In today’s fast-paced and competitive manufacturing landscape, companies are constantly seeking ways to improve efficiency, reduce costs, and accelerate innovation. One of the most transformative trends in recent years has been the adoption of in-house fabrication and additive manufacturing (AM), commonly known as 3D printing. These technologies enable companies to produce parts, prototypes, and tools directly within their facilities, bypassing traditional supply chains and external vendors.
In-house fabrication and additive manufacturing offer a wide range of benefits, from faster production times to greater design flexibility. In this article, we will explore seven key advantages of bringing fabrication and additive manufacturing capabilities in-house, and how these technologies are revolutionizing industries such as aerospace, automotive, healthcare, and consumer electronics.
1. Faster Time-to-Market
Why It Matters:
In today’s competitive market, speed is a critical factor for success. Companies that can bring products to market faster gain a significant advantage over their competitors.
How In-House Fabrication Helps:
- Rapid Prototyping: Additive manufacturing allows for the quick production of prototypes, enabling designers to test and iterate on their designs in a matter of hours or days, rather than weeks.
- Reduced Lead Times: By eliminating the need to outsource production, companies can avoid delays associated with external vendors, shipping, and communication.
- On-Demand Production: In-house fabrication enables companies to produce parts and tools as needed, reducing the time spent waiting for external suppliers.
Example:
A consumer electronics company can use in-house 3D printing to rapidly prototype and test new product designs, allowing them to launch innovative products ahead of competitors.
2. Cost Savings
Why It Matters:
Reducing production costs is a top priority for manufacturers, as it directly impacts profitability and competitiveness.
How In-House Fabrication Helps:
- Elimination of Tooling Costs: Traditional manufacturing methods often require expensive tooling and molds. Additive manufacturing eliminates these costs by building parts layer by layer.
- Reduced Material Waste: Additive manufacturing is an additive process, meaning it only uses the material needed to create the part, minimizing waste.
- Lower Inventory Costs: In-house fabrication allows for just-in-time production, reducing the need for large inventories of spare parts and components.
Example:
An automotive manufacturer can use in-house 3D printing to produce custom jigs and fixtures, saving thousands of dollars in tooling and inventory costs.
3. Design Freedom and Innovation
Why It Matters:
Innovation is the lifeblood of any industry, and the ability to experiment with new designs and concepts is essential for staying ahead.
How In-House Fabrication Helps:
- Complex Geometries: Additive manufacturing enables the production of complex geometries that are difficult or impossible to achieve with traditional methods.
- Customization: In-house fabrication allows for the easy customization of parts and products to meet specific customer needs or application requirements.
- Iterative Design: Designers can quickly iterate on their designs, testing new ideas and making improvements without the constraints of traditional manufacturing processes.
Example:
A medical device company can use in-house 3D printing to create patient-specific implants with intricate geometries, improving patient outcomes and reducing surgery times.
4. Improved Quality Control
Why It Matters:
Quality control is critical for ensuring that products meet the required standards and specifications.
How In-House Fabrication Helps:
- Direct Oversight: By keeping production in-house, companies have direct control over the manufacturing process, allowing them to monitor and address quality issues in real-time.
- Consistency: In-house fabrication ensures consistent production quality, as the same team and equipment are used throughout the process.
- Testing and Validation: Companies can quickly test and validate parts and prototypes, ensuring that they meet the required performance and safety standards.
Example:
An aerospace manufacturer can use in-house additive manufacturing to produce critical components, ensuring that each part meets the stringent quality standards required for aviation.
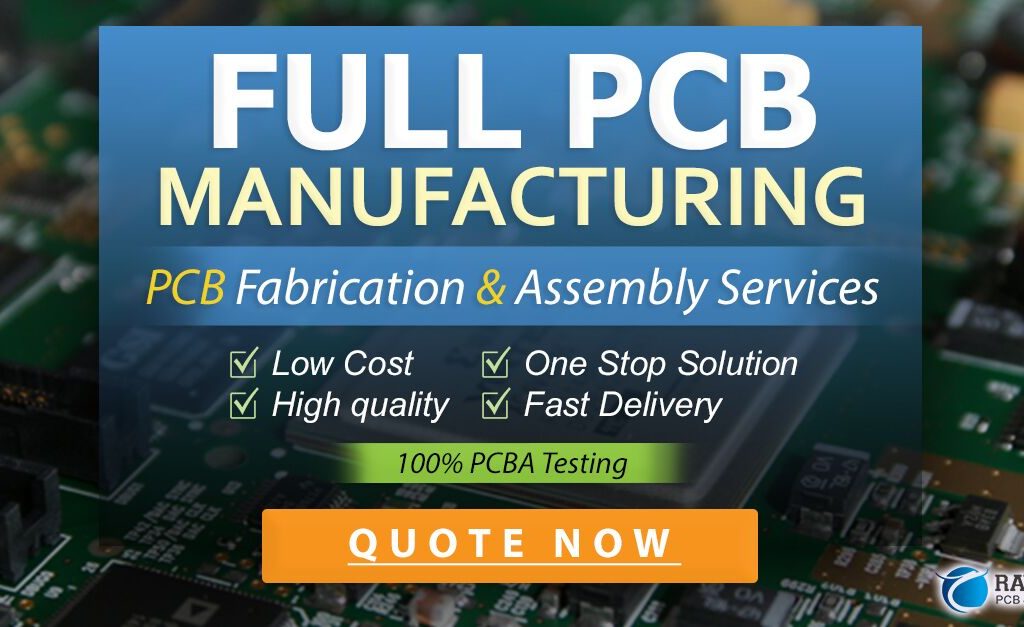
5. Enhanced Supply Chain Resilience
Why It Matters:
Global supply chains are vulnerable to disruptions, such as natural disasters, geopolitical events, and pandemics. Building resilience into the supply chain is essential for maintaining business continuity.
How In-House Fabrication Helps:
- Localized Production: In-house fabrication reduces reliance on external suppliers, making the supply chain more resilient to disruptions.
- On-Demand Production: Companies can produce parts and components as needed, reducing the risk of shortages and delays.
- Reduced Dependency: By bringing production in-house, companies can reduce their dependency on a single supplier or region, mitigating risks associated with supply chain disruptions.
Example:
During the COVID-19 pandemic, many companies used in-house 3D printing to produce personal protective equipment (PPE) and medical devices, ensuring a steady supply despite global shortages.
6. Sustainability and Environmental Benefits
Why It Matters:
Sustainability is becoming increasingly important for companies, as consumers and regulators demand more environmentally friendly practices.
How In-House Fabrication Helps:
- Reduced Material Waste: Additive manufacturing is an additive process, meaning it only uses the material needed to create the part, minimizing waste.
- Energy Efficiency: In-house fabrication can reduce the energy consumption associated with transporting parts and components from external suppliers.
- Recyclable Materials: Many additive manufacturing processes use recyclable materials, further reducing their environmental impact.
Example:
A consumer goods company can use in-house 3D printing to produce packaging prototypes, reducing material waste and energy consumption compared to traditional methods.
7. Competitive Advantage
Why It Matters:
In a competitive market, companies need to differentiate themselves through innovation, efficiency, and customer satisfaction.
How In-House Fabrication Helps:
- Faster Innovation: In-house fabrication enables companies to quickly develop and test new ideas, staying ahead of competitors.
- Customization: Companies can offer customized products and solutions, meeting the unique needs of their customers.
- Cost Efficiency: By reducing production costs and lead times, companies can offer more competitive pricing and better value to their customers.
Example:
A sports equipment manufacturer can use in-house 3D printing to produce custom-fit gear for athletes, offering a unique selling point and gaining a competitive edge in the market.
Conclusion
In-house fabrication and additive manufacturing are transforming the way companies design, produce, and deliver products. By bringing production capabilities in-house, companies can achieve faster time-to-market, cost savings, design freedom, improved quality control, supply chain resilience, sustainability, and a competitive advantage.
For your boss or team, understanding the benefits of in-house fabrication and additive manufacturing can lead to better decision-making, increased efficiency, and a stronger position in the market. Whether you’re in aerospace, automotive, healthcare, or consumer electronics, these technologies offer a powerful toolset for driving innovation and success in the modern manufacturing landscape.