Introduction
High-Density Interconnect (HDI) printed circuit boards (PCBs) have become a cornerstone of modern electronics, enabling the development of smaller, faster, and more efficient devices. As the demand for compact and high-performance electronics grows, so does the need for advanced PCB stackup designs. One such design is the 2+N+2 PCB stackup, which is widely used in HDI boards to achieve high signal integrity, reduced size, and improved performance. This article provides an in-depth exploration of the 2+N+2 PCB stackup design, its benefits, applications, and best practices for implementation.
What is a 2+N+2 PCB Stackup?
A 2+N+2 PCB stackup is a specific configuration of layers in an HDI board. The term “2+N+2” refers to the arrangement of the layers:
- 2: Two sequential lamination layers on the top.
- N: A core layer (or multiple core layers) in the middle.
- 2: Two sequential lamination layers on the bottom.
This design is particularly suited for HDI boards, which require high routing density, fine pitch components, and controlled impedance. The 2+N+2 stackup allows for the use of microvias, blind vias, and buried vias, which are essential for achieving the high interconnect density required in modern electronics.
Key Features of 2+N+2 PCB Stackup
1. Sequential Lamination
- The top and bottom layers are built using sequential lamination, which involves adding layers one at a time and laminating them together. This process enables the creation of microvias and blind vias, which are critical for HDI designs.
2. Core Layer
- The core layer (or layers) in the middle provides structural stability and serves as a reference plane for signal routing. The number of core layers (N) can vary depending on the complexity of the design.
3. Microvias and Blind/Buried Vias
- Microvias are small vias with diameters typically less than 150 microns, used to connect adjacent layers. Blind vias connect an outer layer to an inner layer, while buried vias connect inner layers without reaching the outer layers.
4. Controlled Impedance
- The 2+N+2 stackup allows for precise control of impedance, which is crucial for high-speed signal integrity.
Benefits of 2+N+2 PCB Stackup Design
1. High Routing Density
- The use of microvias and blind/buried vias enables higher routing density, allowing for more connections in a smaller area.
2. Improved Signal Integrity
- The controlled impedance and reduced signal path lengths in a 2+N+2 stackup minimize signal loss and crosstalk, ensuring reliable performance in high-speed applications.
3. Compact Size
- By enabling more connections in a smaller space, the 2+N+2 stackup helps reduce the overall size of the PCB, making it ideal for compact devices.
4. Enhanced Thermal Management
- The layered structure of the 2+N+2 stackup allows for better heat dissipation, which is critical for high-performance electronics.
5. Cost-Effective for HDI Applications
- While HDI boards are generally more expensive than traditional PCBs, the 2+N+2 stackup offers a cost-effective solution for achieving high-density interconnects without excessive layer counts.
Applications of 2+N+2 PCB Stackup
The 2+N+2 PCB stackup is widely used in applications that require high-density interconnects and high-speed performance. Some of the most common applications include:
1. Consumer Electronics
- Smartphones, tablets, and wearables rely on HDI boards with 2+N+2 stackups to achieve compact designs and high performance.
2. Automotive Electronics
- Advanced driver-assistance systems (ADAS), infotainment systems, and engine control units (ECUs) use 2+N+2 stackups to meet the demands of high-speed data processing and reliability.
3. Medical Devices
- Portable medical devices and imaging systems require compact and reliable PCBs, making the 2+N+2 stackup an ideal choice.
4. Aerospace and Defense
- Avionics, communication systems, and radar equipment benefit from the high-density interconnects and signal integrity offered by 2+N+2 stackups.
5. Networking and Telecommunications
- Routers, switches, and 5G infrastructure rely on HDI boards with 2+N+2 stackups to handle high-speed data transmission and processing.
Design Considerations for 2+N+2 PCB Stackup
Designing a 2+N+2 PCB stackup requires careful planning and attention to detail. Below are some key considerations:
1. Layer Configuration
- Determine the number of core layers (N) based on the complexity of the design. For example, a 2+4+2 stackup has four core layers, while a 2+6+2 stackup has six core layers.
2. Material Selection
- Choose high-quality materials with low dielectric loss and good thermal properties. Common materials include FR-4, Rogers, and polyimide.
3. Via Types and Placement
- Use microvias, blind vias, and buried vias strategically to maximize routing density and minimize signal path lengths. Ensure proper via placement to avoid signal integrity issues.
4. Impedance Control
- Calculate and control the impedance of critical signal traces to ensure high-speed signal integrity. Use impedance matching techniques to minimize reflections and crosstalk.
5. Thermal Management
- Incorporate thermal vias and heat sinks to dissipate heat effectively, especially in high-power applications.
6. Manufacturing Constraints
- Work closely with your PCB manufacturer to ensure that the design is manufacturable. Consider factors such as minimum trace width, via size, and layer alignment.
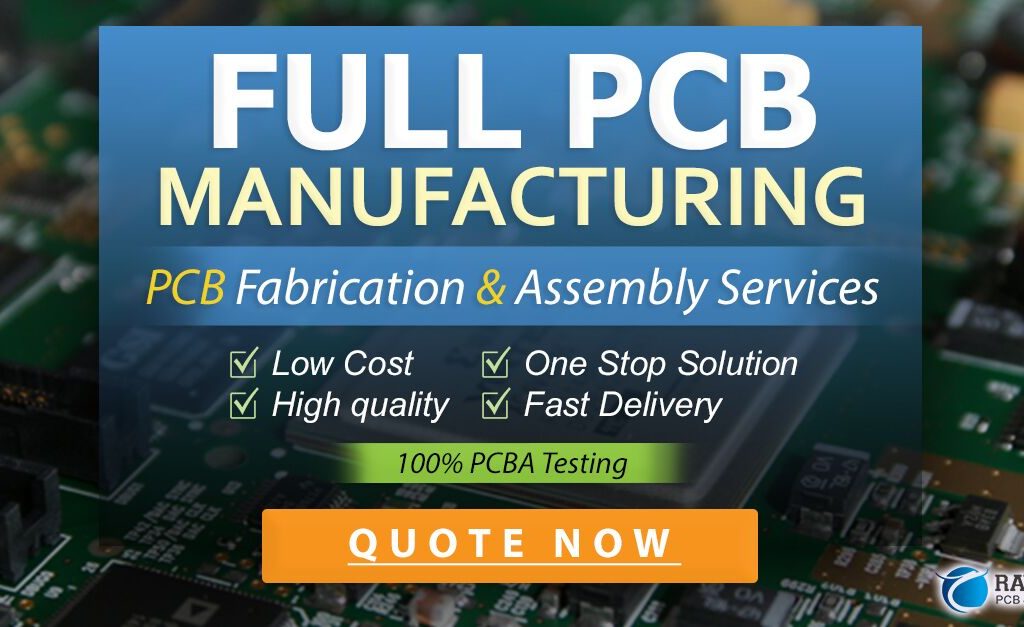
Step-by-Step Guide to Designing a 2+N+2 PCB Stackup
Step 1: Define the Requirements
- Identify the number of layers, signal types, power requirements, and thermal management needs.
Step 2: Choose the Layer Configuration
- Decide on the number of core layers (N) based on the design complexity. For example, a 2+4+2 stackup is suitable for moderately complex designs, while a 2+6+2 stackup is better for highly complex designs.
Step 3: Select Materials
- Choose materials with appropriate dielectric constants, thermal conductivity, and mechanical strength.
Step 4: Plan the Via Structure
- Use microvias for connections between adjacent layers and blind/buried vias for connections between non-adjacent layers.
Step 5: Route the Traces
- Route high-speed signals on inner layers with reference planes to minimize interference. Use differential pairs for high-speed signals to reduce noise.
Step 6: Perform Signal Integrity Analysis
- Use simulation tools to analyze signal integrity, impedance matching, and crosstalk. Make adjustments as needed.
Step 7: Verify Thermal Performance
- Simulate thermal performance to ensure that the PCB can dissipate heat effectively. Add thermal vias and heat sinks if necessary.
Step 8: Collaborate with the Manufacturer
- Share the design with your PCB manufacturer and address any manufacturability concerns.
Challenges and Solutions in 2+N+2 PCB Stackup Design
1. Complexity
- The 2+N+2 stackup is more complex than traditional stackups, requiring advanced design tools and expertise.
- Solution: Use advanced PCB design software and collaborate with experienced engineers.
2. Manufacturing Costs
- HDI boards with 2+N+2 stackups are more expensive to manufacture due to the use of microvias and sequential lamination.
- Solution: Optimize the design to minimize layer counts and via usage without compromising performance.
3. Signal Integrity Issues
- High-speed signals are prone to reflections, crosstalk, and losses in HDI boards.
- Solution: Use impedance matching, differential pairs, and proper grounding techniques to maintain signal integrity.
4. Thermal Management
- High-density designs generate more heat, which can affect performance and reliability.
- Solution: Incorporate thermal vias, heat sinks, and adequate spacing between components.
Future Trends in 2+N+2 PCB Stackup Design
As technology continues to evolve, the 2+N+2 PCB stackup design is expected to incorporate new advancements:
1. Advanced Materials
- The use of materials with lower dielectric constants and higher thermal conductivity will improve performance and reliability.
2. 3D Printing
- Additive manufacturing techniques, such as 3D printing, may revolutionize PCB fabrication, enabling more complex and compact designs.
3. AI-Driven Design Tools
- Artificial intelligence (AI) and machine learning (ML) will enhance PCB design tools, enabling faster and more accurate optimization of 2+N+2 stackups.
4. Integration with Flexible PCBs
- Combining 2+N+2 stackups with flexible PCBs will enable the development of innovative products with unique form factors.
Conclusion
The 2+N+2 PCB stackup design is a powerful solution for achieving high-density interconnects and high-speed performance in modern electronics. By understanding its features, benefits, and design considerations, engineers can create compact, reliable, and high-performance PCBs for a wide range of applications. As technology advances, the 2+N+2 stackup will continue to play a critical role in shaping the future of electronics, enabling the development of smaller, faster, and more efficient devices.