating, which involves depositing a thin layer of copper onto the board using a chemical bath.
Photoresist Application
After the copper foil is applied, a layer of photoresist is applied to the board. Photoresist is a light-sensitive material that hardens when exposed to UV light.
Exposure and Development
The PCB layout is then printed onto a transparent film called a photomask. The photomask is placed on top of the photoresist-coated board and exposed to UV light. The areas of the photoresist that are exposed to light harden, while the unexposed areas remain soft.
After exposure, the board is placed in a developer solution that removes the soft, unexposed photoresist, leaving only the hardened resist that corresponds to the PCB layout.
Etching
The next step is to etch away the unwanted copper from the board, leaving only the traces and pads that form the circuit. This is typically done using a chemical etching process, such as ferric chloride or ammonium persulfate.
Stripping and Cleaning
After etching, the remaining photoresist is stripped away using a chemical stripper, and the board is cleaned to remove any residue.
Drilling
Holes are then drilled in the board for through-hole components and vias. This is typically done using a computer-controlled drilling machine.
Plating
The drilled holes are then plated with copper to create electrical connections between the layers of the board. This is typically done using an electroplating process.
Solder Mask Application
A layer of solder mask is then applied to the board to protect the copper traces from oxidation and prevent solder bridging during assembly. The solder mask is typically green, but other colors are available.
Silkscreen Printing
Finally, a silkscreen layer is printed onto the board to add component labels, logos, and other markings. This is typically done using a screen printing process.
pcb assembly
Once the PCB fabrication is complete, the board is ready for assembly. The assembly process involves several steps:
Solder Paste Application
A layer of solder paste is applied to the pads on the board using a stencil printing process. Solder paste is a mixture of tiny solder balls and flux that helps the solder adhere to the pads.
Component Placement
The components are then placed onto the board using a pick-and-place machine. This machine uses a vacuum nozzle to pick up each component and place it onto the corresponding pads on the board.
Reflow Soldering
The board is then passed through a reflow oven, which melts the solder paste and creates a permanent electrical and mechanical connection between the components and the board.
Inspection and Testing
After assembly, the board is inspected visually and electrically to ensure that all components are properly placed and connected. This may involve automated optical inspection (AOI), X-ray inspection, or functional testing.
Frequently Asked Questions (FAQ)
What is the difference between a PCB and a PCBA?
A PCB (printed circuit board) is the bare board without any components attached. A PCBA (printed circuit board assembly) is a PCB with all the components soldered onto it, ready for use in an electronic device.
What is the typical turnaround time for PCB manufacturing?
The turnaround time for PCB manufacturing varies depending on the complexity of the design and the fabrication options selected. For simple, 2-layer boards, the turnaround time can be as fast as 24 hours. For more complex, multi-layer boards, the turnaround time can be several weeks.
What is the minimum trace width and spacing for a PCB?
The minimum trace width and spacing depend on the PCB fabrication process and the design requirements. For standard PCBs, the minimum trace width is typically 0.006 inches (0.15 mm), and the minimum spacing is typically 0.006 inches (0.15 mm). For high-density PCBs, the minimum trace width and spacing can be as small as 0.003 inches (0.076 mm).
What is the difference between surface mount and through-hole components?
Surface mount components are mounted directly onto the pads on the surface of the PCB, while through-hole components have leads that are inserted into holes drilled in the board and soldered onto the opposite side. Surface mount components are smaller and can be placed more densely on the board, while through-hole components are more robust and easier to solder manually.
How much does PCB manufacturing cost?
The cost of PCB manufacturing depends on several factors, including the size and complexity of the board, the number of layers, the materials used, and the quantity ordered. For small quantities of simple, 2-layer boards, the cost can be as low as $0.50 per board. For larger quantities of more complex, multi-layer boards, the cost can be several dollars per board.
Conclusion
PCB manufacturing is a complex and precise process that involves multiple steps and specialized equipment. From design to fabrication to assembly, each step must be carefully controlled to ensure the highest quality and reliability of the final product. By understanding the PCB manufacturing process, designers and engineers can create better, more efficient, and more cost-effective electronic devices.